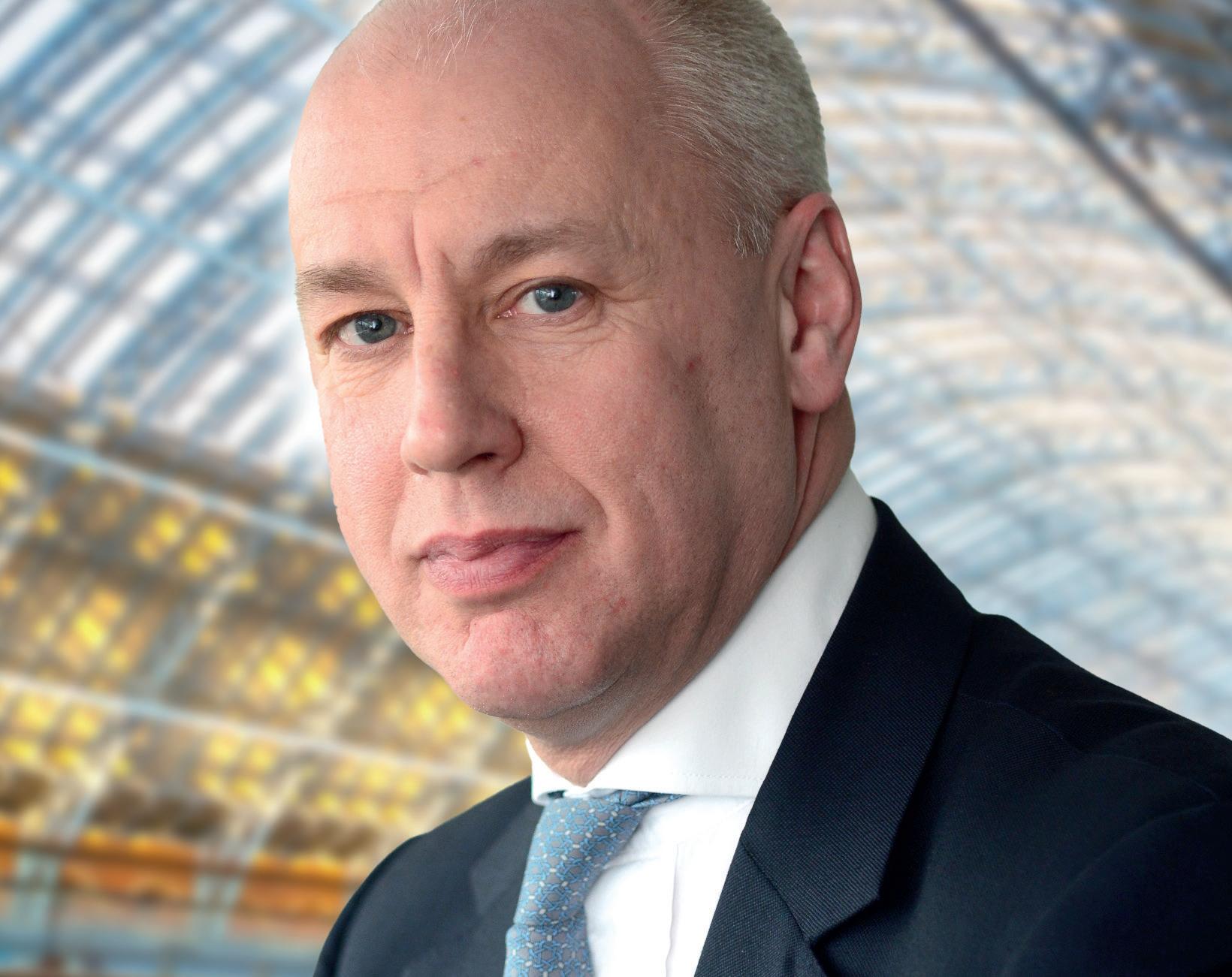
8 minute read
Deploying the first hydrogen trains in passenger service in the UK
Alstom’s UK&I Managing Director Nick Crossfield discusses working together with Eversholt Rail to decarbonise the rail sector
Britain’s leading train manufacturer and maintenance provider Alstom, and leading British train owner and financier Eversholt Rail, are working together on the UK’s first new hydrogen train fleet.
