
7 minute read
Storied Success in Tunnelling
From the UK to Oman and Chile to Azerbaijan, Mobil Baustoffe experts have been involved in a big array of construction sites
Mobil Baustoffe, a subsidiary of STRABAG SE, a Europeanbased technology partner for construction services, specialises in the reliable and cost-effective production of concrete for large scale construction projects such as tunnels, dams and similar major projects around the world. The project related production of aggregates made from tunnel excavation material, the production of tunnel segments for TBM driven tunnels and the production of annular gap filling materials, as well as consulting are all part of Mobil Baustoffe’s services.
The company started in 1998 with its first concrete deliveries for a tunnelling project in Germany. Since then, many projects – from tunnels to airports – were added to the reference list. Well known tunnels like the Gotthard base tunnel in Switzerland or the Brenner Base tunnel in Italy have been built using Mobil Baustoffe’s concrete. In 2008, Mobil Baustoffe was purchased by STRABAG and can since rely on the strong network of its parent company.
Success story: Crossrail
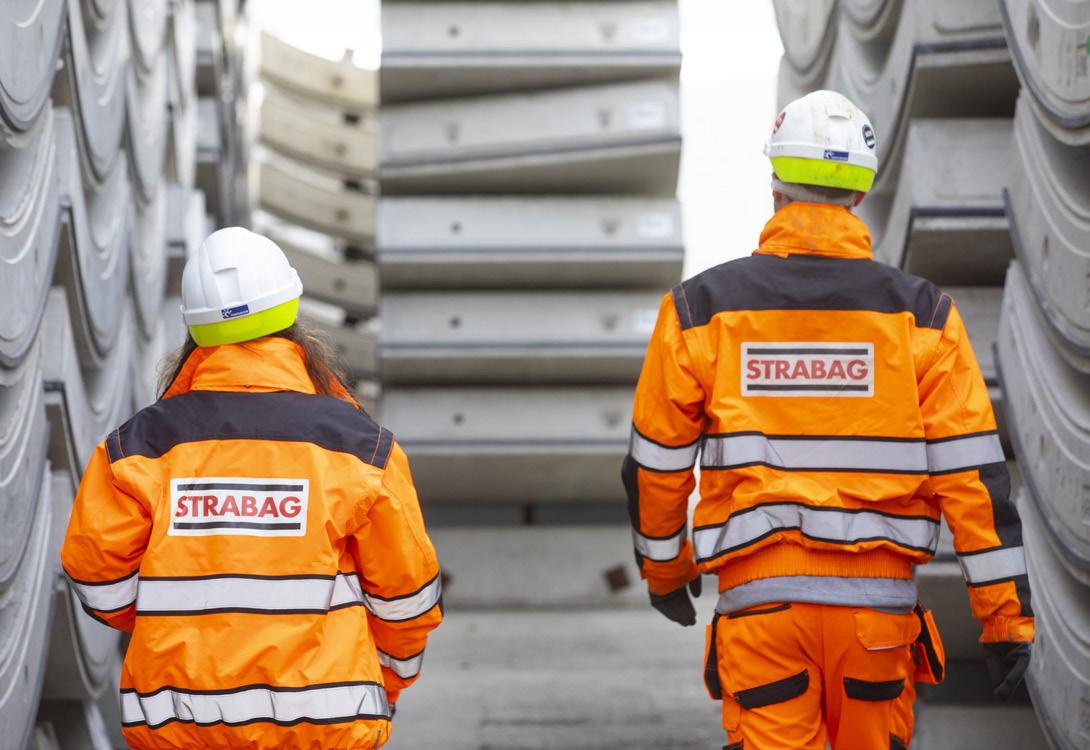
In the UK, Mobil Baustoffe was involved in the Crossrail projects C300 and C410 in London for the BFK JV. For the C300 lot, the team produced the backfill grout component A using a bespoke setup directly at the tunnel entrance. The containerised grout plants were designed to ensure continuous production of grout even in the unlikely event of one plant breaking down. Using seven interconnected powder silos meant not only achieving the storage capacity required, but also to use the constituents in both plants if necessary. The unloading of grout into the client’s vehicles was performed in close cooperation with the site directly at the start of the tunnel.
