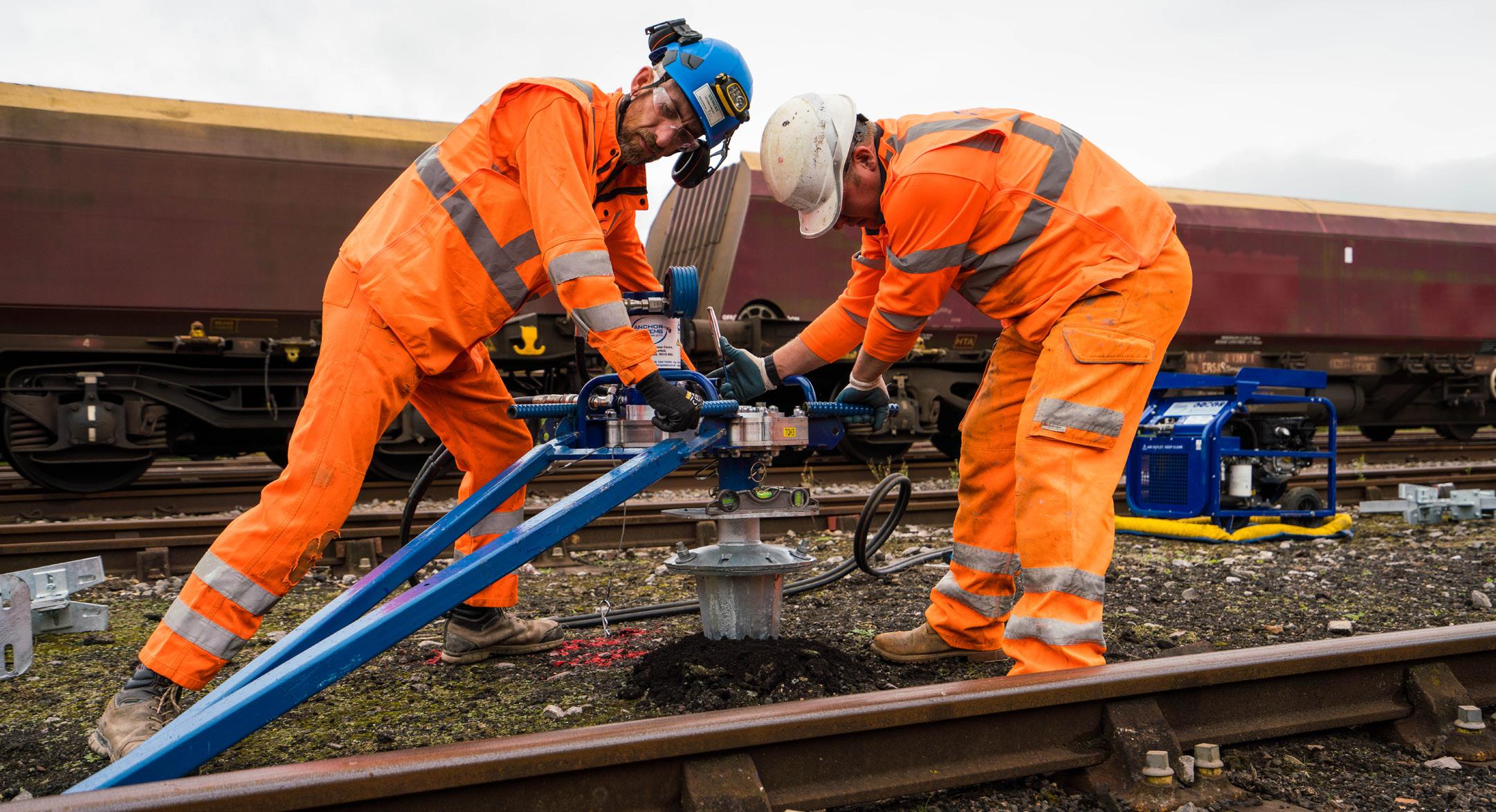
15 minute read
Anchor Systems94 Omnicom Balfour Beatty96 Galvanizers Association
Eco-Friendly Foundation Systems
On average the Anchor Screw foundation offers an embodied carbon reduction of over 70 per cent
The use of Anchor Screw products, from Anchor Systems (International) Ltd, is growing rapidly within the rail sector, including access staircases, barriers, platforms, LOC stages and almost any trackside asset.
The Anchor Screw is an easy to install foundation solution that eradicates the need to use traditional methods, such as concrete. It is entirely manufactured in the UK from recycled steel and offers a design life of over 100 years. The design of the patented domed head and bespoke interface plates, makes this foundation system the most versatile and flexible option, ensuring the structure mounted on top is always level and correctly positioned. Anchor Screws come in a selection of sizes to suit a range of loads and jobs, and can be used in multiples, with a common interface plate, to achieve even greater capabilities. Typically installed in less than ten minutes, the Anchor Screw allows work to progress without the need for drying times. The portable, hand-held installation equipment means that no OLE isolations or RRV’s are required either.
A very good example of where the Anchor Screw was proven to have huge time and cost savings, was the Westbourne Park Segregation Barrier project.
A 400-metre segregation barrier was required within six foot at Westbourne Park Station to divide the Network Rail and Crossrail Tracks, however the depth of ballast was over 1,000mm. This was considered in the clients original proposed segregation barrier solution, which would utilise multiple concrete foundations, involving multiple RRVs, ballast removal, waste management, onsite concrete shuttering, and mixing. This method of installation was estimated to take more than 20 weekend shifts with an initial budget of over £1 million, deeming the works uneconomical for the client and the network.