The Memorandum of Understanding (MOU) sees them share technical and commercial information necessary for Alstom to design, build, commission and support a fleet of 10 three-car hydrogen multiple units (HMUs).
“These trains will set numerous precedents through the approvals process and their acceptance into service,” said Nick Crossfield, Managing Director at Alstom.
Decarbonising the network “They will then need to demonstrate how operators can transition their services (and their behind the scenes operations) from diesel to hydrogen. They will be doing the same to diesel that diesel did to steam while at the same time decarbonising great stretches of the network.
“By working together with Eversholt Rail, we have been able to exploit each other’s strengths to be able to make an unprecedented move in the market, introducing a novel technology to the UK, privately financed and proactively looking forward to meeting the clear needs of the market.”
The trains will be built by Alstom with the HMU fleet based on the latest evolution of the Alstom Aventra platform. The single-deck train has been
Nick Crossfield, Alstom’s UK&I Managing Director
developed for the requirements of mainline train operations, from high-capacity metro systems to intercity services.
Nick, who was appointed MD in September 2015, said: “The Alstom Aventra is the next generation of the Aventra platform developed by Bombardier.
“Since our acquisition of Bombardier, we have set about optimising the platform, blending Alstom’s and Bombardier’s technologies and know-how to realise the benefits of combining two such technically strong companies.
“This new platform can be configured as an Electric Multiple Unit, a Battery Electric Multiple Unit or an HMU, and has been designed as such from the outset.



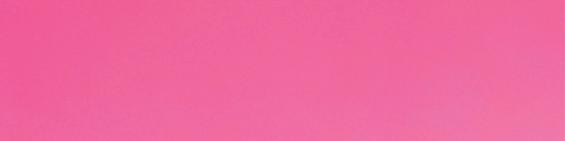
NOTHING TO SNOOZE AT SNOOZE AT
Subscribe today for all the best news in UK rail from 7am daily
news.railbusinessdaily.com
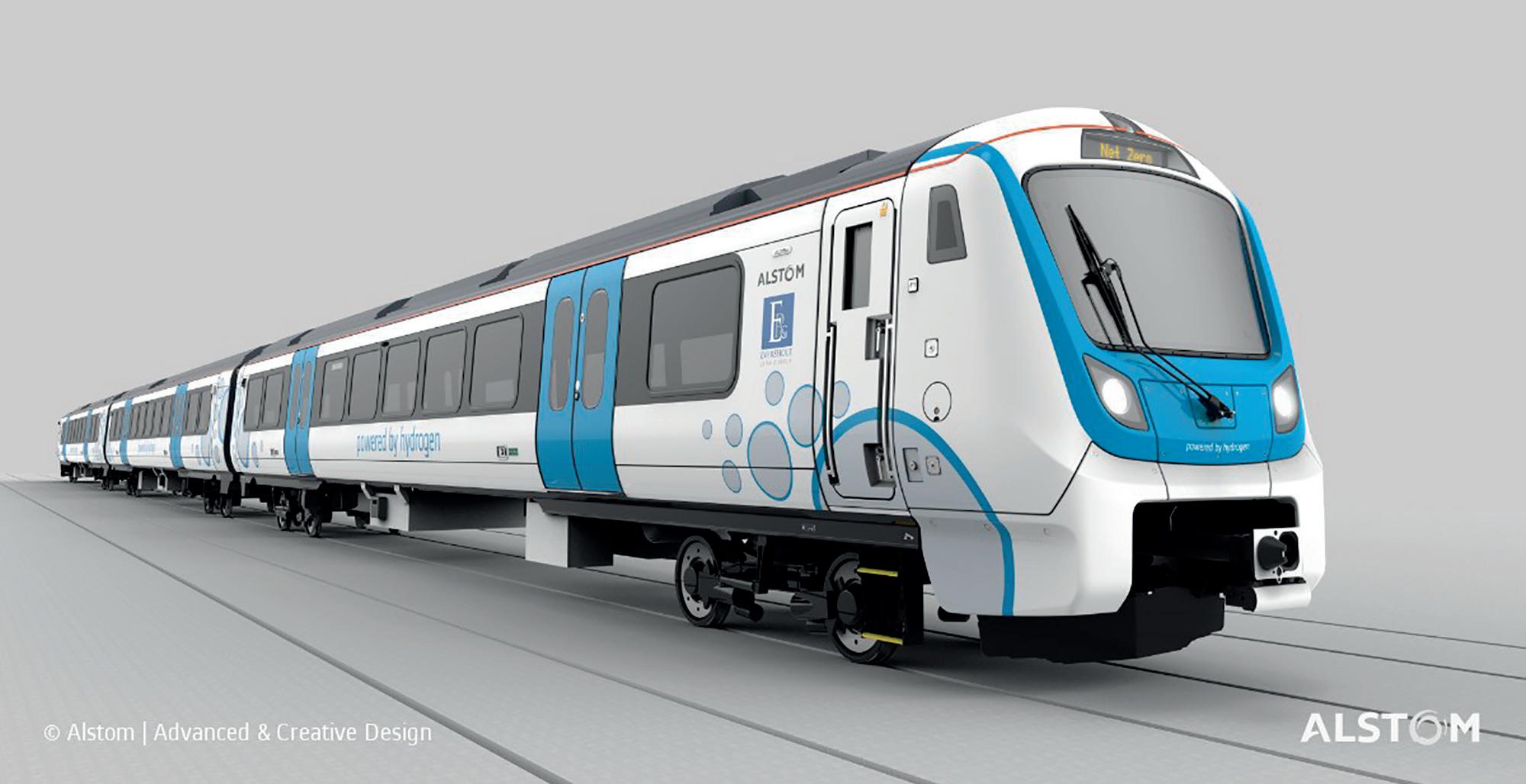
“In terms of the hydrogen variant, this means we have optimised the packaging of hydrogen equipment on the roof, we have maximised the internal ‘furnishable space’ that remains as flexible and versatile as the rest of the Aventra family.
Hydrogen solution “As the hydrogen trains form part of the family, we can also support fleet commonality across differing types of traction, simplifying operations in line with the Williams-Shapps recommendations.”