For the C410 lot, Mobil Baustoffe developed a tailor-made concrete mixing plant for the production of concrete right in the centre of London. The concrete batching plant with a 3.33m³ twin-shaft mixer was designed to have the smallest footprint possible to fit in the space given. Using an overhead silo for aggregates and a large, screwed cement silo, the team was able to achieve the storage capacity of constituents needed for 300 m³ of concrete as specified by the client. The delivery of the constituents was performed smoothly right into the heart of London via Oxford Street.
Using the plant in a 24/7 shift system, they were able to supply concrete directly into the client’s concrete pump (placed under the batching plant) at any given time. Under challenging conditions, Mobil Baustoffe fully satisfied the needs of its customer.

Success story: Finnetunnel
Mobil Baustoffe successfully produced 48,000 tunnel lining segments with extremely low tolerances for the construction of Finnetunnel for Deutsche Bahn. In doing so, it exceeded the planned performance by up to 40 per cent. This allowed the client to complete tunnelling work for the two tunnel sections within the given timeframe. The production took place in a factory built directly in front of the tunnel in a brand new and bespoke shed housing the carousel system, the curing chamber and a storage area. Mobil Baustoffe also developed special concrete mix designs with its concrete technologists.
With the support of an external concrete expert, the need for the segments coating, which is normally required by the German standard for the given ground water condition, could be eliminated. This also helped to reduce costs. According to the client, the production of the tunnel lining segments for Finnetunnel showed a quality never seen before in a comparable timeframe. For this project, Mobil Baustoffe produced the segments, the concrete and the backfill material – a real ‘one stop shop’ approach for everything concrete related.
Success story: Cityringen Copenhagen, Denmark
For the Cityringen Project in Copenhagen, Mobil Baustoffe successfully produced over 125,000 high precision segments for about 30 kilometres of tunnel. To do so, the team installed a production yard within the confines of Sassnitz Ferry Port on Rügen island (Germany). Production of reinforcement cages and segments was done in two separate sheds.
The planned output was exceeded by up to 35 per cent. The client shipped the finished segments via vessel to a storage yard in Copenhagen and eventually by truck to the respective sites along the tunnel line.

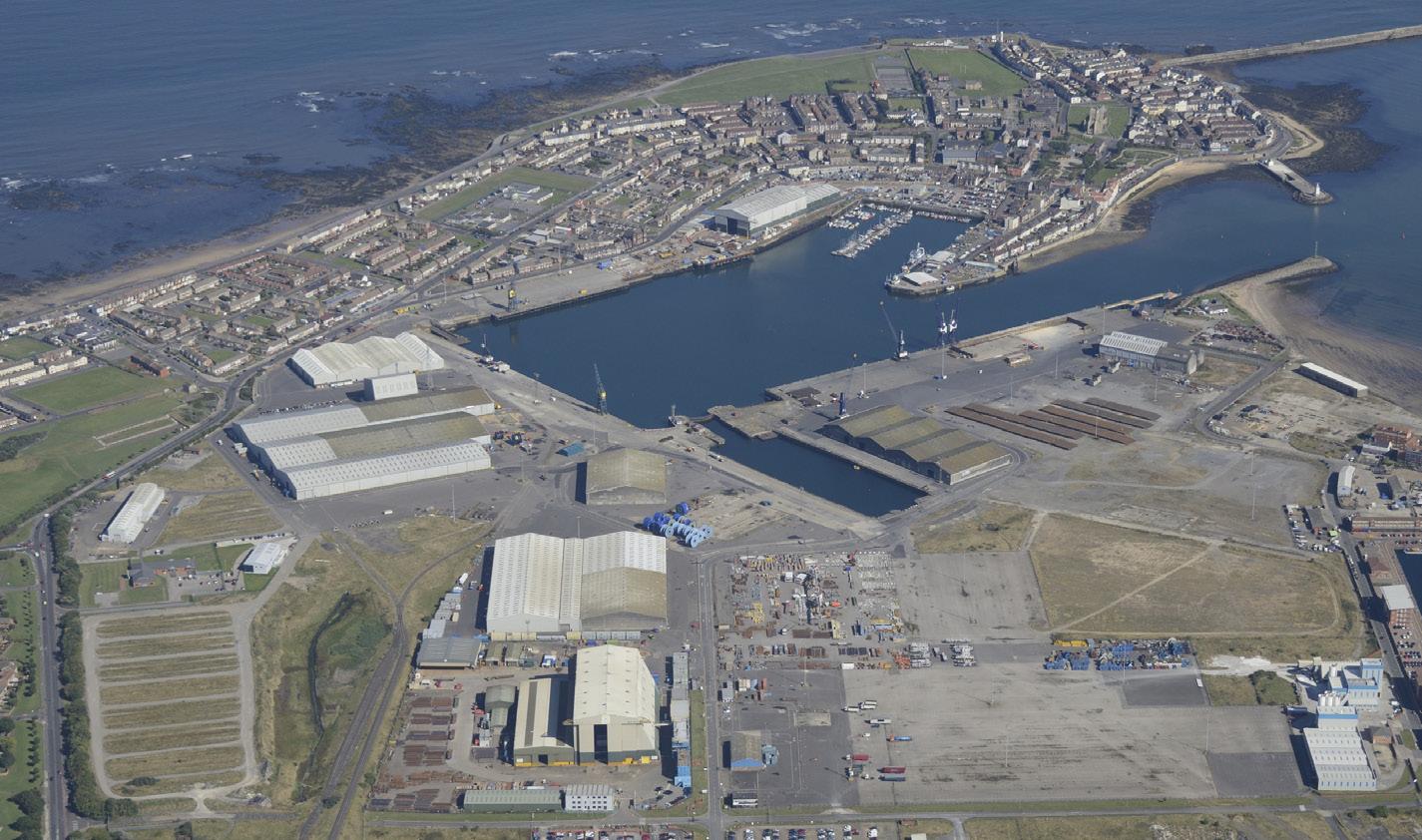
Success story: North Yorkshire Polyhalite Project, UK
On this site, Mobil Baustoffe experts produced the concrete for STRABAG’s segment precast factory. During a short period of very high demand for prefabricated segments, Mobil Baustoffe supported the site with a rapidly setup segment production in its existing facility in Sassnitz, Germany. The segments were then shipped to the UK and placed in the tunnel. Only teamwork and outstanding cooperation could lead to these fantastic results.

