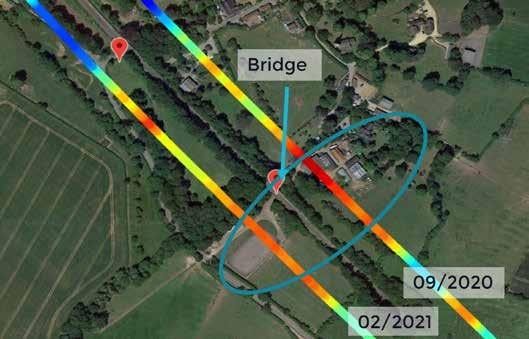
6 minute read
Fibre Optic Movement Sensing (FOMS)
PAUL DARLINGTON
Remote conditioning monitoring of assets is now an essential part of any asset management strategy, which can include monitors for earthworks and track formations. Fixed monitors are great, but they can only monitor the area where they are located. They also need power and a communications link, which can be problematical in some locations. Similarly, monitoring equipment attached to trains has provided enormous benefits for such applications as track and traction contact system asset management, but monitoring by trains only occurs when the train passes any location. This can be weeks apart in the case of a dedicated monitoring train, and it can’t easily monitor and assess earthwork movements near to the track until it is too late.
Fibre optic monitoring provides a third option for remote condition monitoring of earthworks and track formations, including switches and crossings. It can be used to perpetually monitor, 24 hours a day, 365 days a year, providing ubiquitous live data along a length of a section of railway, and not just at the location where the system is deployed. This is because fibre optic monitoring can use the extensive network of around 20,000km of fibre cables already installed along most rail routes in Great Britain. Rail Engineer recently spoke to Focus Sensors Ltd to learn more about its novel and most promising and exciting Fibre Optic Movement Sensing system (FOMS), which could revolutionise remote condition asset management of earthworks and track.
FOMS
Based on seismic principles, FOMS has already proved very capable of detecting and characterising ground stability issues beneath rail supporting structures. By structures we mean anything physically supporting the railway and not just ‘hard’ structures such as viaducts and bridges. A number of trials have been executed on sections of track with known ground stability issues and the results have been correlated and verified with traditional fixed monitoring techniques. The system has also been deployed on areas of track where no known problems were previously detected, and ground stability issues have been detected that had not been identified using traditional methods. The trials have also successfully demonstrated that FOMS can monitor changes in ground stability over time and distances much more safely and efficiently than current remote monitoring methods, and requiring no local power supplies or communications connectivity.
A fibre optic cable consists of one or more very fine strands of glass, each of similar thickness to a human hair and referred to as a fibre. The centre of each fibre is called the core, which provides the pathway for light to travel. The core is surrounded by a layer of glass called the cladding, which reflects light inward to avoid loss of signal and allows the light to efficiently pass through bends in the cable. The light transmission is used to transmit very high rates of data and all modern telecoms networks use fibre optic cables.
Fibre sensing uses another characteristic of fibre. This is when light is reflected or ‘backscattered’ as it propagates through the fibre in response to a change in temperature, a bending or pulling force to the cable, or by mechanical waves in the fibre’s proximity. The change in backscatter is detected allowing the location and cause of the change to be determined. FOMS can detect the change in mechanical waves produced by infrastructure issues to a linear accuracy of one metre along the fibre.
Seismic principles
Focus Sensors Ltd has developed all the required hardware and software to capture and process the data for FOMS. The data being processed by the system is huge and challenging, and is typically 50Mbps. Focus Sensors has had to develop its own software platform to turn the raw data into useable information. The company’s background and experience is with seismic investigation in the oil and gas industries using optical sensors. Seismic investigation involves using such things as air guns and sticks of dynamite to create what are known as ‘sources’ and to monitor how the source is reflected and transferred through the ground.
FOMS for rail uses the same principles, but with the train as the active source which is used to quantify a transfer function with the optical fibre, which includes the rail, sleepers, and the supporting ground. A method has been developed using seismic principles to separate the source effect of the support ‘structure’ under the train from the signal the train is generating itself, and the result is FOMS.
As a train moves along a track, its weight creates sources which go through the rail, sleepers, and ground, and into the fibre. But when the supporting structure or earthwork is not as ‘stiff’ as it should be, the direction into the fibre is different, which can be detected and reported. An effective user-friendly way has been developed to quickly show asset managers and infrastructure maintainers issues on a map overlay display. This allows the instigation of further targeted interventions or further monitoring. Colours are used to represent the severity of the support structure failure - red being the most severe and poorly supported, with blue representing a firmly supported structure.
