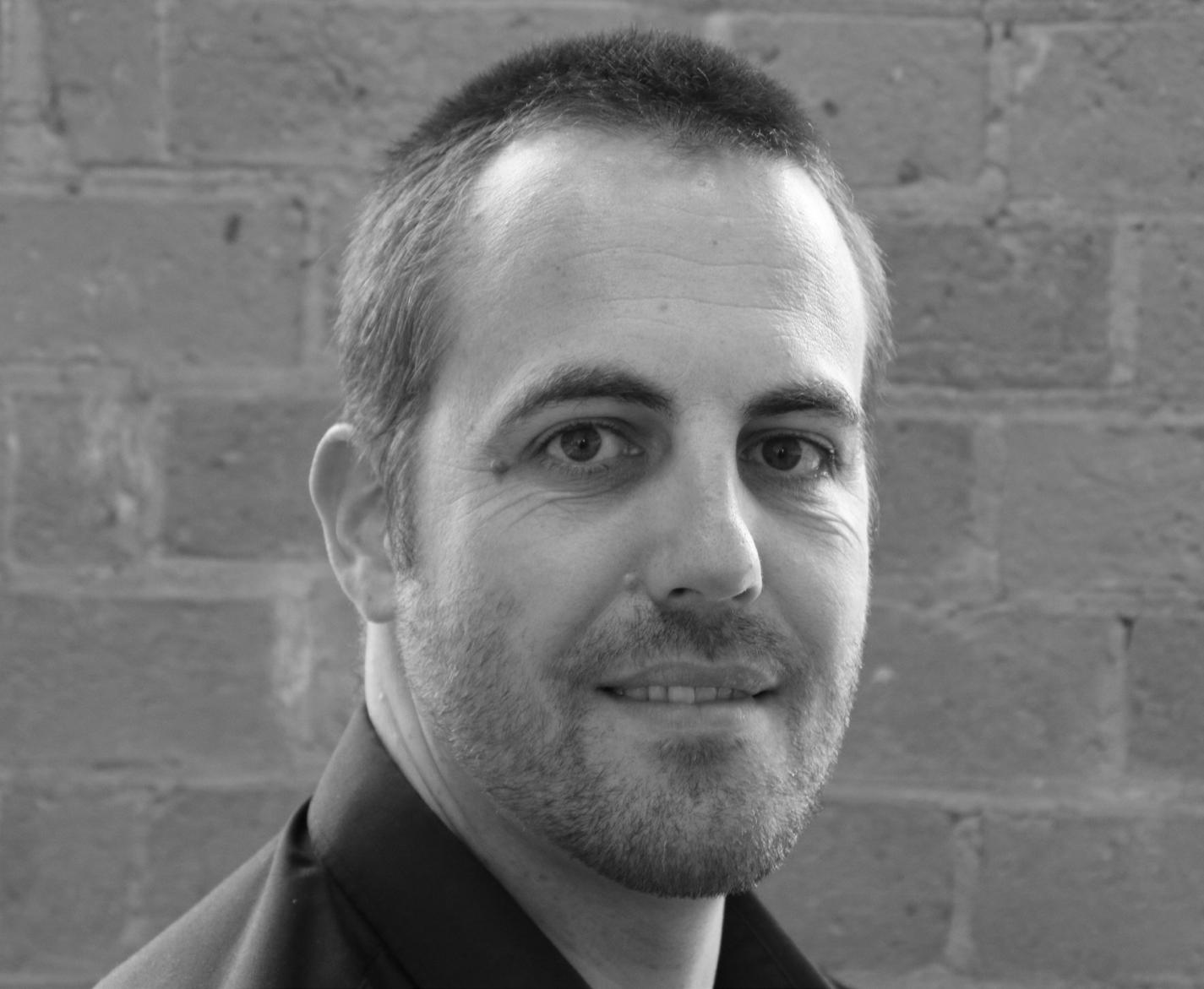
11 minute read
Rail Professional Interview
Sam Sherwood-Hale spoke to Mark Coleman, GeoAccess Ltd Managing Director about the latest inspection and remote access techniques, working holistically and the company’s place within the supply chain
You established the company in 2014 to serve a niche market identified at the time. How has that market grown since then?
We originally established the company to solve a problem for one client. By delivering that service at the highest possible level, we have found that we have a unique skillset that is attractive to a much wider market. Our portfolio of clients now spans multiple market sectors across the whole of the UK. We always strive to provide the best service, so are constantly trying new innovations. Some work, some don’t. This has kept us at the forefront and on our toes constantly which means we can react quickly and efficiently to changing demands and opportunities.
Have standard changes in recent years caused access constraints to become a bigger problem?
