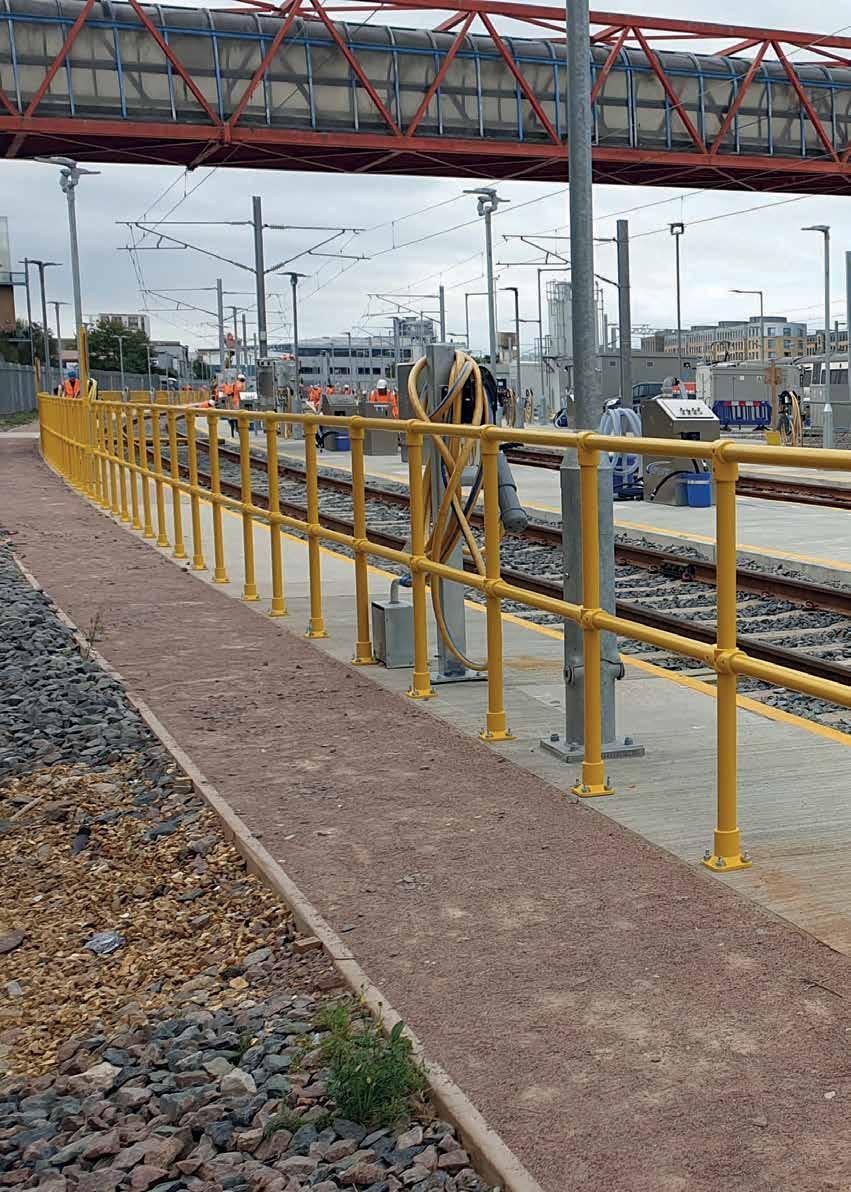
2 minute read
DEVELOPMENT JOURNEY
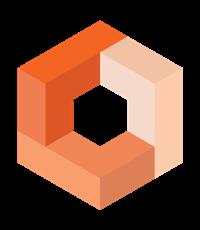
The machine and the techniques it includes have been in development for around 14 years.
