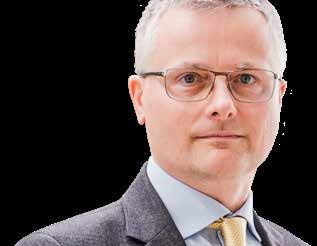
23 minute read
NCB: INDEPENDENT ASSURANCE
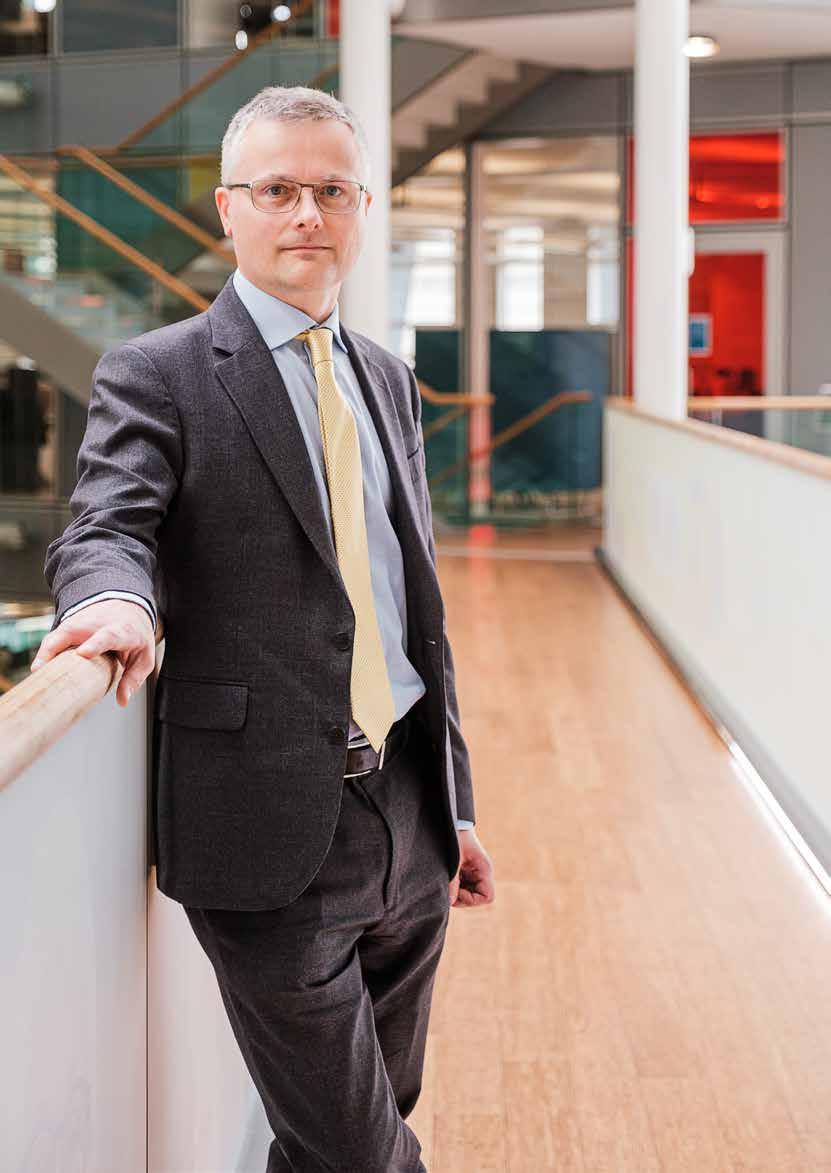
Operating as an independent subsidiary of Network Rail, Network Certification Body (NCB) is the UK railway’s leading infrastructure assessment and certification body. NCB celebrated its 10-year anniversary on 4 April and RailStaff caught up with Managing Director Sam Brunker to discuss the importance of its work, structural change within the industry, and the body’s future relationship with Great British Railways (GBR).
Many thanks for joining us, Sam. To start, would you mind giving us a brief overview of NCB, its work, and its relationship with Network Rail?