I don’t believe so. Safety is our top priority, and with constant innovation and the advancement of technology safer working practices are always being developed. If anything, the change in standards along with new technology has opened up more opportunities and access is actually easier.
You carry out inspection work of various types of assets from earthworks, structures, buildings and coastal defences to wind turbines, transmission towers and underwater assets – providing services that utilise UAVs, ROVs and IRATA qualified operatives. Which part of the business have you seen grow the fastest over the last five years or more?
Without doubt the advancement of new technology has led to a huge growth across all areas, it has had a huge impact. Better IT solutions to collect data from site, turn around reports and share with our clients has seen more efficient working across the board. Important safety information can be shared between site teams and the office instantly, with very sophisticated reports generated from site. The locations and safety of the teams can be monitored in real time. Battery technology and batteryoperated power tools have resulted in lower environmental impacts, which is always preferred by our clients.
But if I had to choose one area that’s seen the most growth it would be new ways of accessing assets remotely using UAVs and ROVs. By removing the need for operatives to work at height, underwater and in confined spaces has resulted in safer working practices, often with the benefit of shorter times on site generating efficiencies that can be passed back to the client. Jobs that use to be undertaken using very costly and timely techniques can now be done at a fraction of the cost and time.
What are some important safety concerns to consider when working in confined spaces?
The operative’s safety always comes first. In the planning stages we would do everything possible to try and reduce the risk, and sometimes this can be done by using a remote access technique instead of manned entry. By removing us from the equation (if possible), removes a great many risks. Planning is critical. The physical structure can pose issues; size, shape, orientation, surfaces, potential snags to name a few. Gases; noxious, flammable and poisonous plus a potential reduction
in oxygen levels. That mundane muddy puddle when disturbed can release a whole host of nasty gases into the atmosphere. Drowning, explosions, entrapment, loss of consciousness. Spiders! I hate spiders. Recently on a culvert inspection job we encountered a large number of false widow spiders staying out of the great British winter! Needles and sharps. It’s amazing what you find hidden out of sight. A rescue plan is really important.
The last thing you need in a rescue situation is another casualty so a well thought out rescue plan is essential. It can be a potentially highly dangerous environment to work in.
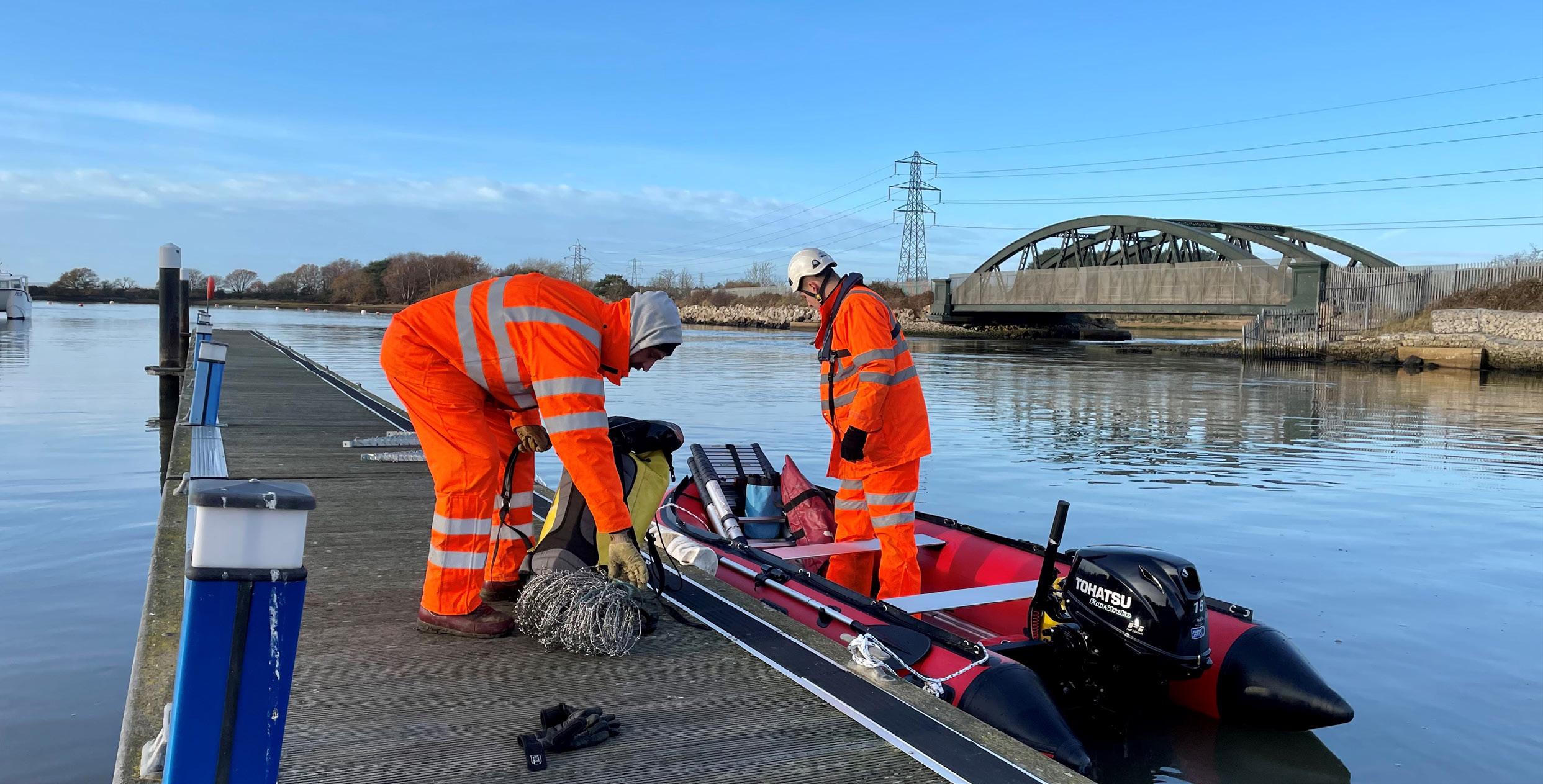
What are some Confined Space Techniques?
Confined space work can broadly be divided into three main areas. Low risk, medium risk and high risk. Low risk confined space has simple entry and exit techniques and adequate ventilation. Medium risk confined space has more restricted/difficult entry and exit techniques and minimal ventilation, while high risk confined space areas have complex entry and exit techniques, and usually an atmospheric hazard that cannot be eliminated. Techniques that can be used in confined space work can include: remote access, rope access, escape breathing apparatus, full breathing apparatus and in/ on or underwater.
What does approaching every job in a holistic fashion mean to you?