Due to this, Network Rail approached Anchor Systems (International) Ltd to discuss the use of their Anchor Screw foundation solution and asked them to offer a design and installation cost for the segregation barrier. Anchor Systems worked with the design team at Network Rail to understand the project requirements and together they developed a suitable design.
A GPR survey confirmed that there
was concrete track drainage located approximately 1,000mm below the ballast level, meaning the traditional ‘off the shelf’ Anchor Screw would have to be modified. Reducing the overall length to 850mm ensured clearance from the existing drain, while at the same time being able to achieve the vertical and lateral load requirements for the segregation barrier in line with NR standards.
Anchor Systems worked with Colas Rail and Network Rail to offer a complete solution with one of our approved installers, to guarantee workmanship and onsite efficiency. A total of 14 nights were required to install over 300 Anchor Screws and erect the barrier, massively improving efficiency, producing a huge reduction in workforce, heavy machinery/RRV’s, concrete, waste management, water consumption and material delivery miles, the entire solution saved the network over £650,000.
Anchor Systems (International) Ltd were also involved in a Network Rail project in Merseyside, where the Anchor Screw foundation system was used for a staircase on a railway embankment. A safe access GRP Staircase was installed on the embankment, requiring Anchor Screw piles and adjustable adaptor plates - all supplied by Anchor Systems.
The GRP access staircase links to a cess walkway with self-closing safety gate. At five
TESTIMONIALS
‘This system is great example of collaborative working. All the work and investment that went into this system demonstrates real commitment by the team for innovation and sustainability. The objectives were to reduce carbon footprint, remove concrete and water usage, remove the need for RRVs and allow a very quick installation – all of which were met and more. Nothing else on the market comes close.’ Clive Marriott: Managing Director at CSM Projects ‘The Anchor Screw system helped to significantly reduce construction time and provided greater tolerance to satisfy gauging requirements on the Westbourne Park Barrier Scheme. Throughout the design stage, Network Rail design and Anchor Systems collaborated to produce a bespoke post that could be installed entirely within the ballast formation. This system has many other applications and can offer significant efficiencies whilst providing a more environmentally friendly option compared with alternative foundation types.’ Sam Fletcher CEng MICE: Senior Design Engineer (Building & Civils) at Network Rail metres high and 13 metres long, it required 16 anchor screws with adjustable adaptor plates to support the structure.
Anchor Systems’ Anchor Screw piles were easily installed into the sloped embankment with portable handheld equipment, meaning the job was completed swiftly and with no isolations necessary. The interface plates can be adjusted, allowing for 7° lateral alteration, meaning the staircase will always be level, even on sloped and irregular ground.
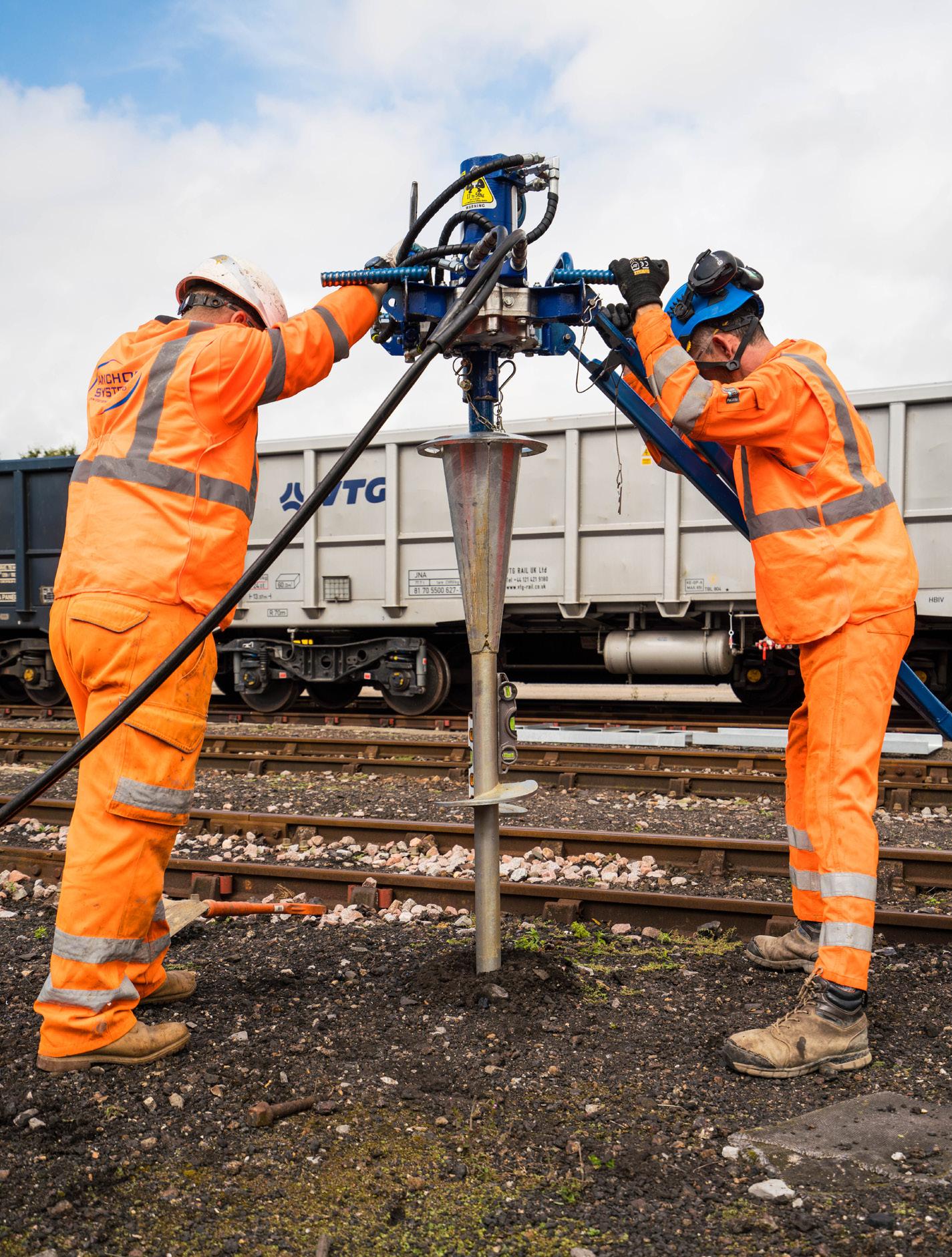
The Environment
Over and above the project benefits, the Anchor Screw offers further benefits to the network and local environment, including: • All materials are recyclable, easily removable, and reusable. • Made in the UK from 100 per cent recycled steel, with a minimum design life of 50 years. • Anchor Screw can be designed to offer 100+ year design life solution. • No wet trades, curing times or excavation. • No requirement for RRVs. • Materials can all be transported by hand and with track trollies. • Portable and lightweight installation equipment. • Reduction in hours on site and workforce required during installation. • Zero HAVS (Hand Arm Vibration). • Installation head offers low noise pollution output offering lower disturbance to local residents. • Adjustable domed head to ensure the asset or interface is always level and offers horizontal and lateral adjustment to ensure the route is straight. The patented dome head of the Anchor Screw and interface plate offers 14° overall tolerance.