NCB was set up and started trading exactly 10 years ago. We’re made up of around 50 engineers specialising in safety and risk management, covering each of the main railway engineering disciplines. We are a subsidiary company of Network Rail and we provide independent assessment and certification services required under legislation to Network Rail and other industry clients. The reason we’re a subsidiary is to meet accreditation requirements that we must comply with to demonstrate sufficient independence from our parent company, which is also our major client.
Our main focus over the last 10 years has been on infrastructure projects, but over the last year or so we have consciously branched out into offering wider assurance services, tailored to the client’s needs. This allows us to apply our niche expertise more broadly and to add value in other areas, such as general safety management and workforce safety as well. We’ve had a few clients in that space over the last year or so, and it has proved to be very successful.
Can you explain the principles of assurance? Why is it important?
Assurance is about having evidence that the right thing is being done. It’s a form of risk management. The greater the consequences of what you’re doing going wrong, the more certainty you need that it’s being done right. A good assurance framework will tell you as early as possible that something’s not right so you can fix it before it’s too late and when it will be much cheaper to do so. NCB has developed a progressive assurance approach that we call PAM (Progressive Assurance Methodology) to help our clients get the most value from this concept.
Another important principle is that the people doing the assurance need to be independent from those involved in what is being assured, and that exists at different levels. Network Rail, for example, has its own internal assurance framework, providing it with a level of confidence in what it’s doing. But NCB provides what is sometimes called third-party assurance that’s required by legislation for more significant activities. It’s complementary to the internal assurance and is needed given the rail industry’s low tolerance for accidents because of their huge impact.
What are the main safety issues currently facing the rail industry? Can you discuss any serious safety issues NCB has uncovered, and how these were put right?
It’s important to state that every fatality is one too many, but without taking away from that, it is a fact that on most comparators our railway has an impressive safety record. I think a key strategic safety issue the rail industry faces right now is to plan and manage the significant changes that are anticipated in a way that prevents our safety record suffering a setback. The industry is under massive cost pressures, and this rightly means that there is no choice but to modernise and to become more efficient and effective. But the safety risks associated with the changes need to be properly identified and managed, and they need to inform the changes so that there is confidence that safety will not deteriorate.
RAIB has just issued its report on Carmont and, amongst many findings in that report, there are clear issues identified in relation to assurance, including the handoffs between the various organisations involved in designing, constructing, and improving the drainage at that location. Going forward, it will be important that any changes in relationships between the industry players do not make these types of issues worse.
NCB has provided independent safety assessment for around 70-80% of infrastructure projects over the past 10 years so, yes, we have uncovered some serious safety issues in our time. I’d rather not discuss the specifics on this, but in terms of how they were put right what I can say is that it always costs lots of money and creates delays. We in NCB are proud to have played our part in making the railway safer in these examples but it’s much better for everyone if the internal assurance regime I mentioned earlier picks up such issues before we do.
The fact that we do occasionally uncover some serious issues demonstrates the need for what we do. All the other less serious safety issues that we uncover, which are far more numerous, help to remove the precursors for the more serious ones.

You’ve mentioned that the Rail industry is facing major changes. How does this expose the industry to increased risk and how can this be mitigated?
I think it’s mainly around the relationships between the different players. If safety responsibility, for example, is currently with one organisation, and it moves to a different organisation, there’s a risk that that transition won’t happen effectively. Or, if one organisation is assuring what another organisation is doing, that assurance regime has got to be effective at providing decision makers with real information; and the formal relationships between the organisations must be designed to encourage and not inhibit this. There’s also risk around the numbers of people – have you got the correct numbers and types of people doing the various activities?
As for how these risks can be mitigated, I’d say apply a robust risk management framework from the beginning, for example by following the Common Safety Method for Risk Assessment and Evaluation (CSM-RA), and have your application of this independently assessed by an organisation such as NCB. And, let the risk assessment be a driver of the decision making, not just a side show.
How important is NCB’s independence from Network Rail? How does it strengthen NCB’s ability to accurately report safety issues?