That’s a good question. For me it means looking at the bigger picture, looking outside the box. Sometimes you are asked to undertake a particular job and if you put the blinkers down and focus all your efforts on that specific task you can miss some great wider solutions and opportunities, both for your client and for you. When looking at each job in a wider context it often offers up solutions that would have been otherwise missed. Sometimes the job you initially get asked to undertake, if looked at holistically, turns into something very different.
How have Remotely Piloted Vehicles helped your work with confined spaces?
Tremendously! If you can remove humans from entering those potentially dangerous environments, you are reducing the risks massively. It’s not always possible, but with the advancement of technology, better cameras, better lighting and better battery power most visual inspections can be undertaken remotely. We use our Elios 2 UAV in a large proportion of our above water remote access confined space work. The Elios 2 is amazing. Photographs, video and thermal data can be collected, with measurements taken and even 3D models created if required. The quality of the data is amazing. Crawler and wheeled vehicles can fit into a pipe with a diameter as small as 150mm, and remotely piloted boats and submersibles offer some great solutions when water depth increases.
You utilised a UAV when carrying out a Visual Tunnel Inspection at Rotherhithe Station, how did it help on that project?
It was amazing and added so much value to the project. By combining experienced structural examiners into the flight crew it meant that we could collect the exact data that was required for the job. We managed to get to areas of the station and see bits of the structure that previously hadn’t been seen for many years and would have required large parts to be taken down to gain access. The real benefit of using a UAV in this situation was the minimal disruption caused. In and out within a short period of time when the line was closed at night, with commuters using the station the following morning without ever being aware. This always amazes me, the amount of work that goes on to keep the train services running safely without the public ever noticing. Incredible. How about training, your staff who work on earthworks inspections are all RSHI (Rock Slope Hazard Index) qualified. How do you go about getting all your staff qualified to the relevant standards for each area you work in?
RSHI training is just one of the many areas of training that is needed to undertake earthwork inspections on the rail network. We manage our training requirements by using a compliance matrix, a competency matrix and training plans for all staff. What do we need to offer the service? How competent are we at it? and what training do we need to continue and get better? We use a combination of specialised external consultancies along with our highly experienced inhouse team. Training never stops. Everyday everybody learns something new, be it on a training course, on the job, or being mentored. Training is another area that we look at holistically too. Sometimes what appears to be a very random course can offer surprising benefits when applied to our workstreams.
How has Covid impacted your ability to get all your staff trained up?
What a challenge it’s been the last few years for all of us! Throughout the lookdown periods and during the height of the pandemic all formal training was halted. However, our work never stopped so we needed to keep learning in different ways. Where would we be without Microsoft Teams! Huge amounts of our training were conducted remotely as both internally and externally we all came up with innovative ways to carry on. Online training platforms and assessments have now become integrated for many of us.
