
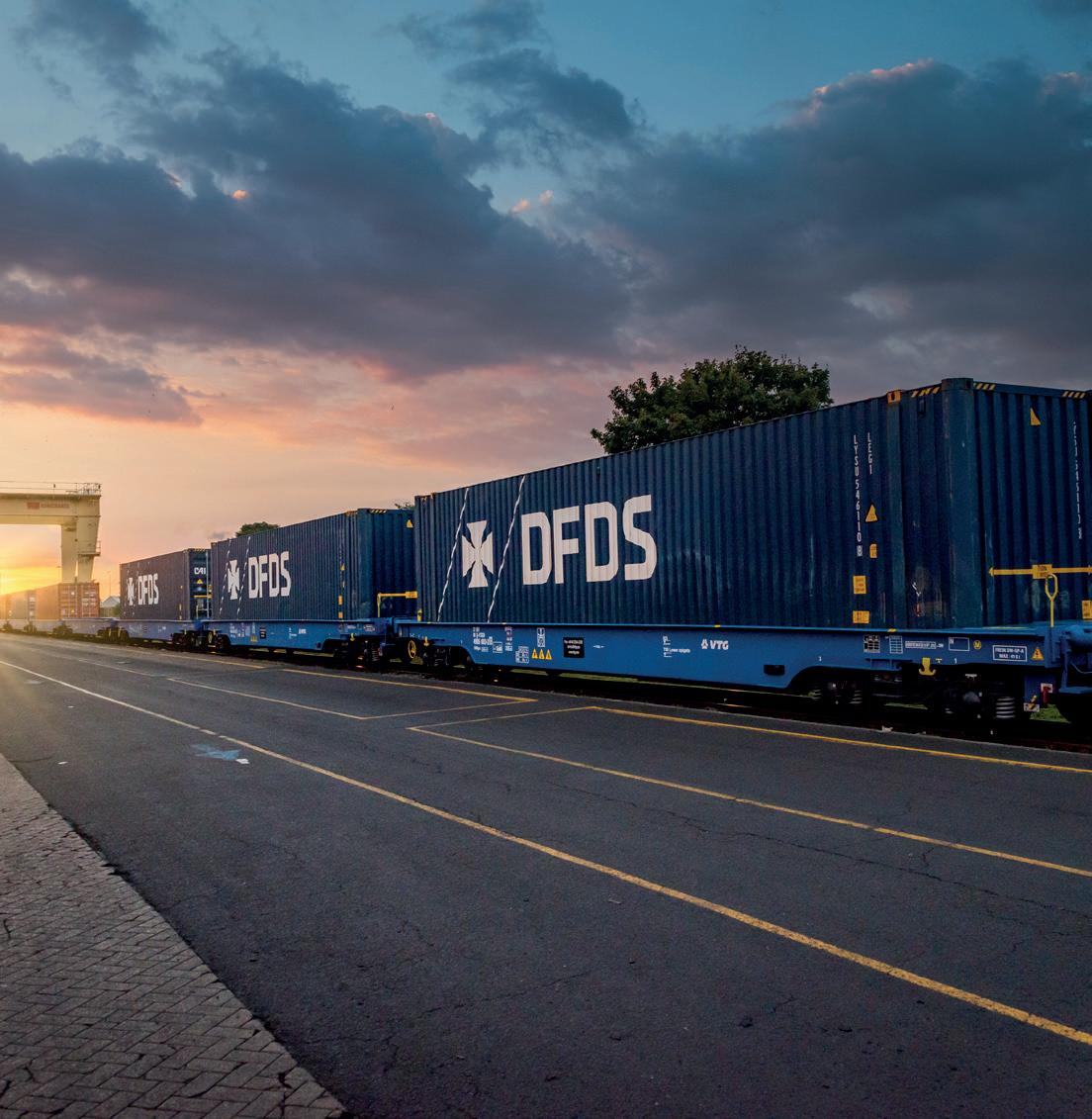
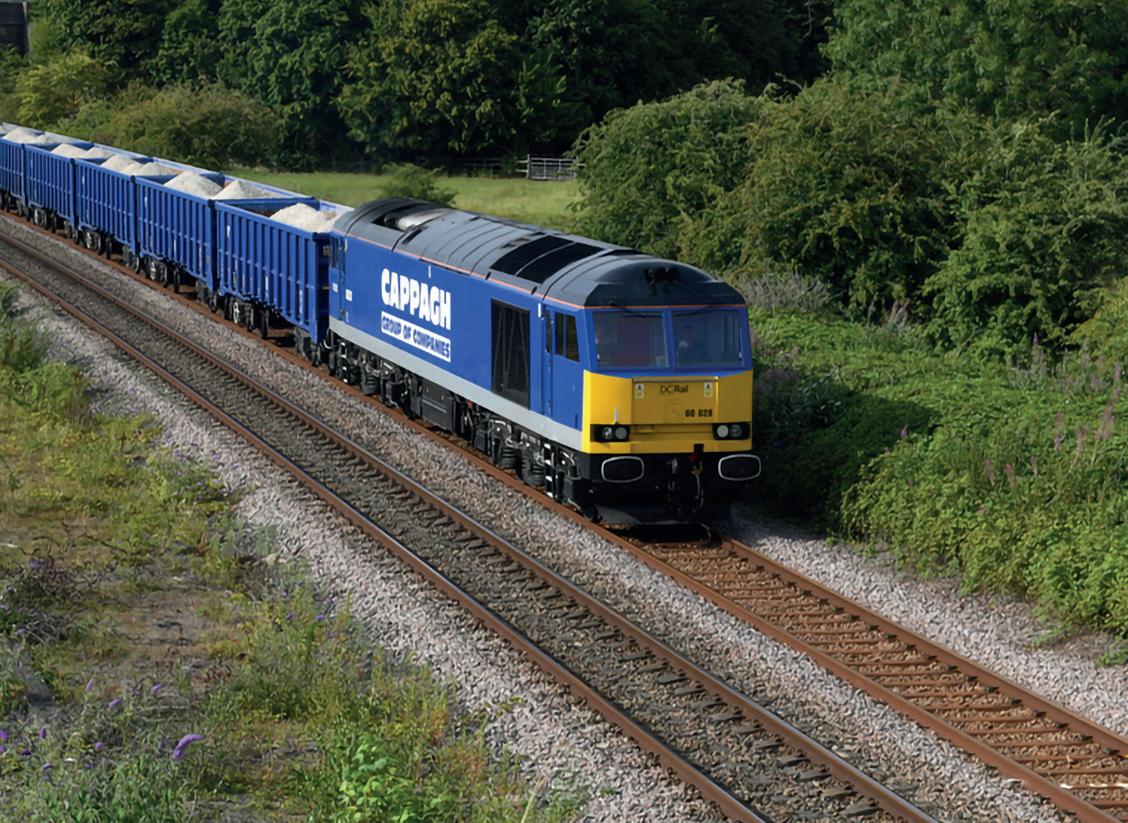


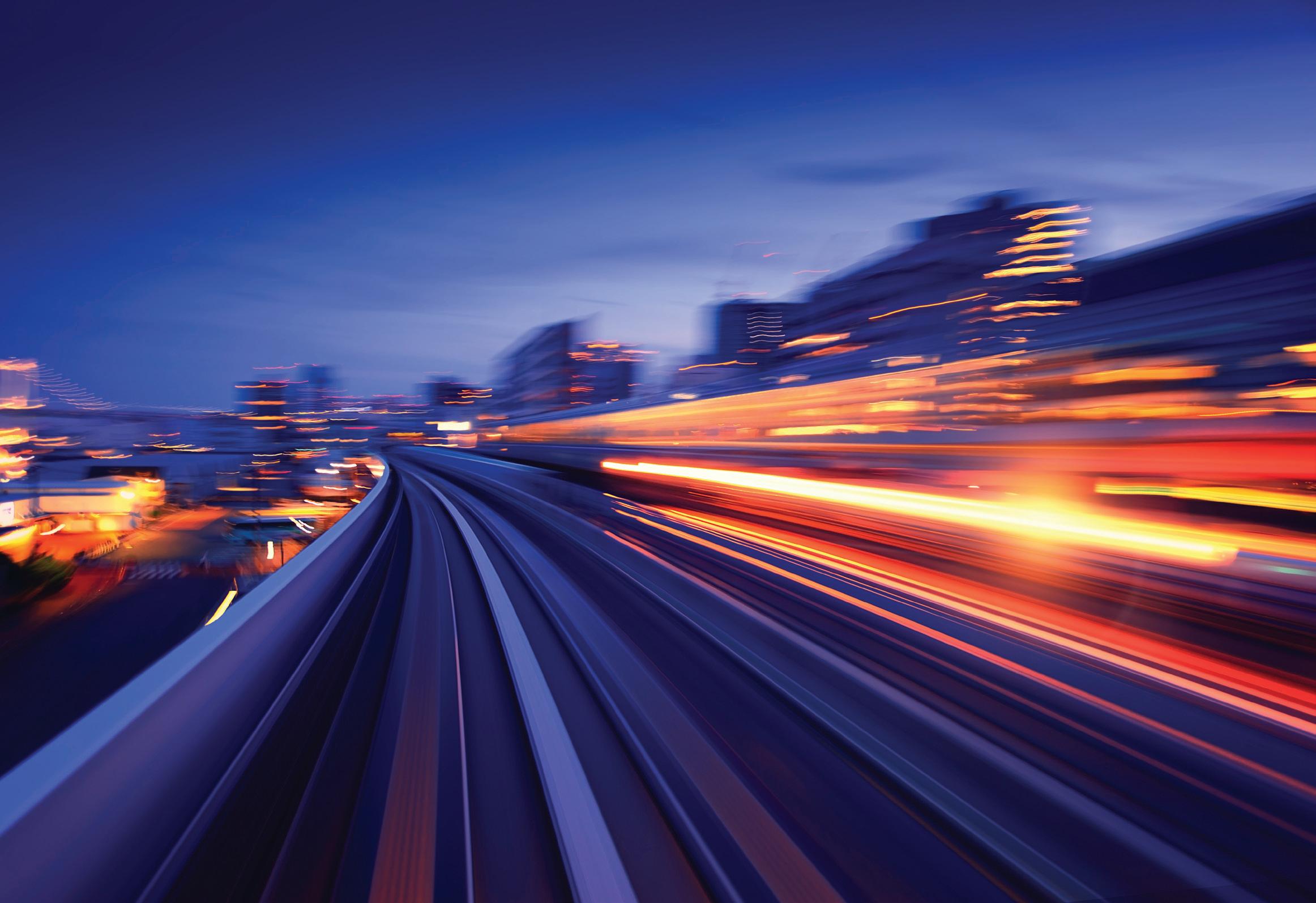
Welcome to Inside Rail Freight 2022, a special edition supplement showcasing some of the collaborations, innovations, and opportunities the UK rail freight market has to offer the industry.
