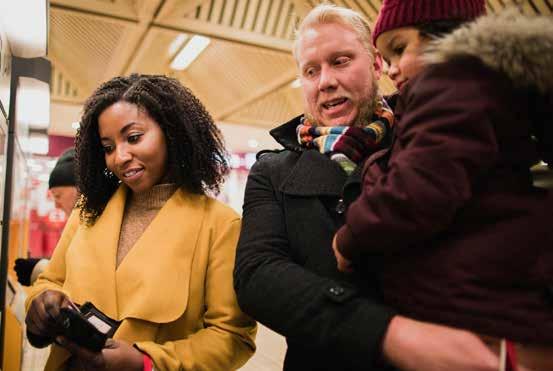
4 minute read
Is rail affordable?
When Dr Beeching wrote his 1963 report, half the UK rail network carried only 4% of the passenger traffic, a third of the passenger fleet was used less than 20 times a year, and the railway employed 475,000 staff. British Railways annual deficit was then £87 million, or £2.3 billion in today’s money.
Today’s rail network is more intensively utilised and employs about a quarter the number of people. Yet in 2018/19, operational funding (i.e., less HS2 and enhancements) cost the taxpayer £4.7 billion or twice that of Beeching’s highly inefficient railway. Privatisation has therefore badly failed to meet its prime objective of reducing rail’s cost to the taxpayer.
To be meaningful, this comparison uses pre-Covid data. Following the pandemic, publicly funded operational costs for 2021/22 are £13.3 billion, of which £6.5 billion was infrastructure expenditure. In the current economic situation, such high costs threaten the railway’s future despite its huge potential to support economic growth and decarbonisation. This is particularly unfortunate as many committed rail professionals are doing much to reduce costs, as we often report. Yet, innovative measures to save on-site costs will have little impact if off-site overheads are a large proportion project spend.
In 2011, Sir Roy McNulty’s report “Realising the Potential of CG Rail” identified various reasons for the railway’s high costs. These included unpredictable, wildly-fluctuating demand for trains and infrastructure enhancements, slow crossindustry decisionmaking, excessive government involvement in operational decisions, and DfT not considering the efficiency of the railway as a whole. Unfortunately, little has changed since his report.

There is much that the industry could do to reduce costs. For example, over-complex safety approvals, high overheads, and mark-ups add significant costs. It is therefore essential that initiatives such as Project SPEED are successful. This needs a ‘one team’ approach with everyone considering what is right for the industry as a whole.
As we report this month, electrification and signalling projects have particular cost challenges.
The excellent PWI’s electrification seminar included presentations on the client’s role, power supplies, third rail electrification, and Irish Railways. Those present were very much aware that future electrification depended on convincing Government that costs can be reduced. Managing director of Network Rail’s Eastern Region, Rob McIntosh encouraged everyone to be hugely curious about driving down costs. He advised that he had a copy of the ECML electrification close out report on his desk as a reminder of what can be achieved. At the seminar, I was advised that this project had 22 electrification design engineers compared with over 200 needed for the Great Western Electrification Programme. The recent ORR signalling market study showed that between Control Periods 4 and 5, signalling project costs had increased by 78%. It is therefore not surprising that Transport Scotland regards signalling as a “distress purchase”. This comment was made at an event organised by the IMechE’s Railway Division (RD) which offered an interesting perspective on rolling stock, operations, and signalling. It was suggested that one reason for high signalling costs is the development of differing interlocking protocols by suppliers who are then ‘locked-in’ to their installed equipment.
Another IMechE RD event that we feature is its action-packed technical tour to Finland, Sweden ,and Norway which offered insights on all aspects of railway engineering. For example, participants learnt how Finland was pioneering the European EULYNX initiative to standardise the interface between signalling system elements to reduce reliance on particular suppliers.
The tour also heard about the ETCS programmes in Norway and Sweden where there was also concern about high costs of monopoly suppliers, complex approval processes, high cost of first of class train installations, and the need to freeze infrastructure configuration for several years prior to ETCS implementation.
The current UK approach to ETCS implementation is described by Clive Kessell in a feature that considers its slow implementation to date, and the challenges to be overcome to deliver the ETCS masterplan. This includes the adoption of the Future Rail Mobile Communication System. Clive concludes that ETCS costs must be significantly reduced if it is to replace conventional signalling. He also reports how the Elizabeth Line, which has ETCS, CBTC and conventional signalling, is controlled from Romford.
ETCS will be signalling the Transpennine route once the route’s comprehensive upgrade is completed in the late 2030s. Paul Darlington reports on this transformative £9 billion programme (£118 million per mile) which will also electrify the route, and provide significant passenger and freight capacity improvements.
Paul was also at an ‘ask me anything’ event organised by the Railway Industry Association’s (RIA) Signalling and Telecoms group which covered level crossings, obsolescence, signal maintenance testing,
ETCS, new technologies, and the need to reduce costs. RIA’s Innovation Conference was also a worthwhile event, as we explain.
Gauging requirements increase the cost of introducing new trains and constrain new freight traffic. Malcolm Dobell’s report on the IMechE’s Railway Gauging seminar shows how solutions are being developed for these problems. He also provides a comprehensive review of the Vehicle/Track System Interface Committee (V/T SIC) and the Adhesion Research Group’s annual report. This covered many topics including rolling contact fatigue (RCF).
RCF was the cause of the Hatfield derailment in 2000. At that time there were 952 broken rails a year. Now there are about 80. Bob Hazel’s comprehensive report describes how this reduction in rail breaks was the result of a transformation in rail management. He also explains that the increase in RCF rail breaks prior to Hatfield was due to a combination of factors that were not understood at the time.
The 10,000 rail squats reported annually are generally repaired by welding. We report on how an automated Discrete Defect Repair machine has been developed to offer quicker and more reliable repairs. We also consider drainage and off track assets (vegetation, fencing, and access points) of which the UK rail network has around 32,000km in an article that explains how Network Rail’s Southern Region is improving its stewardship of its lineside assets.
Finally, Matt Atkins reports on exhibitors at Railtex and its Future Focus sessions which covered innovation, decarbonisation, and exports. Though there were many inventive solutions on display, he notes that the industry must work hard and smart to counter current challenges.
Editor
David Shirres david.shirres@railengineer.co.uk
Production Editor
Matt Atkins matt@rail-media.com
Production and design
Lauren Williamson lauren@rail-media.com
Adam O’Connor adam@rail-media.com
Engineering writers bob.hazell@railengineer.co.uk bob.wright@railengineer.co.uk clive.kessell@railengineer.co.uk david.fenner@railengineer.co.uk graeme.bickerdike@railengineer.co.uk malcolm.dobell@railengineer.co.uk mark.phillips@railengineer.co.uk paul.darlington@railengineer.co.uk peter.stanton@railengineer.co.uk
Advertising
Asif Ahmed asif@rail-media.com
Chris Davies chris@rail-media.com
Craig Smith craig@rail-media.com
Rail Engineer Rail Media House, Samson Road, Coalville Leicestershire, LE67 3FP, UK. Switchboard: 01530 816 444 Website: www.railengineer.co.uk
Rail Engineer Videos http://rail.media/REYouTube
Editorial copy to Email: news@rail-media.com
Free controlled circulation
Email: subscribe@rail-media.com
The small print
Rail Engineer is published by RailStaff Publications Limited and printed by PCP Ltd.
© All rights reserved. No part of this magazine may be reproduced in any form without the prior written permission of the copyright owners.
Part of: ® www.rail-media.com