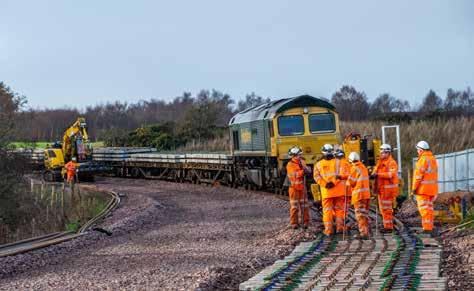
9 minute read
Three ways to lay track
laid track in 6km stages, which was found to be the maximum practical distance that CWR could be dragged along the new formation. The track construction machine lays track at 185 metres per hour.
Borders – sleepers first
In Scotland, the re-opening of the Levenmouth branch in 2024 follows the re-opening of the Borders railway in 2015 and that of the Airdrie to Bathgate line in 2010. The amount of track needed for the Levenmouth, Borders, and Airdrie to Bathgate projects is respectively 19, 65, and 46 single track kilometres.
Levenmouth – rails first
Before track laying on the Levenmouth branch can commence, 216-metre lengths of continuous welded rail (CWR) have to be left in position well in advance of the track laying. This requires sleepers to be lifted off an engineering train, positioned on the track bed using two excavators and a dumper truck. An excavator then thimbles the rails into position for them to be clipped up with a clipping machine. In this way, 220 metres of double track is laid in 8.5 hours, which is 52 metres per hour.
Airdrie to Bathgate (A2B) – rails first
Rails also had to be laid in advance for the A2B project which laid track using Balfour Beatty’s high output new track construction machine which carries sufficient steel sleepers for 1.2kms of track, less if concrete sleepers are used. This machine was also used for the recent Okehampton reopening. As it moves it lays sleepers in position at the rate of 12 per minute, feeds the CWR in place and clips it into position. The A2B project
Borders tracklaying used a technique developed by BAM Rail of Holland which was used on the construction of the Dutch high-speed line which needs sleepers to be in place beforehand. These were deposited on the track bed off lorries in piles of 20 and were then put in place by a spider-fitted excavator. The BAM process has four selfpropelled units which pull the CWR off its delivery train to place it on the sleepers. The four units are a main roller unit connected to the CWR train by a three-metre bar; a power unit, an auxiliary roller and winch unit; and a mobile rail positioning unit on caterpillar tracks. After the rails are in position, they are clipped up by Robel clipping machines. The BAM process was observed to lay track at 185 metres per hour.
Which is best?
Both the Balfour Beatty and BAM ways of laying track do so at the same rate of 185 metres per hour. The Borders project team, many of whom delivered the A2B project, felt that, for a new railway, there was little to distinguish between. Whilst these two automatic processes lay track at three times the rate of the Levenmouth track laying, this does not necessarily make them better. Levenmouth has much less track to lay than the other two projects so it may be difficult to justify this expensive plant, including its set up and transport to site.
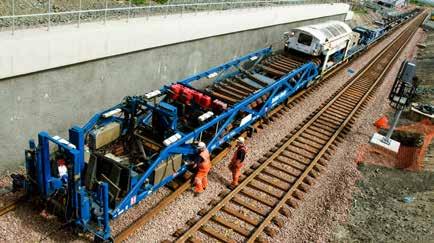
Another issue is the importance of track laying speed to the project programme. Whilst track laying might be on the critical path for a new railway with a long length of track to lay, this is not the case for the Levenmouth project. Another issue is that using high output tracklaying plant locks the programme into its availability. Using conventional plant to lay track, as at Levenmouth, offers greater flexibility.
So, whilst it is interesting to compare these different techniques, there can be no definitive answer to the question of which is best as it depends on the circumstances.
UK Rail is undertaking an unprecedented period of digital innovation and revitalisation. Infrastructure dating back to the era of the steam engine (and steam trains themselves) are being upgraded to create a modern, higher capacity network. It’s an exciting time of progress and digitalisation is accelerating. Yet novelty requires a focus on integrity to maintain and improve safety standards, requiring effective collaboration to efficiently deploy and test new technology. This rigour is essential to realising the potential of digitalisation – moving people and goods even more sustainably as we strive to deliver Net Zero.