It is no secret that the rail freight market plays a huge role in the UK’s economy, indeed, it currently contributes almost £2.5bn and that figure will only continue to grow each year. Freight transport will also provide a key element of the government’s net-zero strategy, as it helps take lorries off Britain’s roads, reducing emissions.
The Rail Delivery Group has reported that every tonne of freight transported by rail produces 76% less emissions compared to road, while each freight train removes 76 lorries from our roads.
With clear benefits for both the economy and the environment the opportunities for the rail freight market are both vast and exciting. This supplement will provide a showcase of some of the brightest organisations working in the sector, with several interesting initiatives and innovations in the spotlight.
The Rail Freight Group’s Maggie Simpson talks about how the sector can use decarbonisation to target new markets, while Direct Rail Services discusses its collaboration with Tesco in distributing the supermarket’s chilled goods using its refrigerated rail service.
Also in the magazine, VTG Rail UK talks about its innovative wagon tracking technology and DB Cargo’s Marie Hill presents the firm’s Virtual Employee Hub. There are also profiles from upcoming SMEs working in the sector such as Mandy Rail and BaileyRail & Logistics, along with a wealth of other content that will provide a complete insight into the UK rail freight market.
Thanks very much to everyone who has contributed to this supplement. I hope you enjoy reading and if you’d like to see anything included in our future publications do please get in touch.
All the best,
How rail freight rose from coal’s ashes 4
For well over a decade Maggie Simpson MBE has been a significant voice in rail freight. She talks to Inside Rail Freight about targeting new markets as businesses look to decarbonise their supply chains
‘Step change’ for rail as trailblazer refrigeration 6 service launches
Partnership between DRS and Tesco for their trailblazing refrigerated rail service wins national recognition
Thinking outside the box 8
Experts from across the rail freight industry came together for a ‘Human Factors in Freight’ workshop held at Doncaster’s National College for Advanced Transport and Infrastructure.
Study paves the way to make rail freight even safer 10 The first ever collaborative project to chart and share best practice in safe train preparation is underway
VTG Connect ‘light years ahead’ in digitalising 12 freight wagons
The UK’s leading private rail wagon hire company has been recognised for its commitment to revolutionising wagon tracking technology after scooping this year’s Rail Freight Group Award for Innovation and Talent for its VTG Connect offering
How farmers in New Zealand could lead to a 14 step change in rail freight technology DB Cargo UK has created an online platform to revolutionise the workplace experience in rail freight
New kids on the block – the family business 18 that’s on track for success Europe’s biggest infrastructure project has got more than 950 apprentices working on the project. CEO Mark Thurston explains why it is so important the project offers opportunities
Driving the future of freight through innovation 20
Opportunities for growth 22 With a career spanning almost 30 years in bulk freight, and the majority of that time in rail freight and construction, Cappagh’s David Fletcher is an expert in his field.
Brothers in arms 26 Leaving behind the securities of the corporate world and setting up your own company is a brave move
Making light work of weighing 30 Paul Horsfall, inventor of the patented Portable Train Weigher (PTW) describes the origins of the unique product, the benefit to the rail freight industry and future innovations
For well over a decade Maggie Simpson MBE has been a significant voice in rail freight. She talks to Inside Rail Freight about targeting new markets as businesses look to decarbonise their supply chains
AsDirector General of industry body the Rail Freight Group (RFG), Maggie Simpson has had a front row seat in the changes that have massively affected the industry in recent times.
“I’ve seen massive changes in rail freight,” she said.
“When I first started working in this industry GBRf was very much a new kid on the block, the Class 66s were still being delivered at scale and coal was booming.
"I think there were something like 10 trains a day in and out of Felixstowe and now there are 36. London Gateway didn’t exist. The transformation over this time has been enormous.”
Maggie’s epic rail freight journey began at the Strategic Rail Authority. She began working with the RFG in 2005, initially writing policy responses, and then rising through the ranks to lead the team and become one of the most important and respected voices in rail freight in the UK.
“The landscape of rail freight has changed hugely. When I began my career in the industry coal was king,” she said.
“But structurally the rapid death of coal and tax changes in 2015 saw plenty of commentators saying the industry was going to curl up and die.”
What strikes me is that customers have a real appetite to transport their goods on rail. The ambition is there. I think we’ve got an exciting window over the next five to 15 years to attract more customers to use rail.
Maggie Simpson MBE.
But, despite the doom and gloom facing the industry as coal traffic dropped off a cliff edge, rail freight proved its resilience by being agile to attract emerging and new markets.
Maggie said: "The resilience shown by the industry in reshaping to capitalise on the new dominance of intermodal and other bulks in the place of coal meant it didn’t allow itself to curl up and die.
"That resilience has been a real constant thread all the way through and there have been a lot of different changes that have happened over that time."
“Make no mistake about how bumpy the last few years have been for everyone in the economy and these challenges aren’t showing any sign of slowing down any time soon. That’s the real challenge for the industry at the moment, along with industrial relations.”
approved leading to the likes of the 50-acre East Midlands Gateway, which includes a rail freight terminal capable of handling up to sixteen 775m long trains a day, container storage and HGV parking. This leads on to the current developments of SRFIs in the West Midlands and Northampton.
Maggie is confident in the future of rail freight. She said: “What strikes me is that customers have a real appetite to transport their goods on rail.
"The ambition is there. I think we’ve got an exciting window over the next five to 15 years to attract more customers to use rail, and notwithstanding the current economic climate the environmental advantages will keep driving more companies to use more rail freight.”
And what of the digital transformation? What needs to happen to make sure rail freight keeps up?
Maggie adds: “Technology in the industry has to move forward because the railway in general, and freight specifically, is held back by some of the heritage systems. If you’re still planning your railway on systems designed in the 1970s that’s going to hold you back. What we’re seeing is individual businesses making big strides in the next innovations, which is great.”
Rail freight is a very close industry, although different operators choose different ways of working. Should the rail freight industry come together more closely in terms of standards of operations and how would that affect competitive markets?
