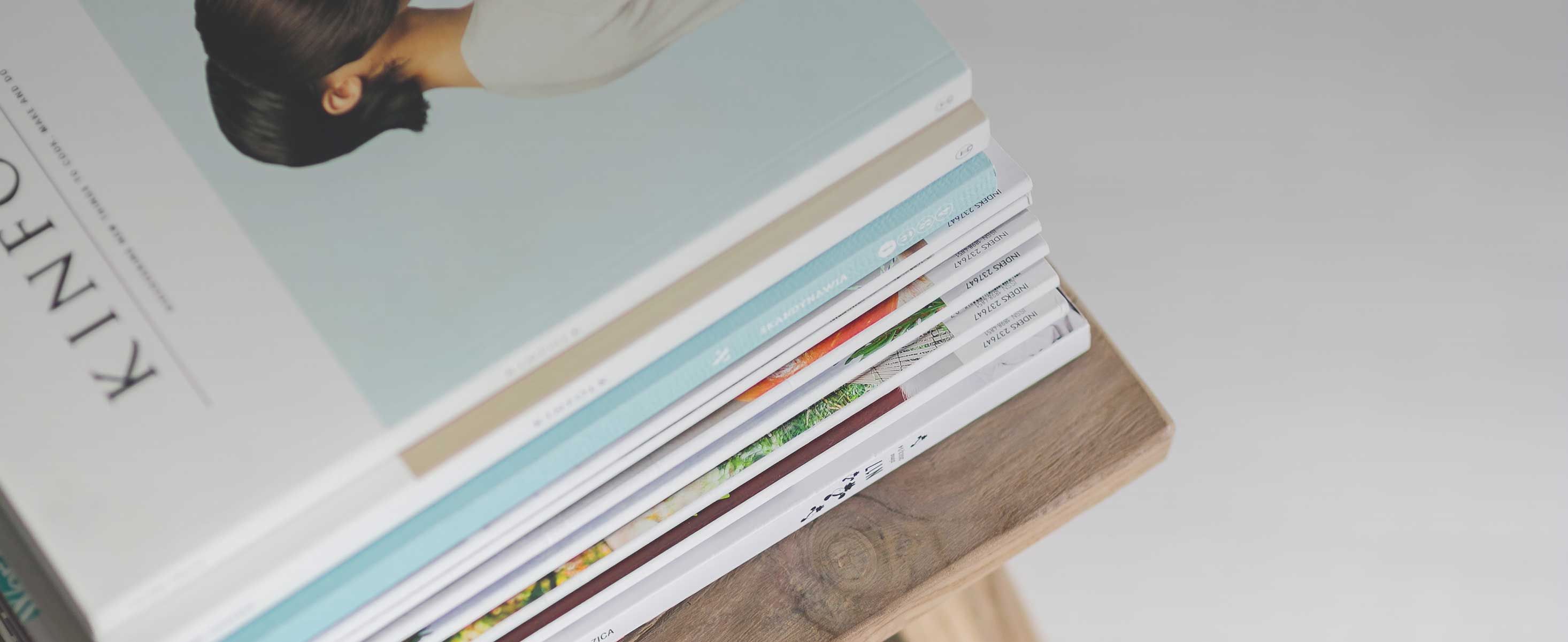
7 minute read
AUTOMATED DISCRETE (RAIL) DEFECT REPAIR
This article is about metallurgy, welding, and managing rail defects, three areas where your writer lacks expertise, having last welded anything as a trainee in 1971. At that time, in your writer’s rolling stock department there was a rule of thumb that, for structural components, rolled or forged steel was good, casting was bad and welding was dodgy. A lot has happened in the last 50 years, and there is now a huge body of knowledge that allows castings and welds to be applied confidently in high stress situations.
Rails have a hard life. The contact stresses can be high, resulting in transverse cracks that can develop under the rail head leading to loss of sections of rail, a defect type know as a squat.
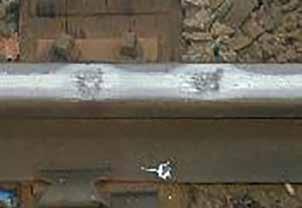

On the GB national network there are typically around 10,000 squats or other defects resembling squats reported annually, of which around 80% are less than 100mm long and around 65% are <15mm deep. In principle, the shallower defects take less time to repair than the deeper ones. The current process involves: machining the rail head using flame cutters and angle grinders to remove the defect, heating the rail to at least 343 C, Manual Metal Arc (MMA) welding with an appropriate grade of wire, followed by grinding to profile. This process is generally carried out in the dark by skilled welders, but they have limited ability to verify the quality of the repair. The work is cancelled if it is raining and the weld often fails within weeks or even a few days. An experienced operator can usually deliver only one repair per overnight shift. The alternative is to cut out a length of rail, typically 9.5 metres, and weld in a new length, another time consuming, costly, inefficient and not environmentally friendly process. So, consider this scenario; the ultrasonic team have been out and have recorded a large number of sub 5mm discrete cracks that can be tolerated unless they get bigger and a much smaller number of > 10mm cracks that the standard dictates must be attended to urgently. If you were the area track manager which repairs would you prioritise? Yes, the urgent ones, of course. But what if the process was quicker so that several repairs per night could be completed and in all weathers? And what if those welds were reliable and repeatable with the entire process recorded? Might you then be able to plan to repair all the sub 5mm discrete defects, largely eliminating the emergency repairs of larger defects? Enter the automated Discrete Defect Repair (DDR) machine which a group of Network Rail engineers saw demonstrated at the Ecclesbourne Valley Railway in January 2023. Rail Engineer was there.