Have you changed your approach to work at all over the last two years?
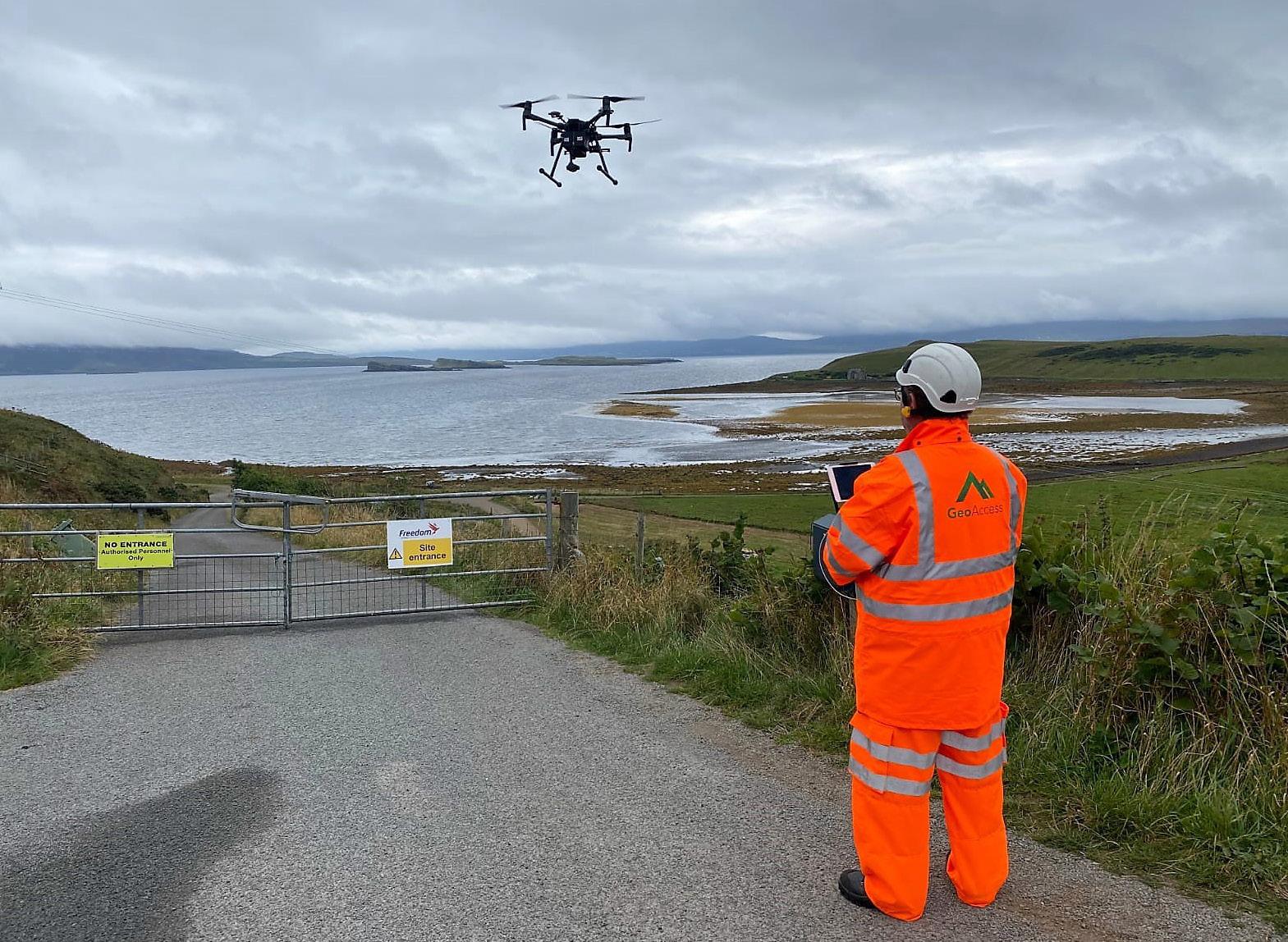
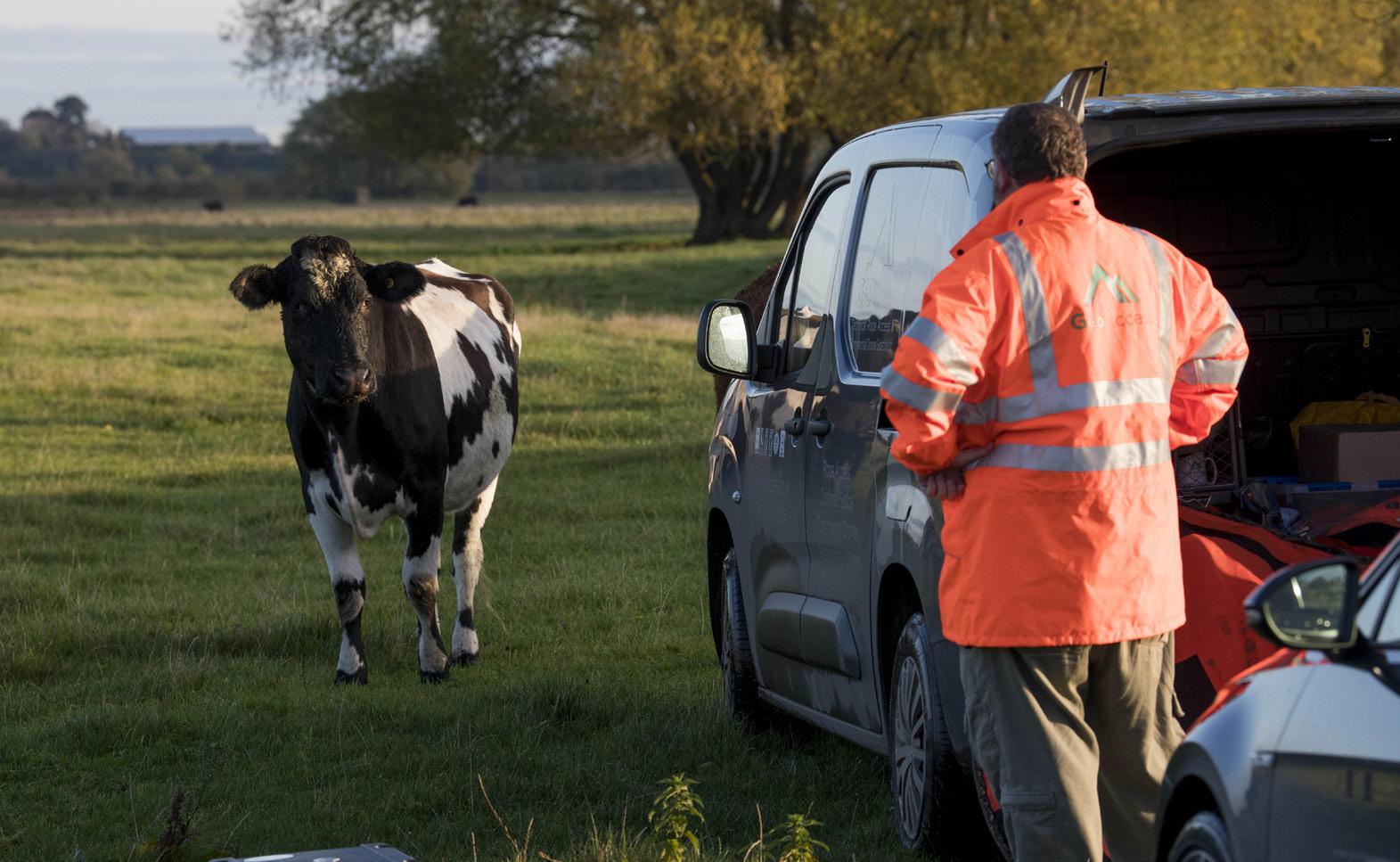
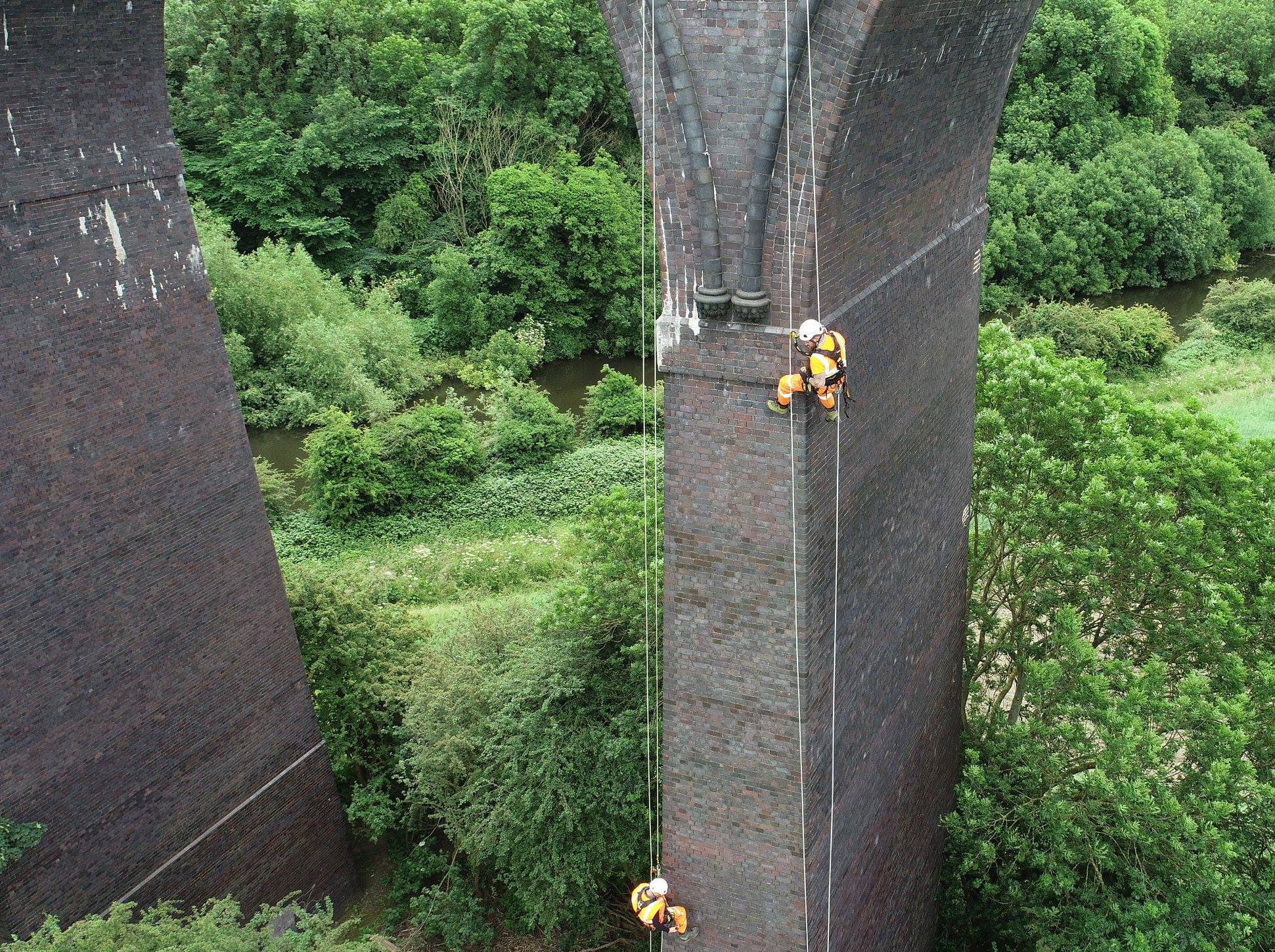
to demand. Certainly when it comes to office work, home and flexible working has really been important. For an SME like ourselves it has made us realise that we don’t need offices all over the country. A centralised base and remote working provide a great balance. Meetings. Oh my, how many of us have driven for three or four hours for a meeting that’s lasted thirty minutes! I’ve loved getting back to face to face meetings but ‘Teams’ meetings have a place and are a great way to be efficient with your time and are thankfully here to stay. One thing remote working has highlighted over the last two years is the importance of looking out for each other. By removing the need to go into an office every day, its more important than ever to keep a check of mental and physical health. Both for yourself and for your co-workers.