“I think there’s more that can be done in sharing good practice, so the timetable for example, anything within that space there has to be a systems approach,” Maggie said.
“But on the flip side we always have to remember that this is a competitive industry, collaboration can sometimes mean that a project only moves at the speed of the slowest contributor.”
Partnership between DRS and Tesco for their trailblazing refrigerated rail service wins national recognition
Direct Rail Services (DRS) has scooped two awards alongside Tesco for the introduction of a refrigerated rail service which has been described as a ‘step change for rail.’
It is Tesco’s first refrigerated rail service, distributing chilled goods from Tilbury to Coatbridge by low CO2 rail twice a day, seven days a week.
The service has now been nationally recognised after winning the Rail Freight Group’s 2022 Awards in Driving Rail Freight Growth category and the Freight and Logistics Achievement of the Year at the National Rail Awards.
The RFG judges called the launch of Tesco’s first refrigerated rail service, operated by DRS, as trailblazing, saying that ‘reliably moving chilled produce in large quantities is a step change for rail’.
The judges added that the service would help to drive the whole chilled food market to
increase its use of rail, and the significance of that should not be underestimated.
The 415-mile route uses DRS’s state of the art Class 88 bi-mode electric locomotives which can run on electricity and produce zero exhaust and greenhouse gas emissions. This service alone will take at least 17,000 containers off the road each year, saving Tesco 7.3 million
road miles and nearly 9,000 tonnes of CO2e.
DRS is part of Nuclear Transport Solutions (NTS), a subsidiary of the Nuclear Decommissioning Authority (NDA).
Speaking about the awards successes Seth Kybird, NTS CEO, said: “We’re very proud of this service and the work we’re doing with our customers to introduce new and innovative freight trains to the rail network.
“It’s absolutely fantastic that we’ve been recognised for our efforts and the work we’re doing to promote the use of rail as the environmental choice for big retailers in the UK.
“Each train removes around 40 lorries from Britain’s road network and we’re running two trains a day, seven days a week. But the journey doesn’t stop here as we continue to encourage the use of rail freight for retailers across the country.”
David Peattie, NDA CEO, added: “This is wonderful news for Direct Rail Services and extremely well-deserved recognition.
The journey doesn’t stop here as we continue to encourage the use of rail freight for retailers across the country.
Seth Kybird, CEO, Nuclear Transport SolutionsDRS 88010 intermodal service resplendent in specially commissioned ‘fridge wrap’ passes Golborne Junction on route from Daventry to Mossend
“DRS plays a crucial role in the NDA’s mission, safely transporting materials across the UK, and offers world-leading and innovative rail operations for Tesco, keeping the supermarket shelves full, all while supporting our carbon net zero ambitions.”
All rail freight delivers 76% fewer CO2 emissions when compared to road; linking with other rail operations from across Europe at Tilbury Forth Ports ensures that fresh produce can travel with a significantly reduced carbon footprint.
DRS was established in 1995 as lead supplier of rail transport and associated services to the nuclear industry and it is a wholly owned subsidiary of the NDA. In 2021 Nuclear Transport Solutions was formed as a centre of excellence for nuclear transport, packaging and logistics expertise, which operates DRS and Pacific Nuclear Transport Ltd.
DRS also provides market-driven solutions to domestic intermodal transport, rail infrastructure support and asset hire market sectors. It operates throughout Great Britain at more than 20 locations with its head office based in Carlisle, Cumbria.
The event was hosted by Newcastle University, the National Freight Safety Group (NFSG) and the Rail Safety and Standards Board (RSSB) who are collaborating to deliver risk management and insight into safey and performance in the UK’s rail freight yards.
The work aims to understand human factors influencing freight train preparation and the Condition of Freight Vehicles on the Network (CFVN). Building on recent work on site complexity, wagon maintenance and freight planning, the workshop aimed to capture the human challenges and solutions for safe and high-performance freight operations, with the aim of leading the sector’s collaborative approach to reducing and mitigating freight derailments.
Addressing the audience, David Ethell, of the NFSG, said: “Today’s workshop is an information gathering exercise. We’ve got some hugely experienced rail freight people in this room, some of the best talent in the industry to help us take this forward.
“This workshop will cover the tasks of train preparation, the difficulties involved, as well as discussing examples of good practice and effective working.
"We will also discuss the factors around a site that can increase the complexity of work, for example the number of moves within the yard and the type of freight managed.
“The industry needs to better understand the role of the people working at the front end of operations for these amazing trains that we run, the ground staff and the wagon fitters. Their role has changed massively in the last five to 10 years, they’ve gone from predominantly working at the same depot preparing coal trains to, in many cases, becoming mobile operatives working at a range of different sites with a variety of goods carried, at all times of the day and night and in all weathers. They have a complex role which demands that they make quick decisions.
“There are approximately 200,000 train movements a year across the UK but just one incident can ruin the whole rail network for at least
Lonergan, Lead Human Factors Specialist at RSSBa while, and mostly importantly, put people at risk.
"Each freight operating company has a slightly different method of working and training module.
"What we want to see come out of our work with Newcastle University and the RSSB is the development of a new collaboratively agreed rail industry standard for train preparation activities in the form of an NVQ at level two or three. This will ensure a standardised way of working across the industry.”
The specific objectives of the day were to validate, through structured activities:
1. A process map of the rail freight system – capturing the upstream influences and downstream impacts of performance in the freight yard;
2. A structured set of human factors and human performance issues in the freight yard aligned to the process map;
3. Potential system-level solutions to deliver safety, performance and well-being in the freight yard.
James Lonergan, Lead Human Factors Specialist at RSSB, facilitated the day alongside David Ethell. He said:
“When we speak about human factors the overriding areas must always be around safety and well-being. When you get the working environment right for the person on the ground this also contributes to performance, satisfaction in their role and inclusivity.
“There are also easier things to put right, does that person have adequate PPE? Is there enough lighting for someone to be able to do their job properly in the middle of the night? What are the facilities like for break times?”
When we speak about human factors the overriding areas must always be around safety and well-being. When you get the working environment right for the person on the ground this also contributes to performance, satisfaction in their role and inclusivityJames
James also spoke about how outside factors could affect work force performance and that organisations should be looking at how to help their colleagues with issues that could affect their well-being, for example worries over the current cost of living crisis.
“We are looking to gain a strong understanding of the processes that affect work in the freight yard,” he said. “We’re looking at the roles of people, processes and technology and then we will start to map the human factor challenges, not just in the yard but in other parts of the system that may increase the likelihood of unsafe working practices. Let’s think outside the box and think about systems-level solutions including data, processes and, most importantly, collaboration across the industry.”
The joint work being undertaken by Newcastle University and conducted by Dr David Golightly, Lecturer in Human-Systems Integration, the NFSG and RSSB is running in tandem with the Condition of Freight Vehicles (CFVN) project which is endorsed by the ORR and RAIB. It is funded by Network Rail’s £22m FNPO Safety Improvement Programme (FSIP) – and has been
The workshop aims to capture the human challenges and solutions for safe, high performance rail freight operations.
developed to bring the freight industry together to look at processes for train preparation, wagon maintenance and the important role human factors play in performing safety critical tasks to reduce risk and improve performance across the network.
The results of the workshop in Doncaster will be shared with all delegates and opportunities for change will be available as a report and at a ‘Human Factors for Freight’ Information Day planned for early 2023.
railbusinessdaily.com/rbd-publications/
READ THE LATEST EDITION ONLINE NOW
The standardisation of train preparation, wagon management and maintenance processes is at the heart of a new study which aims to reduce the risk of freight vehicles entering the network in an unsafe condition.
The Condition of Freight Vehicles on the Network (CFVN) programme launched at DB Cargo’s Margam depot in March 2022 and moved to its second focus site at Freightliner’s Basford Hall marshalling yard at Crewe in September. The project findings will lead to the introduction of a new rail industry standard for the safe preparation of freight trains across the UK’s rail freight industry.
Funded by Network Rail’s £22m FNPO (Freight and National Passenger Operator) Safety Improvement Programme (FSIP), the project is endorsed by the National Freight Safety Group (NFSG), Rail Accident Investigation Branch (RAIB), the Rail Delivery Group (RDG) Freight Board and the Office of Rail and Road (ORR).
With thousands of rail freight wagons and hundreds of freight train services delivering vital goods throughout the UK and beyond each day, the overwhelming majority of freight vehicles travel on the network without incident.