Alstom and Eversholt Rail have previously worked together on the Breeze project – a hydrogen rolling stock solution for the UK rail sector, through the proposed conversion of an existing EMU to hydrogen power. Building on the long-standing relationship across many fleets, they worked together to develop a conversion of the Class 321 EMUs into Class 600 Breeze hydrogen trains.
As an asset owner and investor in the rail market, Eversholt Rail was keen to work with the world leaders in hydrogen train technology, to learn and to develop its fleet options. From Alstom’s point of view, Nick says it was very productive to work closely with a key customer, understanding their priorities and objectives.
“I suspect Breeze will prove to be the most successful train we never sold,” said Nick. “By developing it, promoting it and offering it as a firm offer to the market, we demonstrated the intent of both Alstom and wider stakeholders like Eversholt Rail to commit to this new and innovative technology.
“In so doing, we helped move the market from merely curious to completely expectant of hydrogen trains in the UK. Network Rail concluded in its Traction Decarbonisation Network Strategy that many hydrogen trains will be required both before and after 2050, and expert opinion across the sector concurs.
“As this demand has matured, it became clear that a new-build option could be even more attractive than a conversion – we can package equipment better to overcome the limitations of a conversion, we can offer stateof-the-art underpinnings and the trains will have a 35-year life.
“With much of the DMU installed base too old for conversion, this is the ideal solution.”
This project builds on Alstom’s commitment in taking a leading role in decarbonising the rail sector. It was the first company to produce a hydrogen-powered train – the Coradia iLint – which is in operational service in Germany and made its debut in Sweden in August last year.
Clear market “We are used to being innovators at Alstom, but the thrill of leading the way never fades,” said Nick.
“We of course have already introduced hydrogen trains to passenger service in Germany, with orders in France and Italy too. There is a clear market requirement in Britain for hydrogen trains, driven by the laws of both economics and physics.
“Hydrogen is the only form of zero carbon energy storage available to power trains over sufficient distances to allow us to replace polluting diesels on non-electrified routes.
“The reason we need energy storage is because in certain places and on certain routes we cannot immediately electrify the network, often for reasons of cost.