Tunnel construction works along HS2 (UK)
STRABAG using the expertise of Mobil Baustoffe has been awarded the contract to produce approximately 84,000 precast concrete segments for the tunnel construction works along HS2 (High Speed Two). The segments will be produced in a state-of-the-art factory built and operated by STRABAG UK Ltd in the port of Hartlepool in the north of England. The project, commissioned by Skanska Costain STRABAG JV (SCS JV), will be realised on a leased industrial site at Hartlepool Docks to be developed into a production factory, storage and transport facility. With delivery starting in spring 2023, the high-quality tunnel segments will be used on HS2 construction sites in London: the eastern section of the Northolt Tunnel, consisting of a 5.6 kilometre long, twin-tube tunnel between Green Park Way Ventilation Shaft and Victoria Road Ancillary Shaft and the Euston Tunnel, a 7.2-kilometre twintube tunnel between Euston and Old Oak Common Railway Stations.
The manufacture of the precast tunnel segments (Hartlepool, UK)
Considering the precast manufacturing process, the units will be manufactured by means of an automated carousel system, the carousel consisting of a main production line, a concrete cabin, a curing chamber and a pre-storage area. The moulds are prepared along the production line by the installation of the appropriate cage and any other specified fixings. They then enter the concrete cabin where they will be filled with the concrete mixed in the batching plant and transferred inside the building by the flying hopper.
Once the concrete is poured and vibrated and the surface of the unit is finished, they are checked to ensure consistency of the final cast unit. Having travelled along the main production lines, the moulds will enter the curing chamber where the high temperature of the environment will accelerate the hydration process of the concrete to allow the unit to gain sufficient strength and be demoulded and transferred to the pre-storage area. The curing area is a three-stage process where the moulds initially enter an area of higher heat, then travel slowly to two other zones of decreasing heat.
Having undergone the initial curing stages, the moulds enter the pre-storage area where they will be tilted by a tilting table, then lifted and stacked for approximately 24 hours prior to exiting the building through the table conveyor and taken to the precast unit storage area by the trolleys/forklift. Once in these storage areas, the precast units will continue the curing process for 28 days until they can be transported from site as a finished product.
Tel: +49 89 89 54 57 4 – 11
Email: office@mobil-baustoffe.com
Visit: mobil-baustoffe.com