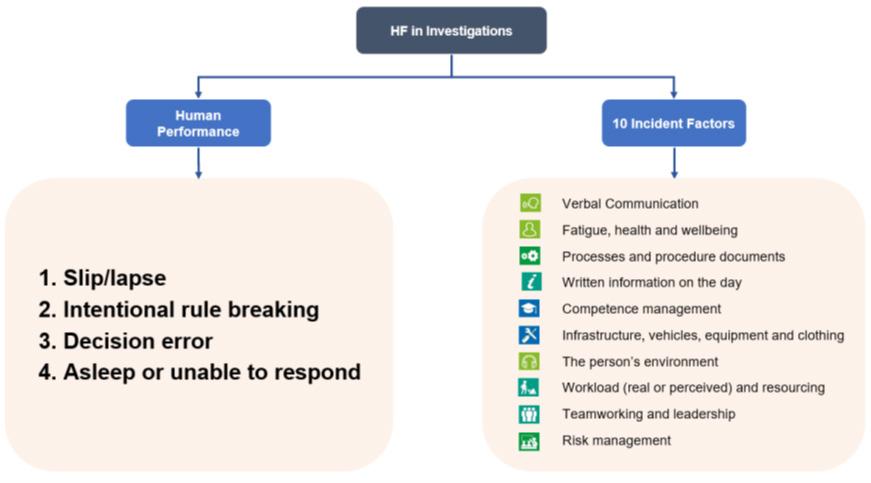
3 minute read
SAFETY AND SECURITY
Inputting Detailed Cause Information into SMIS
We all know that accidents seldom have a single cause. They arise from multiple causes that come together to form a casual chain
Therefore, whilst it is often an unsafe act by an individual that is the immediate cause of an incident, there are usually weaknesses in the system that have made that act by the individual more likely.
Because of this, the 10 Incident Factors were developed, which are geared towards identifying the broader issues that may contribute to an adverse event. These are now joined by a framework of human performance factors, as set out in the rail industry’s investigation standard, RIS-3119TOM (Figure 1). The best way to see how these elements can help is with a couple of case studies. The Safety Management Intelligence System, known to many as SMIS, is the rail industry's online health and safety reporting and business intelligence software. It collects and provides access to information on thousands of safety-related events that happen each year on the rail network in Britain.
Case study one – freight
GB Railfreight (GBRf) has been inputting detailed cause information into SMIS since January 2019. As the company’s Head of Safety, Stuart Anderson, says: ‘We have been targeting causes of incidents which are linked to our three most common ten incident factor groups: equipment design, risk management and competence management. We have also invested in a non-technical skills programme based on the cause data from our safety events.
We want to continue to build on this to enable us to deliver the safest freight working environment for our employees which has a direct link to their wellbeing and in-turn the sustainability of the business.’
What does this look like in reality? GBRf has entered causes for 129 events which have mapped in turn onto 351 causal factors.
When the ten incident factors were analysed across all events, the most common categories were infrastructure, vehicles, equipment and clothing (IVEC), competence management and risk management.
SMIS cause data becomes richer the deeper you dive into the analysis. For example, when you look at event type, different incident factor categories feature more heavily. So, for SPADs, Competence management is the most prevalent group whilst for slips trips and falls and railway operating incidents IVEC issues are the most common. The detailed cause data in SMIS includes factor descriptions which bring the data to life. Descriptions like: • Train Manager was new in post and had broken periods of mentoring whilst in training due to mentors being used for other tasks. • The rear two wheels of the wagon came off the rails due to compacted sand on the railhead causing the rear wagon to derail.
Human Factors Framework for Investigations (RIS-3119-TOM)
Case study two – passenger
The Operations Standards team at Greater Anglia has also been inputting cause information for 50 events, with a total of 173 causes.
Steven Starling, Operations Standards Manager at Greater Anglia says: ‘Competence management was identified in several incidents due to being unable to travel in the driving cab for assessment during the Covid-19 pandemic, and our simulators being replaced. This resulted in many trainees not having simulator experience before passing as train drivers. Assessors now follow up assessments carried out via download with one to one socially distanced or telephone professional discussions. Additionally, newly qualified and at-risk drivers are prioritised for simulator sessions on their re-introduction. By introducing this, we achieved a reduction in operational incidents.
‘Vehicle and infrastructure issues highlighted several wrong side door releases that were caused due to the setup of onboard CCTV DOO equipment. The design issue was factored out with support from the manufacturers.
‘We have also acquired support to assist in further developing Non-Technical Skills (NTS). One-to-one coaching sessions are used with high-risk drivers, Driver Managers are being upskilled on their NTS knowledge and are asked how we can better integrate NTS within assessments. The next phase for GA in this journey is to establish a NTS leadership team to implement a structure to further implement the NTS approach.’
Read the full case study at https://www. rssb.co.uk/services-and-resources/case-studylibrary/smis-the-benefits-of-inputting-detailedcause-information