Process Development
There are three aspects to successful automation on the railway: the technology, the machine that makes use of the technology, and the means of deploying it. An important secondary consideration is what to do if a machine were to fail part way through the process. The demonstration was very much about the technology and the machine. The technology was developed in a partnership between Jay Jaiswal of ARR Rail Solutions, and David Hydes of LWS Rail Machines whilst machine design, fabrication and programming of control software were undertaken by James Penty and Andrew Grundy of Pressure Design Hydraulics Limited. The project is sponsored by Network Rail under the In2Track/Shift2Rail programme.
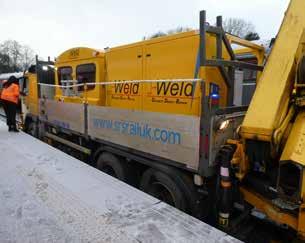
Technology
Jay Jaiswal, founder of ARR said that many years ago he developed a low temperature pre-heat system/submerged arc weld restoration process that was successfully patented by Corus/Tata Steel/British Steel and then transferred to the current owner ARR. The novel process was used for in-situ restoration of side worn embedded grooved rail without compromising the polymer material used to embed the rail in the street. This process is now extensively employed on light rail systems by Inline Track Welding who, at the time of writing, were working on the Blackpool system.
Jay said he had further developed this process to enable repair of discrete defects with pre-heating at 60°C to 80°C compared with the current manual process where Network Rail’s standard specifies the already mentioned value of ‘at least 343°C’. Moreover, the weld deposition would be applied automatically. His remit for the development was:
» To increase/maximise repair integrity, process consistency, repair productivity, and simplicity of operations through process automation and standardisation;
» To reduce/minimise the cost of repair, track possession time, complexity of equipment and skills;
» Whilst avoiding or eliminating high preheat temperature, need for re-stressing and (if the only alternative was rail replacement) aluminothermic welds.

Prototype machine: machine onto the track.
The demonstrator machine has wheels to allow it to be pushed along the track over short distances to enable accurate positioning over identified defect. For the demonstration it was delivered to site using a large road/rail vehicle (RRV) with a built-in crane.

Once on the track the machine is connected via various power, data, and air/vacuum lines to a generator/control unit that stayed on the RRV. The machine is not equipped with ultrasonic equipment to verify the location and size of defects. Instead, it relies on a pre-identified defect being marked on the rail. The machine is manually pushed over the defect and a laser pointer employed to position the machine precisely over the centreline of identified defect. A tablet is used to set up the length and depth of milling, to start/stop the process, as well as monitor the machine though various temperature, current, and other sensors.
Once the “go” button is pressed, the following routine is carried out automatically:
» Once in position over the defect, the machine is locked into position through automatic deployment of multiple hydraulic clamps;
» A pair of lasers are traversed over the rail head to establish the incumbent rail profile either side of the defect to be repaired. This provides the baseline to ensure precise re-profiling across the repaired area so that the passing wheel does not experience any discontinuity;
» The heaters, that had been switched on earlier, are automatically engaged to both sides and undersides of the rail head and start the process of pre-heating to the required temperature of 60°C to 80°C;
» The rail is milled to a predetermined depth to remove the defect. Typically, this is 100mm long and can be up to 12mm deep, although options are possible;
» The machine measures and snips the welding wire to the precise stickout length required as well as undertaking a self calibration process to ensure the wire is positioned precisely in the excavated cavity for the start of welding.
» Once the rail reaches the set temperature, the welding operation is started automatically and the welding head is traversed across the rail head in a square-weave pattern (unconventional for the rail industry) to cover the excavated length;
» The deposited layer is allowed to cool for a prescribed period following which a peening gun is automatically traversed over the welded area to remove the slag in preparation for the next layer of deposition;
» The weld cooling period is used to snip the bulb at the wire tip, cut to the precise stick-out length, and complete the selfcalibration process;
» Deposition of the next weld layer follows the peening process and this sequence of operations is repeated to execute a total of four layers of weld deposit;
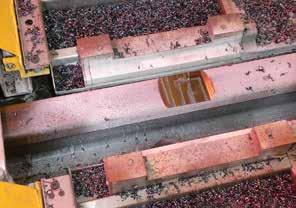
» After deposition and peening of the fourth layer, forced air cooling knives are traversed over the repaired area to cool the rail down to the specified temperature of <50 °C;
» Once the required temperature is reached, the CNC milling operation is initiated to achieve near perfect blending across the repaired area.