Over the last five years GeoAccess has successfully delivered over 20,000 inspections across all Network Rail routes. How has your relationship with Network Rail evolved during that time?
Relationships are really important to us, and our relationship with the teams at Network Rail has evolved enormously over the years. We always want to provide the best service we can to our clients, at the most efficient price and using the best available techniques. We strive to be the best. We are not afraid to try new ideas and can react quickly and efficiently. I love brain dumping our ideas in meetings with the route asset teams, no matter how crazy they appear. Working together to provide solutions results in our clients receiving the best service we can provide.
More recently, you’ve grown GeoAccess into an Asset Management company – what made you decide to go in that direction?
When we started out it was all about providing a technical rope access solution for earthwork inspections on the network. As we have developed and grown we quickly realised that our knowledge and expertise could offer much, much more. As an asset management company specialising in inspections, we now offer a greater breadth of services to a larger sector of the market.
You’re a small aircraft Pilot yourself, where do you see UAV and drone technology going in the next ten years?
UAV platforms and payloads have advanced exponentially over the last ten years, and in the next ten I believe they will continue to do so. Artificial Intelligence and machine learning is also going to see explosive growth. Civilian drones are already being pushed to fly further, deeper and in more remote places than ever before. In the UK we have one of the busiest and most congested airspaces in the world. Advances in
technology will result in traffic management services starting to integrate manned and unmanned aviation into the same airspace with real time deconflicting flight paths. The first important step in automated unmanned inspections.
What do you have planned for the year ahead?