David Ethell, Independent Project Manager for the National Freight Safety Group (NFSG), which oversees the CFVN programme, said: “The FOCs have been working with industry colleagues to continually reduce risks associated with rail freight on the network for some time.
"This is a sector wide project looking at learning and sharing good practice from across all the freight operating companies in Britain, to find where improvements can be made so we can introduce one common industry standard for the safe preparation of freight trains and vehicles.”
Data analysis by Network Rail, freight operators and the Rail Safety and Standards Board (RSSB) has shown that a significant number of delays on the network related to freight are due to wagon defects. If undetected, these defects have the potential to cause delays and safety risks to rail traffic. Data reviewed between 27th March 2022 and 30th September
2022 showed that 121 freight trains were stopped on the network with more than 50% reported as brake system fault related.
David said: “The maintenance of freight wagons to prescribed standards and the safe preparation of trains by competent staff are fundamental requirements of operating a safe freight railway. Data from RSSB, Network Rail and freight operators has highlighted that vehicle preparation and condition is a regular precursor factor in safety incidents occurring to freight trains whilst traversing the network.
“By resourcing the CFVN workstream with support from NFSG, the ORR and Network Rail, the freight industry is able to collaborate and build understanding of the factors impacting this risk.
"Our key purpose is to reduce the risk of vehicles entering the network in an unsafe condition and ultimately reduce the risk of freight train derailments.”
The CFVN team spent 15 days at DB Cargo’s Margam freight yard – one of the company’s busiest sites where on average around 40 freight trains arrive and depart the yard each day. They focussed on work planning, site complexity, wagon condition and human factors. Dougie Hill, chairman of the NFSG, told DB Cargo maintenance and engineering staff: “We need to start listening to you.
"You are the experts on the ground doing this job day in and day out.
"Your expertise is absolutely critical to the safe delivery of operations for freight trains. If we’re going to continually make improvements, we need take your knowledge and experience and put it into the mix.”
Marc Binney, Head of Safety for DB Cargo UK is keen to point out that this is not a finger pointing exercise.
He said: “This is a project incorporating all the rail freight operators where we are looking at things collectively to find what we can do better together as an industry.
"When I look at the other freight operators, I see that we are all doing some train preparation and processes slightly differently so this project
The first ever collaborative project to chart and share best practice
This is a sector-wide project looking at learning and sharing good practice from across all the freight operating companies in Britain, to find where improvements can be made so we can introduce one common industry standard for the safe preparation of freight trains and vehiclesDavid Ethell, Independent Project Manager for the National Freight Safety Group.
is looking at how we can introduce a cohesive industry wide standard.”
Jess Lippett, Senior Regional Freight Manager at Network Rail, said: “As an industry we are at our strongest when we work together, share best practice and ideas for an even safer railway.
"It’s crucial to team up with our partners across the rail freight industry for this important project and the enthusiasm from everyone has been phenomenal.
"The CFVN project will give us vital data and insight to feed into the first industry-wide standard for the safe preparation of freight trains. It is ground-breaking and will lead to building even better standards for the future.”
The project team relocated to Basford Hall in early September and will be confirming a third study site towards the end of the year.
Geoff Spencer, Chair of the National Freight Safety Group Steering Group (NFSGSG), which oversees the CFVN programme, explains why the Freightliner site was selected.
He said: “Basford Hall is a busy local distribution centre (LDC) and is a multi-user site for a number of freight companies. It’s important
to look at a site like this because it gives us on the ground opportunities to see how operators are currently doing things differently.
“The focus areas for the Basford Hall safety project centre around train planning, shunting operations, human factors, and marshalling trains as well as the inherited negative impact on site capacity. The ground staff at Basford Hall interface with assets and infrastructure within various environments and these have been openly discussed and observed by the team.”
Jimmy Pettitt, Freightliner’s Head of Operational Safety, is keen to see the introduction of standardised tasks across
the industry including better controls and equipment, improved walkways and lighting, and a better understanding of the minimum time needed to carry out wagon preparation.
He said: “Freightliner welcomes the CFVN project because it sees the rail freight industry working together to further improve standards to the highest level. One of the important things for me about this project is that we are giving the ground staff a voice. They are the experts in train preparation and we need to listen to them. They’re doing this task day in and day out so we need to make the task as safe and efficient as we can.”
VTG
Rail UK is actively harnessing the future’s technology for today’s rail freight through a number of innovations and technological developments.
Defined by judges of this year’s Rail Freight Group awards as being ‘light years ahead of other software projects’, VTG’s investment in VTG Connect is part of the company’s commitment to revolutionising the way information is gathered about wagon condition, status and location.
Digital wagons fitted with telematic systems are an essential and integral part of this vision. Indeed, every wagon in VTG’s entire European fleet is being fitted with telematic technology to make rail the backbone of smart, sustainable logistics.
Giving the best view on your freight Sam Hunt is the Project Engineer in charge of the VTG Connect programme in the UK and said: “VTG Connect gives our customers eagle eyes on their wagons, freight and transport chain by providing sensor-enabled data analysis of freight wagons.
"It allows customers to pinpoint the exact location of a wagon at any given time, track its performance and receive data such as what time it departed and arrived at its destination, and whether it was stationary for a period of time and where that was.”
In the past, VTG Connect has even been used to identify where along a journey a wagon was graffitied. This was achieved by analysing the journey to determine where the wagon was stationary for an extended period of time and allowed the customer to tighten up security measures within the area.
It also allows customers to intelligently use data from digital freight wagons, establishing tracking and tracing, shock monitoring and environmental temperature measurement.
In the future, it is hoped VTG Connect could be used for custom-specific applications and be connected to individual hardware solutions that add extra functions such as weight measurement and lock monitoring. These are a few of the additional innovations that VTG is currently working on.
Sam added: “VTG Connect can generate reports on the mileages of individual wagons and the overall fleet.
"This invaluable information can then be used to implement more intelligent maintenance regimes because it can be determined exactly how many miles a wagon has done and so when it is due for service, allowing for proactive plans to be made as to when wagons should be taken out of the field for mechanical review.
“By allowing customers to keep connected to their wagon, freight and entire transport chain at all times, they are able to implement more robust processes for smooth operations. We believe that digitising wagons from end to end is fundamental to keeping rail freight competitive as a mode of transportation.
"They are a crucial factor in enabling us to give our customers innovative services that make their logistical processes and collaboration with rail carriers more efficient.”
VTG provides the UK's most comprehensive fleet of purpose-designed and built rail vehicles on flexible leasing arrangements. Its fleet now comprises around 4,200 wagons, including a ‘standard freight’ sector for dry and solid products, a tank sector for petroleum and chemical products, plus an intermodal sector covering a comprehensive range of container platforms including the award-winning Ecofret, and Megafret platforms suitable for international traffic via the Channel Tunnel.
The UK’s leading private rail wagon hire company has been recognised for its commitment to revolutionising wagon tracking technology after scooping this year’s Rail Freight Group Award for Innovation and Talent for its VTG Connect offering
VTG Connect gives our customers eagle eyes on their wagons, freight and transport chain by providing sensor-enabled data analysis of freight wagons
The programme to equip all VTG UK wagons with Connect is in full swing with over 2,000 vehicles already fitted with the technology. New wagons are added regularly to meet emerging market demands and specific customer requirements as part of a continuous improvement and replenishment process.
In addition to its ground-breaking Ecofret wagon, saving money by eliminating wasted space on maritime intermodal trains, VTG has also received industry awards for its introduction of high efficiency, aluminium-bodied cement
wagons, plus the first fleet of UK biomass wagons. The company has led the industry in repurposing redundant coal hoppers, optimising them for aggregates traffic following the downturn in the ESI coal market.
Sam concludes: “Rail freight in the UK has a critical role to play in the move to overall carbon reduction and the drive to deliver more goods by environmentally friendly means. VTG Rail’s innovative work with its customers will ensure it remains at the forefront of this evolving and dynamic sector.”
The VTG Connect hardware is riveted to the wagon superstructure, preferably to the solebar. The device is then paired to the wagon via a pairing app. Solar cells combine with a built-in battery to guarantee a stable power supply.
The wagon’s current position is regularly determined via satellite receivers (GPS, GLONASS, Galileo and BeiDou). Data is transmitted via the mobile network. During normal operation, the data is updated every five minutes and the location can be accurate down to one metre.
Secure (ISO 27001-certified) data centres receive data packets from the wagons, analyse them and transform the data into useful business information. This is then made available on a protected online portal or via data interfaces.