Development Of The Techniques
Preheat:
The DDR process only requires pre-heating to 60°C to 80°C to achieve at least comparable weld quality and meet the microstructure and hardness specified in relevant standards. The technique was first developed around 20022006 to help Sheffield Supertram restore the worn gauge corner of their embedded track. Supertram had bought a machine for welding the gauge corner without pre-heat which was unsuccessful. Jay Jaiswal developed low temperature pre-heat system/submerged arc weld restoration process (patent originally granted to Corus/Tata Steel/British Steel and subsequently taken over by ARR Rail) to provide a measure of pre-heat without compromising the polymer material used to embed the grooved rail. This has been used for many thousands of metres of embedded rail, most recently in Blackpool.
Between 2006 and 2008 early Proof of Concept trials of the idea of low preheat process for in-situ repair of rail head defects were progressed slowly through Corus/Tata Research & Development. Some trial weld repairs using laboratory facilities and pre-milled cavities were undertaken to test the concept. Although using low pre-heat is common with the grooved rail process, discrete defect repair is distinctly different because of the use of Flux Cored Arc Welding, the square weave operation to control heat dissipation, and the total automation from start to finish.
The process for automated repair on plain line rail grades R260 and HP335 has taken place and will be developed for other rail grades.
The challenge now is to obtain approval from Network Rail for both the low preheat weld restoration process and the machine for automated delivery of the process (patent pending).
Combining Machining And Welding Into One Machine
Between 2009 and 2011 the first prototype was developed. This is when Jay Jaiswal engaged with David Hydes who owned Lincoln Welding Supplies (before he started LWS Rail). A third party built a machine to try the concepts and although, as a first prototype, it lacked the degree of automation of the current unit, it served the purpose of demonstrating that milling and welding processes could be incorporated into one unit for in-situ repair of rail head defects. Furthermore, the supporting process stages such as preheating, weld peening, and reprofiling remained manual.
There was a quiet period between 2011 and 2015 with Jay’s retirement from Tata Steel and setting up his own company (ARR), although it was agreed he could take the development with him. Some practical work to optimise welding parameters and gain further confidence in the process was undertaken as ARR funded work. However, considerable internally funded effort was spent on developing ideas on machine design and automation.
2018 was the start of the involvement of Network Rail started though IN2Rail, then In2Track2 and In2Track3 programmes under the generic Shift2Rail banner. The funding from these programmes provided for the construction of the current machine and based on the confidence from the DDR process, a second machine for the restoration of worn crossings. Pressure Design Hydraulics was contracted to build the machine and write the software - some 75,000 lines of code.
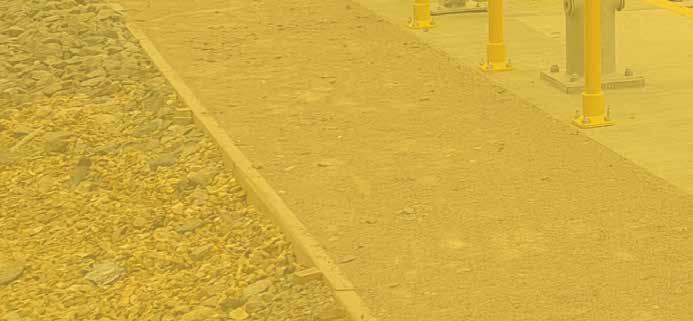
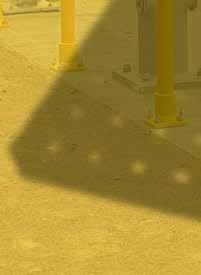
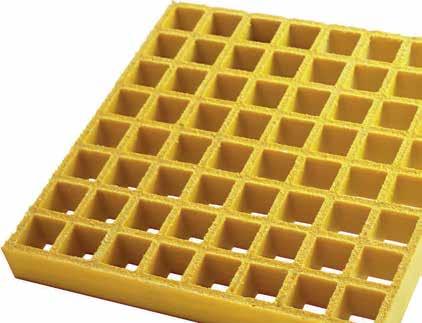
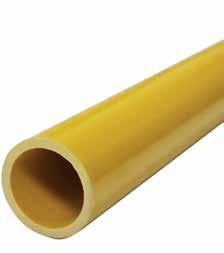