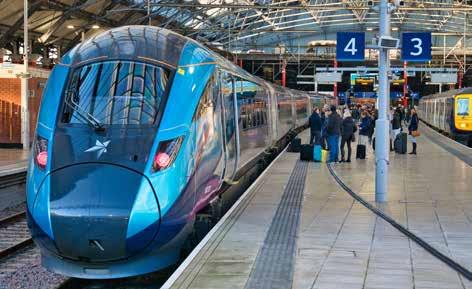
14 minute read
Station stops
SOMETHING TO DWELL ON?
Issue 197 of Rail Engineer (July/August 2022) featured timetabling and described why at the heart of every railway there must be a good, efficient timetable. There are many factors which must be carefully considered for an effective timetable, and this article looks at train dwell time at stations.
A train stopping for longer than timetabled at a station is a common cause of train delay. Most of these delays are small and are ‘subthreshold’, meaning they do not go through the delay attribution process. But even delays of a few seconds can, when aggregated, adversely impact the overall performance and capacity of the network.
Train dwell time is the time a train spends at a scheduled stop without moving, while passengers deboard or board the train. This can be a complicated subject and depends on many factors. These include station and platform design, train design, passenger type and volume, and human factors / passenger behaviour. Interactions between passengers, stations, and trains, as well as interactions between passengers themselves, all make dwell time one of the most challenging factors in train operation, particularly in very busy railways such as metros.
Peak hour train service frequency in many rail systems can be limited by dwell times. Signalling technology has improved to enable trains to run closer together and more frequently, but this in turn creates more passenger volume, which then affects dwell times leading to possible conflicts at junctions and effecting signalling and traffic management. This can have a detrimental effect on the timetable. Factors such as train overcrowding, poor train design, and poor station layout can lead to excessive dwell times at multiple stations.
Station dwell time
Dwell time is defined in the IEEE 1471.1 Standard as “the time a transit unit (vehicle or train) spends at a station or stop, measured as the interval between its wheels stopping and starting”.
The time includes train door opening and closing times, passenger alighting and boarding times, door clear checking times, and any scheduled additional stopping time in the timetable or which may be required for train regulation purposes. In some railways it also includes time for Platform Screen Door (PSD) opening and closing. Normally there is a minimum dwell time to ensure that passengers can board and alight without getting hit by the closing doors.
Dwell times can vary according to type of railway and route. The train doors could close and the train departs when passengers have finished boarding, or the dwell time is set to a specific minimum time at a station or on the whole route - even if all passengers have not boarded (typical in busy metros), or the train doors are closed well in advance of scheduled departure time, so the train can depart exactly as per the timetable. On some railways and routes, say where trains generally wait for connecting passengers to board, dwell times can vary between different stations on the line and at different times of the day.
Design of trains and stations
Design factors affecting dwell times typically include:
» The number of trains on a route needs to accommodate the predicted passenger demands, otherwise overloaded trains will not meet dwell time targets. Sometimes train overcrowding, and greater dwell time, can be caused by cancelled trains due to poor rolling stock reliability and availability. This also includes train crew availability.
» We are all living longer and become less mobile as we age, so trains need to be designed so that passengers with mobility issues can still easily board and alight. The number of train doors and the internal design of trains will affect boarding and alighting times for everyone. Different train types, door positions, and small platforms may mean boarding passengers cannot keep clear of the doors to allow passengers to alight first.
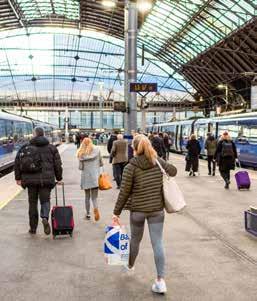
» Busy trains need wide opening doors, but modern, safer, more crash resistant trains generally have fewer and smaller door openings than older trains. A ‘one way in, one way out’ train design with separate exit and entrance doors, as on some buses, would assist train passenger alighting and boarding, but this would be very difficult to implement and manage.
» Where train crew /drivers manually close the doors, they need to be able to clearly observe or obtain assurance from the platform staff that the train doors are clear of passengers. Where train crew may be carrying out other duties, such as checking tickets, they must be able to access the door opening controls when required. It is not unknown on some busy routes for a member of the train crew to have to push their way back through a busy train to their cab to open the doors, with the train stationary in the platform and passengers waiting to alight and board.
» Station entrances and exits along busy rail routes should ideally be varied to ensure more even train loading. Passenger flow modelling should be undertaken to ensure that passengers alighting from one train do not delay passengers boarding another. This is important where large numbers of passengers transfer between two trains at an island platform or where escalator capacity restrictions create large numbers of passengers on the platforms. For existing stations it may be possible to make modifications to ease the situation. Stopping door positions of trains should be easily identified and marked so passengers can ideally wait clear of doors.
