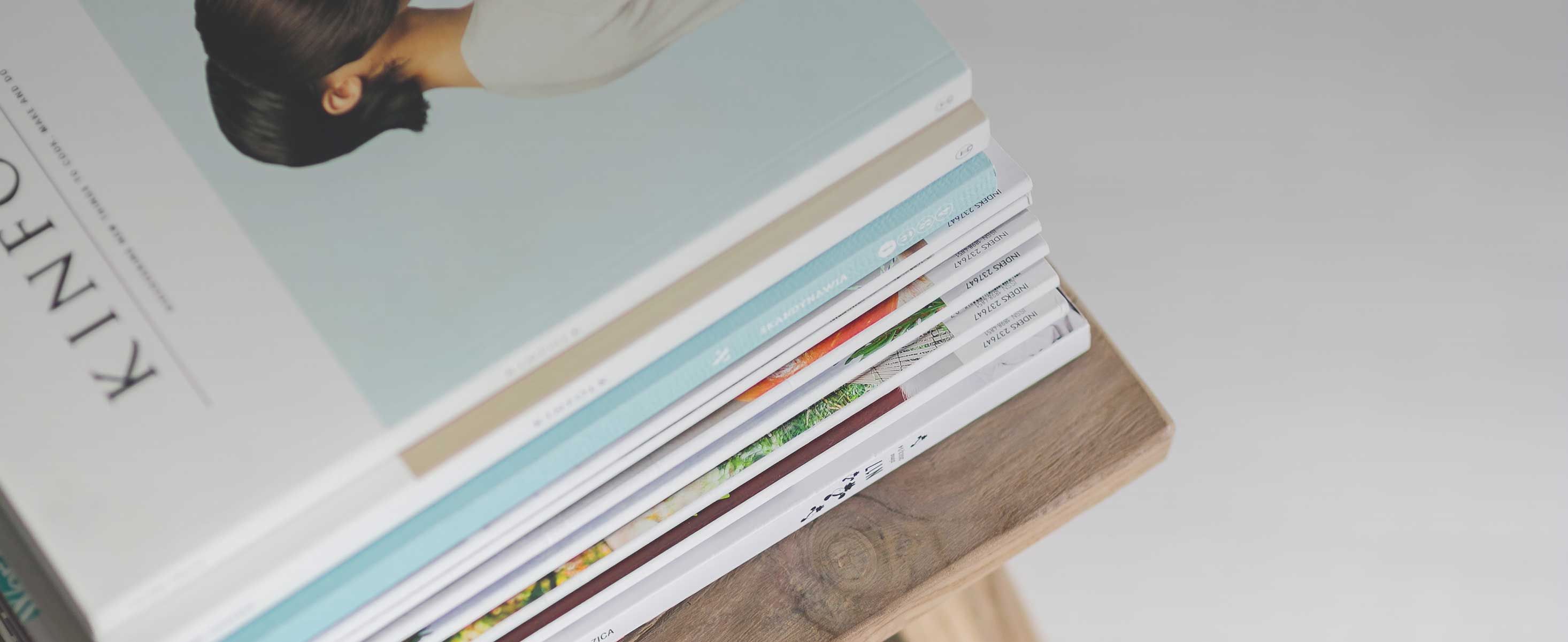
2 minute read
VEHICLE/TRACK SYSTEM INTERFACE AND ADHESION ANNUAL SEMINAR
Held in Manchester and online, the annual reports of the Vehicle/Track System Interface Committee (V/T SIC) and the Adhesion Research Group showcased a variety of research and development papers. As has been said before, even though railways are coming up to 200 years old, there is still much to be learned about the Vehicle Track Interface.
Squats
The project aimed to model the conditions that would lead to the formation of squats, a form of rolling contact defect in rails.
He described a working hypothesis that a combination of contact stress and tangential force appears to be a reasonable way of forecasting squats. Although just one parameter has previously worked reasonably well to predict rolling contact fatigue (RCF), a combination of different models for what initiates and makes squats grow might be needed.
Rcf And Spalling
He highlighted the need to account for the different effects of leading and trailing wheelsets within a bogie and the effects of different vehicles in a train which may be travelling at different speeds though the curve. He presented force/direction plots for two locations which produced very different results: in one location, leading and trailing wheelsets have similar contact positions, with forces in different directions, whereas in another location, leading and trailing wheelsets have different contact positions and less interaction of the forces in different directions.
Mark’s final remarks were about wheel RCF which is an emerging issue on some newer fleets. He said that wheels are more complex to analyse than rails given braking and traction forces, curves and cant deficiencies, and running direction reversals. All these need to be understood - an area for more work!
Monitoring Wheel Bearings
Starting with the V/T SIC presentations, Dr Mark Burstow, Principal Vehicle Track Dynamics Engineer at Network Rail, reported on the work of the permanent project group. He focussed on rail squats, spalling, and wheel rolling contact fatigue.
Mark explained that spalling of material from the head of the rail is generally, but not exclusively, a low rail/ tight radius curve problem and whilst the mechanism is understood, it is a challenge to predict the location and magnitude of spalling.
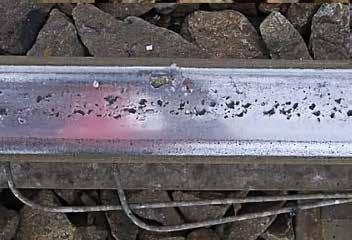
Rail Engineer has reported extensively on monitoring passenger train wheel bearings with both axle box mounted sensors and trackside monitoring kit. We have reported the value of such monitoring to assess bearing and wheel tread condition leading to better planning and sometimes reducing the frequency of maintenance.
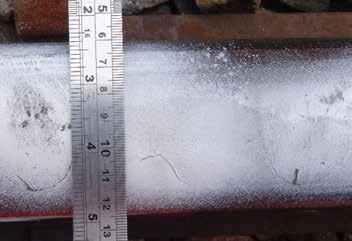
Vehicle mounted sensors can also provide information about track condition.
Several freight train derailments have been caused by defective or collapsed axle box bearings. Accident investigation reports have recommended research into improved axle bearing monitoring. Professor Adam Bevan from the Institute of Rail Research, Huddersfield University, reported on the business case for dynamic response monitoring of freight wagon axle bearings (Acoustic monitoring of axle bearings for freight vehicles, T1267). The university’s work evaluated several on-train and wayside systems and concluded that there is a good business case for monitoring freight vehicle axle bearings using wayside thermal and acoustic monitoring technology. Onboard sensors were not favoured, partly because of the sheer number of sensors