Our railway constantly needs to evolve. From lowering cost and carbon to increasing capacity, safety and reliability, we’re being challenged to improve almost every aspect of rail. But our infrastructure is built on aging technology, especially the signalling system. To meet this growing demand to improve capacity and reliability, the UK rail industry has embarked on a journey to digitalise the railway, including the transition from lineside signalling renewals to digital signalling through the European Train Control System (ETCS). Pioneering the latest generation of this digital signalling technology across the route on the East Coast Main Line (ECML), one of the UK’s busiest rail routes, is revealing both the challenges and benefits of the digital signalling rollout. By validating and optimising it on a high-speed, mixed-use railway involving all operator sectors, ECML’s digitalisation establishes the pattern for other lines to follow.
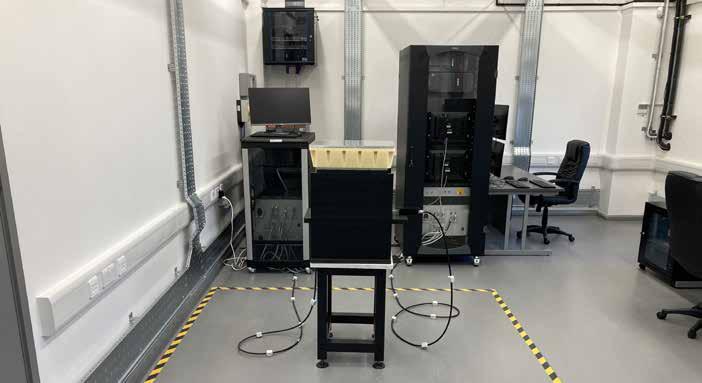
Network Rail’s Long Term National ETCS Masterplan, supported by government and industry, will enable digital signalling across the network. But effective independent testing is required to ensure multiple suppliers’ equipment compliance and compatibility. The UK Railway needs a common, repeatable testing capability and acceptance process to ensure these new products, and their software upgrades, are certified rigorously and efficiently – to enable and expedite the national ETCS rollout. That’s why Atkins has worked with Network Rail to commission the National ETCS Test Lab, where products from different suppliers can be tested for compliance with the GB Reference Design. Signalling equipment suppliers have each developed their own on-board and trackside ETCS solutions, and while these all accord with the European Railways Agency mandatory specifications, they must now be configured to the latest standards and UK specific requirements. Otherwise, we risk incompatibility, safety issues, and costly delays. real risk of integration failure, increased costs, and disruption to passengers. Network Rail has recognised the value of an impartial testing regime. To ensure consistent and seamless interoperability, and mitigate the dangers of incompatibilities, the path to
The lab opened in June 2022 and is available to provide testing services for ETCS Programmes, Signalling OEMs, and ETCS retrofit programmes for ROSCOs, TOCs, FOCs, Inspection Fleets, On Track Machines and Heritage & Charter.
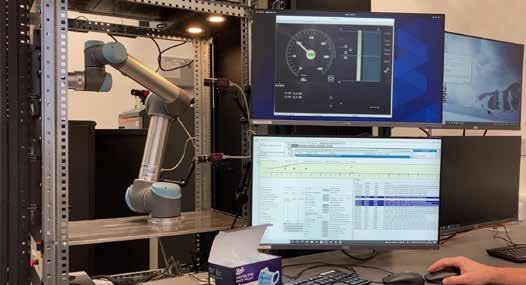
“As Head of Train Control Systems at the ORR I am delighted to see the introduction of these test facilities. They will undoubtedly accelerate the production of evidence that supports the authorisation of ETCS products for use on the GB network.”
Ian Maxwell, Head of Train Control Systems, ORR
One track mind Deploying ETCS demands a high level of confidence in novel technologies and how they integrate into the existing railway. Misalignments could threaten the integrity of the whole system and are more costly to resolve once commissioning is underway. Innovation alone is no silver bullet. Without an integrated and interconnected framework to assure innovation, there is a progress must be paved with effective integration - and assurance that all technologies meet high standards.
Atkins is perfectly placed to guide and manage this process. Atkins’ Technical Investigation Centre (TIC), renowned historically for its excellence in independent forensic testing, specialises in investigating safety-critical signalling equipment failures that occur in operation. As
“We are delighted to have delivered yet another of the key enabling projects that pave the way for National ETCS transformation. This facility expands our capability through life – from R&D, through product acceptance, to in-operation fault diagnosis. The project has been a tremendously successful collaboration with Network Rail and our partner Multitel – delivering to schedule despite the challenges that Covid presented. We look forward to welcoming clients to the National ETCS Lab in 2023.”
Mark Fielding-Smith, National and Digital Services Director, Atkins the UK’s signalling systems integrator and the Rail System Integration Partner on the East Coast Digital Programme (ECDP), Atkins has long been at the forefront of new approaches in digitalisation, collaboration, and innovation. With the opening of the National ETCS Test Lab at Egham, in partnership with Multitel, we have extended our test capability to provide national product acceptance services prior to entry into service.
