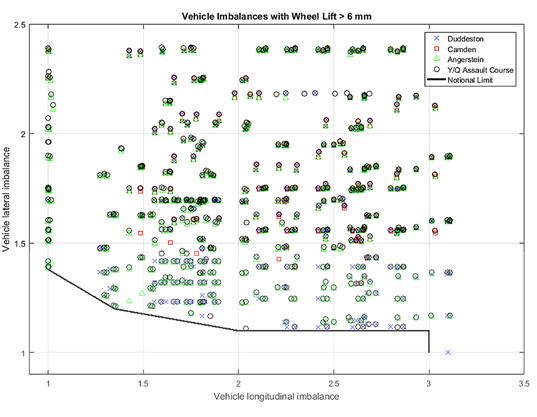
7 minute read
WAGON MAINTENANCEImprovements to freight
When publishing the report into the 24 August 2020 freight train derailment at Llangennech (Issue 194 - Jan/Feb 2022), Simon French, the outgoing chief inspector of the Rail Accident Investigation Branch (RAIB), made this hard-hitting comment:
“The rail industry’s approach to the safe maintenance of freight wagons needs to improve. In this investigation we found that there were inadequate maintenance practices, and a failure to appreciate the importance of the correct fastening of the various components of the tanks wagons’ braking system.
“This is not the first time that we have investigated an accident where RAIB has identified serious issues with the maintenance of a freight train. Over the last decade we have identified deficient wagon maintenance as a factor in more than 10 investigations, including maladjusted suspension, undetected frame twist, and worn bogie pivot liners.”
RAIB’s recommendations were aimed at a number of different organisations including the wagon owner and maintainer, as well as the equipment supplier, the certifier of the
Entity in Charge of Maintenance (ECM), Network Rail, and RSSB. The reports and comments pointed to a culture that needed changing rather than the particular events leading to the Llangennech derailment. Subsequently, the RAIB has commenced an investigation into the derailment at Petteril Bridge Junction, Carlisle on 19 October 2022, where the immediate cause – a severely flatted wheel with a false flange that derailed the train on points – was similar to that at Llangennech.
To illustrate the work done to prevent such derailments, this article is in two parts, firstly reviewing the work being carried out by the Rail Wagon Association (RWA) to improve the facilities and culture for freight wagon maintenance. Many of these activities started before the Llangennech report was published. The second part covers two innovations that have been developed by the University of Huddersfield as part of their work with RSSB.
The Rail Wagon Association
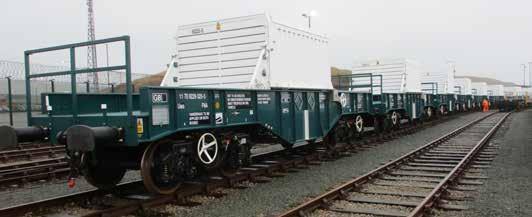
The RWA is an industry group comprising almost all the various parties involved in rail wagon operations: owners, builders, lessors, entities in charge of maintenance, maintainers, operators, Network Rail, users (freight customers), certification companies, and component suppliers. This list of stakeholders illustrates the complexity of today’s freight operations. Rail Engineer talked to The RWA’s general manager, Steve Taylor and vice chairman Les Bryant, who is a rail veteran of 44 years, Davis Group’s engineering director, and chairman of RWA’s Engineering Committee, a group of senior representatives from all parts of its membership.
A key task of the engineering committee is to consider relevant incident reports, investigation recommendations and, where appropriate, set up working groups to address issues identified, e.g. following the derailments at Angerstein and Ely. They have also identified the need for research and were one of the sponsors of the recent research project on wheelset coatings (RSSB T1226, available on RSSB Spark). The Llangennech accident led to the RWA setting up three working groups examining: task analysis, training and competence (T&C), and safety critical components. The RWA sees these three topics as inter-related and crucial to delivering a sound maintenance regime.
The task analysis group started at a very basic level to ‘decide what task analysis is’ in order to develop guidance for RWA members. Any task analysis has to include the required competence level of the people carrying out the work, so it in turn becomes a major input to the training and competence work.
Best practice
Les said that the training and competence work activity is ongoing. It aims to professionalise the wagon maintenance workforce, whilst recognising that wagon maintenance is often carried out in less-than-ideal conditions, and the comparatively low level of technology that has to be dealt with. Against this background the group has, so far, commenced a review of a sample of members’ T&C systems, with the aim of identifying a best practice model using the best of already developed courses to support qualifications for wagon maintainers. This work will lead to a framework for basic skills foundation training and further development.
Finally, a safety critical component list for a generic wagon has been established from available guidance. It comprises: axles, wheels, bearings, bearing end caps, bogie frames, suspension and damping, axle boxes, brake rigging, slack adjusters, and valves on tanks. This list is important as it identifies the components for which enhanced record keeping and traceability is required. By comparison, in the EU the Technical Committee of the VPI (European umbrella for organisations like the RWA) recommended that only the wheels and axle of a wheelset should be considered as safety critical components.
This graph shows that when the acceptable criteria for lateral imbalance and for longitudinal imbalance are examined together, the combined acceptance area is much lower – the area under the solid black line.
Research And Development
Uneven loading
quantitative understanding of the relationship between the two factors. Their work bridged that gap leading to an updated method of assessment in GB Standard GMRT2141 issue 4; specifically, the requirement is for acceptance testing of new wagons, and only applicable to container-carrying vehicles.
Scrap in container in the Camden Road West derailment 15 October 2013: a) as found after the derailment and b) as repacked to replicate original weight distribution.
Les also reported that guidance has been offered to the National Freight Safety Group on what an optimal maintenance facility might look like (previous RAIB recommendation) and is working with Network Rail to capture, for analysis, incidents reported in control room logs that do not make it into industry shared alerts, i.e., NIR reports.
