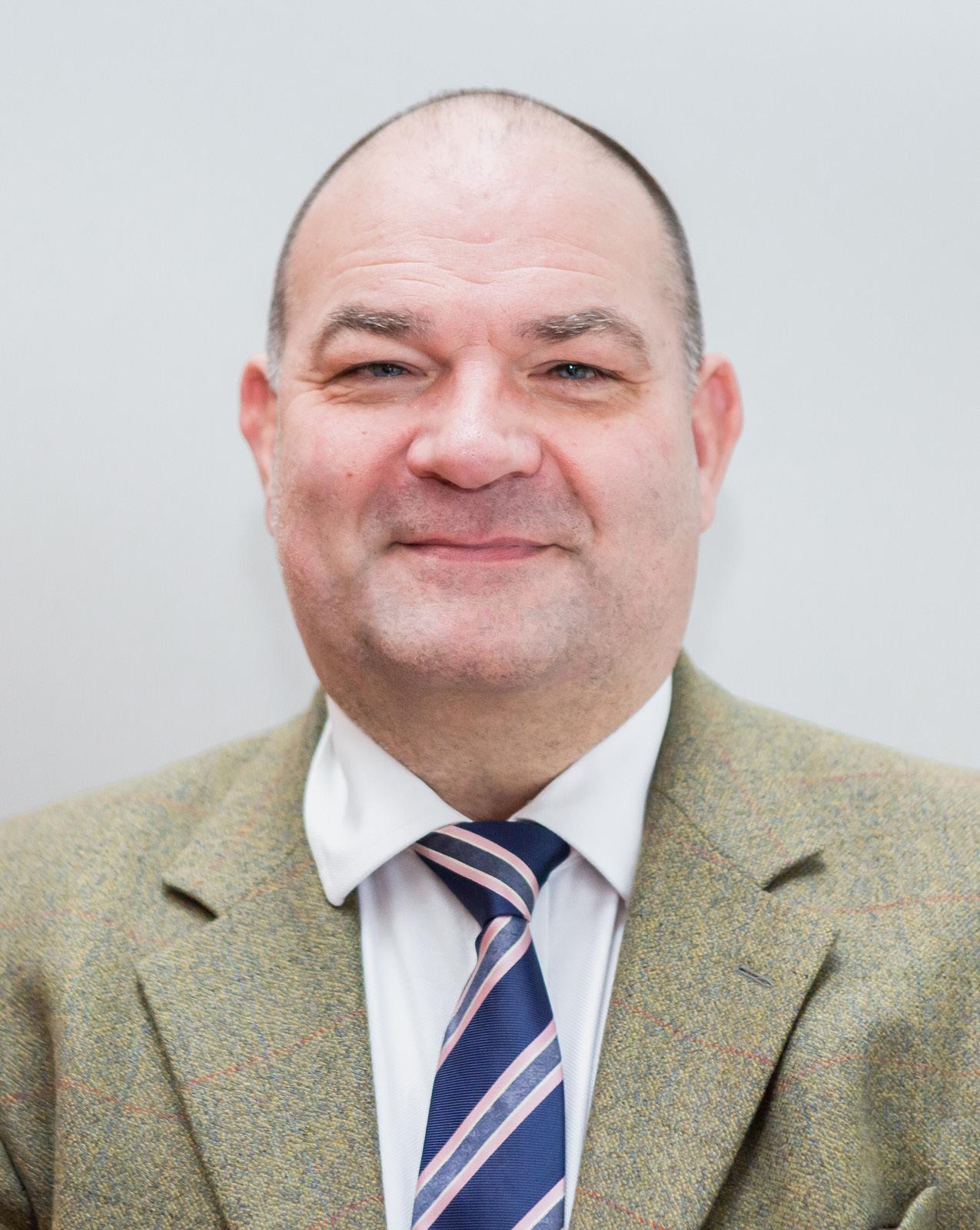
10 minute read
Rail Professional Interview
Interview David Girdler, McCulloch Group CEO
Sam Sherwood-Hale, Editor of Rail Professional spoke to David Girdler, McCulloch Group CEO about eliminating manual handling, tailoring solutions to client’s problems and being at the forefront of innovation
McCulloch Group has been in business for 30 years, having joined in 2021, how much have you’ve learned about the company in that time?
