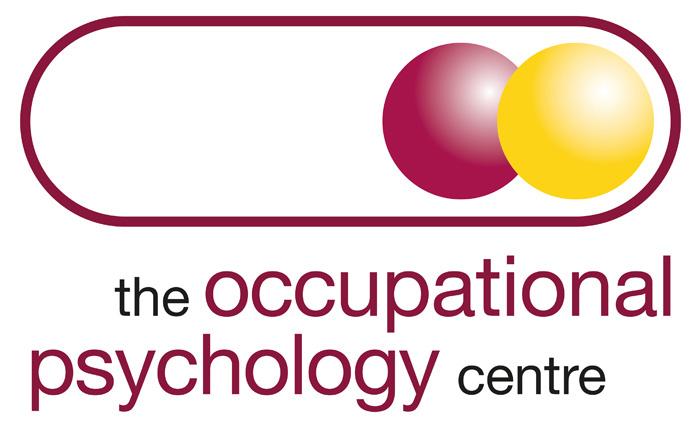
11 minute read
SAFETY AND SECURITY Gaynor Stewart and Dr Stephen Fletcher on preparing
Preparing for Every Eventuality
Gaynor Stewart, and Dr Stephen Fletcher, share some insights from a safety incident simulation in a controlled environment preparing for the worst possible eventualities

In January 2021, Alstom completed its acquisition of Bombardier Transportation. As part of the change management and people management processes, team integration was a high priority. It was important to merge the two teams from Alstom and Bombardier, creating co-ownership and a sense of belonging in the new organisation as well as building capability, agility, and strong structures. Post-pandemic there was also a need to reconnect employees, creating inclusive teams across the two businesses.
So, a team building event was decided upon that could also explore how well equipped and prepared the newly merged business was, should there be a major safety incident involving one of their trains. The concept of running a major safety incident simulation was initiated.
To support the training, Alstom decided to call in the expertise and experience of the Occupational Psychology Centre (OPC) who’ve worked in the rail industry for over 30 years. The OPC are a team of occupational and business psychologists, specialising in safety performance, with a drive to help build successful, high performing and motivated teams – so, extremely well-equipped to support Alstom’s people management change programme and a major safety incident simulation.
The people involved
Broadley, MD Services, Alstom UK & Ireland, who also took part in the cross-functional team event too. During planning discussions, Gaynor Stewart and psychologists from the OPC, decided to extend the learning opportunity and make the simulation more realistic, by inviting other key stakeholders from the Office of Rail and Road (ORR), Rail Accident Investigation Branch (RAIB) and the Train Operator, Avanti West Coast. This made the simulation event even more high profile, adding more realistic dimensions and additional learning opportunities for all involved.
The simulation scenario
The OPC created a fictitious ‘worst-case’ train derailment scenario, which went like this – at, approximately 11:55 on 17 November 2021 a Pendolino train on route from London Euston to Edinburgh station suffered a significant derailment incident, North East of Carstairs Junction. The train was in reverse formation. The train departed London Euston at 06.43am. Onboard are approximately 130 passengers including eight TOC staff, and two onboard cleaners. The emergency services are instantly activated and en route to the site, along with Avanti mobilising their immediate response teams.
Without delay, Alstom employees had to organise themselves into operational teams to deal with the simulated major safety incident. They were overseen by controllers and observers from across Alstom, the ORR, RAIB and the OPC. In real time they needed to deal with emerging critical issues. They were fed information throughout the simulation on an hourly basis, along with having to deal with simulated phone calls, media enquiries, fake reports and interference.