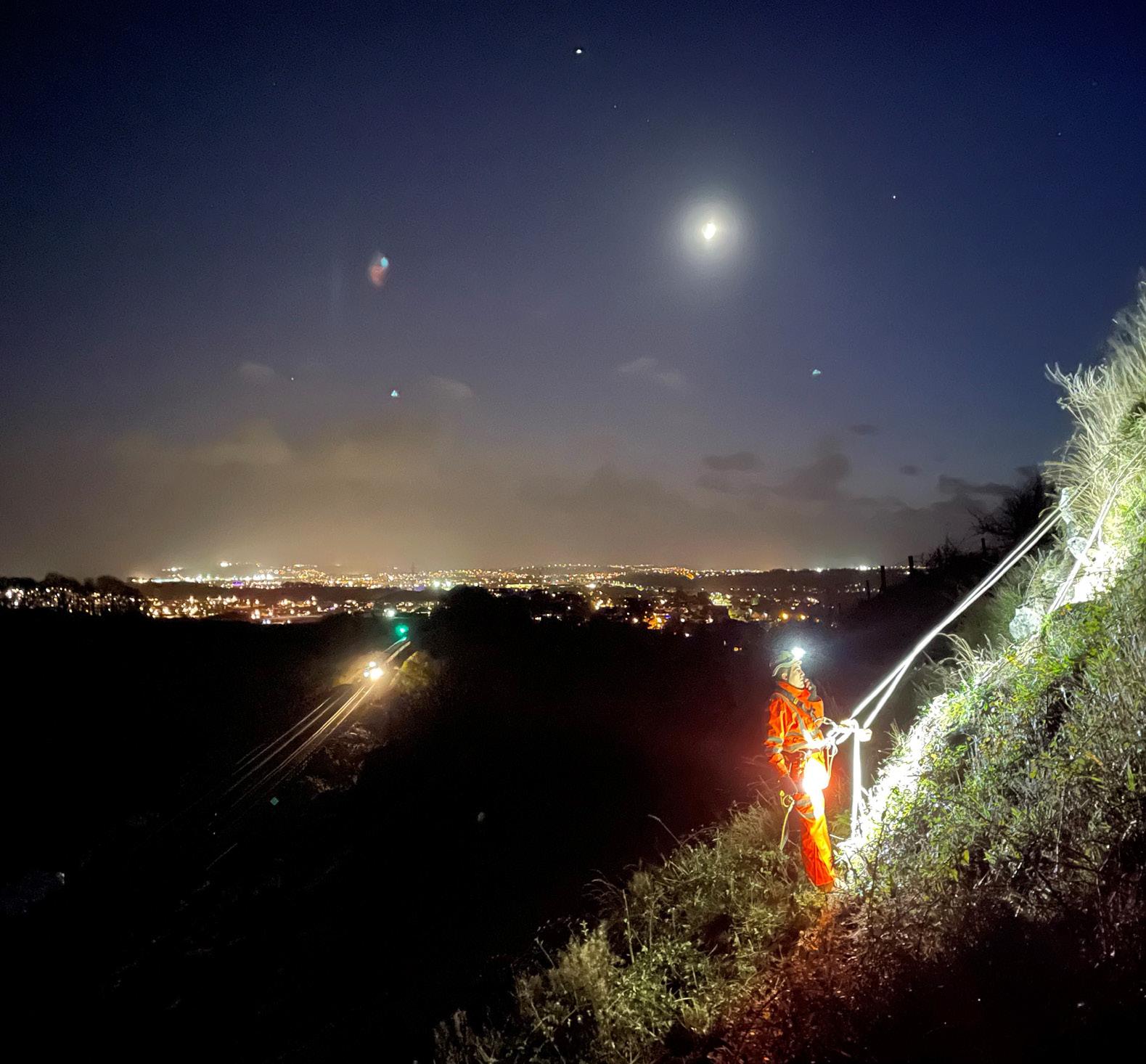
Having recently been awarded the Earthwork Examination Frameworks for Southern region and Western route, complementing our already awarded Wales route contract, means operationally we are extremely busy with these services. The teams have grown in order for us to deliver the contracts but we will be working really hard over the next twelve months to bolster our Earthwork Examiner Resources further still with the training and mentoring of a number of new recruits. We are working closely with a number of clients to explore the use of UAVs and ROVs in their workflows and management regimes to provide better asset knowledge and Research & Development is going to be pushed harder this year exploring new innovative techniques and solutions.
With the coming launch of Great British Railways, how do you anticipate your place within the supply chain changing?