» If a platform is lightly loaded with waiting passengers, then generally they stand back and leave space for alighting passengers. But if the platform is busy there can be a tendency for people to ‘move to the front of the queue’ in order to improve their chance of obtaining a seat. This may then affect passengers leaving the train and adversely impact the dwell time.
» Platform Screen Door (PSD) designs, while providing safety improvements and the ability to operate fixed dwell times, can add to average station dwell times. The door opening times can add two or three seconds and door closing times an extra five or six seconds. This can be a problem with trying to run frequent headways on some railways and may raise concerns with providing PSD’s. With railways that operate Automatic Train Operation (ATO), poor ATO accuracy may result in trains not aligning with the PSD doors, and requiring additional time for the train to align.
Station operation, passenger information and human factors
Some railways may have station staff available to make announcements to direct passengers to lightly loaded carriages and assist with train loading. In some parts of the world staff are provided to ‘greatly assist’ passenger loading –such as the white gloved ‘passenger pushers’ on the Tokyo metro. Announcements can also be made to inform passengers of service changes to assist loading, such as advising to wait for the next train if the expected train is very loaded.
Encouraging alighting passengers to prepare early by moving to the train doors prior to arriving at the station can help station dwell times. Regular commuter passengers are more likely to assist with this, although the days of ‘slam door’ stock and passengers opening the doors and alighting before a train has come to a standstill are no more. However, from a safety perspective, should passengers be encouraged to stand and move before a train comes to a stand? Leisure train users, who may also have large items of luggage, are more likely (but not always) to remain in their seats till the train comes to a stand anyway.
Train crew changes at station platforms will affect dwell times. If a guard arrives to open the doors just before a train departs at a terminal station, this can affect dwell times. Other factors, including passenger expectations, culture and behaviour need to a be considered. For example, the acceptable number of passengers per square metre varies around types of railways and the world. On some routes where there are long times between services, passengers may hold the doors open for others rather than wait for the next train, which increases dwell times.
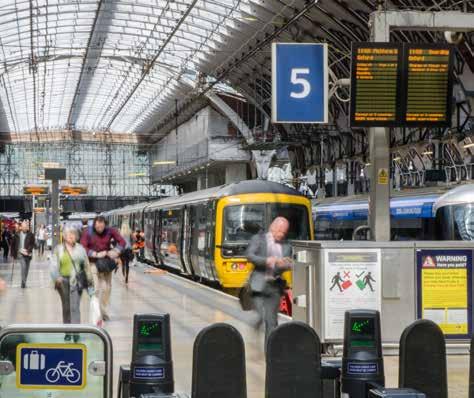
Signalling and train control
Signals in conventional signalling are placed such that the signal design headway can be achieved within the line constraints without delaying the train, while allowing for signal sighting, equipment operation, and the specified station dwell times.
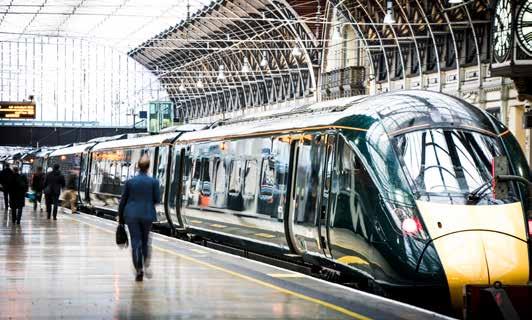
For timetabled services, the signal design will take into account operational differences, including extended dwell times, differences in driving styles, and different train types. The traditional way to cater for longer station dwell times is to design for the peak hour conditions for the predominate rolling stock. This should be based on real or predicted dwell time data for each station and not nominal, or there is a risk that the signalling may not achieve the specified line capacity.
Stopping patterns must also be considered with dwell times, and changing a station signalled as non-stop into a stopping station can affect overall line capacity. To achieve tight line headways, the signals approaching the station may need to be very closely spaced, placing additional speed restrictions on rolling stock with poor braking characteristics, which can further impact dwell times.
So, what can be done?