The initial report of the simulated derailment that Alstom teams were presented with was the location of the site. It was remote with difficult terrain access i.e.; the main road was approximately 1/2 mile away with thick woodland which impeded access to the stricken train. Mobile phone signal reception was intermittent. The Wi-Fi equipment wasn’t working and the GSMR in the cab was defective. There’s a reservoir nearby with the possibility that a number of carriages have skidded into the water. The Government Environment
Simon Kay, Inspector, RAIB
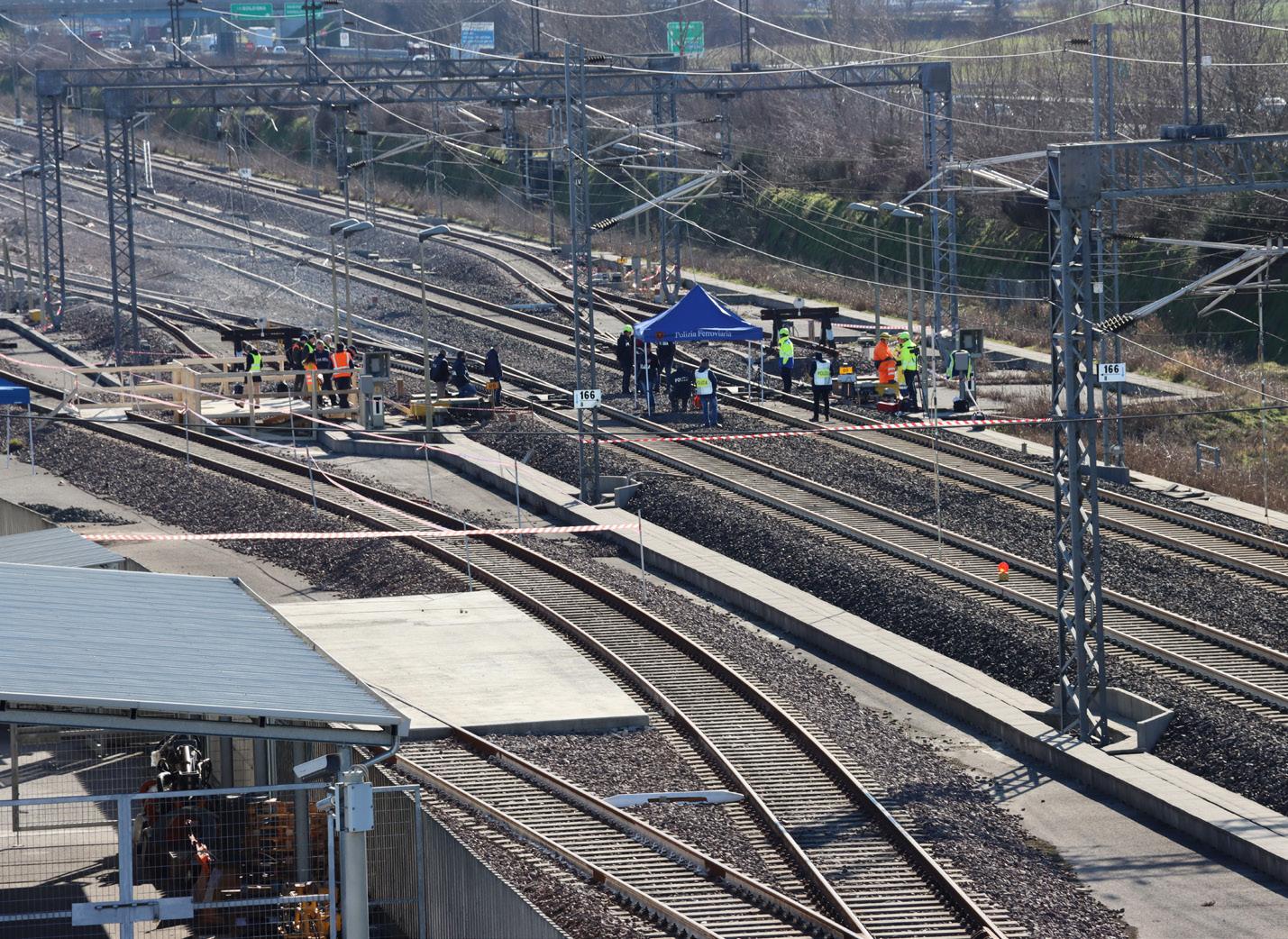
Dr Steve Fletcher, Director and Occupational Psychologist at the OPC
Agency has become involved and they’re requesting information regarding substances on the train i.e., transformer oil, gearbox oils. The weather conditions are hampering the rescue. It’s wet and stormy. There were initial fatalities reported along with some serious passenger injuries and some minor injuries. All-in-all, a difficult and tragic safety incident is depicted.
Rapidly, simulated media activity kicks off with news reports of the derailment and twitter feed from locals and passengers alike – providing valid as well as fake information. The multi-organisation team running the event fed information to the role-players each hour – some was ‘factually correct’ other information was deliberately misleading. They received documents, phone calls, announcements, reports, images and media video recordings of the scene unfolding at the simulated derailment. Just as in a real-life major derailment incident – teams had to prioritise, as well as sift what was factually correct or spurious and act swiftly to respond to all information and requests in an appropriate manner.
The cross-business observers monitored how Alstom teams set themselves up; how well they responded to information; their leadership qualities; internal and external communications to stakeholders, emergency agencies or enquirers; their transparent and accurate incident logging; how well they dealt with media enquiries and the overall strategic management and direction of a such a difficult scenario. The official observers team collected evidence and scrutinized processes – all to provide strengths and development opportunities for Alstom as a whole organisation and individual employees.
As the simulation unfolded over the twoday event, further issues came to light and started to complicate the scenario – was it a crash, or was it a derailment and what was the root cause?
There were obstacles to resolve to aid the emergency services trying to rescue train operatives and passengers trapped because of faulty electrics and inoperable doors; questions and challenges from ‘on-site’ emergency officials about the train functionality and liquid leakage – all challenges for Alstom’s newly merged engineering team; along with a fake retired Alstom employee who set themselves up as an unofficial media ‘spokesperson’ at the simulated derailment site.
Key operating teams were set up to manage and oversee certain aspects of the simulation event, these included a Senior Leadership Team (SLT) responsible for oversight, the strategic management and direction of the incident and policies/ procedures; an Investigation Control team dealing with the operational activity; a Communications team, for internal communications between teams and information flow, along with external media enquiries and management; and an Incident Control team, dealing with activity, resolution, engineering and logging.
