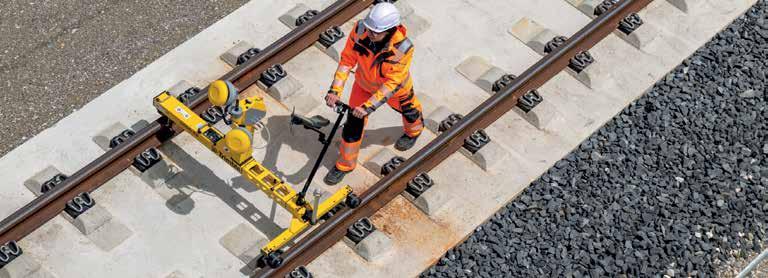
3 minute read
Trimble Track Survey & Scanning
that would be required and partly because there is no electrical supply on the wagons. The technology review also highlighted that failed or missing lubrication cannot easily be detected by acoustic/ vibration monitoring alone. Thermal monitoring is more suitable in this case, however, but the time from detection to catastrophic failure can be short. Effective lubrication is therefore an essential part of a working good condition bearing system.
Lubrication
Keith Mack, quality standards manager at LNER, Chair of the BSI group on roller bearings, and Chair of the RSSB Wheelset Management Group, took up the issue of lubrication management with “what to do when your standard lubricant is withdrawn from the market?” Renolit MP3, a lubricant used extensively and for a long time, was withdrawn from the market because the sodium nitrite used in its composition had been banned. The Bearing Group within the Wheelset Management Group managed the change by creating a framework for managing the change; GMGN2682, Approval of Changes to Axle Bearing Lubricants.
The Group supported discussions with operators whilst working with potential suppliers on an alternative. Generally, Mobil Mobilith SHC100 lubricant was adopted although there are alternatives. There has been good take up for passenger vehicles with no known problems.
Keith also cited the Ohio derailment on 3 February 2023, where many wagons carrying hazardous materials became derailed when an axlebox failed. He pointed out that axlebox failures are few, especially considering the number of wagons in service but when they happen, the costs can be huge, perhaps large enough to put an operator out of business.
With Trimble® GEDO systems, modern technologies are individually combined according to the respective applications. The Trimble GEDO CE 2.0 track measurement trolley can be equipped with total station, GNSS, laser scanner and inertial measurement technology. With evolving requirements and new development requests, the exible and modular design allows Trimble GEDO systems to be adapted.
High Temperatures
While Brian Whitney, Engineering Expert, Track and S&C Network Rail, usually talks about managing rail to try and reduce rail breaks to near zero, this year he talked about infrastructure performance during the hot weather in summer 2022. As everyone probably knows, rail expands in summer and contracts in winter. Traditional jointed track allows a level of expansion at the joints but there is no such opportunity with continuously welded rail (CWR) which, unless adequately restrained, will either expand, causing damage, or buckle. CWR theory sensibly states: “CWR track shall have the buckling strength required to withstand the environmentally and operationally imposed loads for the range of expected operating conditions.”
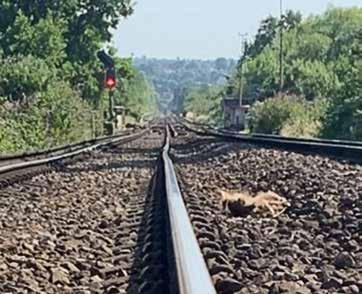

A buckle is generally not created solely by hot weather and high rail temperatures, but by the presence of at least one other factor such as:
Flat bottom rail on concrete sleepers, well bedded into strong ballast with appropriate side shoulders, generally delivers this objective. As well as buckling risk, track forces induced by high temperatures can also affect other track equipment, such as high compressive forces pushing the rail ends together at insulated rail joints causing track circuit failures and CWR exerting forces on switches and crossings leading to points failures when the point operating equipment is forced out of adjustment. Brian added that the opposite – high tensile forces during cold weather – lead to an increase in broken rails and affect the performance and reliability of S&C. In general, the maximum compressive and tensile stresses allowed are known and this allows the determination of temperature range to stay within these limits. The point at which there is no longitudinal stress is known as the stress-free temperature (SFT). On plain line, the right stress level can be achieved by cutting out a measured section of rail, literally stretching the two ends and re-welding.
» Ballast disturbance (e.g., tamping, stoneblowing, opening out, lifting and packing, or slewing track)
» Ballast deficiency (e.g., insufficient ballast in the cribs or on the shoulder)
» Seized joints (e.g., over tightened fishplate bolts, lack of lubrication)
» Low joint closure temperature because expansion gaps are too small or too few in jointed track with rail lengths
>18 metres
» Poor condition of fastenings, coach screws etc., leading to rail creep
» Low stress-free temperature
» Poor top and/or line (e.g., voiding sleepers, misalignments)
» Disturbance due to sleeper and bearer changing.
Managing Buckling
UK engineers manage buckling risk by determining the temperature of the rail, having a record of the SFT, a record of any deficiencies or disturbances that affect the lateral stability of the track through a Critical Rail Temperature (CRT) Register. This information is used to calculate each site’s CRT to
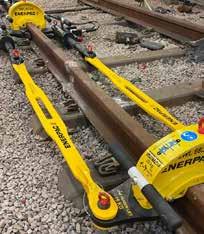