We have to satisfy our external auditors that we comply with regulatory independence requirements, and this includes an appropriate degree of independence from Network Rail in the way we are set up. There are a few options as to how this is achieved but the principle of what the accreditors are looking for is separation, so that our assessors are not under pressures that conflict with the need to report findings impartially. NCB being a separate legal entity is a good way of ensuring that. What you don’t want is the pressure that naturally comes to bear on projects nearing completion cascading onto the independent assessors in such a way that inhibits them reporting safety issues.
You recently authored a white paper – The Value of Independent Safety Assurance. Can you tell us what this covers and the motivation behind its development?
The white paper covers a lot of what we’ve been talking about. I wrote it to inform the industry debate in this space, given the increasing importance of getting it right as we head into a period of significant change. It is important for rail to learn from other industries and the white paper refers to two major incidents - the Boeing 737 Max air crashes and the Grenfell tower tragedy - to which compromised independence in the certification process was a contributing factor. I want to help the rail industry avoid making similar mistakes as it considers restructuring.
What will be NCB’s relationship with GBR when it replaces Network Rail as the operator for rail infrastructure in the UK? Do you have concerns for the future independence of NCB?
It is too early for NCB’s relationship with GBR to have been considered yet. However, perhaps a more important question is, how will GBR obtain the necessary internal and thirdparty assurance for its safety critical activities? And in the meantime, who is going to provide the independent safety assessment of the GBR organisational design, as required by CSM-RA? That’s a question that I think needs to be asked now.
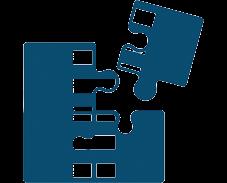
PEOPLE MAKE MISTAKES
AND ALWAYS WILL
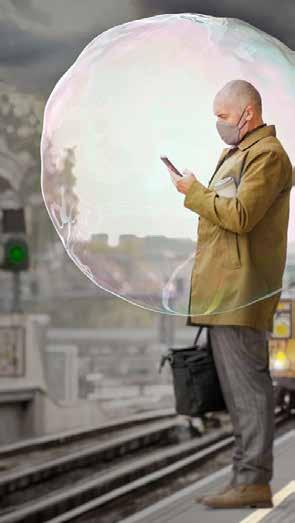
One of the factors that leads to accidents and incidents is the behaviour of those who travel or work on the rails. Often, this is a result of individuals not following rules and/or procedures but it is sometimes a reflection of failures and miscalculations on the part of management or supervisors. Errors of judgement are a fact of life, and some accidents are unavoidable, but passengers, workers, and those in charge can take steps to minimise the risks.
Colin Wheeler.
Hand trapped in train door
On 14 January at Wood Street Station in North East London, a passenger attempted to board a train but became trapped when their hand was caught in the closing rear doors of the fourth car. The train was the 08:22 departure. As the train moved off, the passenger was forced to run alongside it for approximately 20 metres until the train stopped. The doors were then released, and the passenger’s hand was freed without injury.
Following a preliminary examination and an assessment of the gathered evidence, the Rail Accident Investigation Branch (RAIB) has decided to publish a Safety Digest. Arriva Rail London, which operates the London Overground on TfL's behalf, is undertaking a full investigation and working with the RAIB. A frightening headline
The RAIB website recently reported a “Near miss with two trackworkers and collision with a tree on the line” at Uphill Junction near Weston-super-Mare, Somerset. This occurred at around 13:10 on 14 January. The train was travelling at 95mph when it struck part of a four-metre tall, 165mm tree at the junction. The workers were part of a team working on vegetation on the embankment adjacent to two running lines that were both open to traffic. After felling, the tree came down the embankment and landed in the cess.
The workers went onto the open line and tried to remove the tree. They became aware of the approaching train and moved two metres clear “several seconds before
London Gateway derailment
RAIB is also investigating freight train derailment that occurred at 05:45 on 24 December. The 22:35 GB Railfreight service from Hams Hall (near Birmingham) to London Gateway derailed on the Down Thames Haven line on the approach to London Gateway Port, near Stanford-le-Hope in Essex.
The freight train involved was formed of a class 66 locomotive and 33 wagons, all of which were of the ‘container flat’ type. The initial derailment occurred on Network Rail managed infrastructure, when the leading bogie of the 12th wagon derailed on plain line at about 13mph. The train continued travelling for around 500 metres after this initial derailment, before it reached a set of facing points within the port boundary, when a further four wagons derailed.