FIGURE 7 - DDR machine illustration (Pressure Design Hydraulics).
FIGURE 8 DDR machine photographed in situ.

FIGURE 9 Completed ‘excavation’ of defect. Rail clamps retracted.
FIGURE 10 Completed weld.
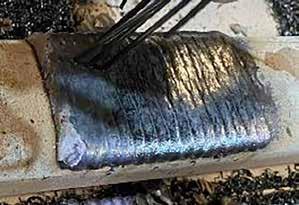
FIGURE 11 Peening to remove slag (Jay Jaiswa).
The machine minder has an important role, inter alia, to make sure the right weld wire is used, to change the milling head if it wears during milling operations (a two-minute task), and to use a vacuum wand to clear swarf and other debris from around the track at the end of the process. Clearly this person does not have to be a welder but welding skills might be useful in case corrective action has to be taken if the machine failed mid task. This was the first test on a working railway and there were a few teething troubles, but none of this detracted from the completion of an automatic rail repair and, since then, Jay reported, all have been understood and have been fixed. The repaired sample has also been examined and is compliant with relevant standards.
FIGURE 12 - Final profile machining in operation in workshop trial (Jay Jaiswal).
FIGURE 13 - Completed and machined weld (Jay Jaiswal).
The key requirement is, of course laboratory assessment of the visually excellent quality of the finished weld which was later confirmed. Network Rail’s route and region representatives were impressed. Since then a patent has been filed for the developed process and equipment and is planned for publication by the UK patent office followed, hopefully, by the grant of a patent. An international patent has also been filed.
Deployment
In a later conversation with Network Rail’s project managers Adam Glover and Alex Mould, together with technical expert Mike Poulter, it became clear that more work is needed on the deployment method. Mike said that deployment using a crane is unlikely to be viable, but they are thinking along the lines of a rail mounted vehicle with a tail lift type device that could quickly lower the machine onto the track and recover it after welding has been completed. Another thought is that the DDR unit could be deployed using the Mobile Maintenance Train (MMT) that is currently undergoing Product Acceptance. Southern Region engineers see great potential value in using MMT for this purpose, for example.
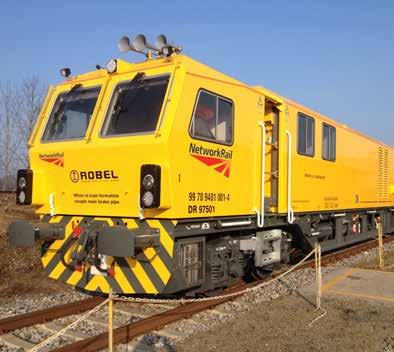
Mike said that once the weld repair processes are developed for each rail type and the machine is fully developed, he was confident Network Rail’s welding professional authority will be able to approve them in order to realise the true potential of DDR. “Who wouldn’t want quality, repeatable and recorded welds?”, he observed.
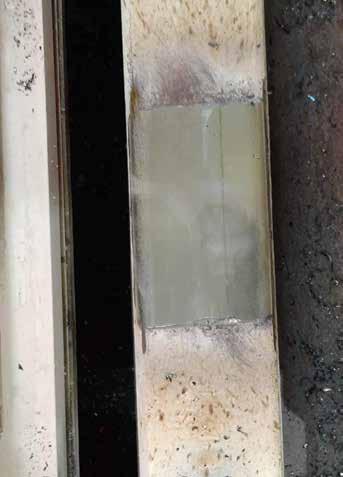
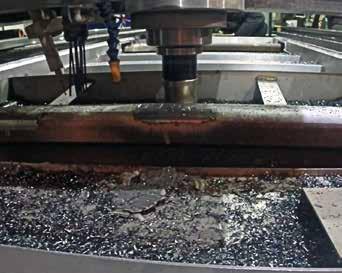
Adam concluded by saying that, in March 2023, a further test at Wirksworth would be carried out before a trial on Southern Region during Summer 2023. He would expect to see roll out on a production basis in 18 to 24 months. He expected the current development funding (EU Shift2Rail programme) would come to an end but Network Rail will continue to develop the DDR machine/process within R&D going into CP7.
Credits: Thanks are also due to Ecclesbourne Valley Railway’s Operations Manager Helen McKortel, who ably organised site access and who observed that tests such as these help provide much needed income for Ecclesbourne and other heritage railways when closed to the public during the winter.