INDUS™
The FOMS system is part of the company’s family of INDUS Distributed Optical Sensing System products and can be deployed in a number of ways. One way is a temporary installation typically in an equipment room with a fibre distribution point. The equipment consists of a small
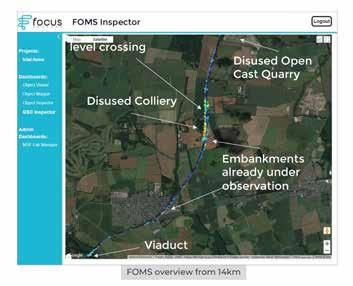
2U equipment rack requiring less than a 100W and a Wi-Fi or 4G cloud connection, which can typically be deployed in less than four hours and no track access is required. A FOMS monitoring point can typically monitor up to 40km (80km bidirectional) using a spare ‘dark fibre’, although Focus Sensors says it may be possible at some point in the future to also use active ‘lit’ fibres carrying telecoms data with no interference.
A number of successful tests have been demonstrated on a 13km section of live railway. Most of the route was blue, which was fantastic, with the railway well supported, but there were some issues identified with areas shown not in blue. Some embankment slips were identified and shown in red, along with a number of old disused mine shafts. Voids under the track and worn switches and crossings were also identified in red. A number of the identified risks were issues the infrastructure manager already knew about and was successfully managing, but others were new and had not been previously identified. The FOMS system was proved to be able to monitor a section of track every time a train passes and highlight when any structural stability issue changes.
An example was with a disused mine shaft that the asset manager was aware of as it was creating some instability issues, but they didn’t know exactly where it was located and, as typical in such cases, no records existed. The traditional way of identifying the exact location of the shaft would have been to dig lots of trial holes, but FOMS was able to locate the shaft with an accuracy of one metre and only one hole would be required to inspect the old shaft.
Some trials were done on another section of track over three years. One location was recorded as experiencing some movement in the first year, excessive movement in the second year (suggesting something had changed around the area), but then very little movement in the third year. It turned out that in the second year the maintainer had identified that the track needed to be lifted and tamped. So FOMS had detected an emerging issue which got worse but was then successfully resolved.
FOMS has also successfully identified voids and wear with
Switches and Crossings (S&C) and identified a blocked culvert causing localised flooding and an area of movement, followed by good stability once the culvert had been cleared.
Benefits of FOMS
When the rail network was built nearly 200 years ago, thousands of earthwork embankments and cuttings were quickly constructed. Many were poorly built and without the knowledge of soil mechanics and geotechnical engineering that exists today.
A report by Thomas Telford in 1829 said that many railway earthwork embankments were largely formed by the ‘end-tipping’ of material down the formation. It was a process he disapproved of as it would “delay consolidation and increase the tendency for slipping”.
Today, the main rail network still has over 190,000 of these earthwork assets and remote condition monitoring is an important tool to manage any instability issues. But fixed monitors can’t be installed everywhere and FOMS is a new technique for monitoring ground stability, using optical fibres which are already installed next to the railway. FOMS has been successfully used to monitor issues such as embankment slips, disused mineshafts, track voids, S&C condition, and drainage problems.
The monitoring can be put in place in a few hours and up to 80km of route can be safely monitored continually from one location, with results presented via a user-friendly web interface or as regular survey reports to the maintainer and asset manager.
FOMS can be considered to be similar to a track patrolman walking the track and observing any changes to critical infrastructure which may require more investigation and intervention. However, with FOMS it can detect changes before they are visible and can observe safely 24/7, 365 days a year if required.
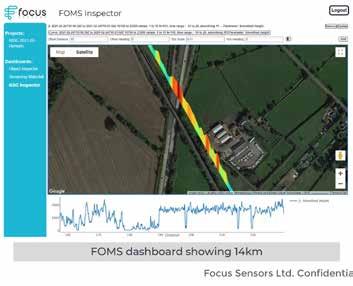
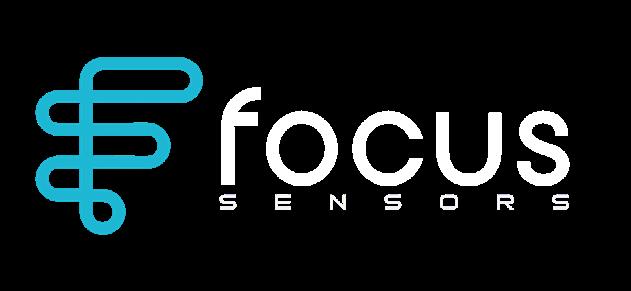