
14 minute read
Influential Railroaders
from Railway Age May 2020
by Railway Age
CONGRATULATIONS to Kansas City Southern EVP Administration & Corporate Affairs Warren Erdman for being selected one of Railway Age’s 10 MOST INFLUENTIAL INDUSTRY LEADERS
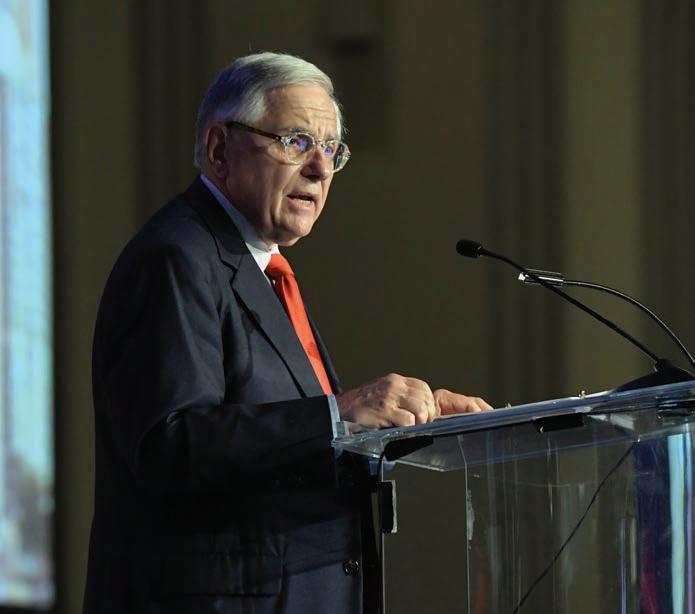
“I’m a product of those with whom I’ve associated throughout life. That is why I often say at FRA, it is from you, about you and ultimately for you. In essence, I truly serve the people.” — Ron Batory
Tracy Miller, Senior Vice President Operations Southern and Eastern Regions, Canadian Pacific With 25 years of Class I operations experience, Tracy Miller consistently enhances the efficiency of the operation by looking at every single move that is made and considering the impact in the larger picture. He’s able to create efficiencies by changes

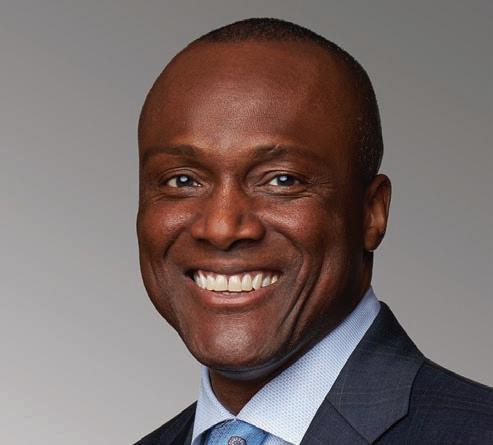
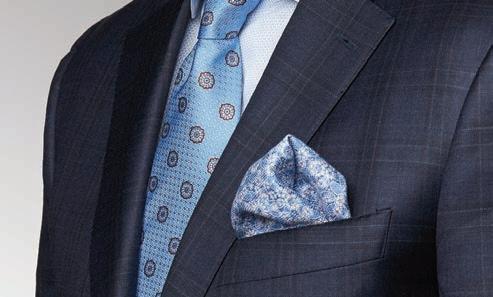
The CP family congratulates Tracy L. Miller for being named a top 10 Reader’s Most Inuential Leader.