The Rail Safety and Standards Board (RSSB) IntelliDwellTime (IDT) demonstrator project developed a software solution that generates and analyses dwell data to a high level. The tool displays dwell time at every station stop on the network to the second, and breaks it down into three phases:
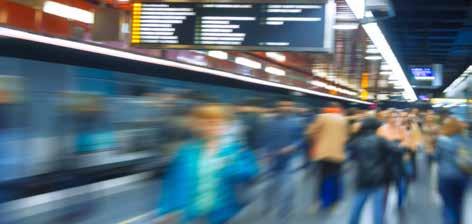
1. Wheels stop to doors open
2. Doors are open
3. Doors closed to wheels start
The tool provides the ability to drill down to see dwell time variation across a wide range of parameters, such as by station or service. The development of the IDT tool was led by Porterbrook, in collaboration with Abellio ScotRail, data science company Elastacloud, and the University of Southampton. The Abellio ScotRail data showed that over 40% of dwell time arises in the third phase, which interestingly means there is more time between doors closing and wheel start than between doors opening and closing.
IDT also correlates dwell time data with other factors, to help identify the root causes of delay. The tool could also be used to compare options and support operational or infrastructure alterations.
RSSB also did a feasibility study towards the development of a real-time digital twin to reduce dwell time variations on the Thameslink route. This project used simulations to establish correlations between delays and the flow and density of people at key nodes, such as ‘bottleneck’ stations. It opened a technical path for industry to improve dwell time performance through real-time passenger flow prediction and crowd management. Details of all the RSSB’s research work on dwell times is available on its Research Catalogue website.
Improving dwell times is not easy, but very often better measurement and management and making small changes to existing practices can make a difference – and much more cost effectively than redesigning stations and trains.
A study 10 years ago by the CoMET metro benchmarking group, identified that the key passenger issues on dwell times were: people boarding trains not letting people get off first; passengers holding or blocking doors; passengers crowding doors and vestibules; and passengers bunching on platforms.
Traditional solutions to these problems included publicity campaigns, signs, and announcements. However, people soon get bored with static signage and repeated announcements, which blend into the background and are ignored. So, the messages must be dynamic and campaigns regularly changed, and announcements must use a variety of phrases that are appropriate to the situation. Effective platform and train staff can make announcements to reduce crowding and the risk of repeated door closures, to encourage more efficient passenger movement, and they can assist passengers with reduced mobility. Technology and signage are also evolving to persuade passengers to change their behaviours. More real-time data enables a better understanding of train loading and crowding, allowing more to be done to improve things. Systems to show the space available on trains in each carriage are also now available, which can provide passengers with increased confidence that they will find a seat and aid them in doing so. This could mean moving down the platform to a less busy part of the train or waiting for the next less busy train.
Summary
Train dwell times at stations is a complex subject with many factors, and even a delay of a few seconds at multiple stations can have a dramatic effect on a timetable. It is a subject that needs a system approach, including station and train design, signalling, passenger information, human behaviours, communications, operations, new technologies, and ways of working to minimise the impact on the operational railway.
Capital delivery is an important feature of delivering a safe and efficient railway. It is essential that best use is made of all the resources available, in order to promote consistency, continual improvement, and to inspire creative and innovative solutions.
Rail Engineer recently met with Eoin O’Neill, capital delivery director Network Rail North West & Central region, to discuss how he and his team are working to enable Network Rail and their suppliers to work more collaboratively together, and with a greater ‘systems’ approach. This is to enable everyone involved in projects to better manage their resources and supply chains, and to help deliver the right project solutions and SPEED (Swift, Pragmatic and Efficient Enhancement Delivery) to halve the time and slash the cost of railway investment.
Eoin explained that, historically, the cost and time to deliver projects was not challenged as effectively as it could be, and that specified outcomes were not adequately scrutinised.

The Covid-19 global pandemic exacerbated these inherent issues and there is now a need for reforms across parts of the rail investment process - especially as the challenges of Control Period 7 (CP7) are fast approaching.
The region is changing from being a collection of business functions, that have largely operated and measured performance in isolation of each other, to being a more integrated ‘one team’ organisation. One that is better aligned and makes best use of its knowledge and expertise to achieve the best investment outcomes.
Eoin accepts this will take time to mature and he acknowledges the region is in the foothills of its journey to improve, which is why the region is taking the initial steps to be a more safe, effective, and efficient organisation as the railway approaches CP7 and beyond.
We discussed the need for a greater ‘systems approach’ to deliver a safe and efficient railway, on time and more cost effectively. The railway is a ‘system of systems’ and needs all the component parts and its people to work together and to support one another. No one or any particular asset is more important than another. A railway infrastructure manager’s role is simple, and is to provide a safe and efficient train path from A to B. But to do this requires earthworks, structures, track, signalling, power, communications, buildings, and stations; not forgetting managing the interfaces with neighbours, train operators and other parties, and the people who operate the railway. The railway is more ‘connected’ than ever so, a system approach is vital, and people and organisations can no longer operate in their ’functional silos’. Otherwise, it simply won’t work. Train operators and the supply chain also need to be part of the railway team, and not thought of as ‘contractors’. The supply chain also needs visibility and a steady stream of work. ‘Boom or bust’ helps no one, and it just increases costs and project delivery risks.