Tel: 01342 719 362 Email: info@anchorsystems.co.uk Visit: www.anchorsystems.co.uk
Predict and Prevent, Infrastructure Management
Omnicom Balfour Beatty provide intelligent measurement insights to the rail industry, promoting a safer, more efficient, and sustainable railway for all
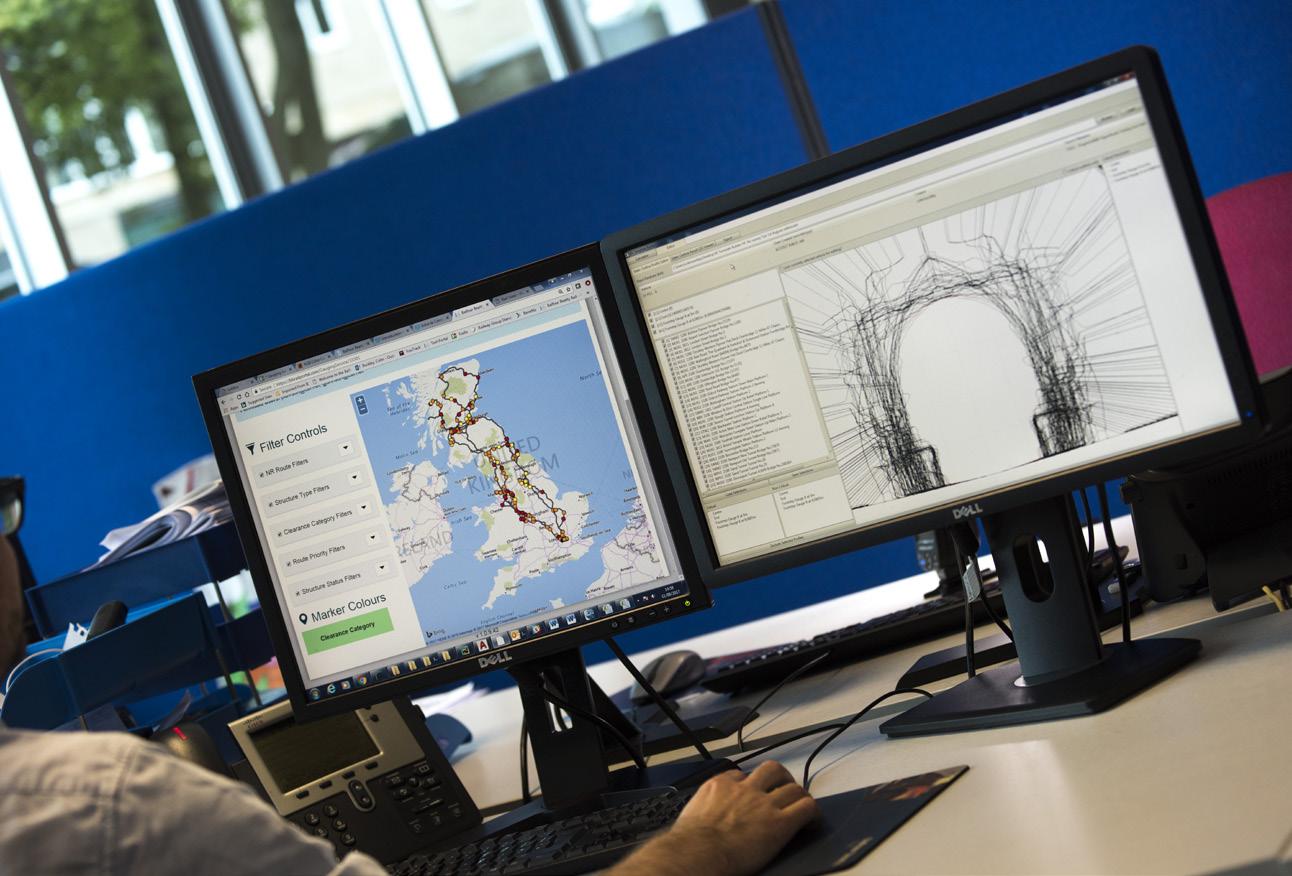
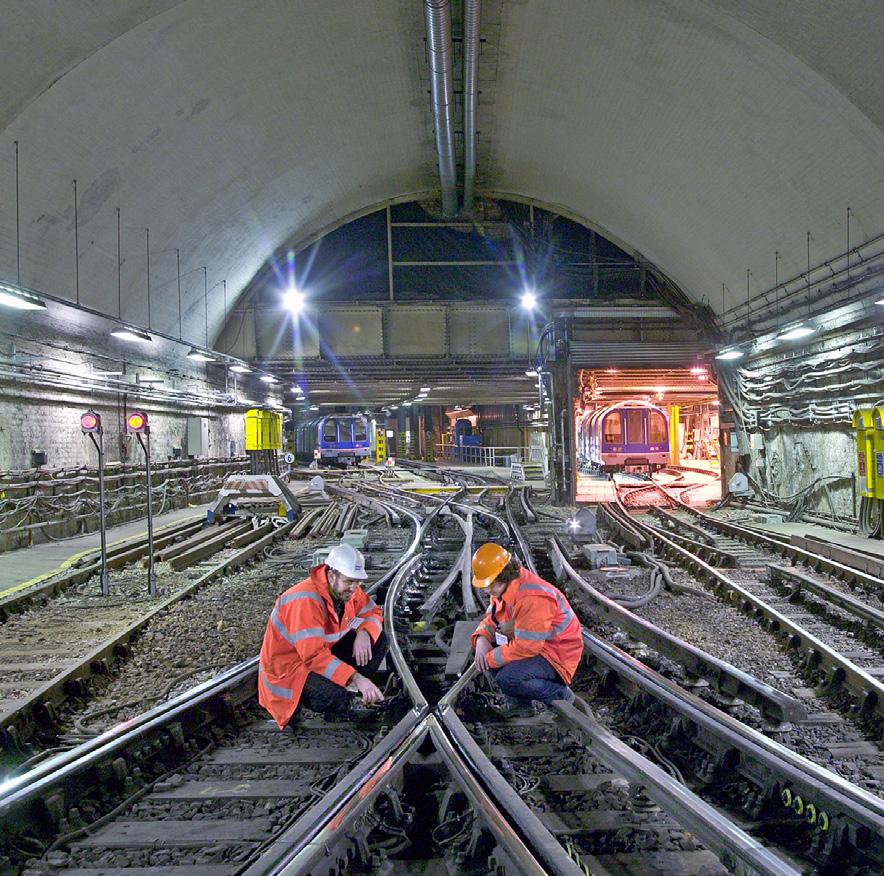
Indeed, the world’s most valuable resource is no longer oil, but data. At the core of the digital transformation of the rail industry is the ability to harness the power of data insights – with this, it is possible to usher in a vastly improved rail network for all.
Operating at the forefront of the industry’s technological evolution is Omnicom Balfour Beatty (OBB). OBB’s unique capabilities extend right through the data cycle from point of capture to processing and visualisation.
The UK railway serves as a complex and vital transit infrastructure for millions of individuals every day, however by nature of being close to two-centuries old, the once mighty British railway faces numerous challenges in terms of safety, efficiency, and sustainability. To overcome the lacking modernity that the industry needs, increased investment in the transport sector, as well as a positive embracement of technology, will be vital for the next era of train travel.
While increased digitisation provides the means for innovation and improvement across all rail, it is no secret that the performance of train services has not met such expectations for improvement in recent decades. When Britain’s Rail Network was first privatised, the government predicted that a combination of increased competition between train-operating companies and general free-market forces in the sector would contribute to vast improvements in service. However, today the very contrary has come to fruition as ticket prices have risen, and lateness hit a 13-year high in the UK in 2018.
As fragmentation of the railway is reversed and Network Rail (NR) transitions into Great British Railways (GBR), they will undoubtedly incentivise the industry to provide data collection services (DCS) – further emphasising its place in the era of ‘big data’. OBB recognises that harnessing such data insights will be key to monitoring infrastructure and equipment whilst optimising maintenance and the improvement of safety. From this, operational and technical complexity can be reduced across the industry and the ability to accommodate additional transit capacity on the network can increase - without the need for building expensive new physical infrastructure.
The vision shared amongst market innovators, like OBB, is to encourage the move to a more predictable railway whilst eliminating the hefty cost, safety and efficiency considerations associated with unplanned maintenance. But, to achieve this GBR will require three things: expertise in data science methods, expertise in railway domain knowledge and the ability to access the data.