During the simulation event strategically, important decisions also needed to be considered and dealt with by Alstom’s SLT, as in any real-life major incident. Questions such as, should Alstom recommend suspending the Pendolino fleet? Were other train operating fleets still operationally safe too? Immediate enquires from the RAIB team about the possible derailment causes and information requests to uncover any underlying causes of the safety incident. What and where was the evidence of any causes? Along with more challenging questions, such as possible accountability, responsibility and legal considerations and what role might a fleet manufacturer, such as Alstom play in those. The whole way through the simulation, all the delegates were faced with some very intense and difficult challenges.
Dave Whitehouse, Director of Safety and Security at Avanti West Coast
Incident operations
Regardless of whether this was a simulated event for a train manufacturer or for any other rail operating business, there were some beneficial crisis management learnings that could be considered as helpful, but these are by no means definitive.
In the event of any kind of crisis or major safety incident, it is essential to have an Emergency Recovery Plan (ERP) for key roles and players, with internal and external focus, strategies and priorities. An ERP can lay down clear protocols for how to manage any unexpected critical incident effectively, efficiently and as safely as possible. Including a Command Structure with clear roles, responsibilities and accountabilities that are ‘off the shelf’ is extremely useful.
Once created these can be adapted to any unexpected emergency or safety critical situation with speed; giving clarity and immediate direction to employees allowing a much more efficient operation and swift response earlier on.
‘I applaud Alstom for arranging this event. Effective emergency planning ensures the mitigation of risk and consequences of foreseeable emergency scenarios’.
Nigel Bunce, HM Inspector of Railways
Communication
Communication planning and preparedness is essential in any kind of ERP for both internal and external communications. Considerations that were well played out by Alstom teams and highlighted via the simulation event were about; efficient and clear internal communications to their own community; Communication timing – the right information to the right person at the right time. It’s important to have a single point of contact in each operational team. Appointing the right trained ‘spokesperson’ for external communications is crucial – someone who can deliver clear and consistent messages with care and consideration for the audience. This also includes what not to say! Always having one point of contact for the Emergency Services. In a very multi-media channel world, bringing structure and consistency to any and all communications is a real strength.
Recording and logging
In any major safety incident, recording all information accurately and clearly is essential. Alongside of this is a document control protocol e.g., what, where, status, who has it, who’s responded to it or when will this happen. A timeline logging protocol for information may often be the most beneficial process and requires a loggist in each individual team. These individuals are the ‘Information Gurus’! The go to person and initial contact – But just because they have the information, does not mean they respond to every request. An employee allocated to this role in an emergency needs excellent communication skills – listening, verbal and written; focus and attention to fine detail abilities along with data processing, management and checking skills. In any major safety incident, the need to record what decisions were made and why is crucial in case of external scrutiny or legal implications, if relevant.
The support, input, feedback and insight from the ORR, RAIB and Avanti West Coast added real authenticity to the simulation event. Dave Whitehouse, Director of Safety and Security at Avanti West Coast said: ‘We routinely conduct safety exercises containing a broad spectrum of scenarios. Having the opportunity to run one of these jointly with our critical partner, Alstom was really beneficial for both organisations. Neither of us ever want to have to activate our crisis plans and thankfully due to the professionalism and commitment of our teams it’s a rarity in our industry. None the less, it’s important that should we be required to react to a major incident we’ve ensured that quality time has been invested to vigorously test the robustness of our plans. Therefore, enabling us to implement them swiftly, professionally and effectively to protect the safety of all our staff and passengers.’
At the OPC, we are passionate about driving individual and organisational – performance. This simulation was many months in the making with lots of time, hard work and effort expended by key people across all the organisations involved to ensure its success. By doing a major safety event simulation, what we’re really doing is ‘future-proofing’ our organisation – Planning and preparing for the unexpected and equipping our leaders, teams and individual employees with the skills, and abilities to perform exceptionally well under extreme conditions. We often talk about individual resilience, but this type of exercise provides organisational resilience – in case of the worst possible eventuality. It’s unusual for a major safety simulation event like this to be organised and run by a train manufacturer. It displays the high-calibre responsibility of Alstom’s approach to their train operating clients and the industry as a whole. An extremely fulfilling piece of work that comes along in a rare moment and a real privilege for the OPC to be involved in such an important learning event.
For Alstom, this was a huge investment of time, resources and effort from a multifunctional, cross-business team, including our Senior Leadership Team – testing our resilience and response agility to such a safety incident event. It was extremely well organised but very intense! Everyone took it really seriously despite it being a role-play scenario. Employees’ motivation, commitment and enthusiasm were apparent right from the start with everyone aiming to ensure the safety incident emergency was managed as effectively and efficiently as possible. Individuals were very professional – conscious of any safety implications their actions and decisions would have, therefore responding with cautiousness and careful consideration. I believe there was a significant return on investment with major learning and ‘future proofing’ for both the Alstom organisation, as a whole, and individual managers too.

Gaynor Stewart, Customer Services Director at Alstom
Gaynor Stewart is Customer Services Director at Alstom and Dr Stephen Fletcher is Director and Occupational Psychologist at the Occupational Psychology Centre (OPC).