Les considered that RWA members recognise their safety responsibilities, provide industry experts to focus on technical and engineering issues for freight and concluded that “we work well together”.
Several incidents have been caused, at least in part, by wheel unloading issues caused by wagon defects or by uneven loading. RSSB commissioned research from the University of Huddersfield (UoH). This work, largely carried out by Phil Shackleton, sought to understand how much unevenness might be acceptable and, based on input from organisations that load wagons, to provide guidance on preventing uneven loading. Their paper, presented to the 2022 World Congress of Railway Research, identified that the derailment risks of uneven loading and of wagons operating on twisted track were understood individually, but there was no
The adjacent graph shows modelled situations where there is a wheel lift of 6mm for various conditions of vehicle lateral and longitudinal imbalance. The Duddeston, Camden, and Angerstein cases feature track geometry which is recreated from post-derailment site measurements, while the assault course cases are idealised track forms based on the requirements of vehicle acceptance standards. In principle, longitudinal imbalance is more tolerable than lateral imbalance, but it is impractical to control lateral imbalance on container wagons. As described below, Freightliner managed the un-controllable risk of lateral imbalance by controlling the longitudinal imbalance, shifting the point on the imbalance map to where there is greater tolerance in lateral imbalance. Freightliner’s guidance to help manage imbalance was as follows:
Container handlers know the mass of each container, but not the weight distribution. However, during interviews researchers gained an understanding of how containers are loaded. For example, where containers are being used for transporting scrap, a 20-foot-long container might be placed on its end and scrap lowered into the up-ended container from a crane or grab. This often means that the load is concentrated at the opposite end from the doors and it might be a heavy load, such as a scrap transformer.
Previous guidance, to minimise risk of tampering, was to place containers on wagons with the doors inboard as this ensures that the doors cannot be opened in transit. In these circumstances, it might lead to the load being outboard of the bogie and thus a significant longitudinal imbalance. So, supported by a risk assessment, new guidance enabled the placement of containers carrying scrap with the doors facing towards the nearest buffers which would place the load inboard of the bogie, a very simple risk reduction measure.
Predictive wagon maintenance
UoH’s Phil Shackleton has also investigated the use of data from the wheel impact load detectors (WILD) installed at strategic locations on the network. This work was also presented at the WCRR in 2022. WILD was initially installed to detect serious wheel defects such as flats that might harm the track.
As originally installed, these provide an alert identifying which train/wheel has generated the high impact, but UoH was commissioned to explore whether WILD data could also be used to detect wagon defects, such as a twisted vehicle frame, twisted bogie frame, or abnormal suspension behaviour (for example wheel unloading due to incorrect suspension packing) or a broken spring. The important point to make is that WILD was never intended to provide measurements for this purpose, so it was important to develop a robust process that used the available data and a statistical approach to identify wagons that need attention.
UoH reported that WILD measurements were supplied by Network Rail for use in the project. The dataset represented 18 months’ traffic from June 2019 but only the data related to wagons fitted with radio frequency identification devices (RFID) tags were used. Around 2.4 million axle passes were recorded in the data set which equated to roughly 600,000 vehicle passes. 2855 unique wagons of 90 different wagon types were represented in the data set. A broad range of information was included in the WILD data set, such as the wheel load measurements and a number of derived metrics, date and time, vehicle identification, train information, WILD site identification, vehicle ownership and operator, etc.
As the researchers put it, “due to the significant uncertainty in individual measurements in the WILD dataset a statistical analysis strategy was adopted, with the aim of identifying statistically meaningful anomalies in measurement distribution for a specific vehicle compared to other vehicles of that class in the dataset.”
Results
Having developed a robust method for using the data, the researchers presented results for vehicle diagonal imbalance for a fleet of the same vehicle type. This shows the range of data points for each vehicle with the blue boxes showing the statistically significant results and clearly highlighting the few vehicles that might need investigation.
The data showed the impact of scheduled maintenance – a step change in the diagonal imbalance following scheduled maintenance. Whether the wagon is loaded or tare is another factor that helps to identify the likely nature of a defect.
Recently, it was announced that all 15,000 wagons will be fitted with RFID tags which will allow alerts to be related to the particular wagon (noting that some are already fitted). Fitting RFID tags is the key to adopting the results of UoH’s work and its research findings have been shared with the freight industry with a view to this being adopted on a business-as-usual basis.
Rail Engineer will, no doubt, return to this topic.
This chart shows the range of data obtained from individual vehicles, with the rectangular bar areas showing the statically significant results; in simple terms, the higher the bar, the more likely the wagon requires investigation.
Time history of vehicle diagonal imbalance measurements where the effect of scheduled maintenance interventions are clearly seen.
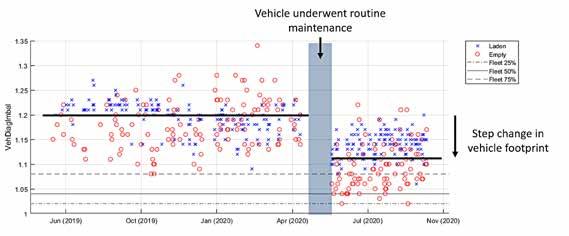
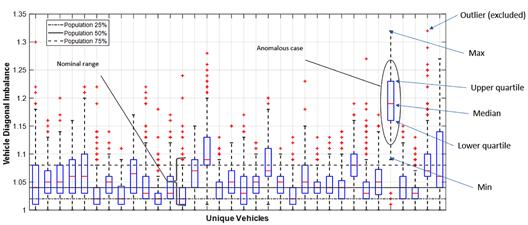