
18 minute read
Chiltern ATP obsolescence
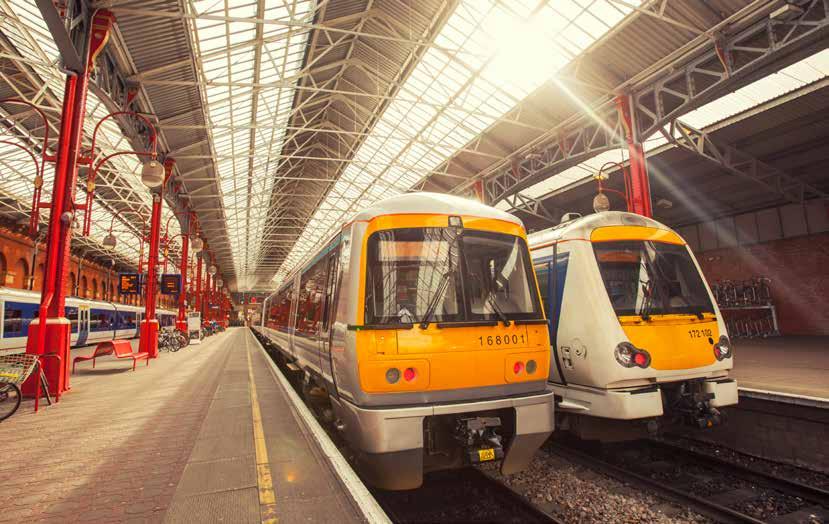
obsolescenceChiltern ATP
PAUL DARLINGTON
In a signalling system with lineside signals and fitted with an Automatic Train Protection (ATP) system, a brake application will automatically be applied if a train is going too fast, thereby protecting the train from passing signals at danger. This is achieved by transmitting infrastructure data, including the maximum speed limit, to trains by a communication system.
ATP consists of equipment located trackside and on-board trains, with the communication normally delivered by using inductive ‘loops’, beacons or a radio link.
Following the investigation into the 1988 Clapham Junction Railway Accident, recommendation 46 of the report required that, after a specific type of ATP system had been selected, British Rail (BR) had to fully implement ATP nationally within five years. This would have been a huge task, but BR instigated two ATP pilot systems – one on the Great Western route and one on the Chiltern route – to help identify an ATP system that should be installed nationally.
The Chiltern route was selected for an ATP system based on the LZB system used in Germany. This was developed by Standard Elektrik Lorenz (SEL) and was called SELCAB. SELCAB used inductive
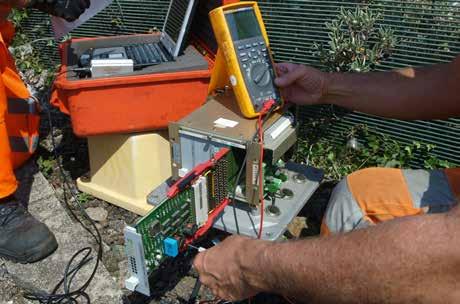
loops to communicate between the track and train on the approach to signals, using loops sometimes several hundred metres long and terminating at the foot of the signal.
SELCAB had some adaptions to fit the BR market, which made it a bespoke system and one not used elsewhere. On the Chiltern route, it was fitted between Marylebone and Aylesbury (excluding the Transport for London (TfL) section from Harrow on the Hill to Amersham) and from Marylebone to Anyho Junction on the route via High Wycombe. All the original Class 165 multiple units were fitted with the ATP system, but not locomotivehauled trains.
ATP systems may be continuous or intermittent, with the Chiltern system being an intermittent one. Continuous ATP systems provide constant communication with the train throughout its journey, but, in an intermittent ATP system, the data is transmitted to the train only at specific transmission points along the track. These are normally at signals and high-risk locations between signals.