“Hydrogen adds an extra dimension to our planning and complements electrification plans perfectly by providing a more cost-effective solution for those hard to electrify, longer-range regional routes.”
The intention is that final contracts for the first 10 trains will be signed early this year, allowing operators the opportunity to put these trains into service before the end of 2025.
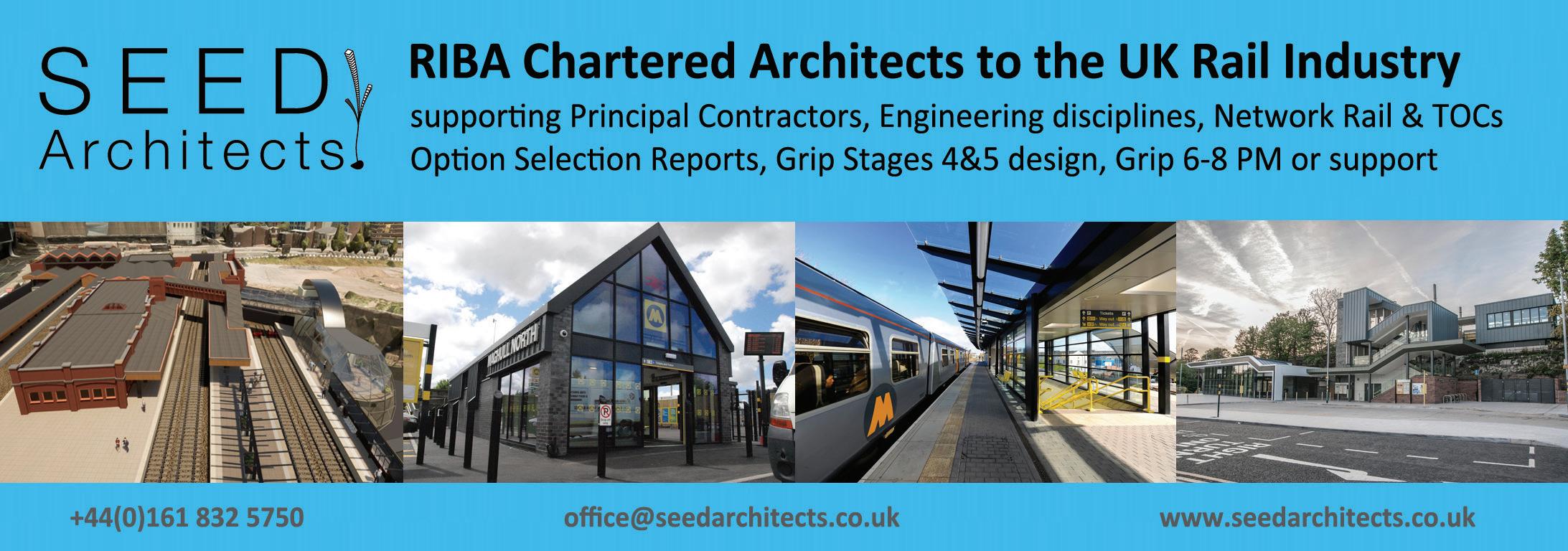
Structural Fabrications Ltd: ‘Steeling’ the show in UK rail
Meet the director at the forefront of the rail industry, advancing all-in-one steelwork solutions with prime expertise, prowess and precision
On any rail infrastructure project, steel and metalwork are core components and key foundations to the project’s success.
The ranging variables of track and traffic conditions found in the railway environment means that there are comprehensive roles that steel entails in sustaining the rail network. Structural Fabrications Ltd is a Derby-headquartered design, fabrication, installation, and maintenance organisation, delivering excellence to every project it undertakes, with more than 30 years’ experience operating in the industry.
By working in close partnership with its customers, Structural Fabrications Ltd administrates products and services that surpass the array of demands from the UK rail industry. From design, fabrication and delivery to installation, maintenance, refurbishment, and project management, Structural Fabrications Ltd strives to excel in all its specialities – including providing steel for track, safety rails, bridges, plus stations and depots.
From concept to completion Suj Kang, Structural Fabrications Ltd’s Managing Director and the business’s very own ‘man of steel’, said: “When it comes to our bespoke steelworks, we recognise that there is no one-sizefits-all solution. That’s why we treat each project individually, taking it through the entire lifecycle and establishing the customer’s vision into reality.’’
Structural Fabrications Ltd has a wealth of expertise and an exemplary track record of delivered projects across the UK rail infrastructure. Notable projects include an upgrade to Kidderminster Station, where the team carried out the fabrication and installation of the main building steelwork, waterproofing roof, and fascia panels at the refurbishment of the station building, and most recently Coventry Station.
At Cadder Station, the Structural Fabrications Ltd project team was selected to design steelwork connections, fabrication, galvanisation and installation of a new access pipe bridge and canopy, with the complex installation achieved using a mobile crane and spider crane for a safe and systematic delivery.
Another success was the delivery of a refurbishment to West Hampstead Station, a complete station upgrade completed on behalf of Buckingham Group Contracting. The work provided improved accessibility and capacity, with new stairs, lift towers, bridge and a concourse building completed. Works involved steelwork, cladding, glazing, waterproofing and fascia.
Discussing the refurbishment, Suj said: “This was a particularly challenging build at a busy operational London railway station. We developed a modular design strategy that would allow the structures to be installed over a series of single-night line closures to minimise disruption at the station. We were able to build the majority of the concourse during the day, allowing the station to remain open to the public.”
He added: “Each module was designed to allow most of the cladding to be fitted offsite, dramatically reducing installation time. The project was a major success, with the new station displaying a much-improved aesthetic, including a new bright and airy entrance, and vastly improved accessibility for passengers. This is a great example of Structural Fabrications Ltd team’s wider project management capabilities.”
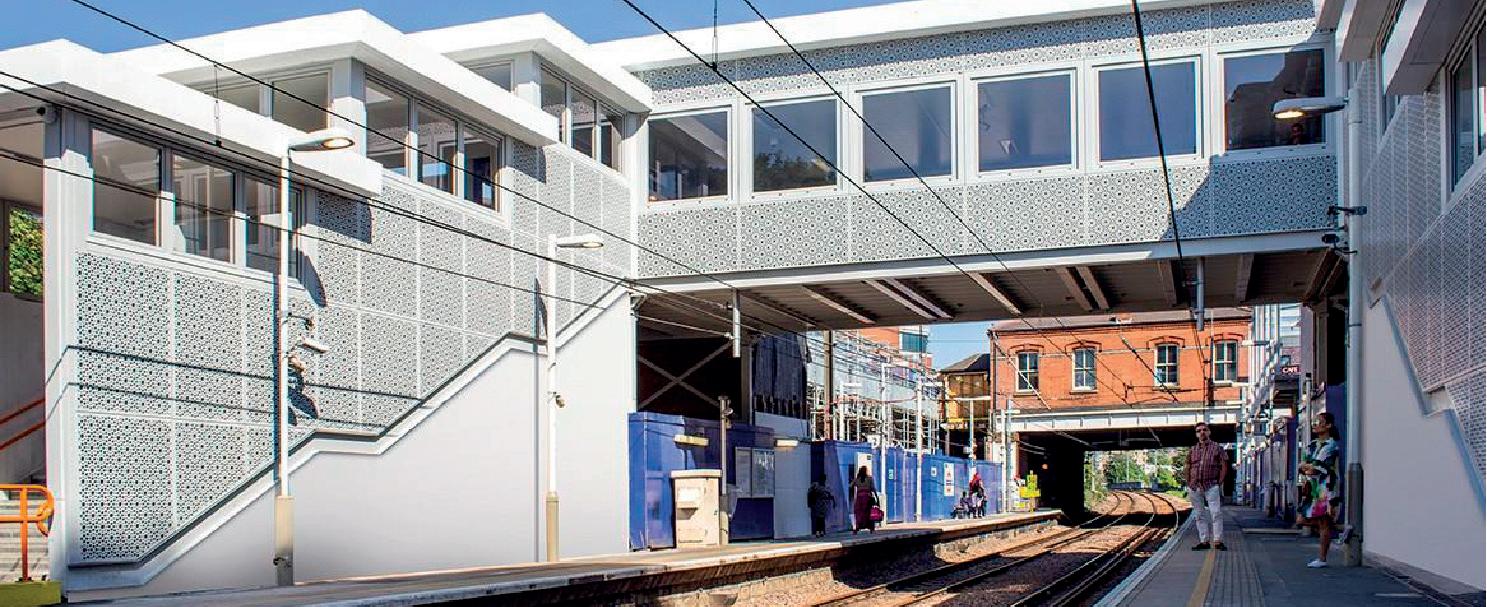
A wide skill set The variety of skill sets that Structural Fabrications Ltd can offer to projects in the rail industry is diverse, with many projects incorporating design development, site surveys, 3D modelling, 2D drawing production, the procurement of materials, steel fabrication, painting, cladding, glazing, installations, maintenance, repairs and more. In addition to these services, the company also supplies specialist PTS staff to the industry, with labour supply available to cover a wide range of operations with very flexible terms.