The first to derail was the middle wagon of an Ecofret2 set of three which were semi-permanently interconnected by steel draw bars. The wagon that derailed was the only wagon not loaded with a container. There were no injuries, but extensive damage to track and signalling within the port boundary resulted. Temporary repairs were made so that the port could re-open on 4 January. An RAIB investigation is underway looking at wagon characteristics and loading, track condition and the way in which the train was driven.
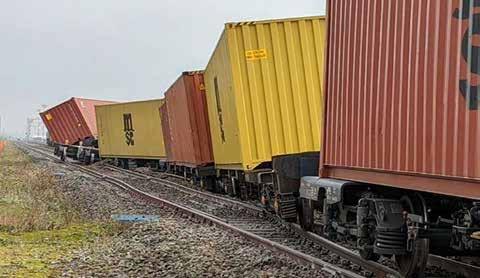
the train passed”. The train hit branches of the tree and scattered debris. Their attempt to move the fallen tree was unsuccessful and moved it to a position where it was foul of the running line. The bulletin comments that this was “one of several recent safety incidents involving de-vegetation works beside the track each of which could have been much more serious”. RAIB has decided to publish a Safety Digest which will hopefully examine how the work was planned. passengers, driver and guard evacuated onto the track and were then taken back to Reedham Station by a rescue train. No-one was hurt and the train was recovered undamaged, but the line remained closed for a week while repairs were made.
A “significant tidal surge” affected drainage from the Broadland rivers and raised the level of the New Cut. The Environment Agency’s flood warning had not predicted a flood level higher than the flood defences. RAIB’s investigation is underway.

Acetylene or propane?
Network Rail’s Safety Central website and its Safety Bulletins are usually concise and to the point. One issued on 20 December refers to a technical issue but is arguably indicative of less than complete communication between local workers and a contractor’s choice of gas. Capital Delivery Contractors went into Sevenoaks Tunnel to cut out some metalwork from a ventilation shaft using propane but were told by the maintenance welding team that they could not use propane inside the tunnel. Consequently, they removed their oxy-propane equipment. However, the contractor had assessed the risk and identified the problem of using acetylene which is lighter than air so proposed propane as a safer alternative.
Network Rail’s standard for ground level welding recognises the use of acetylene because propane could gather at low level and create fire or explosion risk. The Safety Bulletin says that a review of Network Rail’s standards is now underway and its listed discussion points comprehensively address risks and method statement issues. There is no reference to the management failure to keep their own welding people aware of contractors working in their geographical area. Train driver fatality near West Worthing
On 1 February a train driver was struck by a passing train and fatally injured near West Worthing. The train had been driven from Brighton before entering the siding where it was timetabled to wait before returning to West Worthing Station. It would then form the next passenger service back to Brighton. At about 20:33, a second train travelling at around 33mph passed the stationary train in the siding some 300 metres west of West Worthing Station. It struck and fatally injured the stationary train’s driver who had left the train cab and descended to track level. The news story from the RAIB, whose investigation is underway, says "train drivers should not normally need to leave their trains as part of their duties while waiting in this siding”.
Near miss with LOWS operated warning system
At 10:08 on 28 February, a train driver reported a near miss with track workers at Sharnbrook East Midlands who were regulating ballast protected by a Lookout operated warning system (LOWS). Details can be found on Network Rail’s Safety Central website. The LOWS Controller “received a warning which he cancelled in error” for the Up line. Immediately afterwards he received another warning which he wrongly assumed was a reinstatement of the earlier one.
A train on the down Line then passed the team who were in a position of safety. The up line train, for which the LOWS warning had been wrongly cancelled then came round the curve. The controller shouted for the team to stand clear, and they moved to both sides of the track. The driver saw them move clear and reported the incident to the signaller.
Stopping the use of lookouts was overdue when it eventually happened but should we still be using LOWS in the twenty-first century?