Intermittent ATP systems are mainly ‘an add-on’ to lineside signals, with their main purpose being to prevent trains from overrunning stop signals. However, the SELCAB system could also supervise train speed for Permanent Speed Restrictions (PSRs) and pre-programmed Temporary Speed Restrictions (TSRs), but not Emergency Speed Restrictions (ESRs) - unlike the trial ATP system provided on Great Western route, which was based on the Belgian TBL (Transmission BaliseLocomotive) ATP system.
TPWS not ATP
In 1994, Railtrack, the newly-privatised rail infrastructure company, took over the installation of the Chiltern ATP infrastructure system and put the deployment through its new safety review panel process. This provided independent safety assurance and moved it from a pilot system into full use.
At the same time, a study was also carried out into the cost-benefit of providing ATP across the whole national network. This concluded that the ‘cost per fatality prevented’ of £14 million could not be justified and so it was decided that ATP deployment would not proceed beyond the two trial systems.
A project was then launched jointly by Railtrack and the British Railways Board (which, at the time, was the exclusive train operator) to pursue a Signal Passed At Danger (SPAD) Reduction And Mitigation (SPADRAM) project. The main outcome of SPADRAM was the Train Protection and Warning System (TPWS).
An enhancement of the Automatic Warning System (AWS), TPWS was, and is, a simple system that reduced ATPpreventable risk by around 70 per cent but at a fraction of the cost. AWS uses an electromagnetic arrangement to provide drivers with an indication to show if they are approaching a red signal or not. If a driver reacts to the first warning given by AWS, they will normally have time to stop at a red signal. The risk is that the warning is not enforced and can be over-ridden by the driver. In more complex situations, such as running on cautionary signals, it relies on a driver’s vigilance to initiate the brake application.
TPWS added radio frequency (RF) loops, to provide an automatic train stop, and an overspeed sensor on the approach

to the signal. TPWS does not entirely prevent SPADs from occurring, but, in the majority of cases, it reduces or avoids the consequences of drivers failing to react to signals. TPWS was mandated by the Railway Safety Regulations 1999 (RSR1999), which came into in force from January 2000.
RSR1999, and therefore the law, requires infrastructure managers and train operators to permit only trains with train protection equipment fitted to operate. Train protection equipment is defined as a
EXPERIENCED PROVIDER FOR
KEY CLAMP GRP HANDRAIL

GET YOUR EZI QUOTE WITHIN 1 HOUR

GRP STEPS & WALKWAYS
Call or email today for a quote from your drawings or product requirements.
T 0117 970 2420 E sales@eziklampsystems.com
GRP FENCING
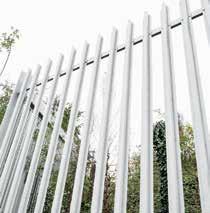

ARMCO CRASH BARRIER
system which can stop a train if it passes a red signal, if it approaches a red signal at too high a speed, or if it is driven too fast.
These new regulations also said that, where it was reasonably practicable to fit ATP, then it had to be used. This meant that both the Chiltern and Great Western ATP systems were to remain in service alongside TPWS.
The timescales for TPWS fitment were challenging and required it to be fitted on all trains and at all ‘selected signals’ (such as converging junctions and complex track layouts) by 1 January 2004. Today, Railtrack is criticised by some for its project management performance, but complete fitment of TPWS to all trains, and over 12,000 signals, 650 buffer stops, and around 1,000 permanent speed restrictions, was completed by December 2003.
TPWS has been a huge success and SPADs are no longer the risk they once were. The RSSB annual safety report for 2019/20 highlighted that the 10-year rolling average for fatalities caused by train accidents had fallen significantly since 1994, partly due to the reduction in signal over-run risk.
Once fitted, however, the benefits derived from TPWS undermined the economic case for providing full ATP, but TPWS trackside equipment is only fitted to signals beyond which conflicts, or other serious situations, are likely to arise. This meant there are many hundreds of signals, such as most automatic signals, with no TPWS protection.