In the year that I have been here, it was important to me to get to know the founders, twin brothers Danny and Billy, and the McCulloch team, some of whom have been here since the business’ inception, to gain an understanding of the DNA of the business and I can confidently say that McCulloch Group has been at the forefront of changing the way we work on the railways.
The company began with Danny and Billy working on the railway and observing standardised working practices. This lead to the identification of better ways to complete certain tasks on the track, new methods, as well as inventing and developing new and patented machinery which would not only improve efficiency plus health and safety practices, but also saves time and money. We have documented evidence of some clients reducing previous high injury workstreams to achieving zero accidents and incidents through the adoption of our innovative plant.
From an industry perspective, obviously technology is continually evolving, and we have to respond to that by developing our products and processes. A good example is our response to the climate crisis which is going to be, if not already, the biggest challenge the rail industry faces in the next ten years. We’ve recently launched our first entirely electric product, the TRTe™, which we believe to be the first zero-emissions rail solution in the world.
As we enter our thirtieth year as a business the biggest change is the transformation from an entrepreneurial
style of business to one based on a formal business footing. We are positioned for exponential growth and the new structure is imperative to facilitate sustained success. However, the entrepreneurial culture is at the forefront of everything we do and the business will always maintain a quirky edge, which I personally love.
How do your different machines reduce man/machine proximity?
Most of our machines have been designed to replace manual railway tasks, be it removing and replacing rail panels, lifting or laying cable, or even transporting waste and debris away from the track. By utilising our machines to complete these tasks, particularly in the case of machinery that is remote controlled, it creates an exclusion zone allowing on-track workers to have a safe clearance. The vast majority of rail machinery is adapted from civils equipment. This is inherently inefficient as it is a corruption of plant that was inefficient to begin with.
An example being that McCulloch equipment generally lifts from within its own footprint. This is essentially more stable and efficient than the business as usual kit on the market.
All of our machinery is certified for work under live overhead line equipment – so that in itself means we’re keeping men off the track under live environments and removing the dangers that these environments entail. This creates an exclusion zone and keeps the operators out of harms way. This is complemented by the halo and camera system which is also in use on some of our plant. It would be a simple step to have no boots on the ballast at all, with our equipment fully operated remotely. Clearly
there is some way to go to enabling such change, but we are ahead of the curve and are also working on fully automated systems with some external partners.
We are developing a system that will completely revolutionise the repair and removal of switches and crossings (S&C). I expect this to be delivered within this
financial year and it will enable significant savings to be made in planning and execution of S&C works. A recent trial saw the panel placed in just 14 minutes! This will be shared on our new website and social media platforms in due course.
How do you eliminate manual handling?
Eliminating manual handling is at the core of everything we do at McCulloch Group and it’s the primary focus of much of our innovative kit (you can research our products to understand this more fully on our website). We work on the railway and so are actively engaged in the evolution of our own equipment with trialling and development being seamlessly integrated into our work. By the time new equipment hits the market, we will generally have put at least 100 hours of real time usage on the system.
As key products have proven popular, we’ve continually developed new additions with Billy inventing new machines and attachments to eliminate more manual handling and Danny from an operational perspective.
The Panel Lifter was developed around Network Rail’s decision to prohibit the use of any Road Rail vehicle from lifting 60ft concrete track panels. Do you typically look at regulations when developing new machinery in this manner?
Regulations are extremely important but I would not say that we are driven solely by regulatory issues. Most of our equipment is invented and developed out of a vision to improving the way in which works are undertaken in the railway and quite often this has a regulatory aspect, so we always take regulations into consideration when developing new, or existing machinery. Our purpose at McCulloch Group is to make rail infrastructure projects safer, greener, more cost-effective and time efficient. We can only do that by continually developing our offer in line with not only UK regulations, but also those in all the continents where we operate, from North America to Australasia and most places in between. We have a saying that ‘If you don’t have McCulloch equipment, then you can’t compete’.