I hope the coming of Great British Railways is going to see many of the barriers of entry removed that SMEs face in the current market. Collaboration and Innovation from the experts in their fields will result in a much more diverse, reactive supply chain. To be the best you need to use the best and the wealth of knowledge and expertise in SMEs is astounding. We’ve already seen this happening with great effect in the Civil Examination Framework Agreement (CEFA) contracts under Network Rail. Previously delivered nationwide by one supplier the CEFA contracts have been broken up into regional/route areas and by discipline. Some areas have taken the services in house, and some gone out to the supply chain. This has resulted in Network Rail getting a much more diverse reactive and efficient supply chain.
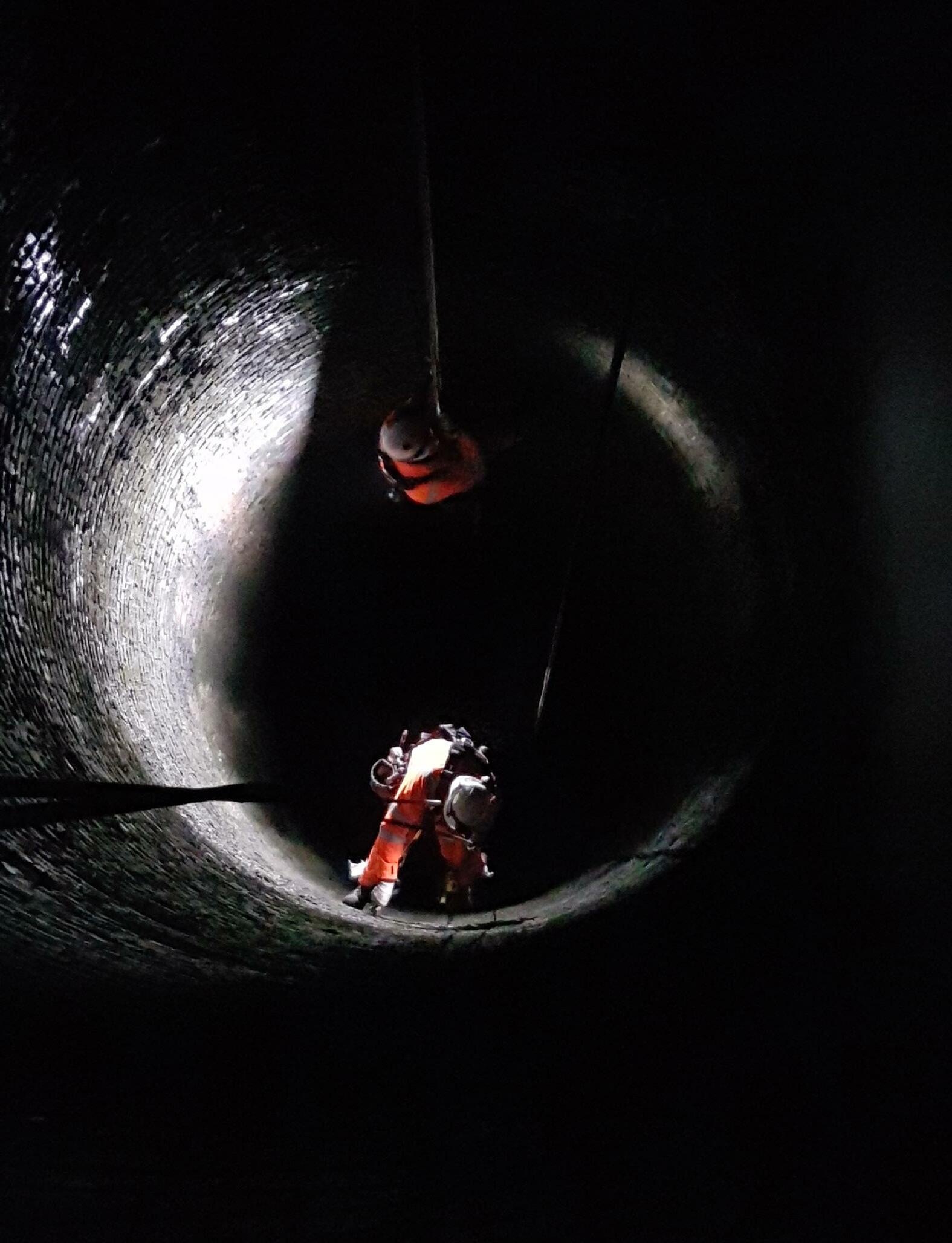
What do you expect to be the biggest challenges that come from this transformation of the railway industry?
Behavioural changes are going to be a challenge. Great British Railways is going to require everybody to work together. Collaboration is key as to work more efficiently we need to work smarter together, with shared knowledge with a common goal. The public perception is going to be a tough nut to overcome too. Lots of talk about improving the service and putting customers first is going to fall on deaf ears if it is not backed up by real change.