to switching operations, reiterating the importance of following the plan, changing the plan when it isn’t as efficient as it can be, and so much more.
The combination of Miller’s extensive railroading knowledge and solid operating background enhances Canadian Pacific’s leadership team’s bench strength, and bolsters the company’s long-term people development and operating goals. He does this all while treating everyone with respect and dignity. The efficiency CP is seeing today would not be possible without people like Miller, as everyone has a desire to be more efficient and respectful. He has the buy-in and discretionary effort from his entire team. Miller started at CP as Vice President of Corporate Risk - U.S. in March 2019; earned the Vice President of Operations - Southern Region title in July 2019; and has been SVP Southern & Eastern Region since September 2019.
Albert Neupaver, Executive Chairman, Wabtec Board of Directors
Al Neupaver has led Wabtec through its greatest growth period, to a Fortune 500 company.
Al Neupaver joined Wabtec on Feb. 1, 2006 as President and CEO, and a member of the company’s Board of Directors.
Neupaver has led Wabtec through its greatest growth period, to presently $11 billion and an NYSE Fortune 500 corporation. Mergers and acquisitions during Neupaver’s time include Standard Car Truck (2008), Faively Transportation (2016) and GE Transportation (2019). Neupaver championed LEAN approaches, reduced waste, added value, exemplified passion for new product development and supported V-ETMS PTC on all classes of railroad implementation and communication. He was named Executive Chairman on May 14, 2014. On May 10, 2017, Neupaver assumed the role of Chairman of the company’s Board of Directors. Prior to joining Wabtec, he spent nine years as president of the Electromechanical Group of AMETEK, Inc. Under Neupaver’s leadership, the Electromechanical Group increased its operating profit by almost 60%, more than twice the rate of its sales growth. Neupaver joined AMETEK in 1988 as Vice President and General Manager of its Specialty Metals Products Division. Prior to AMETEK, Neupaver spent 11 years with Pfizer, Inc. in several engineering, operating and business management positions. He served in the U.S. Naval Reserves for 25 years and retired as a Captain in 2002.


There’s a reason why Superman is referred to as the Man of Steel. The high-tensile alloy is strong yet modifiable. It serves as the foundation of Clark Kent’s alter ego, as well as the foundation of the rail industry. So it doesn’t take a railroader X-Ray vision to see that extending the life of steel rail by as much as 10 times is a solid idea. Rail grinding, milling and welding all can do just that. In addition, they’re excellent ways to reduce surface defects, increase fuel savings, move heavier loads and support faster train speeds. optimum profile so that it meets with the wheel at the proper contact area,” according to Dereck Bartz, Global Product Manager for Rail Treatment, Harsco. “There are a lot of things that can affect the wheel/rail interface, things like worn wheels—not all wheels are brand new and not all wheels are at condemnable limits—but there is a variety in between those two spectrums.
SUPERHEROES OF RAIL