It is recognised that UK regulations are at the top end of global standards, so given that all our kit is approved for use in line with UK regulations we know it will also meet regulations across the world with little or no change required to achieve compliance.
You also enhance your machinery throughout the years, such as the plough attachment on the TRT, what is that process like? How do you go about upgrading the machines?
We like to use the phrase ‘built for rail people, by rail people’ when talking about our products. Our product development cycle is driven by people who have extensive track experience, many of whom still work on track; who are on top of what’s happening in the industry, developments in regulations, new projects etc. They see the equipment in use and are full of ideas when it comes to how we can continually improve ontrack projects. Historically, Danny’s work in Operations compliments Billy’s innovations and there is a strong synergy between the siblings which drives this process and keeps us relevant.
Although our kit performs exceptionally well, we always have an eye to future innovation. Nothing stands still in this industry, but if we are standing still, we are going backwards.
Examples of creating new attachments for the TRT or even the creation of the TRTe, its entirely electric sibling, are made in direct response to what we see happening on track and a sheer determination to make it better, as well as customer requests – and this is a growing aspect of the business. We have a team of designers and innovators who relish solving the challenges brought to them. Combined with our manufacturing capability, including an existing relationship with Unipart Rail who assemble some of our equipment, our sizeable research and development team are cycling many innovative additions through the product cycle. This is n area of huge growth and the team is ever increasing to keep pace.
What machinery do you have that is certified to work under live overhead line equipment? All of our machinery is certified to work under live overhead line equipment. This is an incredible advantage as it can save around four hours per shift and this opens up midweek working to operators and owners of infrastructure. It is incredibly inefficient to wait for isolation. We experience this first hand on a regular basis. Just last week we were able to remove two 709ft rails and had also replaced one of them before the Road Rail Vehicles (RRVs) had even moved. This efficiency gain makes mid-week working viable and it ought to be the first choice for working. We know of the pressures that isolating overhead line equipment can cause, not only to infrastructure projects, but also to the railway network as a whole.
Our products carry out the manual tasks within the live environment, controlled remotely from track teams who can then stay within the appropriate distance from the track, keeping in line with regulations, and getting the job done quickly, efficiently, and safely.
Tell me about the McCulloch Rail trolley system, what does it do and how does it work?
The McCulloch Rail Trolley system is designed to transport heavy pieces of scrap and rail materials to and from the track.
It’s the piece of kit that’s designed to be used alongside other machines like the TRT or the Panel Lifter to create a seamless production line. This stops track teams from doing any heavy lifting or using clunkier manual machinery, such as Iron men, to transport individual pieces from the track to the designated place, a safe distance from the track. We have developed a far safer and more efficient method, so it is really disappointing to see such archaic practices still being used and smart employers have embraced the change and are reaping the rewards, as are the staff who can be deployed on other work. The industry faces a significant challenge in securing the resources required to maintain the railway and this will only worsen in the future. Our equipment allows that precious resource to be better used in a safer and more efficient manner. Everybody wins.
When a client comes to you with a particular problem, what’s your process for coming up with a solution? And how closely do you work with clients throughout the project?
We talk a lot about our products, which are inventive in themselves, but what’s a bit harder to get across is how we tailor solutions, using our range of products, to the challenges our clients present us with.
As previously mentioned, we are increasingly getting a lot of new clients coming to us with problems, seeking solutions and we have a dedicated team of designers and innovators who, if they haven’t seen it before, can find a solution.
The UK rail industry has a fairly small number of organisations responsible for railway infrastructure, so we tend to have close working relationships with the same people and companies. If a client comes to us with a project and its associated challenges, we look at that project holistically before assessing which products and contractors are required, before working out projected timescales and costs. A lot of our kit is designed to move about the track easily and within restricted spaces like tunnels, so bringing different machines together for specific projects is pretty simple and fairly seamless. We like to solve as many issues as possible and contribute to a safer railway.