In contrast, ATP is fitted to every lineside signal and permanent speed restriction, and provides continuous speed supervision, unlike TPWS which has limited capabilities to protect over-speeding. With ATP, the braking calculation is carried out on-board, and is therefore relevant to the characteristics of a particular train. The design of trackside TPWS is based on a general model of train braking ability, which may not be effective for all trains that operate on a particular route.
The Chiltern ATP equipment was supported by Alcatel and then Thales, but, with the system a bespoke ‘one off’ and no other systems ever deployed, keeping a complex technical system such as this one operational for longer than ten years was a major achievement. So, it was no surprise that, in 2011, 21 years after its instigation, Thales formally advised of the Chiltern ATP system impending obsolescence.
Just consider how many people have a computer or mobile phone still in use from 1990? ‘Last buys’ of equipment were initiated to create a stock of spares that would sustain the fixed infrastructure and fleet fitment. ATP equipment had originally been procured for the TfL Metropolitan Line, but was never fitted, as the line used mechanical train stops. This unused ATP equipment has helped to keep the infrastructure part operational over the years, otherwise things would be even worse than they are.
A life extension programme for the on-track part of the system had been instigated some years ago. This consolidated documentation and training materials, with Park Signalling using its creative retro-engineering skills and modern technology to produce a replacement solution for programming and verifying the EPROMs that hold the TSR and ESR data. This was called the LEU Sequencer and replaced the ancient XS2045A machine originally supplied by GEC General Signal.
Park Signalling has prepared the TSR and ESR configuration data for Chiltern ATP since 2018.
The obsolescence problems were even worse for the on-board equipment, with no modern equivalent available and with the spares stock for the trains depleted to critical levels. Continued operation of the current level of ATP protection was becoming unsustainable and something needed to be done to replace the obsolete ATP system.
Options for obsolescence
Providing a European Train Control System (ETCS) would seem the obvious solution, as ETCS Level (L) 2 delivers ATP and is also the long-term signalling solution for the country. However, the rest of the signalling assets on the Chiltern route are not life expired and there are other routes in the country with a greater need for the resource and capital required for ETCS. The planned deployment date for ETCS on the Chiltern route is around 2035, during Control Period 9.
Table 1. Comparison of system functions. Function ATP ETCS L2
Supervision.
Transmission failure monitored. (Beacon or radio or inductive loop)
Display to driver. Continuous supervision of driver using distance to go calculations.
Yes Changes to partial supervision mode with immediate brake application.
Yes Cab display and audible Warnings. Continuous supervision of driver using distance to go calculations.
Yes Balise - failures reported on radio.
Yes Cab display and audible Warnings.
Monitors changes in permanent speed restrictions (PSR).
Monitors adherence to max line- speed.
Monitors diverging speed at junctions.
Yes Changes displayed to driver, based on braking performance.
Yes
Yes
Yes Changes displayed to driver, based on braking performance.
Yes
Yes
Monitors temporary speed restrictions (TSR). Yes Yes
Stop train if it passes signal at danger.
Prevent train approaching signal faster than braking performance permits.
Monitor position light moves (call-on).
Yes Within overlap.
Yes Within overlap.
Yes Using distance to go calculations based on train braking performance.
Yes
Yes Using distance to go calculations based on train braking performance.
Yes Standard TPWS Intermittent supervision and contact with lineside infrastructure.
Yes Failure indicated for most TPWS failures, signal on approach is held at red.
Yes Only brake demand and TPWS isolation/failure. Some PSRs Speed checked on approach to the PSR and only Regulated PSRs. Enhanced TPWS Intermittent supervision and contact with lineside infrastructure.
Yes Failure indicated for most TPWS failures, signal on approach is held at red.
Yes Only brake demand and TPWS isolation/failure. Some PSRs Speed checked on approach to the PSR and only Regulated PSRs.
No No
Partial Regulated PSRs when no restricting junction signal controls are provided.
Partial On regulated TSRs if in place more than 12 months or, less than 12 months on >100mph lines with >200 trains per day.