Technological Progression and OBB’s Contribution
In the knowledge that future rail companies should be underpinned by punctuality and excellent customer experience, why then
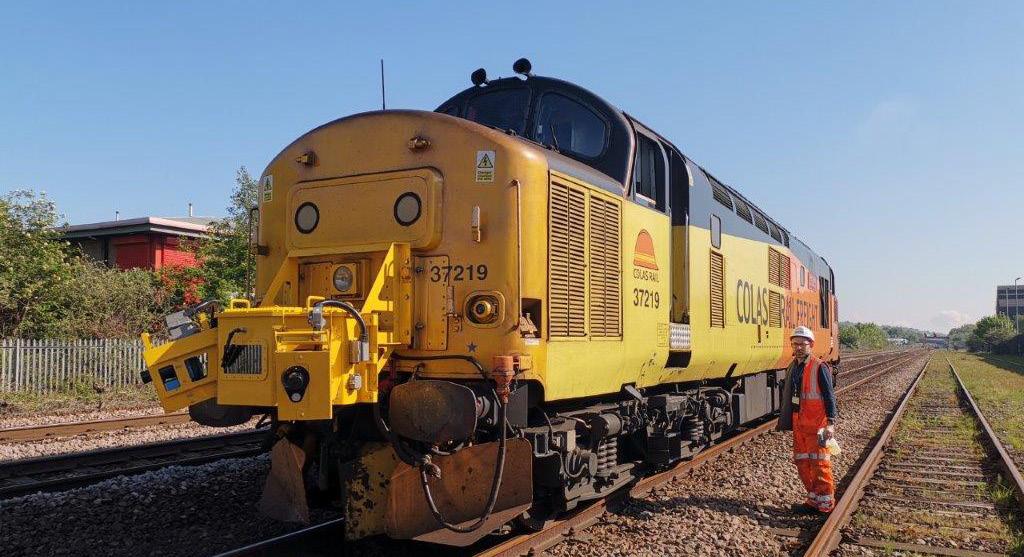
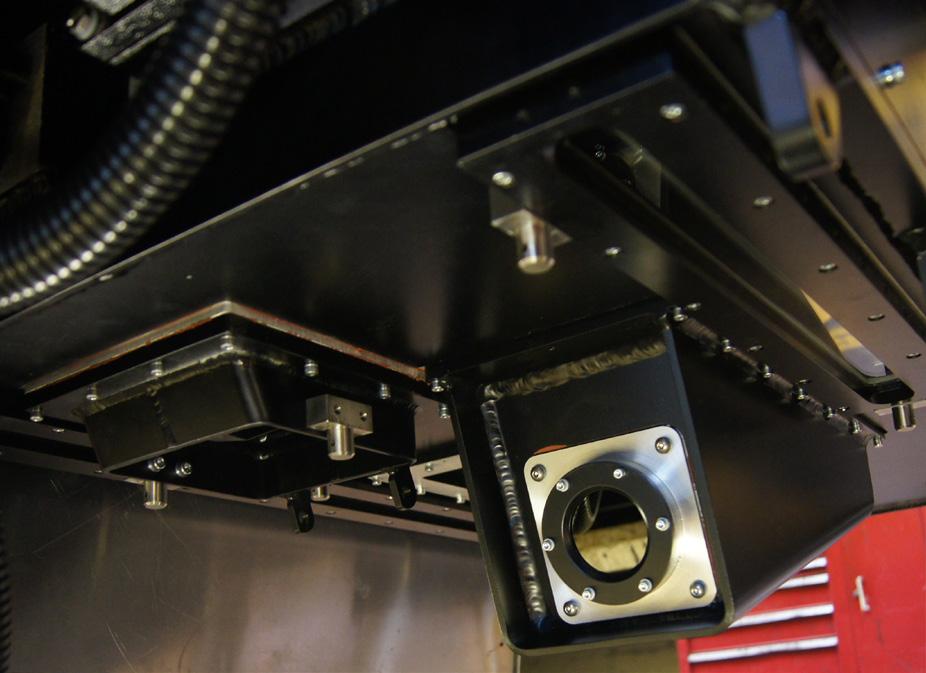
Sanjay Razdan, Managing Director of Omnicom Balfour Beatty, 2022
(according to the latest ORR reports) is it the case that only 72.4 per cent of services arrived on time in Q1 of 2022? Some argue the root of this problem is a lacking investment in the smarter technological solutions necessary for overcoming this statistic.
For instance, through machine learning, predictions concerning disruptive asset failures can be identified sooner so that intervention is anticipated with more effective maintenance scheduling. This, in turn, helps train operating companies to avoid delay-repay compensation penalties and protects the safety of passengers by decreasing the likelihood of rail defect development.
Reducing the need for urgent, unplanned, and reactive work means that technicians are less required to be exposed to trackside risks through the avoidance of red zone working. This ‘predict and prevent’ ideology is core to the business offering that OBB provides to the industry.
OBB aims to support customers in realising and optimising the power of data. Possessing extensive skills and experience in single and multi-disciplinary solutions for a wide range of rail projects, OBB also offers expert training and support across the suite of software and hardware products available. Based in both York and Derby, OBB is surrounded by industry experts and is well positioned to leverage the specialist knowledge that exists in such localised industry clusters. Over its 24year history, OBB has seen a substantial increase in capability, starting with just event monitoring systems and scaling up to include infrastructure monitoring, remote condition monitoring and mobile mapping systems.
Infrastructure Monitoring
With Balfour Beatty’s acquisition of Omnicom Engineering the company took over the development of various infrastructure monitoring tools. Adopting such technological capabilities gave rise to the OBB product ‘OmniVision’ – a powerful automated visual track inspection solution comprised of AI-powered computer vision software in conjunction with highresolution cameras that are mounted onto trains collecting information at high-speed (typically 125 mph in the UK). This helps to reduce the frequency of track inspection patrols by delivering powerful track defect insights straight to the user’s desktop. Whether users are concerned with missing fasteners, excess ballast or ineffective rail clamps, this technology allows for detailed inspection of track elements at 70,000 images a second. The utilisation of these tools permits a vastly automated workflow that leverages the latest in plain-line pattern recognition (PLPR) machine vision and now Deep Learning AI to assess the rail profile using big data processing and hyperdetailed track geometry data. PLPR is live on 70 per cent of the network and improves asset quality, with a significant reduction in track defects.
Mobile Mapping
Survey tools, such as ‘OmniCapture3D’, add laser-scanned point-cloud capture, data mapping and asset modelling so that a virtual model can be created of the network. This data can then be viewed from multiple angles using software programmes such as ‘OmniSurveyor3D’ – another powerful tool that builds a digital environment map for the particular benefit of signal sighting simulation and immersive driver route learning.
Known across rail as the industry’s leading engineering tool for gauging and clearing assessments, OBB’s ‘ClearRoute2’ software utilises both a user’s own survey data as well as infrastructure data from the national gauging database to inform design and planning decisions through vehicle modelling and compatibility assessments.