The 2021 Williams-Shapps report said: “Wider industry transformation is already moving towards an environment predicated on ‘whole system thinking’. It recognises that existing adversarial relationships are the key reasons for high cost, low value, and inefficiency in the sector”.
Eoin’s spend of £1 billion - £1.5 billion, looking forwards to year 5/CP6 and average through CP7, sounds a lot, but the NW&C region is large, and is nearly a quarter of the whole GB network. The region is the ‘backbone of Britain’ and the economic spine that links major cities. It runs from London Euston and Marylebone in the south, through the Chiltern and West Midlands regions, the Northwest of England and Cumbria before joining with Scotland at Gretna. The West Coast Mainline is the busiest mixed-use railway in Europe, serving London, Birmingham, Manchester, Liverpool, and on to Edinburgh and Glasgow. The region has 8,000 employees, delivers 246.5 million annual rail passenger journeys, and moves 700,000 tonnes of freight every week. Even in the current challenging times and following Covid-19, over the next few years passenger growth is expected to rise by 12% and freight by 18%. Major railway upgrade schemes in the region to cater for this growth include East West Rail, Midlands Rail Hub, Euston station redevelopment, Crewe Programme, and interfacing with HS2 as well as renewing the existing infrastructure. The asset base requiring interventions includes 571 stations, including the four managed stations (Birmingham New Street, Manchester Piccadilly, Liverpool Lime Street, and London Euston), 712 level crossings, 7,100 bridges, 150 signal boxes, large sections of AC and DC traction systems, many delicate earthworks, some of the longest tunnels in the country, and the underground Mersey Rail system of Liverpool.
System intelligent requirements
For the huge capital programme for the region, Eoin and his team need to work closely and openly with the route and train operators to get the right access and provide affordable value-based requirements, which Network Rail’s new Minimum Viable Product (MVP) value management process drives at. They need the asset managers and sponsors to deliver timely and fit for purpose ‘intelligent’ remits. These should not be too detailed and prescriptive, and they need to be output performance based. Just specifying in detail what has been supplied before stifles innovation and creativity. The remits and specifications need to be performance based and to ensure that suppliers new to the railway understand the outputs required and limitations.
So, for example electrical and electronic systems need to work in the harsh electromagnetic environment of the railway by limiting the unintentional generation, propagation, and reception of electromagnetic energy, which may cause unwanted effects such as electromagnetic interference or even physical damage to operational equipment. Suppliers new to rail may not appreciate the requirements, but they may well have novel ways of achieving them.
If a footbridge is requiring renewal, then the asset managers remit should not be a detailed design for a new bridge. A performance requirement to allow a number of people (including those with limited mobility) to move from one location to another may allow for another public right of way and an existing underbridge to be used. Even if this is not possible, a performance-based remit will allow for new ways of construction and delivery.
The capital delivery team and its suppliers also need to step up and perform more collaboratively in a system engineering approach and not in a ‘silo’ way, simply ‘passing the baton’ problem on to someone else. Maintainers and operators know their areas in great detail and can help projects to deliver better. They should not be brought in right at the end of the project, but need to be involved from the beginning. Everyone in rail is on the same team, including suppliers, and the real competition is road and air transport.
To illustrate an example of a system engineering approach, Eoin described a requirement to introduce new rolling stock which needed more electric traction power. The traditional engineering solution would be to immediately start building more infrastructure and a new power supply system to operate the new trains. But a systems approach would be to see first if it would be possible to operate the railway differently with a revised timetable and train acceleration curves, which may not need more power. Even if this was not possible it may reduce the power requirement and the associated cost.
In such projects it needs everyone, including operators and suppliers, in the same room very early on in a project to identify collaboratively and collectively what needs to be done to deliver the required system outcome, and at the lowest and most affordable cost.
Smarter work allocation
The internal Network Rail Works Delivery group is now an integral valued part of Capital Delivery, and there will be a ‘smarter’ defined work allocation process to ensures projects are allocated to the optimal framework of delivery, based on values and complexity. This will also allow a tailored work categorisation approach that recognises the differences between project and work types to remove a ‘one size fits all’ approach. This will also provide a more appropriate contracting strategy, pricing mechanism, incentivisation, and assurance activity to be used by project type. The more tailored work categorisation will also allow for a more diverse supply base with clear entry channels for Small Medium Enterprises (SMEs).