Marie Hill, DB Cargo UK’s Chief Transformation and Digitalisation Officer, is on a mission to create and introduce technology that will revolutionise ways of working in rail freight.
Earlier this year, Marie was placed 15th in the CIO 100 UK, which recognises the most transformational CIOs (chief information officers) across all industries and sectors. The CIO 100 celebrates technology and business leaders who are driving change in their organisations and is a showcase of the achievements of those executives and their teams.
Marie became a permanent member of DB Cargo UK’s board in 2019, having previously been the company’s Head of IT. She has always had a passion for embracing and driving technological change to benefit both the organisation and its employees. The latest ground-breaking technological innovation that she and her team have been leading on is
the creation of a Virtual Employee Hub, something inspired by an article Marie read regarding an app that had been created for farmers in New Zealand.
Marie said: “I learned about farmers in New Zealand who can use an app with inbuilt GPS info, so if they’re in a certain location they know whose farm they are on. If they cross the boundary onto another farm, it provides the contact details for the manager of the farm
as well as alerting the user to any potential hazards on that site.
“It was a lightbulb moment. I thought, how applicable this could be for rail freight yards and the industry as a whole.”
That’s when Marie’s concept for the Virtual Employee Hub was born: an app that can be used to give vital information about a site or methods of working that can be accessed 24/7 at the touch of a button.
Marie added: “One of the things I’ve liked to do over the last couple of years is to experience what our employees do day in and day out.
"For example a ground staff member - what is their day like?
"In order to produce technology that can help make their job easier, and their experience in the job better, I needed to be able to know, at least for a short while, what it felt like to stand in their shoes."
It was a lightbulb moment. I thought, how applicable this could be for rail freight yards and the industry as a whole
Marie contacted the digital agency in New Zealand which built the farmer’s app to discuss how they may be able to work with DB Cargo UK to create a similar, innovative solution which would work, initially, for DB’s operational staff. The brief was to use technology to streamline processes and make working lives easier for DB Cargo UK colleagues by introducing a centralised ‘one-stop shop’ where all documents and forms relevant to their role could be accessed easily and directly from a tablet.
What you want, quickly
“If you’re looking for information that takes more than one or two clicks to find then people just aren’t going to bother going any further,” Marie said.
“We’re conditioned by our online habits at home, you can shop for what you want online easily and quickly.
"That’s what today’s, and tomorrow’s workforce expect at work too and at DB we are investing and striving forward to make sure our tech is the best that it can be for our people.”
The Virtual Employee Hub has been developed using feedback from within the business and was initially targeted at drivers and ground staff. Following on from the original concept, plans are in place to continue developing the platform to provide enhanced
features such as communication channels, workflow and shift management, incident reporting and safety guidelines, adding value to more areas of the business.
"The technology is the easy part. What we’re doing here has been done in other industries separate to rail freight, but there is something to be said for designing your own tech, bespoke to your needs.
"For me, this whole concept is a lily pad, it’s a window and a stepping-stone that can link every area of information that you need to do your job."
The Virtual Employee Hub's key features include:
Automatically displays documents relevant to a person’s job which will save them searching for the correct document each time
The ability to complete and submit forms
Quick links for access to external sites
Quick links to the HR SharePoint site allowing easy access to HR Polices, HR forms as well as DB Cargo UK Health and Wellbeing resources
Marie said: “The backbone of this is technology but the Virtual Employee Hub should never feel like it is being run by the tech. It should become a way of life, a way of working.
One-step uniform ordering
Route and skill signing module
We’re conditioned by our online habits at home, you can shop for what you want online easily and quickly. That’s what today’s, and tomorrow’s workforce expect at work too and at DB we are investing and striving forward to make sure our tech is the best that it can be for our peopleMarie Hill, DB Cargo UK’s Chief Transformation and Digitalisation Officer
Rail freight operators are in prime position to take advantage of the push to switch freight from road to rail.
Whilst it is unclear when the legislation for Great British Railways (GBR) will pass, there is a GBR freight transition team in place which has been outlining its plans to make GBR freightfriendly. Moving more freight by rail will reduce dependence on road transport, thereby reducing emissions and congestion.
UK Rail Leasing (UKRL) is playing its part in the rail freight sector’s success, providing vehicle engineering and maintenance and is working in partnership with market leading freight operators and train manufacturers, in addition to national and regional passenger train operating companies.
Rail freight operators need a capable engineering and maintenance partner to guarantee safety and reliability. UKRL is that partner, offering engineering services, maintenance and servicing, operating from fully equipped workshops at spacious mainline connected maintenance depots. UKRL provides anything from full vehicle overhaul, through to daily cleaning and fuel point exams and servicing.
Darren Sharpe, operations director at UKRL says: “I think it’s important to say that we have been successful not just because of first class facilities, but because the rail professionals within the UKRL delivery team is second to none. They are hugely experienced and are not easily daunted, primarily due to the fact that they have tackled most problems in their long careers.
Innovation is rooted in this combined experience and it’s the key to effective problem solving.”
The company, founded in 2013 when it took over the Leicester depot, has grown quickly. Utilising well located facilities and experienced staff, it is ideally placed to respond to the growing demand for rail vehicle engineering and maintenance services. In Leicester, UKRL has made a multi-million-pound investment in a modern Traincare and CET facility which is now used by regional train operators.
UKRL will also soon be breaking ground on a new purpose-built maintenance shed in Leicester; a further £1.5M investment in the site supported with a development loan from HSBC. The new shed will consist of a 4 bay, 2 pitted road, maintenance facility with overhead cranage and static 25Kv OHL test capability. This will allow
UKRL has also expanded beyond Leicester and has agreed a 14-year long-term lease for the rail connected buildings, on the former Brush Traction site at Meadow Lane. The historic Loughborough site was established in 1865 and seen locomotive manufacturing for more than 150 years. Loughborough’s extensive repair, overhaul and test facilities give UKRL the ability to offer significantly increased capacity and Level 5 services to the rail operators.
Mark Winter, managing director said: “With the rail industry seeing an ever-decreasing capacity challenge, we are helping our growing customer base with the addition of the Loughborough facility. The new maintenance shed in Leicester will also give us extra capacity. We have also been expanding our commercial and track side services throughout the UK in response to increasing demand.“
“Whether it’s engineering, modifications, obsolescence management, spares and repairs or Traincare services, we will know exactly what’s needed at every stage of a project. We can also provide bespoke solutions to meet new challenges and maximise the useful life of rolling stock, which is what our customers want now.”
If you are looking for rail vehicle engineering or rail maintenance? If so, contact: Darren Sharpe, Operations Director or Chris Moss, Sales Manager 01162 622783 or info@ukrl.co.uk
In only its third year of trading, Mandy Rail is celebrating after winning another major, long-term maintenance contract.
It is the latest success for Mandy Rail, which was founded in 2019 by Mark Hedley and Andy Hird – hence the name Mandy Rail. Their company has gone from strength to strength since then and now employs 20 staff responsible for the maintenance, repair and overhaul of freight wagons, alongside an experienced back-office team.
Mark and Andy met working in the industry
where they gained invaluable experience before deciding to take the leap of faith and start out on their own.
Mark said: “I have three young children, but I didn’t see starting our own business as a risk at the time because me and Andy knew we were good at our jobs and that we could make a success of it.
“Three years on, we’re very proud to be building a family business. Andy’s dad is our finance director, my wife works with us, as well as my brother and Andy’s brother.
RAILLY
NOBODY BETTER Our websites win you work
in SEO to increase visibility
years of rail industry
value and creativity guaranteed
We don’t want to be a big corporate, we want to keep our company built on family traditions, in fact one day I’m hoping my kids will join the firm.
Rail.
"We also have two more father and sons working in our operational team and we’re very proud that the dads are teaching their sons their trade.
“So it’s very much a family affair and that works for us. We don’t want to be a big corporate, we want to keep our company built on family traditions, in fact one day I’m hoping my kids will join the firm.”
Their HQ is in Durham, but they also expanded this year to open a Doncaster office to oversee company activity across the UK. The Touax contract brings to a close a fantastic year for the company with highlights including Mandy Rail signing a contract with Britain’s largest wagon leasing company, VTG Rail UK, in the summer, to maintain its 50-strong IIA hopper wagon fleet running out of the Port of Tyne.
Mark Hedley said: “It’s absolutely fantastic that Mandy Rail has won this new business. Contracts such as this bring continued stability
and allow for further growth. Mandy Rail is a close-knit team, and I am delighted for everyone who works with us as we continue to build our company’s presence and excellent reputation in the market.”
Andy Hird added: “Our successes in our first three years of trading is proof that hard work pays off. We’ve got a fantastic team behind us
and a great vision as to how we will continue to build Mandy Rail by providing the highest quality in maintaining freight wagons to keep Britain’s wagons rolling. The future looks bright and very exciting.”
Cédric Scheiffer, Touax’s maintenance organisation manager of the fleet of wagons, said: “Mandy Rail is a maintenance supplier committed and motivated to build with its customers maintenance solutions and services allying with availability, reliability and quality. Touax Rail was one of the first to trust Mandy Rail and today, this contract signed is the proof for the future, that Touax believes in the team and its capacities to maintain Touax wagons in the UK.”
Mandy Rail is an independent company which provides freight wagon maintenance, repair and overhaul. The company prides itself on developing partnerships with its customers such as Entities in Charge of Maintenance (ECMs), wagon owners and leasing companies by building on sound foundations in accordance with established Railway Industry safety standards and regulations that keep the railway safe.
We have all experienced a seismic societal shift in the past few years. From the way we travel, to the integration of remote working and a shift in the way in which we shop, moving away from bricks and mortar to e-commerce models, there is no denying that we live vastly different lives to those of five years ago.
Whilst teams are returning to the office, more people are working from home which means less commuter travel. More people are buying goods online, which means more items need transporting.
This means that for the rail industry there is the potential to run more freight trains and promote modal shift – i.e., place more containers onto trains. This benefits the UK by removing heavy goods vehicles (HGVs) from our already congested road network, reducing the carbon impact of transporting container freight by road, and increasing the profitability of the railway.
Promoting modal shift and a greener future Rail freight contributes almost £2.5bn to the economy, playing a big part in reducing congestion and emissions and is more environmentally friendly than road.
According to the Rail Delivery Group, every tonne of freight transported by rail produces 76% less emissions compared to road and each freight train removes 76 lorries from our roads.
This in turn reduces carbon emissions and congestion, freeing up capacity across the transport network and improving air quality.
The green benefits of rail freight are being driven heavily by the Department for Transport (DfT) with incentive schemes such as Modal Shift Revenue Support (MSRS) - a £20m grant, which freight carriers can bid for a share of to support the modal shift to rail.
However, despite the widescale use of MSRS, finding new freight routes for additional trains can be challenging due to a multitude of factors, including:
Road haulage is seen as easier and more accessible than rail freight, especially at short notice, for short journeys and for single containers.
Highways are less regulated with no significant barriers to commercial participation, and therefore are free to use the latest technologies to develop and evolve solutions at a faster pace.
Railway planning systems and processes limit the availability and visibility of freight paths resulting in under-utilisation of network capacity.
Freight trains that already run on the network are not always full, which promotes the view that there is no demand for using rail as a viable freight option.
The network appears congested because of the way freight timetabling works, i.e., there is no incentive to remove paths that are not going to be used, and no penalty for not doing so.
The aim is that this will provide Network Rail and freight operators with a more realistic view of operations and available capacity
PathPlanner: technology designed to drive the freight industry forward 3Squared has developed PathPlanner, an innovative software solution designed to help freight operators run additional trains. It does this by utilising over seven years’ worth of historical train records to help planners quickly identify available paths which can be bid to Network Rail through the Very Short-Term Planning (VSTP) process – therefore allowing them to take advantage of much-needed spare, and potentially wasted, capacity. But we haven’t stopped there.
3Squared has been collaborating closely with partners across the supply chain – including Network Rail, Logistics UK, Maritime Transport, Rail Freight Group, Solent Stevedores, GB Railfreight (GBRF) and Eddie Stobart Logistics – to better understand how we can harness technology to help rail freight become a viable alternative to road.
Utilising this knowledge, we developed a Proofof-Concept “Train Capacity Management” portal within PathPlanner to help operators fill trains that have space on them. The system provides a realtime data exchange between railway and logistics systems to surface the required operational information. Operators can identify available
space on freight trains and book a container onto the train at short notice - typically within a couple of hours of the train’s departure – with sufficient time to locate the container and load it onto the train.
PathPlanner is a critical innovative solution we are working hard to make available to support the drive towards modal shift, moving freight from road to rail and supporting the industry’s aim to be more responsive by applying technology to realise the potential for future freight recovery.
In 2021, Network Rail completed a £17m upgrade around Southampton to enable longer trains in and out of the docks. Poised to end in April 2023, Solent Stevedores is now investing to strengthen its capability to receive and dispatch longer trains (from 520m to 775m) and more trains (from nine to 16 per day), culminating in more capacity which needs to be filled.
However, there is no visibility of current available capacity in and out of the port, so Solent Stevedores is currently unsighted as to how, or if, it can find the additional paths. This is where 3Squared comes in.
Having already completed the Proof-ofConcept “Train Capacity Management” solution at Southampton Western Dock, we are now working on a “Network Capacity Management” solution which will help to highlight freight paths in the timetable that are not going to be used.
The aim is that this will provide Network Rail and freight operators with a more realistic view of operations and available capacity.
Analysis shows that c.50% of booked paths are not actually used but remain in the timetable, which presents a bloated network.
Through harnessing new technologies and innovations, we can identify where the opportunities lie for the freight market, create a roadmap on how to capitalise on these opportunities and embrace making a greener, positive change for the future.
For more information on how 3Squared can support you with your freight planning needs, get in touch with Jason Durk, Principal Consultant via hello@3Squared.com www.3Squared.com @3Squared
Most industries remain agile to survive, sometimes vastly changing their offering to respond to market demand. Rail freight is no exception.
For almost 200 years, dense, heavy goods were the main products moved by rail, and as the markets have changed over the last decade there was an inevitable shift in the types of goods moved.
But David Fletcher, Director for Rail at Cappagh Group of Companies, which includes freight operating company DCRail, said that the opportunities and growth areas for rail freight in transporting materials for construction are as strong as ever, and what’s more, there is traffic that can be won back.
“Transporting materials by rail has been a great success, but the industry certainly can’t allow itself to become complacent in this. We have to keep moving forward,” David said.
"Greater access to the network and more freight sites in urban areas are key to this," he added.
“We must protect what we have now and be able to build upon that. The external pressure
that we currently face is that the UK has a very busy railway network, and we need more land to be made available for freight in urban areas in order to be able to deliver bulk materials as
close as possible to where they are needed for regeneration and building projects.
“Rail has been really good at moving dense products for the last 200 years. Originally of course this traffic was built on coal, but there is still a significant amount of heavy product that can be moved by rail.”
David said the industry can focus on what it is good at. Until recently, regular traffic included other heavy building products, with little of these moving by rail now:
Bricks – 4m tonnes are produced in the UK each year
Timber – 18m m3 used in the UK
Blocks, paving, precast – 14.5m tonnes Steel, glass, whiteware and tiles
“My view is let’s try to get some of these dense bulk products back on to rail in large volumes,” David said. “There are logistical challenges but many were moving by rail until relatively recently.’’
With a career spanning almost 30 years in bulk freight, and the majority of that time in rail freight and construction,Cappagh’s David Fletcher
is anexpert
in his field. He spoke to Inside Rail Freight about the opportunities and growth areas that he sees for rail freight in construction
I believe that freight being allowed 24/7 access to the network could be the answer, allowing us to move goods when passenger trains are at their quietest, but for this to work we would need to challenge night closures on the railwayDavid Fletcher, Director for Rail at Cappagh Group of Companies Rail freight delivers a vital service and
thereis
stilla significant amount of heavy product that can be moved by rail
This construction market is very competitive and even the smallest differential can be the deciding factor.
David agrees: “Material sourcing decisions are often marginal, with large volumes to move, businesses can change supplier based on pennies, not pounds. So it’s a hugely competitive market that rail is working in.”
Something rail freight has always been able to shout about is its environmental credentials as opposed to road. But how long can the industry keep on banging that drum?
David’s view is that: “We should never forget that the rail freight industry is competing against other modes of transport and our environmental credentials are very sound at the moment, but this might not last forever.
"Road transportation is catching up with us in terms of, for example, electric trucks. So the environmental argument might not be as strong for rail freight in the future if we don’t keep driving forward. We’ve got to maintain the momentum in our overall offering and keep being innovative in that respect.”