Remote Condition Monitoring
Level crossings, represent a particularly challenging interface between NR and the public. They typically require frequent and lengthy inspections due to the safety-critical nature that underpins their use and the complex operational sequences that permit their function. OBB’s solution, ‘OmniLX’, revolutionises the remote condition monitoring model for level crossings by eliminating the need to perform costly, time-consuming manual inspections on a quarterly basis and providing a predictive maintenance regime. Instead, OmniLX, combined with OBB’s advanced dashboarding software ‘Asset View’, provides real-time data insights concerning asset condition and performance – highlighting any degradation present on more than 20 barrier function points on a more consistent basis. This informs asset maintainers sooner and prevents costly failures and repair works that would otherwise be required.
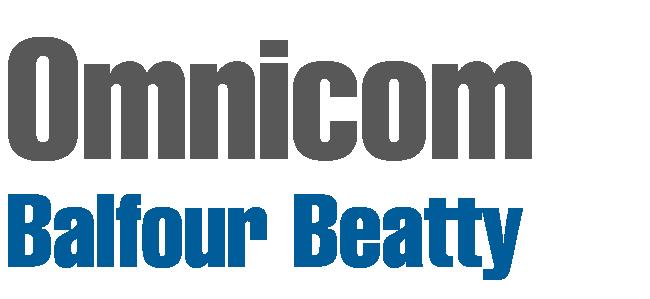
Raynesway
West Service Road Raynesway Derby DE21 7BG
Eboracum House
Clifton Park Avenue York YO30 5PB United Kingdom
Tel:01332 476 070 (Derby) Tel: 01904 778 100 (York) Email: OmnicomCS@balfourbeatty.com Visit: www.omnicombalfourbeatty.com LinkedIn: Omnicom Balfour Beatty Twitter: @omnicombb Facebook: Omnicom Balfour Beatty YouTube: Omnicom Balfour Beatty
Luxury or Long-Term Sustainable Solution?
As the construction sector senses economic turbulence the task of recognizing what is real value for money has become more important than ever
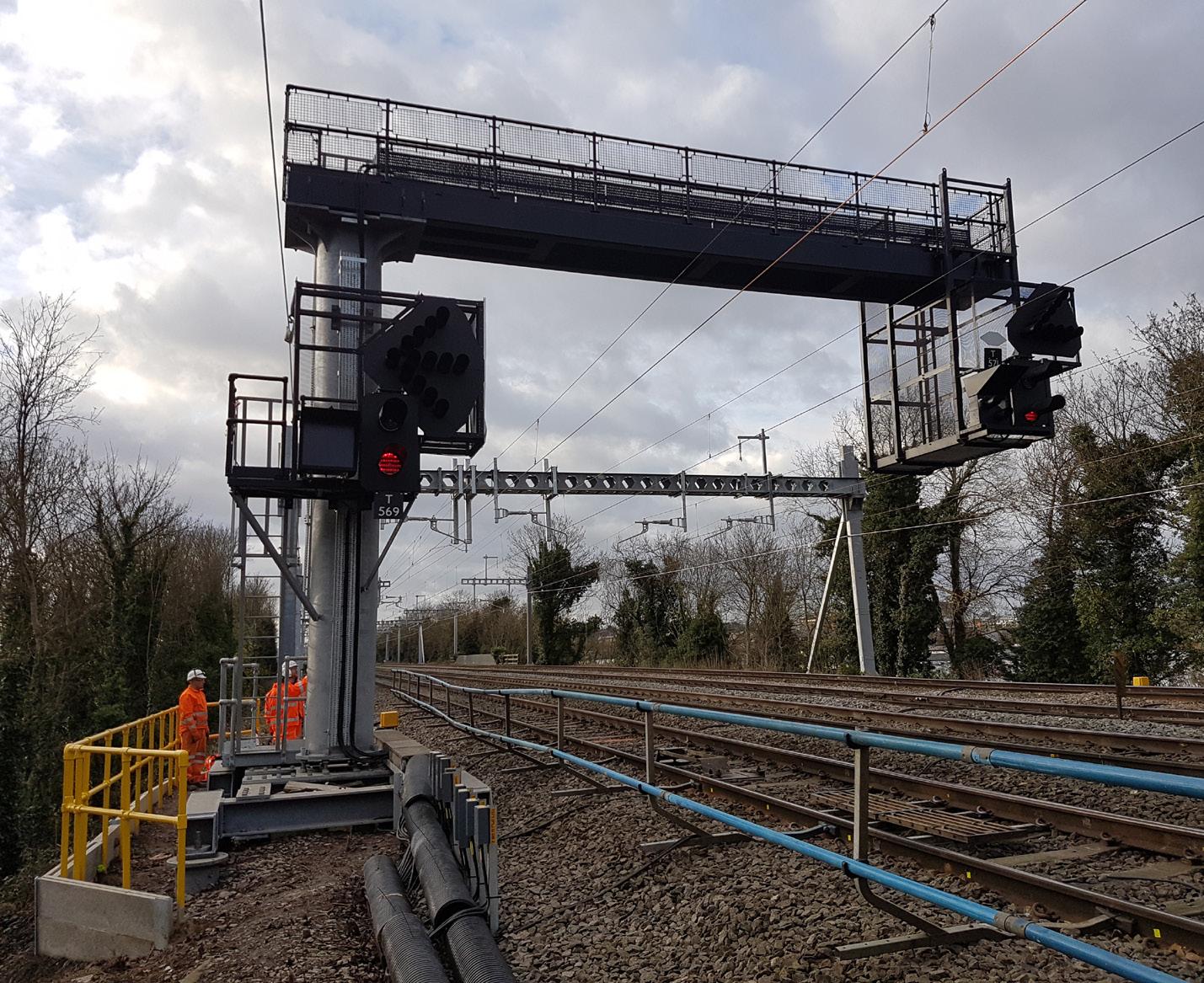
Identifying true value for money is crucial business, especially at a time of economic uncertainty. Couple that with the complexities of reaching both sustainability targets and pledges to support UK business and the task becomes even more demanding. For UK rail transport, the sensitivities around the cost of planned upgrades and major infrastructure expansion, such as HS2, continue to grow, as do the pressures around supply chain and delivery.