Together, the National ETCS Test Lab and the TIC offer the ability to test across the lifecycle – from R&D concepts, through to product acceptance testing and into in-service system level fault finding. In turn, this lab can support Defect Recording and Corrective Action System (DRACAS) investigations, helping to uphold high standards of safety and reliability. The lab includes a GB Reference virtual onboard and trackside system for carrying out operational compliance and interoperability test scenarios. This forms the central component of the National ETCS Test Lab facility that has delivered an endto-end solution to navigate the complexities of ensuring ERTMS/ETCS compatibility.

The National ETCS Test Lab solution is unique in being the UK’s independent test facility for ETCS product and integration testing, providing Network Rail System Authority, ORR and OEMs with a dependable and repeatable reference point for future testing. From additional capacity adaptations to software upgrades to systems integration testing to cyber security testing, there’s a clear need moving forward
“The National ETCS Test Lab allows Network Rail to test changes to the GB Reference Design in a realistic application prior to being formally issued for use on live projects. Being able to test the changes before implementation on a live project minimises the project delivery risk and provides us with the confidence that the changes deliver what we need to operate the railway safely.”
Jonathan Hayes, Head of Programme Engineering and Systems Management, Network Rail
for a trusted and consistent evaluation process, and for providing objective unbiased diagnoses of problems and incompatibility issues. The independence of the lab enables a trusted diagnosis and fault finding when multiple OEM’s equipment are collaborating in the railway. Mutual assurance and trust in the testing operation, therefore, are critical to providing trusted evaluation and compliance assessments. Providing a standard repeatable testing service benefits ETCS Programmes, suppliers, infrastructure managers and railway undertakings by offering a trusted and predictable process for approvals, derisking potential retesting.
In rail we trust
The benefits of a trusted testing system are many and varied. On-site testing is expensive and timeconsuming. Any time interaction is required with the live system, there is potential for disruption to live signalling systems and the trains that depend on them. Although the rail industry has an exceptional safety record, there are clear safety benefits to minimising on-site exposure to workers. Moreover, at the forefront of digitalisation, the National ETCS Test Lab is setting a precedent, establishing a blueprint for the continued national roll-out of digital signalling that will inform and guide the future of safety assurance and signalling acceptance.
As the digitalisation of the UK’s railways continues at pace, it’s important to keep these projects on track. The industry must continue to champion continuous, iterative improvement, whilst ensuring that the systems remain resilient. That’s why, alongside the National ETCS Test Laboratory, Atkins has created a technical innovation hub, uniting conventional signalling and ETCS/ERTMS technology to test signalling systems and focus on the challenges of successfully bringing UK rail into the digital age. This age will be defined by the gains of greater connectivity and centralised control of assets. So too will it need to address increasing concerns, such as data integrity and cyber security. A chain is only as strong as its weakest link, and so cybersecurity testing will be a cornerstone of the national ETCS delivery and will form a key part of the work done at the National ETCS Test Laboratory. Atkins is also collaborating with the National Cyber Security Centre in the delivery of the Defect Recording and Corrective Action System (DRACAS), a system designed to manage, investigate, and solve systemic ETCS faults. These, and several other schemes, are vital to keeping progress on both track and secure.
All aboard Digitalisation is the direction of travel. The journey to transform the rail industry requires continued focus and orientation, to navigate the obstacles and opportunities ahead. The national ETCS Test Lab facility is a foundation that will support the transition to digital, underpinning and reinforcing that progress. As the first of its kind, it’s ushering in new standards and mode vital to unlocking the full potential of digital technology. By 2050, we’ll look back on this shift as momentous and groundbreaking. Yet to get there, we need to work together to propound and execute a clear, integrated vision, safely. That’s what impartial and independent testing is all about.
If you would like to learn more about the National ETCS Test Lab or explore booking testing services, please contact George Walker, digital rail director at Atkins, at George. Walker@atkinsglobal.com
“This facility is a key game changer for the roll-out of ETCS in the UK, building on the lessons from ETCS National Integration Facility (ENIF), Thameslink, and ETCS roll-outs in Europe. The facility allows supplier products to be tested to confirm that it complies with the GB Reference Design and can deliver the functionality and performance needed for the rollout of ETCS in the UK. The capability to test both onboard and trackside system in the ETCS test lab reduces the risk of issues being found during testing and commissioning and reduces the amount of disruption to passengers as it minimises the site testing required.”
Andrew Simmons, Head of Systems Authority, Network Rail