Structural Fabrications Ltd is a RISQS-approved rail supplier and also holds the SafeContractor accreditation. The firm is also a member of the Register of Qualified Steelwork Contractors (RQSC), CE Class 3 + accredited and a member of the Steel Construction Certification Scheme (SCCS).
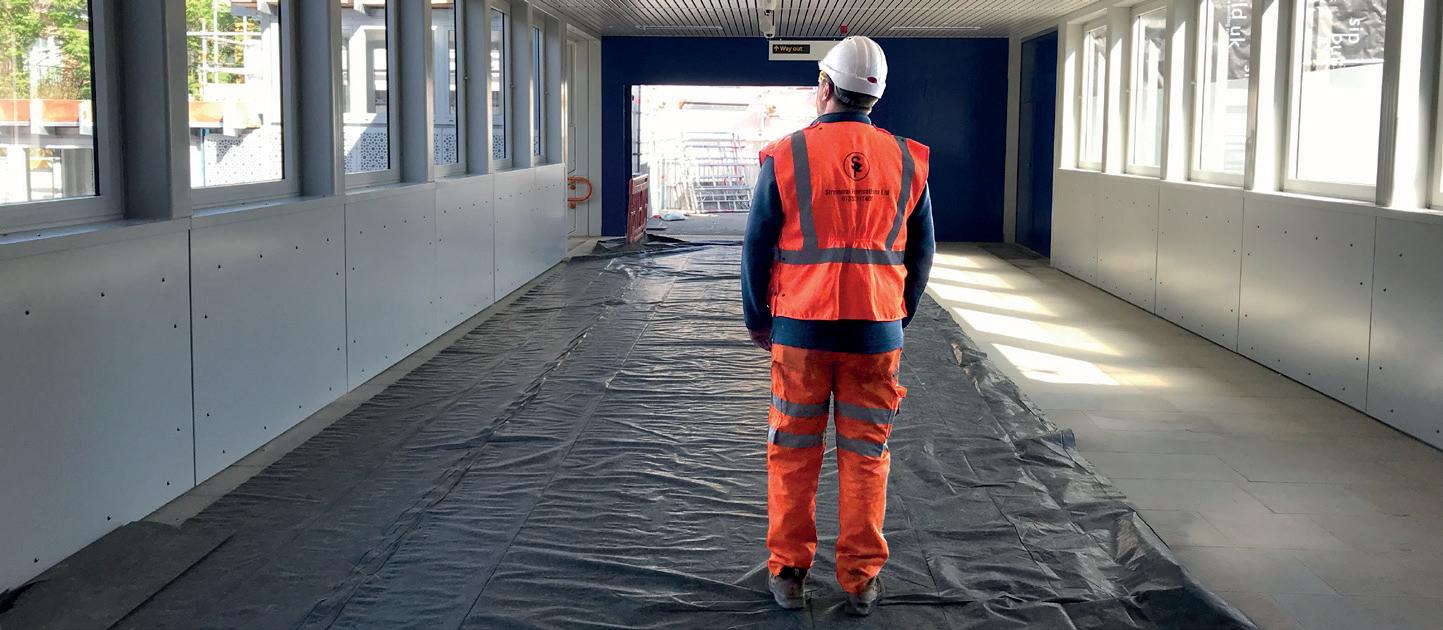
For more information on Structural Fabrications Ltd, call 01332 747400 or visit structuralfabrications.co.uk