In the face of this mounting pressure and rising costs it remains vital that we understand how to quantify value for money and that sustainable, circular solutions remain central. There is little justification for opting for materials or short-term solutions which are unproven, and which will require maintenance or carbon costly replacement in a few short years. Being truly cost-efficient is about choosing the most durable and sustainable option. A product’s value should be assessed by its ability to both meet specifications and last multiple lifecycles.
Meeting climate pledges and spending less over time
It is widely appreciated that choosing circular materials is key if HS2 and other planned network improvements are to meet their stated aim of decarbonizing UK transport. Galvanized steel makes an ideal partner as it aligns with key principles central to circular design and construction. A recent test case in the Netherlands shows that circular models of remaking galvanized components can lead to 40 per cent reduction in environmental costs and ten per cent reduction in costs when compared to other dispose and replace cycles. At scale the potential benefits of integrating circular components and structures into public transport schemes will offer significant economic advantage over the long term and help reduce carbon footprint.
Galvanized steel aligns with the hierarchical, accepted models of circular economics in the following ways:
• Refuse • Reduce • Reuse • Remake • Recycle Priority One – Refuse
Galvanized steel offers the highest levels of durability, delivering once-only solutions that last the lifetime of a building, component or structure. This allows for an emphasis on avoiding the environmental impact of further unnecessary construction.
Priority Two – Reduce
Data on the corrosion protection offered by a galvanized coating shows how the process of galvanizing steel components offers lifetime protection and reduces maintenance burdens over the lifetime of a project.
Priority Three – Reuse
Galvanized steel is an ideal material for reuse, as it is robust and does not damage easily. It is suited to modular design, is easily disassembled for reuse and can provide multiple life cycles of a building or structure. If a building is designed with reuse in mind, entire structures can be repurposed or individual components can be put to diverse use.
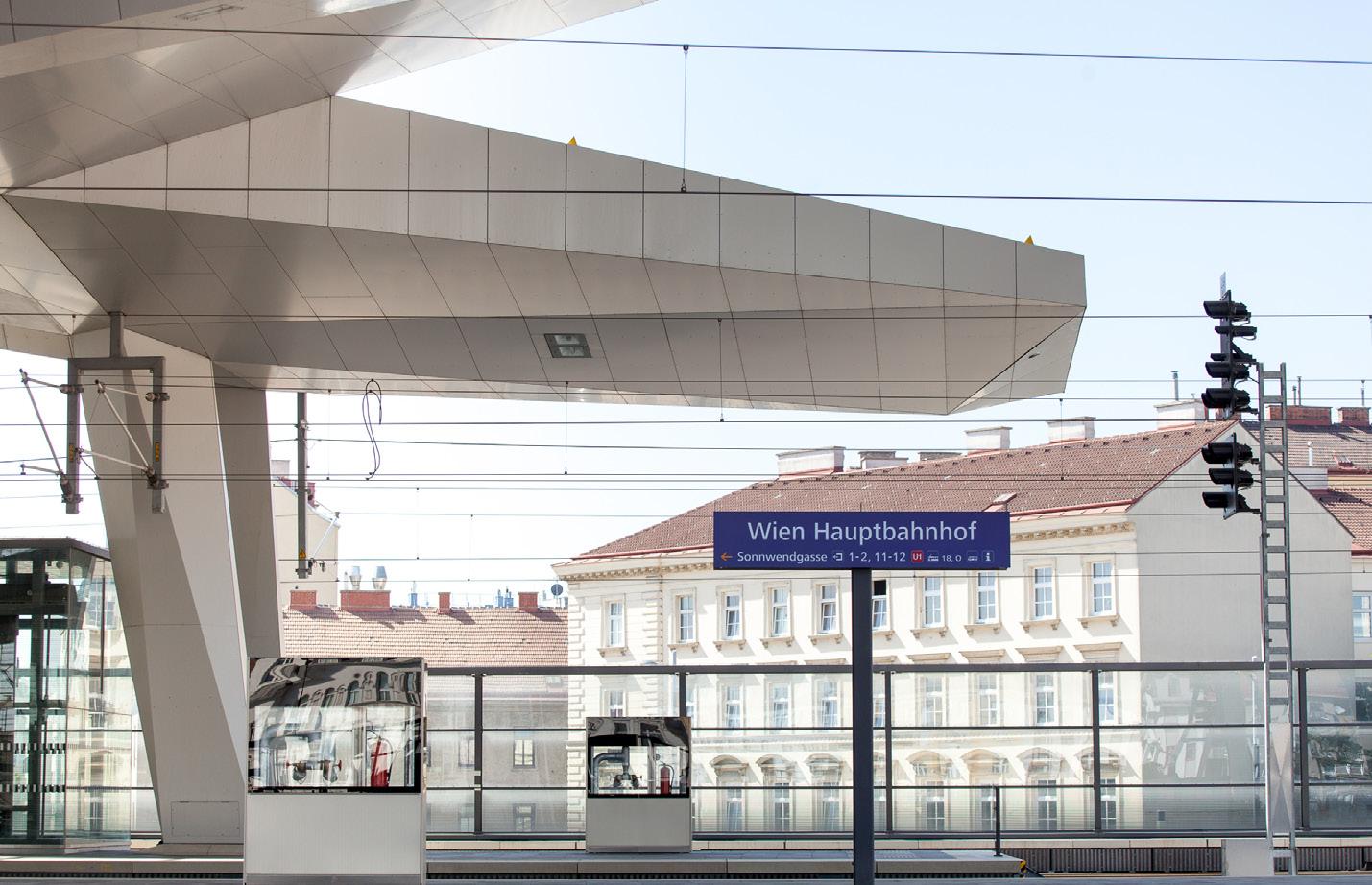
Priority Four – Remake
When the limits of reuse of an existing component or structure have been exhausted, galvanized steel presents an excellent choice for remaking, as the coating stays with the steel and no additional coating is needed in any subsequent use. Galvanized steel components can be easily adapted, re-galvanized and put back into service – avoiding the environmental burden of new steel production.