He said there were many ways to ensure rail freight remained the sustainable transport of choice. For example, longer trains reduce emissions so, if 12 extra wagons were added to a train this would realise:
Payload + 50%, fuel + circa 30%
The efficiency of operations could be improved by better pathing. David commented, ‘’On a 100 mile journey it is not uncommon to find freight trains stood for 20-30% of the journey. A stood train costs money and if we can keep freight moving, we will be better able to compete with other modes.’’
But for rail freight to grow, new connections and new sites are needed.
“There are opportunities to build local hubs in urban centres,” David explained. “There are so many big cities that do not have rail freight facilities, such as Derby, Nottingham and Plymouth. If we’re going to grow rail freight to
deliver on demand, then we need better access to the network close to customers.
“This can be achieved in the form of multiuser and commodity sites close to the end user. Can we, as an industry, think outside the box? Can land be given over to freight from the likes of Network Rail and the passenger operating companies?
"Can carriage sidings be used for freight during the day? We know multi-user bulk terminals can be successful, just look at Burton-upon-Trent, Bow West, Mossend and Middlesbrough.
“And it can be kept simple. We don’t need massive-long sidings with lots of space around them. A 300m long siding and a 20-metre pad, like DCRail has at Leicester, can be sufficient to get a bulk operation started.”
Taking into account the challenges David has spoken about, for rail freight to grow, where will all the extra trains go?
A braver industry
David added: “The railway is full, especially on a Sunday morning!
“There are issues that we need to overcome. Currently stabling is a significant constraint, we need stabling options in key locations and there are inevitably conflicts with other users.
"I believe that freight being allowed 24/7 access to the network could be the answer, allowing us to move goods when passenger trains are at their quietest, but for this to work we would need to challenge night closures on the railway.
“I want all rail users to be treated as equal. Rail freight delivers a vital service. I’d like to see the industry coming together and being braver to find the extra capacity that we need to deliver more products, better and faster for the people of the UK.”
(www.g-volution.co.uk) and SBL-Rail (www.sbl-rail.co.uk) have revealed dual fuel evolution concepts of the Class 37, Class 59 and Class 66 locomotives, representative of Type 3 and Type 5 locomotives respectively and their operations.
Dual fuel engines use compression ignition and combust two fuels simultaneously. This work shows how diesel fuel can be displaced by renewable net zero carbon emission fuels and how adopting dual fuel engines can be a pathway to decarbonise locomotive operations.
G-volution has been developing dual fuel engines since 2008 and together with SBL-Rail now shows how this technology can benefit UK freight locomotives.
The concepts use diesel with biomethane, diesel with biopropane and diesel with hydrogen. The Class 37’s English Electric 12CSVT and the Class 66’s EMD 12-710 engines are replaced by new dual fuel engines and meet the Stage V emission standard. A twin engine concept Class 59 and Class 66 using two smaller new dual fuel engines has also been developed as well as a dual fuel evolution concept of the Class 66’s original EMD 12-710 engine. The locomotives’ original engines could also be evolved to dual fuelling too but modern engines offer higher efficiency, the opportunity to use advanced combustion control strategies and compliance with the latest emission standards.
The original diesel tank/s of the locomotives are replaced with a smaller diesel tank and cylinders for biomethane or biopropane or hydrogen are installed alongside. A range of fuel tank solutions were developed for each fuel, featuring a number of smaller cylinders or instead using fewer larger cylinders.
Biomethane can be manufactured by anaerobic digestion of biomass including organic waste streams e.g. food, farm and sewage waste and there are currently 670 such biomethane production plants in the UK. Biomethane is a renewable fuel replacement for natural gas.
Biopropane can be manufactured through a number of different routes from biomass, organic waste streams or through biological routes. Biopropane is a renewable fuel replacement for LPG (Liquefied Petroleum Gas).
Hydrogen production options are numerous and include manufacture from biomass, hydrocarbons or by electrolysis of water. Currently hydrogen is typically made from fossil fuels (usually natural gas) or electrolysis of water.
The diesel component used in dual fuelling could too be replaced in due course by a renewable diesel-like substance. Dual fuelling lowers particulate emissions too and if a Diesel Particulate Filter is fitted, the engine thus spends less time working against an increased back pressure as the DPF fills. Fewer DPF regenerations are then needed, thus improving engine efficiency and further lowering fuel consumption.
Route simulations were completed using OTMR provided by operators of these locomotives and in combination with dual fuel engine models based on G-volution’s dual fuel combustion research to date. Results are shown in the table below. Hydrogen’s carbon savings assumes green hydrogen is used and hydrogen at a cost 1.3 times that of diesel on an energy equivalent basis.
The new 4 stroke dual fuel engines offers a 10%13% improvement in fuel consumption versus the original engines. Whilst the dual fuel evolution of the EMD engine offers higher replacement rates of diesel, this 2 stroke engine is less efficient than the new 4 stroke dual fuel engines and also doesn’t meet the latest Stage V emission standards.
On an energy equivalent basis, biomethane is 0.5 times the price of diesel, biopropane is 0.6 times the price of diesel and hydrogen is currently 1.3 times (using natural gas) to six times (using electrolysis) the price of diesel. Hence the negative cost savings for the EMD hydrogen dual fuel evolution. The new dual fuel hydrogen engines offer positive cost savings primarily due to these engines’ improved efficiency over the original engine thus overall lowered operating costs despite using a more expensive fuel than diesel. Biomethane and biopropane dual fuel engines offer significant carbon and cost savings versus diesel. Hydrogen also has the potential to do this once produced from renewable sources and once it is much cheaper than it is today.
Please note that this report is based on 2020 fuel prices. Whilst diesel prices are expected to rise in the future, biomethane, biopropane and green hydrogen are disconnected from the crude oil price and their prices are expected to fall as production volumes continue to ramp up. Green hydrogen made through electrolysis relies on renewable electricity and requires electricity prices to fall (or diesel prices to rise even further) for it to offer operating costs savings over diesel.
Further work is now underway to apply our dual fuel evolutions to other types of rolling stock and also includes further dual fuelling concepts including diesel with biogas (the partially purified output of a biomethane plant), diesel with hythane (a blend of hydrogen and methane), and diesel with ammonia.
Jon and Richard Bailey both have vast experience in the rail and logistics industries and have held senior roles for some of the biggest global corporates.
Jon has worked in logistics for over 21 years, 18 of those working in rail where he covered a range of operational and commercial roles in the freight sector including duty manager, service manager, head of rail industry services and head of market development. He then spent three years in shipping as commercial director for DFDS.
Meanwhile Richard spent over 10 years working in the engineering industry in Quality and Production Management roles for a speciality metal manufacturer which supplied the oil and gas industry. Moving to rail freight, Richard spent the best part of a decade covering a variety of operational and planning roles, specialising in planning and crew diagramming disciplines and managed the planning team at the UK’s largest rail freight operating company, DB Cargo.
So, with such a range of experience and highprofile jobs under their belts, what prompted the brothers to strike out on their own?
Jon said: “We had considered starting our own company for a few years and decided the time was right for both our professional and personal lives. Finding the right balance between the two has always been a huge factor in our decision making and will continue to be so.
“We felt that now we have the collective experience and wide-ranging knowledge it was the perfect time to launch a business that brings value to a range of organisations and their supply chains.”
The summer of 2021 saw the launch of BaileyRail & Logistics.
“From day one we had a clear focus on which to build our business,” Jon said. “We pulled together six key service pillars, these being Planning and Timing; Project Management; Modal Shift; Warehousing and Handling; Training, Development and People Placement; Infrastructure.
“We work with clients to advise, create and refine sustainable, cost effective and reliable supply chains by scrutinising every aspect and dependency within them.
"Logistics and supply chains are very often misunderstood, and under-valued, so our philosophy is to work with clients on the wideranging industry challenges that they face, including customers who want to explore alternative modes of transport, refine their current supply chains or work on major infrastructure projects.”
Leaving behind the securities of the corporate world and setting up your own company is a brave move. Inside Rail Freight caught up with Jon Bailey who established BaileyRail & Logistics last year with his twin brother Richard, to find out how the first 12 months in business have been
Many aspects of logistics are intrinsically linked, and we are enabling customers to refine their supply chains to improve performance, reduce cost and reduce their carbon footprint. We’re very excited about continuing this growth in Year two and beyondJon Bailey
RFS has worked closely with the rail industry and all major Freight Operating Companies for more than 40 years, across the UK and Europe.
With custom-built machines, our material handling operations are comprehensive and costeffective for any operation. And, if we don’t have the required machinery, we’ll build it!