It is an incredible industry and I am very proud to be part of a team that is at the forefront of innovation and practical improvements. I’m certainly highly optimistic about the growth of McCulloch Group into the next 30 years.
David Girdler is McCulloch Group CEO
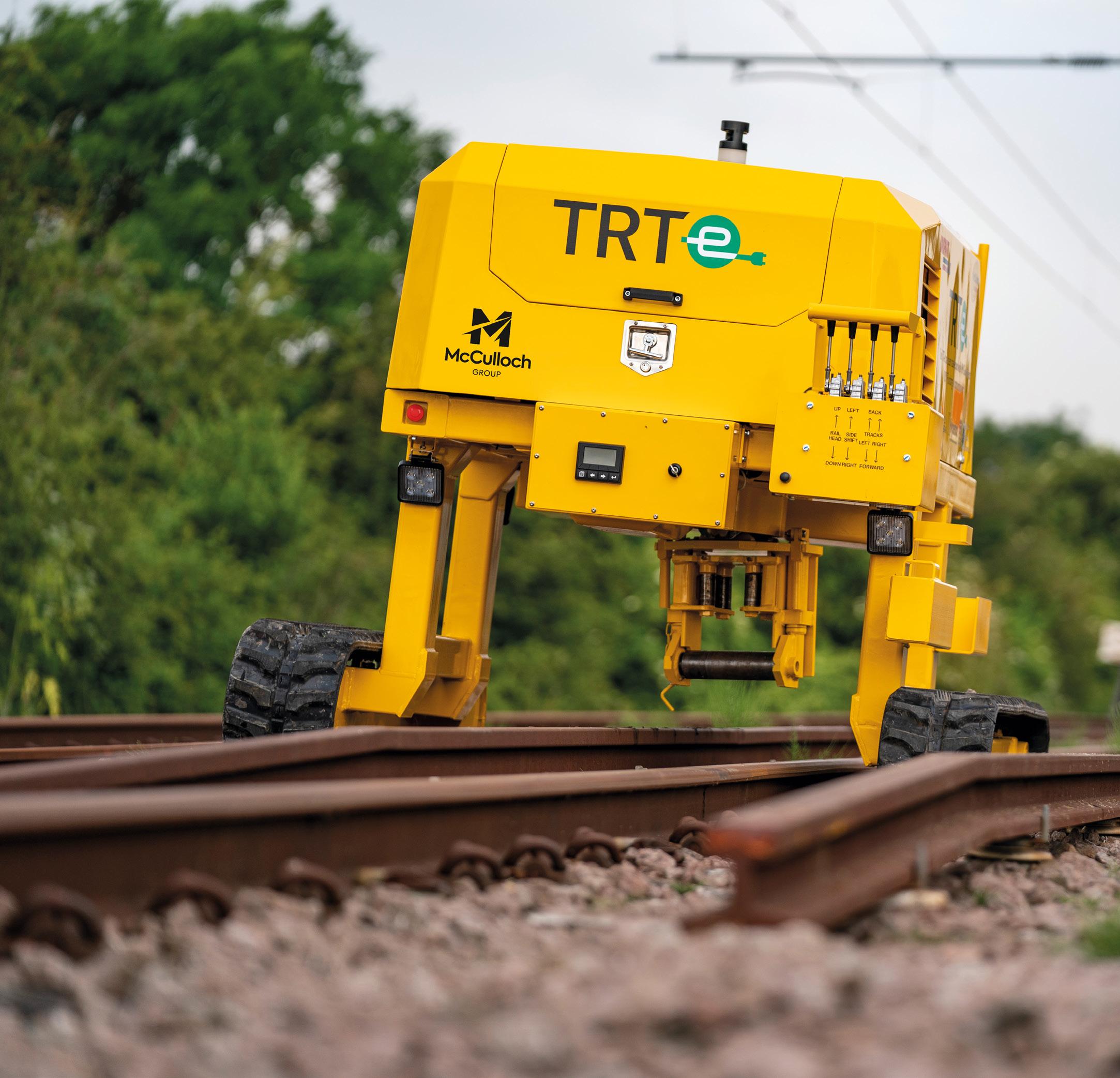
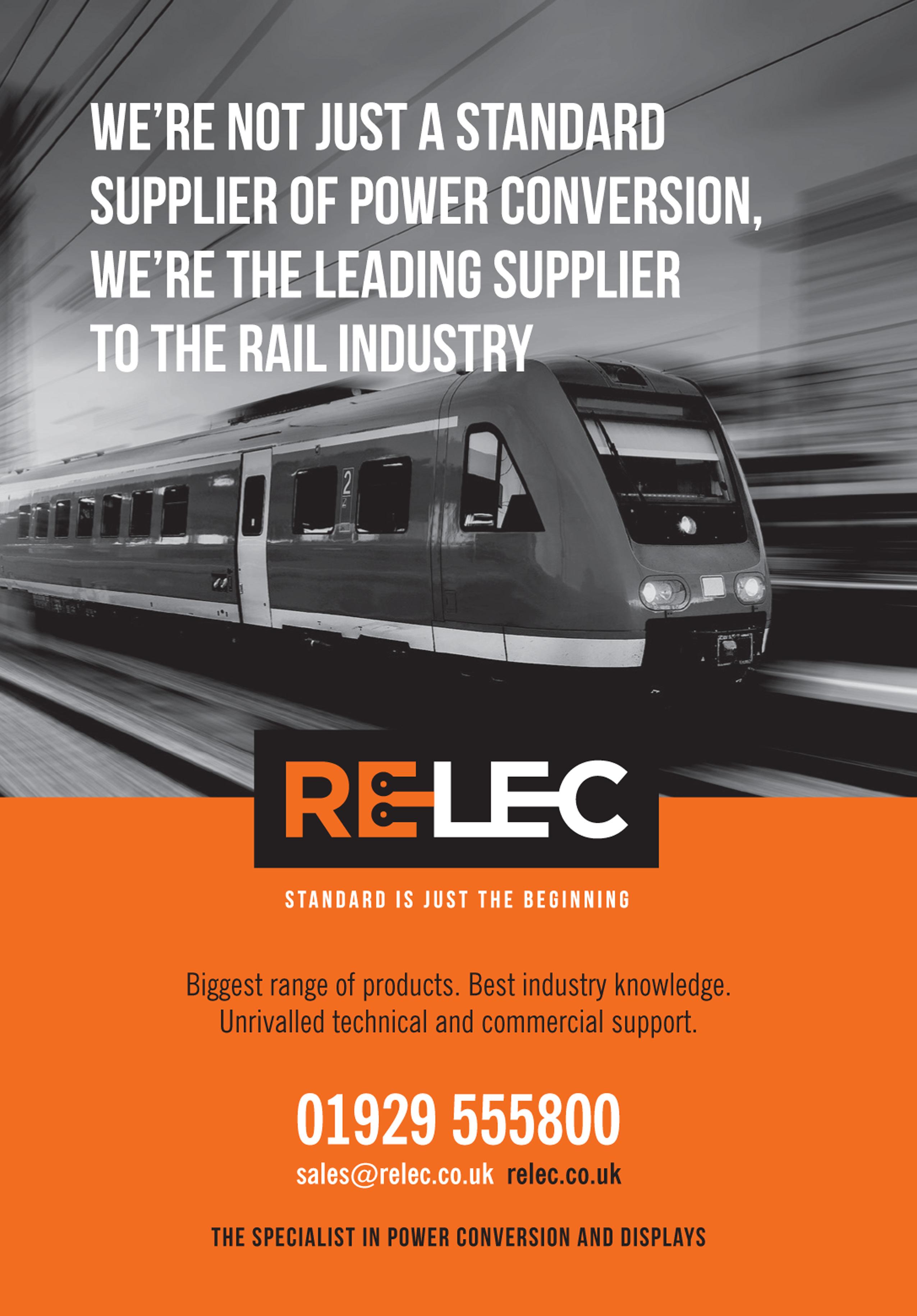