Track formation washed away
At around 07:45 on the morning of 30 January, the 07:25 Greater Anglia Norwich-to-Lowestoft train ran into a section of track where ballast and the formation had been washed away by flooding water from the Haddiscoe New Cut Waterway. This Waterway is northeast of the railway and crosses it, discharging into the Haddiscoe Marshes. Approaching the area, the train driver saw standing water on the tracks ahead and braked. The train consisted of three coaches and a power car which came to a halt with its front carriage above the flowing water.
During the next 20 minutes the water caused the track to sink, and the first carriage tilted both forwards and sideways. The driver attempted to reverse back from the undermined track, but this failed due to the angle of the first carriage. Consequently, the five

Colin Wheeler.
REPORT 02/2022: DERAILMENT OF A PASSENGER TRAIN AT CARMONT
On March 10 the Rail Accident Investigation Branch (RAIB) published its report 02/2022 into the accident that occurred at around 09:37 on the morning of Wednesday 12 August 2020, when a passenger train derailed at Carmont in Aberdeenshire resulting in three fatalities. A briefing for the media took place in Aberdeen on 10 March with Simon French, RAIB’s chief inspector making a presentation and answering questions.
Overview of the dranage system (locations marked 'CP' are catchpits).
The 20 recommendations indicate that radical action is needed by most of the organisations involved and hopefully this will be stimulated by the actions of the Office of Rail and Road (ORR), Procurator Fiscal so that the Great British Railway (GBR) organisation is more successful. INVESTIGATIONS
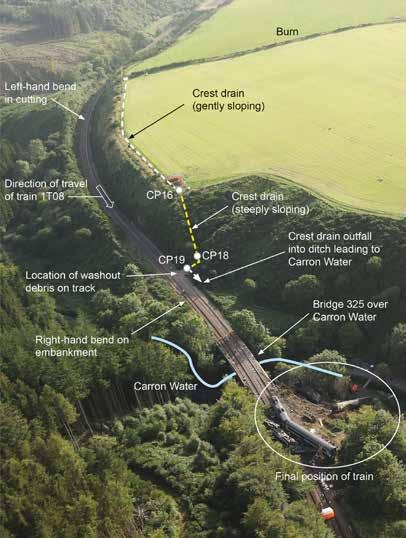
The wording of the preface to RAIB’s reports is especially relevant. It states that: “It is inappropriate that RAIB should be used to assign fault or blame or liability, since neither the investigation nor the reporting process has been undertaken for that purpose. RAIB’s findings are based on its own evaluation of the evidence that was available at the time of the investigation and are intended to explain what happened and why, in a fair and unbiased manner.” Other investigations by Police Scotland with British Transport Police and the ORR will be of interest to the Procreator Fiscal in Aberdeen.
NOT CONSTRUCTED AS DESIGNED
RAIB’s investigation found that the accident was caused by a French drain and the ground immediately surrounding it; installed in 2011/12 as part of a scheme to address earthwork stability problems. The drain was a 450mm diameter perforated pipe with a gravel filled trench. It ran for 306 metres alongside a field edge at the top of the slope and then downwards at a one in three gradient for 53 metres to track level. Catch pits were sited at intervals for inspection and maintenance.
On 12 August 2020, two inches of rain fell between 05:50 and 09:00, a one in a hundred-year frequency event. RAIB’s report states bluntly that “the drainage system was not installed according to the design drawings”. A low artificial ridge or bund was constructed which concentrated the water flow into a short length of gravel filled trench. Consequently gravel, and stony material was washed out. The drainage pipe trench was filled with 20-40 mm gravel and “its use in such a steeply sloping trench increased the likelihood of it being washed away.”
Aecom (appointed by RAIB) advised that the drainage system as designed would have safely accommodated the water flow on the morning of 12 August. But Carillion did not construct it in accordance with the design. The most significant difference was the bund which was built outside
Network Rail’s land and diverted water into a gully, increasing the likelihood of a gravel fill washout. No evidence was found of Network Rail being notified of this bund’s construction.