RFS Works with material handling machine specialist Ashross to successfully optimise rail wagon unloading for your logistics operations.
The highest demand is for unloading machines. Perfect for high-speed unloading with convenient minimal depth grounding required for a faster installation, our unloading machines can typically unload 75 tonnes in 2.5 minutes.
+44 (0)1279 630891 +44 (0)1279 636721 info@rfsworks.com www.rfsworks.com
With over 40 years experience, RFS has the logistical resources and expertise to successfully implement any material handling solution that your project requires.
RFS has world-class expertise in intermodal operations, container handling, terminal operations and on-highway logistics.
The first year of operating has seen BaileyRail & Logistics building firm foundations as it establishes itself in the market.
“We’ve had an excellent and busy year one,” Jon said. “We’ve already started to grow our team and widen our service offering. We’re very grateful for our clients over this first year and have thoroughly enjoyed working with them all.
"Many aspects of logistics are intrinsically linked, and we are enabling customers to refine their supply chains to improve performance, reduce cost and reduce their carbon footprint. We’re very excited about continuing this growth in Year two and beyond.”
Jon says there are inevitable differences between working for a large company and starting your own business from scratch.
“When we were thinking about launching the business, we had considerations about securing work, stability and the financial risks that are always a factor when you are not employed in a permanent position with a global organisation,” he said.
“However, once we’d launched the company, the biggest difference we found between being employed and working for yourself was actually the cultural change. We were used to leading large teams of people, something which gave us great satisfaction. As a start-up business this changed overnight and, in truth, took a little while to get used to.
“But we quickly adjusted these skills to lead in different ways, by focussing on leading our clients and their teams to develop and make further improvements to their own organisations.”
To anyone reading this who is wondering about starting their own business, Jon has this advice:
“I would focus on three areas,” he said. “Firstly, have a plan, focus on the areas where you can add value and your target market. Also, keep in contact with your existing business connections, they will reach further than you realise at first.”
He added: “Secondly, be confident. I know this can be daunting at first but it’s important to back yourself and trust your knowledge and experience.
“Thirdly, collaborate! This is the single most important piece of advice I can offer. Collaboration is key to success when starting your own business.”
We’ve already started to grow our team and widen our service offering. We’re very grateful for our clients over this first year
Drax,the UK’s biggest generator of renewable electricity is expanding its rail fleet by investing in 30 new rail wagons to deliver the biomass it needs to generate enough renewable power for four million UK homes at its North Yorkshire power station.
The upgraded high-capacity wagons manufactured by British firm WH Davis will help to further reduce Drax’s carbon emissions and make its biomass supply chain more resilient and efficient.
Drax’s fleet of 225 rail wagons, the first of their kind in the world, were designed and developed by Lloyd’s Register Rail (now Ricardo Rail) and WH Davis based in Mansfield – the UK’s last independent freight wagon manufacturer.
The innovative design of these new wagons has increased the amount of biomass able to be transported in each wagon by 30 per cent, allowing them to carry 71.6 tonnes of biomass each, reducing the number of rail journeys required and reducing supply chain emissions.
The first of 30 new wagons are expected to come off the production line early next year and go into operation delivering biomass from the Port of Tyne to Drax, reducing emissions on this route by over 25 per cent.
Bruce Heppenstall, Drax Plant Director, said: “Our biomass trains deliver up to 30,000 tonnes of biomass to the power station each day, enabling Drax to power millions of homes and businesses across the UK with reliable, renewable electricity and support energy security.
“It’s therefore vital that we have a robust supply chain and investing in these new wagons will further increase our resilience and cut carbon emissions on our Tyne to Drax rail route by more than a quarter, whilst continuing to support thousands of jobs across the North, including at WH Davis and Davis Wagon Services’ facilities.”
Since it converted two thirds of its power station to use sustainable biomass instead of coal, Drax has transformed its business to become Europe’s biggest decarbonisation project and the UK’s largest single site renewable power generator, playing a critical role in energy security.
This transformation has also preserved and supported jobs – with Drax’s operations supporting almost 6,000 jobs across the North at a time when other power stations have closed.
Each train is able to carry sufficient biomass for Drax to generate enough reliable renewable electricity to supply around 800 UK homes for a year.
Jonathan Hamer, Managing Director of WH Davis, said: “These additional 30 new biomass wagons reflect the strength and depth of the Davis Group, including Davis Wagon Services, to provide a full turnkey solution for customers from manufacture to maintenance.
"This contract builds on the previous supply to Drax for its unique biomass wagon fleet requirements and shows its confidence in the quality and reliability of the WH Davis product.
“As the only rail freight manufacturer in the UK it is important for us to win such contracts to ensure the continuity of skills within our locally based workforce. Drax’s confidence in us allows this to continue and develop.”
Mark Fletcher, Member of Parliament for Bolsover, said: “This is a fantastic investment which will strengthen the UK’s energy security whilst supporting local skilled manufacturing jobs.
“These new wagons will help keep the lights on for many years to come, and they are a real example of how British companies can lead the world in innovation and engineering; I am proud to have such a great company based in the Bolsover Constituency.”
Drax’s biomass comes into the ports on the east and west coasts from North America and Europe, and is brought to the power station by rail, because it is more efficient than road transportation.
Drax is committed to boosting the region’s economy by investing in skills, innovation, transport, and culture. A recent study found that Drax contributes over £700 million to the North’s economy and supports close to 6,000 jobs.
Established in 1988, Weighwell gained invaluable insight into the rail industry by developing a unique Portable Bogie Weighing System.
This weighing system outputted individual wheel weights which greatly assisted ABB Transportation’s bogie production/overhaul work. During this period the idea of a new revolutionary concept was also born.
The patented Portable Train Weigher (PTW) is a unique advancement to the traditional means of weighing rail vehicles. An invention that is light enough for two people to carry, yet powerful enough to weigh a train in any location.
After months of development and testing, the innovative product was launched at the 1997 Railtex exhibition.
Paul Horsfall, managing director said: “Our onsite demonstrations after Railtex proved that what was previously thought to be impossible is now a reality.”
Until its invention there was only one choice when weighing a train in the UK: take it to a fixed weighbridge.
Unfortunately, fixed weighbridges were limited to a small number of locations across the country and the cost of moving trains to these locations was significant.
Various accolades and industry awards followed including Millennium Product status by The Design Council. A Millennium Product represents the very best of British innovation, creativity and design.
The Weighwell PTW is suitable for rail freight terminals that move large volumes of aggregate and spoil. The accurate, userfriendly rail scale is installed without any cutting or drilling to the existing track.
An invaluable asset, the PTW can assist rail terminal managers in their day-to-day activities. The weighing system can highlight dangerous overloading before a train is released on the mainline rail network.
The portable nature of the weighing system is beneficial for temporary locations, short term contracts and one off “spot checks.”
The Weighwell PTW has also assisted the Rail Accident Investigation Branch (RAIB) in identifying uneven wheel loads on derailed freight wagons.
It is usually fairly easy to see if a load is lopsided on a road vehicle, since springs will be visibly more depressed where the weight is greatest.
Yet, the same is not true of a rail freight wagon. A badly distributed load on a freight wagon can result in increased component wear, damage to track infrastructure and potential derailment.
In 2020, the RAIB published a summary of learning relating to freight train derailments. An important area of learning was uneven loading. The National Freight Safety Group’s code of practice also states that freight terminal operators and freight operating companies are reminded of the importance of avoiding over-loaded or
unevenly loaded wagons. This should include: Identifying residual payloads from previous journeys.
Adopting loading techniques which reduce any tendency to fill wagons unevenly.
Using weighing data to identify uneven loading.
The Weighwell PTW has evolved since its inception over two decades ago through frequent collaboration with key industry players. To meet a specific market need, the latest version of in-motion weighing software can now graphically highlight imbalanced wagon loads within specific parameters.
The main benefit of this development is that an immediate visual indication is provided to the operator before the freight train goes onto the mainline infrastructure. The software can help enhance what is currently being done with greater visibility and precision.
Paul said: “Our experienced team continue to research and develop new products to ensure that the global rail industry has an efficient, sustainable and above all a very safe future.”
With over 25 years of experience within the rail industry we continue to offer an economical and convenient way of avoiding dangerous loading issues with a safe, reliable and proven product. This is underpinned by professional and knowledgeable support.
For more details: Visit www.weighwell.com
We know this industry inside out and upside down
The
Industry