Some signals Only signals providing protection at junctions.
Some signals If TPWS OSS fitted.
No Partial Regulated PSRs when no restricting junction signal controls are provided.
Partial On regulated TSRs if in place more than 12 months or, less than 12 months on >100mph lines with >200 trains per day.
Yes All main signals fitted with TPWS TSS.
Yes TPWS OSS as fitted. Designed to stop as many trains as practical before conflicts.
No
ETCS is also best provided when new trains, fitted with ETCS on-board equipment as standard, are provided on a route, but the dates for new rolling stock on the Chiltern route also didn’t match the immediate need to manage the ATP obsolescence. Providing ETCS was therefore not seen as deliverable within the required timescales for the ATP obsolescence, or at an affordable capital cost.
A number of options were considered in detail. The chosen option would need to be affordable and offer value for money. The technology and the skills to support the solution would have to be readily available, and, with the eventual end state of the whole UK railway being ETCS fitted, the selected option would have to fit this objective. The selected solution that met these requirements was Enhanced TPWS. A summary of the functions of ATP, ETCS L2, TPWS and Enhanced TPWS is shown in Table 1 (left).
Enhanced TPWS
TPWS is an expandable system, so additional loops can be provided at automatic signals; buffer stops or speed restrictions. Therefore, it was anticipated that TPWS enhancements could make
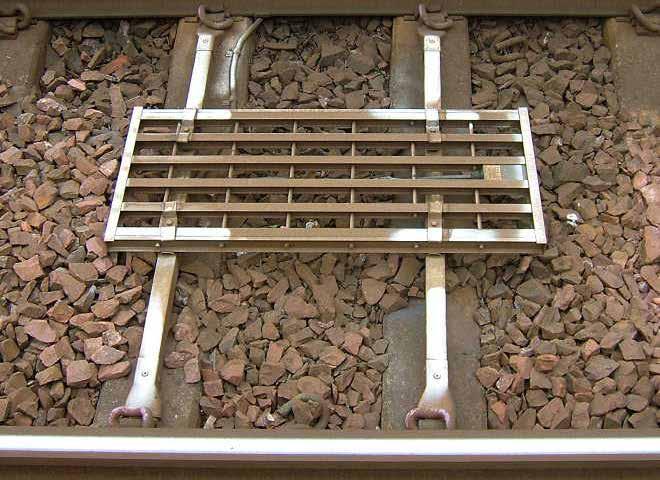
TPWS closely match the functionality provided by the obsolete SELCAB ATP. Enhanced TPWS would provide Train Stop System (TSS) loops at signals not fitted with TPWS and Overspeed Sensor System (OSS) loops designed to stop a train short of a conflict. Enhanced TPWS would also provide optimum protection for ALL trains operating over the Chiltern route, as currently not all trains using the Chiltern route use ATP.
All existing Chiltern TPWS installations would be reviewed as part of enhanced TPWS to check that the designs implemented for the original TPWS project incorporate best practice that had been developed over the years.
On-train TPWS equipment would be upgraded to the most recent design standard, known as Mark 4 TPWS, which benefits from design changes to improve its effectiveness. Compared to earlier TPWS control panels, Mark 4 features three separate indicators to show the cause of a brake demand – SPAD, Overspeed or AWS. It also adds a covered ‘Brake Release’ button, to involve the driver in the brake release process.
SLEEPER SPACING INDEPENDENT LEVEL CROSSING
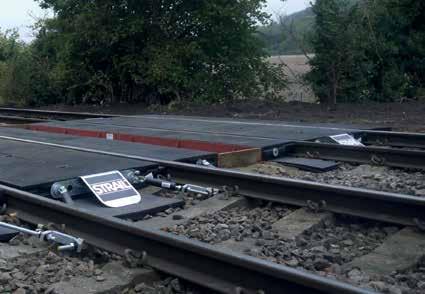
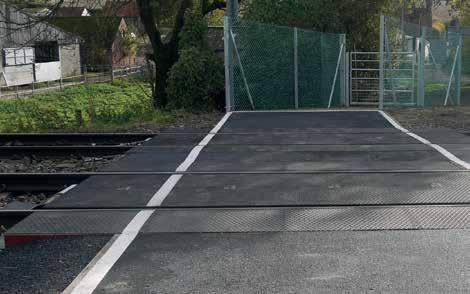
tapSTRAIL - the versatile solution for light duty crossings and RRAPs
Fast, easy installation and removal Easily adapted to fit different flat bottom rail sleeper types with Timber or Rubber packing „One Size Fits All“ Inner panels can be cut in half – easy manual handling Gap free, anti-vandal, lock tight tie rod system
Providing enhanced TPWS instead of ATP would, however, require an exemption from RSR1999 and a demonstration that a TPWS-based system would represent the only reasonably practicable solution. It was important that all stakeholders were made aware of the reasons and benefits of the enhanced TPWS solution, as RSR1999 says that railway regulator the Office of Rail and Road (ORR) may grant an exemption to the law, but is required to conduct a public consultation to assist the decision.
The Chiltern ATP Steering Group was formed, to work across industry boundaries and get the solution going. ATP is a system involving both trains and fixed infrastructure and therefore must be managed as a system, so no one organisation could progress a solution without the help of the other.
The cooperation and collaboration between Chiltern Railways and Network Rail through the early formation of a steering group was instrumental in getting the project instigated for the benefit of both parties. Forming the group with a single purpose and common goals was key.
The steering group quickly decided that the minimum acceptable solution would be for a net neutral impact on safety risk across the route, which would need to be demonstrated to all stakeholders and inform the exemption and public consultation.
Any solution would need to allow the current train fleets – Class 165/0 Networker Turbo, Class 168/0/1/2 Clubman, and Class 172/1 Turbostar trains – to use the Chiltern route without SELCAB ATP.
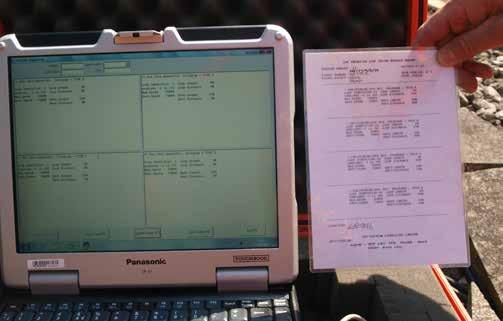
PHOTO: STEVE FULCHER
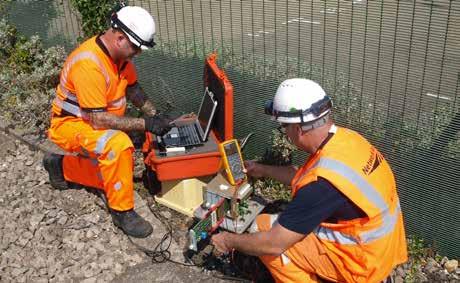
Gary Faulkner and John Bartoszek maintaining the SELCAB ATP.
Independent risk assessment
To provide expert independent guidance, Network Rail commissioned Mott MacDonald to complete a study into the potential solutions for an interim train protection system and Sotera Risk Solutions to provide a comprehensive, independent risk assessment to analyse a wide range of potential future risk control strategies for the route.
The Sotera assessment took into account East West Rail Phase 2, HS2 construction traffic and future passenger growth. The assessment concluded that enhancing TPWS by providing additional lineside fitment between Marylebone and Aynho Junction, together with upgrading the Chiltern cabs to Mk4 TPWS units, would provide a broadly similar, and even marginally lower, level of risk than the existing ATP fitment. It was calculated that the Fatalities and Weighted Injuries (FWI) index would be 1.9 per cent better with all trains on the route using enhanced TPWS, a figure that would be likely to increase further as the network gets busier, compared with maintaining the current ATP fleet.
The risk assessment looked at two strategies to deal with the unrepairable failure of ATP units on Chiltern Railways’ fleet until enhanced TPWS could be implemented. Option A would permit the trains to operate using existing TPWS and AWS. Option B would withdraw the train units from service until the enhanced TPWS upgrades could be implemented (by the end of 2023).
It was considered that, with a worst case of ATP systems failing irreparably on 20 per cent of units per year, the safety risk from Option B would exceed the risk from Option A, taking into account the potential for intermodal transfer to car or bus if trains were withdrawn from service. This strongly indicated the safer option would be Option A, and for trains to continue to operate using TPWS and AWS if their ATP systems could not be repaired.
The Office of Rail and Road (ORR) initially requested two RSR1999 exemption applications. Through close liaison between the steering group and the ORR, it was later agreed these could be made as a combined submission.
A short term (2020 to 2023) application would be led by Chiltern Railways and cover the period where ATP would remain operational on most trains, but be removed from trains that could not be repaired. The selected option (enhanced TPWS) would be implemented during this time.
The long-term application post 2023 would be led by Network Rail and cover the operation of the enhanced TPWS instead of ATP and allow ATP to be removed.
This combined exemption has been granted but is time limited to the end of 2026, to allow a review of the situation until ETCS is provided on the route.
Peter Dray, director at Sotera Risk Solutions, was pleased with the outcome. “The obsolescence of the Chiltern ATP system presented the industry with a complex challenge… a challenge that extended well beyond the immediate
issue of managing a life-expired and unsupported train protection system,” he said. “The proposed way forward needed to account for planned network changes, optimising safety performance, cost, operational performance and deliverability within a tight timeframe.
“It is a credit to the industry that, from a wide range of options identified, a practical and effective solution was arrived at that could be agreed and supported by all the stakeholders and decision makers. The team at Sotera were pleased to be able to support the process through risk modelling of all the options, assisting with option selection and performing cost-benefit analysis.”
Public consultation
The public consultation for “Exemption from train protection duties: Chiltern Railway routes” ran from 17 June to 15 July 2020 and invited any party to express a view on the application, with the ORR committed to consider all views in making its decision. The consultation included all the detailed proposals, risk assessments, options and safety arguments.
This process attracted constructive feedback from industry stakeholders. All of the comments were addressed to the satisfaction of the ORR and an exemption certificate was granted that came into force on 13 August 2020.
The rail industry’s success in identifying an acceptable solution, securing exemptions from RSR 1999 and gaining support from the public consultation is a credit to all involved, is attributed to using recognised industry risk models and specialists who understood how to put together a numerate assessment of risk for the all the options identified. This provided a solid basis for making decisions and justifying the plan for the project, one which was easily understood by all the stakeholders.
Active involvement with stakeholders before the exemption application

submission, together with incorporating feedback into those submissions, minimised the risk of objections to the formal application. The steering group ensured stakeholders, and the regulators who would make the ultimate exemption decision, were ‘taken along the journey’ as the option selection and plan were developed. This meant there were no surprises when the exemption application was submitted.
With the exemption now in place, mobilisation and design work for both trains and infrastructure is underway, with infrastructure and train upgrades to be implemented from early 2021 through to mid 2023. This will allow ATP to be turned off sometime in 2023.
Managing Risk – Optimising Performance
Sotera is a leading, independent safety and risk management consultancy. Founded in 2002 to serve the rail industry, we set out our vision ‘to provide the best, most responsive and cost-effective services’ - a vision that is central to everything we do today.
Sotera works across the industry with operators, equipment suppliers, research organisations and regulators. The dedicated team helps provide solutions to the challenges that face our industry.
> Risk assessment and modelling > Safety performance analysis and indicators > Safety decision making and cost benefit analysis > Research.

How can we help? Contact the Sotera team to see how we can support you.
Telephone: +44 (0)208 2890384
Email: peter.dray@sotera.co.uk