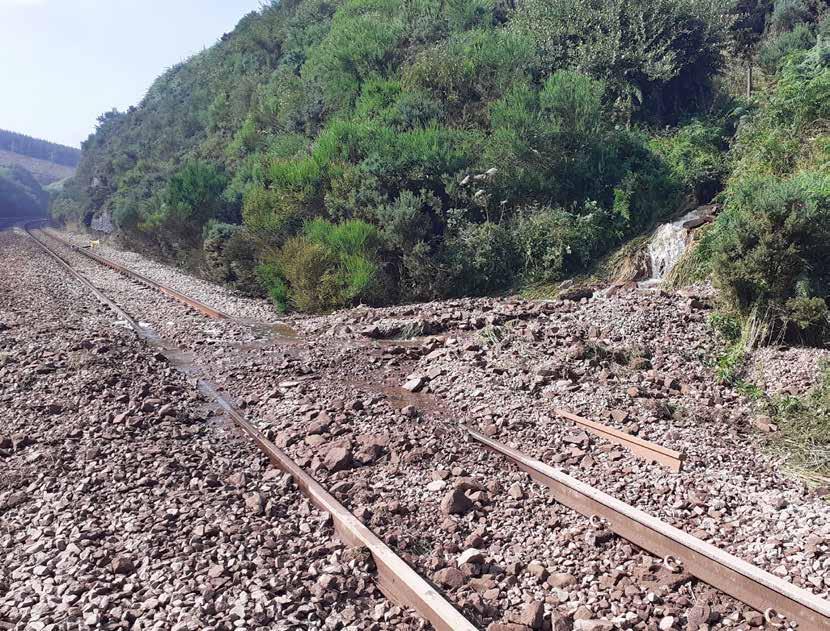
UNNOTIFIED DESIGN CHANGES
Additionally, RAIB uncovered other differences between the designs and the drainage system that was installed including: Pre 2010 drainage not connected into 2011/12 drainage at catchpit 18; catchpit 18 being relocated; lack of textile lining to drainage trench (used to prevent fines clogging up the drain in the area of the washout); holes cut in catchpit sides significantly larger than entering pipes; and a pipe bend not coinciding with a catchpit just a metre downslope of catchpit 18. No evidence was found of any of these changes being referred to the designer.
Arup was the designer and Carillion was responsible for delivering the works as designed. Any changes should have been notified to Arup but none of them were. The report says that Network Rail’s project team was probably unaware that the 2010/11 drain differed significantly from the design and were not required to check it by Network Rail’s business processes.
SEVEN YEARS BUT NO INSPECTIONS
As built drawings were a requirement, but the RAIB investigators found no evidence of their being provided. They are used to assist with future maintenance and are required by the Construction (Design and Maintenance) Regulations 2007. RAIB sample-checked 64 projects and discovered that “more than half of them were missing any trace of a Health and Safety file”. Of 11 sampled drainage projects, five were not transferred into the Network Rail asset management system.
In December 2012 the adjacent landowner visited the sloping drainage system and took a picture of the steeply sloping drain uphill of catchpit 18. This showed slight erosion to the drain’s gravel surface. Copies were passed to both Carillion and Network Rail.
Network Rail’s Ellipse system holds drainage information and is used for inspections and maintenance, but when the work at Carmont ended no entry was made into Ellipse. Consequently, no inspection regime was established for the upper section of drainage and RAIB found no evidence of any inspections between March 2013 and August 2020. 12 AUGUST 2020
At 09:00 there was flooding and a landslip at Ironies Bridge, flooding at Newtonhill (north of Carmont) and another landslip near Laurencekirk Station to the south, but no instruction was given to the driver or signaller for either reduced speed running or for the line to be examined. RAIB found that the controllers had not been given sufficient guidance or training. It questions whether Network Rail “appreciated the risk from very heavy rainfall to earthworks and associated drainage” and whether its management realised that risk mitigation measures had not been effectively implemented in Route Control.
The report states that “despite awareness of risk Network Rail has not completed implementation of additional control measures following previous events involving extreme weather; they still have to complete actions to enhance the capability of operating staff to manage complex incidents.”
RAIB’s “causal factors” are summarised as: (i) the gravel in the drainage trench was vulnerable to washout if large flows of surface water concentrated into a short length of drain; and (ii) Carillion did not construct the drain in accordance with the designer’s requirements.
RAIB’S RECOMMENDATIONS
As a consequence of this accident, RAIB has made 20 recommendations for the improvement of railway safety to the ORR, requiring them to consider each one and where appropriate take action and report back to the RAIB.
The areas covered include: (i) better management of civil engineering construction activities by Network Rail and its contractors; (ii) additional standards and guidance on the safe design of drainage systems; (iii) improved operational response to extreme rainfall events; (iv) enhancing the capability of route control offices to effectively manage complex events; and (v) measures to prevent derailed trains from deviating too far from the track.
The full report and all 20 recommendations can be found at: https:// www.gov.uk/government/news/report-022022-derailment-of-apassenger-train-at-carmont.
STEADY AS WE GO
RSSB'S THIRD QUARTER SAFETY PERFORMANCE UPDATE DEMONSTRATES AN EVEN TREND, BUT THE NEED FOR VIGILANCE REMAINS.
To make sure everyone gets home safe every day, you need to have eyes everywhere. For this, you need data, but you also need to be able to look down to the weaker signals evident in the daily control log, and you need to be able to check that what you’re doing is making a difference.
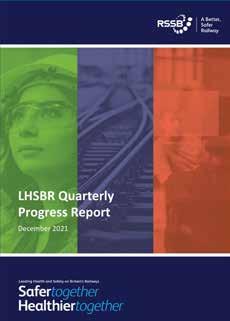
This is exactly why RSSB produced the Leading Health and Safety on Britain’s Railway strategy and why it publishes a quarterly update to make sure members have a clear picture of what’s going on out there. The latest of these reports covers the third quarter of the 2021/22 fiscal year, essentially mid-September to mid-December.
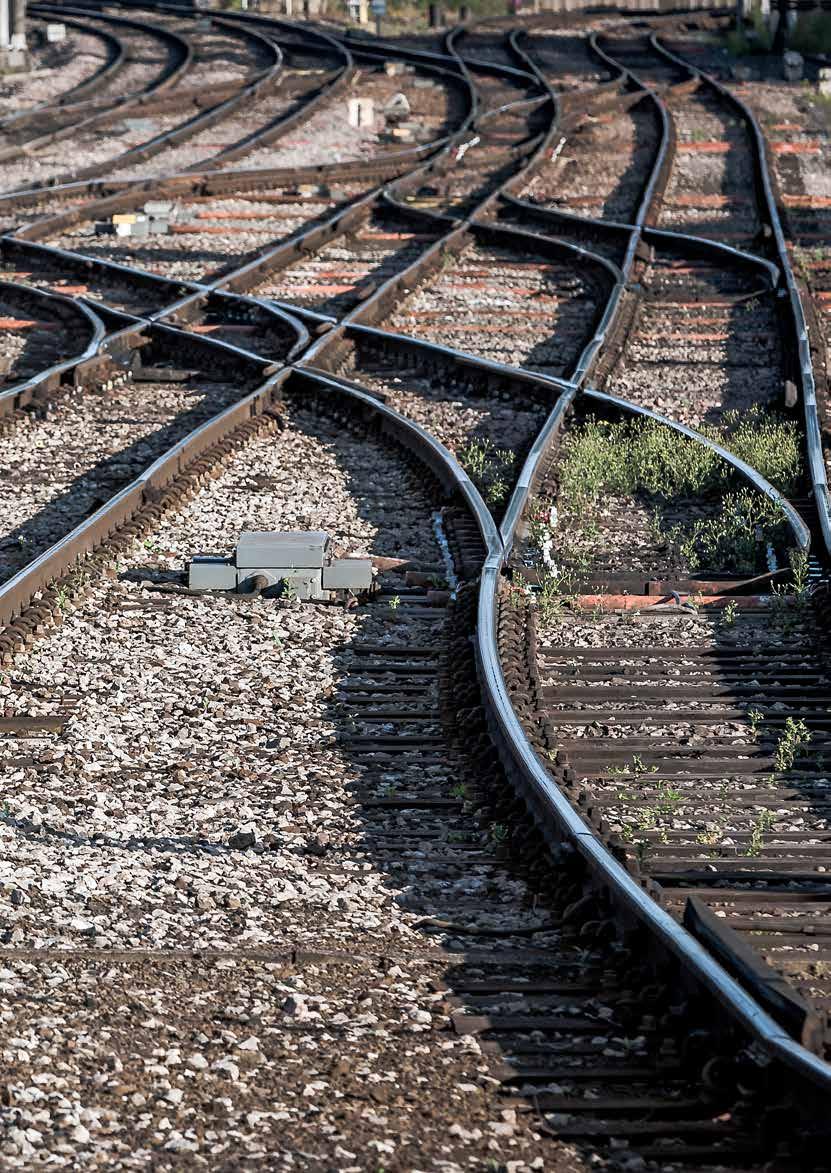
THE BIG HEADLINES
First, there are still train accidents – potentially higher-risk ones, we call them. Four occurred in Quarter 3 (Q3): a buffer stop collision; a collision with a road vehicle at a level crossing; a collision between two trains; and one derailment. One of the precursors to a train accident is a signal passed at danger event, a SPAD. There were 62 in Q3, two more than the previous quarter. The associated risk has gone up too – but this doesn’t mean that the railway is suddenly a dangerous place, as the risk figure will have changed to reflect the SPAD that led to the collision at Salisbury Tunnel Junction on 31 October 2021. As RAIB has revealed, the cause of the SPAD in the first place was wheelslide. RAIB will release its findings in due course, and RSSB – and the Train Accident Risk Group – will take the lessons forward in future thinking and future projects aimed at mitigating against the causes.
The number of recorded trespass incidents in Q3 was just under 2,700, which is down on the number reported in the same quarter last year (2,864). This follows a spike seen at the start of 2021/22 as we were phasing out of the second lockdown and while children were on their Easter holidays. Child-related trespass has continued to rise in line with all trespassrelated events. Cases of children (and older) sitting over the edges of platforms are still being recorded, as are ill-advised games of ‘chicken’ involving running across the track between platforms.