Priority Five – Recycle
Galvanizers Association gives clear end of life information on how steel and zinc are recycled together – without loss of properties – to produce new galvanized steel. As zinc corrodes at a very slow rate, recycling will not happen for many decades, with some coatings providing the best part of a century of use.
Circular principles
The UK galvanizing industry has long been a voice for sustainable construction and has recently produced a publication Galvanized Steel and Sustainable Construction: Solutions for the Circular Economy.
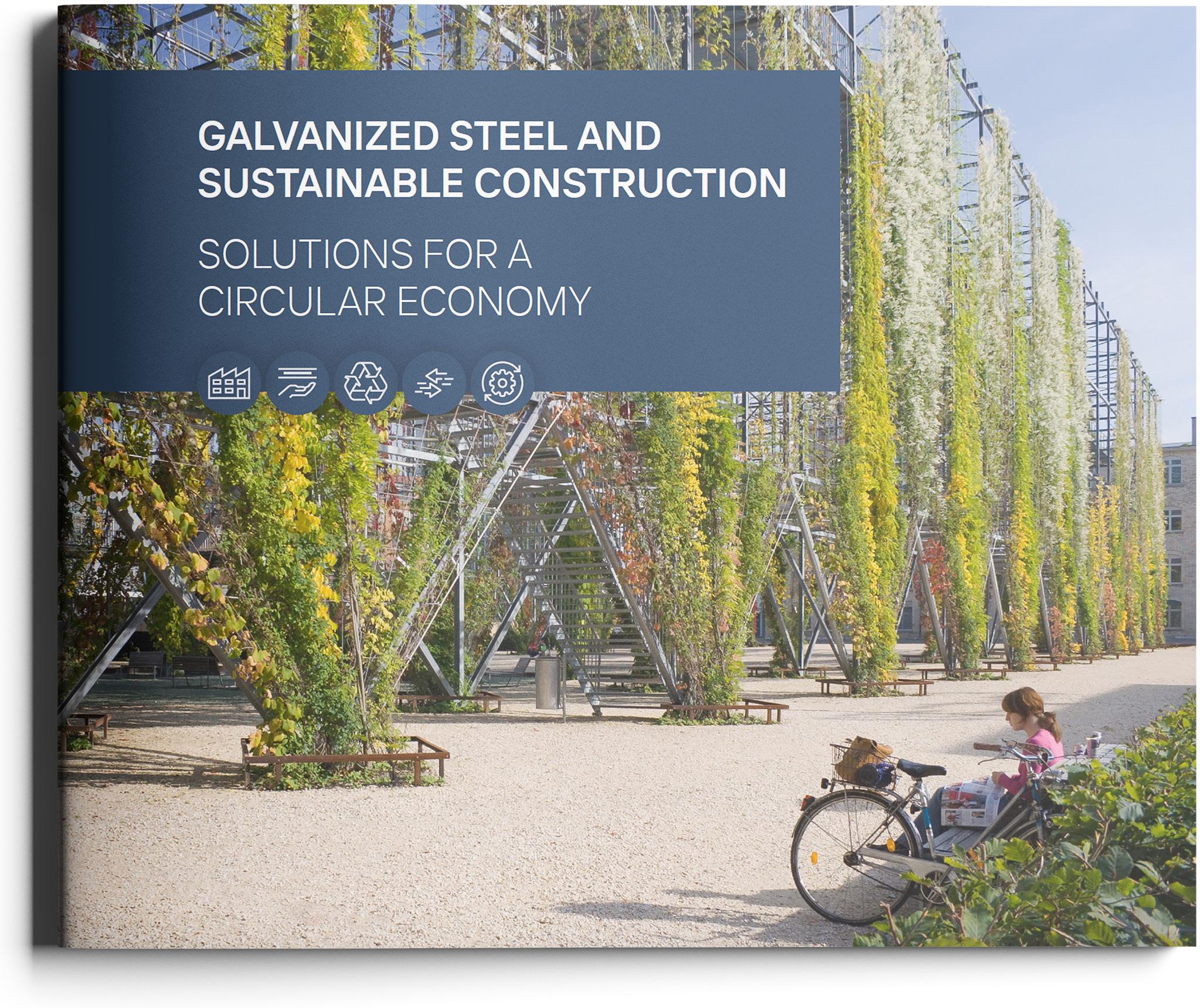
The guide highlights leading examples of how circular principles are already shaping construction throughout Europe and how galvanized steel contributes to cost savings and ambitious, circular design. Yes, building a world class rail network and decarbonizing our existing network in the face of rising costs, may be a tall order. However, this doesn’t mean that cost saving over the long term should be seen as an unaffordable luxury.
Find out how galvanized steel is supporting UK transport and infrastructure projects by joining its Industry Open Day 20 October 2022. For details of participating galvanizing plants near you and to see hot dip galvanizing in action go to: