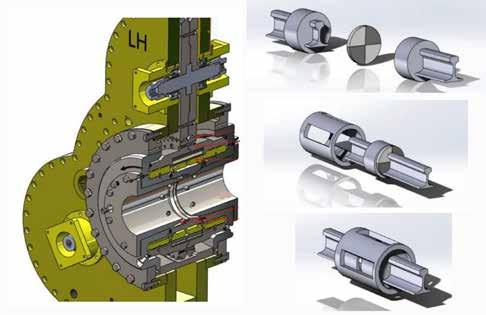
4 minute read
RAIL MAINTENANCE ROBOTS

The development of a robotic Railway Inspection and Repair System (RIRS) was the subject of a presentation by Miftahur Rahman, a PhD student of Cranfield University. His project is the development of an autonomous vehicle to undertake track inspection and repairs. He noted that this had the potential to automate hazardous on-track tasks.
travelled, and recognising known trackside objects. He explained how the limitations of a forwardfacing camera are overcome by having the manipulator arm take multiple images from different positions to provide a data rich 3D model of an object which can be compared with 3D models of other similar objects to detect any anomalies. When working off-track, the vehicle can optimise its route to avoid obstacles and it has object detectors to avoid collisions when working on track. The prototype has been tested on track when it detected simulated rail damage and sent accurate information about its location. Yet various challenges remain. Miftahur advised these include track access, communications, refining location awareness, power, task verification, and cybersecurity. When these have been addressed, the RIRS vehicle is likely to be the first autonomous prototype robotic rail maintenance demonstrator. It will be interesting to see when such robots first see practical use.
developed in collaboration with the Royal National Institute of Blind People and is now being piloted at London Euston.
Navilens code
RIRS uses a Warthog ground vehicle robot with an adaptive trolley that enables it to travel on and off-track. It has a robotic manipulator arm and multiple onboard sensors including LIDAR, real time kinematic (RTK) GPS camera, multiple types of cameras, wheel odometry and an inertial measurement unit (IMU) which measures the three degrees of linear acceleration as well as the three rotational rate components. The vehicle is controlled by Kinetic Kame robotics operating software which uses Gazebo development libraries to provide advanced 3D graphics and simulate dynamic loading.
Miftahur explained that the vehicle can determine its position from RTK GPS, distance
Elevator Pitches
A feature of the RIA Unlocking Innovation events is their elevator pitches when presenters are given a few minutes to convince those present of the benefits of their innovation. Of the nine pitches, only one featured innovative hardware whilst most of the others used AI to improve asset management or provide meaningful customer information. Helping visually impaired people navigate the UK public transport network was the focus of a presentation by GoMedia’s Sven Koster. Its app does this by reading NaviLens codes which, unlike QR codes, can be read from up to 20 metres without the user knowing where they are placed. This has been
Rob Franklin described how his company, Jnction, had worked with rail companies to provide tools customised for their needs using AI. Its ‘Aubin’ wayfinding app is designed to assist the autistic community by providing a journey planner that avoids aspects that cause stress. It is soon to be trialled at Bristol Temple Meads station. The founder of WorkfromHub, Neal Byers, believes there is a need for private working spaces in easy-to-access locations. To satisfy this demand, his company is setting up a network of working hubs which can be booked using an app.
The benefits of AI for asset management were illustrated by Tim Flowers who explained how his company, KONUX offers predictive maintenance, network usage, and traffic monitoring and planning solutions for railway infrastructure management. In particular, KONUX Switch can increase the life of a rail switch and monitor the traffic over it.
AI also offers improved station safety as Duncan Kennon of Createc illustrated by describing how ‘Situate’ offers real-time crowd monitoring using long range LIDAR sensors. As this doesn’t use cameras, there are no privacy issues. Crosstech’s
Hubble application does use a camera, specifically forward-facing video which is analysed by AI to identify and prioritise asset faults as Haydon Bartlett-Tasker described.
Milo Lloyd of ‘The Formal Route’ described how the SafeCap toolset has been developed to provide a fully automated verification signalling interlocking data. It has Network Rail approval and, over the past three years, has been successfully used to verify 60 interlockings developed by different suppliers and identified some safety issues.
In contrast to the other pitches, Stuart Jackman of Jackweld pitched innovative hardware that had been
Level Crossing Systems
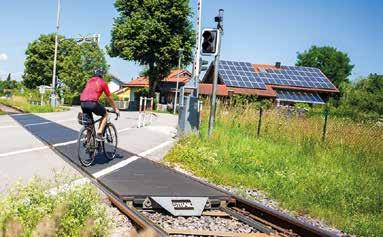
developed to address Network Rail rail welding process challenge statement. This shows that there are around 40,000 aluminothermic welds a year with a 2% rejection rate. Jackweld’s solution is a vibrationless orbital friction welding system which moves a thin steel disc clamped between the rail faces. This provides a solid-state welding process with no melting of the parent metal, and so retains the parent metal’s structure and does not result in fatigue failure initiators. It also has a much-reduced heat affected zone and uses less than 25% of the energy of thermic welding. For these reasons, orbital friction is more reliable and cost effective than thermal welding as well as being ideal for advanced metal alloys. Stuart advised that the system is currently awaiting a Network Rail trial.
Sleeper Spacing Independent System
Heavy Structures Lab
Prior to visiting the University’s heavy structures laboratory, Professor Omar Laghrouche explained how its work has supported the rail industry. This included the 2015 report ‘Geodynamics of train-track-soil under high-speed train loading’ which was undertaken to address concerns raised during the HS2 Bill process. At the time, it suggested that high-speed trains may be derailed due to ground instability due to their travelling close to the wave propagation velocity of the supporting track-ground system.
In collaboration with Balfour Beatty, the University has also developed XiTRACK polyurethane ballast reinforcement which has been used in heavily trafficked locations such as Clapham Junction. Another example is accelerated full-scale testing of railway slab and ballasted tracks on the GRAFT rig which can simulate a year’s loading in a day. The Geo-pavement and Railways Accelerated Fatigue Testing facility (GRAFT) is one of only two academic facilities of its kind in the UK. It has a hydraulic capacity of 200 tonnes (150 tonnes cyclically) which enables accelerated testing of existing and new railway products in realistic railway conditions.
Whilst visiting the heavy structures lab, those present saw the GRAFT rig about to be used to test novel composite sleepers. Also on display was 3D printing of free form structural members and synthetic bricks recycled from construction waste.

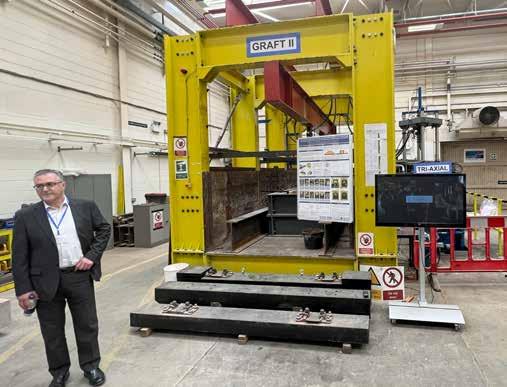
As always, RIA’s innovation events are thought provoking. This one highlighted the opportunities and challenges of AI and robotics for which there are currently few general use applications. This is perhaps not surprising as, for example, the Boston Dynamics robot dog went on sale to the public in 2021 for $75,000. Whilst few can now afford such robots, production at scale could soon see their widespread business and domestic use in the same way that initially expensive mobile phones are now ubiquitous. Yet the event also showed that railway engineering is fundamentally about heavy engineering to control the large forces generated as, for example, a 450-tonne train is supported and guided by rails at 200 km/hr. This is only possible as a result of the research done at universities such as Heriot-Watt.
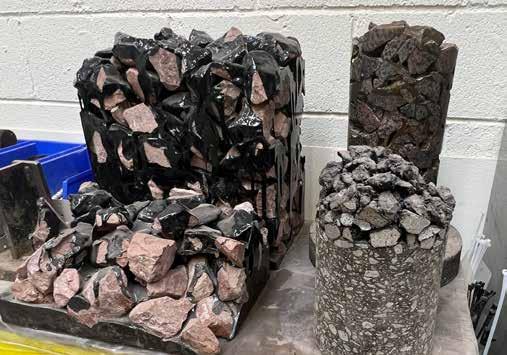
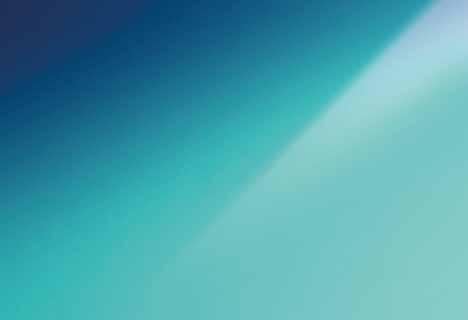
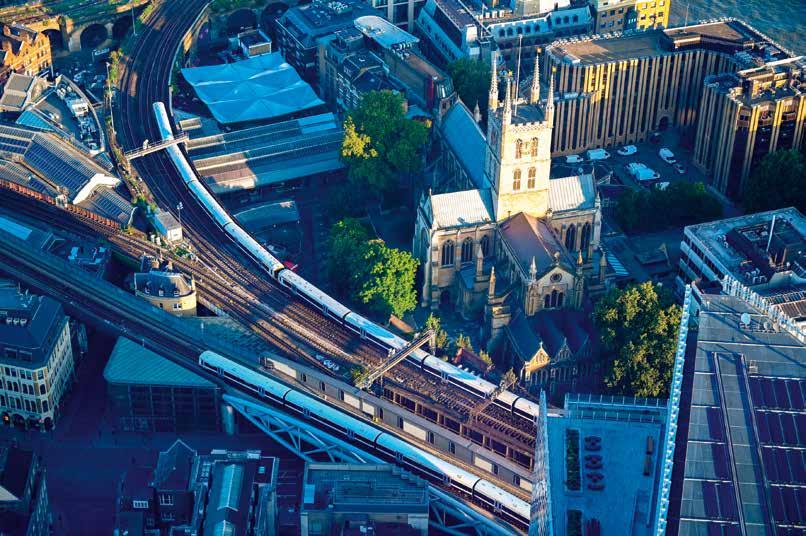