The industry supported the important messages to prevent trespass and shared the new ‘You vs Train’ campaign via social media. A new campaign is also being planned to mitigate the increase in trespass over the holiday peaks. New resources to educate children from ages 3-16, to promote safe crossing use, have also been made available to schools via www. switchedonrailsafety.co.uk.
We are pleased to report that there were no workforce fatalities in Q3, pleased too that near misses have continued to fall. This reflects the efforts of Network Rail’s Safety Task Force (STF) to cut unassisted lookout working and use more line blockages, although a steady increase in line blockage incidents is now starting to be seen.
HEALTH AND WELLBEING
Where safety data has always been comparatively plentiful, the same has not been the case for health and wellbeing. Thankfully, that looks set to change, with the launch of a new Health and Wellbeing Index (HWI). To streamline the data collection process, HWI components have also been integrated into the Industry Health & Wellbeing Performance Measurement System, an ongoing project to develop an industry-wide health and wellbeing monitoring dashboard.
The cross-industry Rail Mental Health Survey report was published on 2 November, with some insightful outcomes. The results showed that over 40% of rail workers are experiencing mental health problems. Rates of anxiety and PTSD were found to be higher among rail workers than the general population. In addition to the main report, companies with high numbers of responses have each received a highlights report for their company. LOOKING FORWARD
The Q3 report reflects a period of improvement, but it is a continuing journey. Here are just three things to look out for in the coming months: • Improving our Safety Management
Intelligence System (SMIS). RSSB is currently working with industry to simplify
SMIS to make it quicker and easier to record events and enable automatic data transfer with company systems. • Rebuilding the Safety Risk Model (SRM).
The SRM provides estimates of the risk from rail operations and maintenance. It is currently being rebuilt to create a simpler more flexible structure which better meets requirements for localised risk assessment. • Developing the regional Precursor
Indicator Model (PIM). The PIM provides a risk-weighted measure of failures, acts, and conditions that have potential to cause a train accident in different circumstances. Following engagement with 30 industry stakeholders, work is under way to update the calculations, produce regional breakdowns and build a dashboard to present the results.
Read the full report at https://www.rssb. co.uk/safety-and-health/leading-healthand-safety-on-britains-railway/lhsbrquarterly-progress-report.