Grinding, milling and welding can extend the life of steel rail up to 10 times that of untreated rail. BY ANDREW CORSELLI, MANAGING EDITOR
And then you’re essentially finding the sweet spot of the right rail profile so that you have proper contact in the proper place.”
Bartz says that the process works thusly: Service providers measure rail at various parts of track—tangent rail, curved rail, degree of curvature, etc.—and then take measurements of a typical wheel profile to get a number of wheel samples that the customer has and try to develop what the average wheel profile is in their fleet.
“And then we work with our Protran group to take that information and run it through our computer simulation, and it produces profiles of what the desired rail profile should be in order to have the proper contact,” Bartz says. “We then use a grinder to shape the rail head to that profile.”
Though it depends on GTMs (gross tonmiles) and the type of rail—light-duty, heavy haul, etc.—Bartz estimates that “it’s pretty safe to say that, over the years, grinding has extended rail life anywhere from three to 10 times over the life of rail that doesn’t undergo grinding.”
Orgo-Thermit, a Goldschmidt Company, is in its eighth year of performing rail grinding with its VM8000 on/off track two-way vehicle. The New Jersey-based welding products and services provider agrees that grinding can add life to the track, but not just worn rails. “Performing rail grinding after the installation of new track is immensely important as the removal of rust and mill scale is the best method to prepare the rail for revenue service,” the company notes.
Maintenance equipment and services provider Loram has its own method for grinding, which serves heavy haul, international, specialty and transit railroads. “Before any grinding happens, Loram collects all the necessary data,” Loram tells Railway Age. “This includes the size of the railroad, rail specifications and the track time available for maintenance. After the data is collected, Loram analyzes the data sources relating to rail wear, rolling contact fatigue (RCF) and defect generation to help understand any trends that may cause different areas on the railroad that require more or less grinding. This then helps to create the overall grind program.
“The data is then used to determine the appropriate size and number of grinders needed to adequately maintain the system. Schedules are created to move the equipment through the railroad’s network to help maintain the entire system at the optimal grinding intervals, which maximizes the efficiencies of the equipment and realizes the greatest rail life savings. A Rail Inspection Vehicle (RIV) is then used to inspect the track to determine the work requirements needed to restore optimal rail profile shape and remove RCF. After the RIV generates a custom grind plan, the grind plan is then executed.”
Loram adds that it has upgraded to its RG400 Series Railpro™ software program, which features added pattern combinations and lets the user control speeds and passes based on real-time machine and rail conditions, and can precisely schedule point-topoint network grinding.
GRINDING IS IN OUR DNA
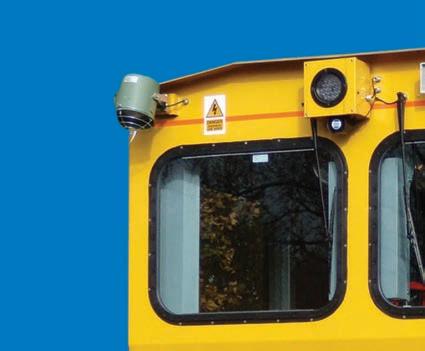
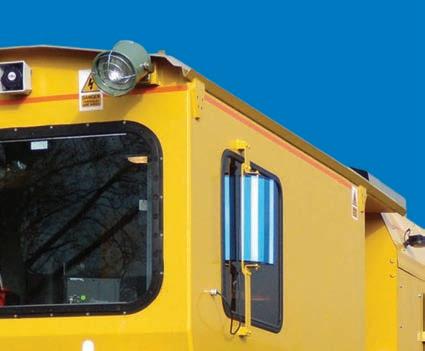
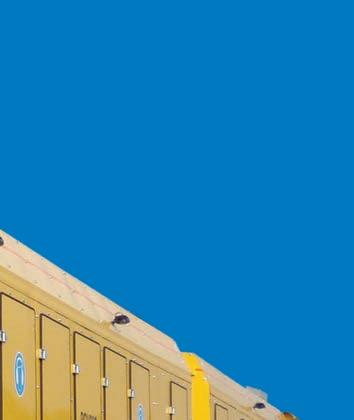
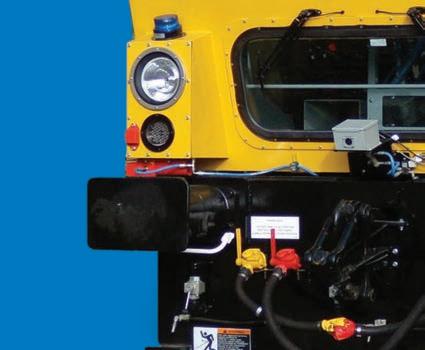

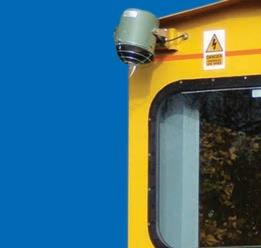

For over a half century, Harsco Rail has been a leader in rail grinding by creating optimal wheel and rail contact, while prolonging the lifespan of the track. The RGH20C Grinder can effectively grind switches, guarded curves, and road crossing, and is available in various gauges, including an adjustable gauge version.
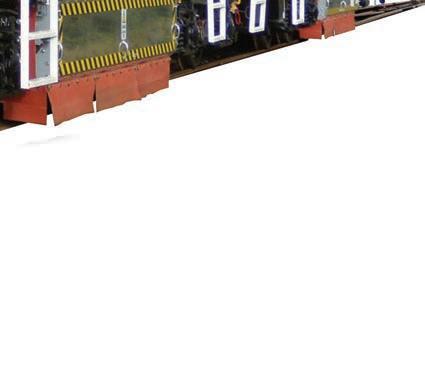




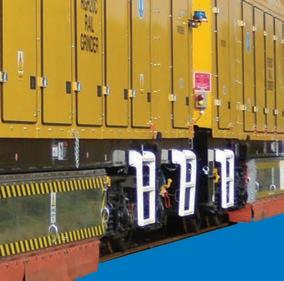

Progress Rail’s welding division offers a full suite of equipment that services the rail welding industry, and in North America it manufactures and provides service for both fixed-plant and mobile welding.

MILLING “Milling is a rotational cutting process and has many benefits of its own,” Dr. Richard Stock, Milling Technology Manager, Linsinger Austria, tells Railway Age. “In essence, the rail material is cut out of the rail surface via a spark- and dust-free process. The temperature on the rail surface elevates only slightly—300-320 degrees Celsius vs. if you’re doing a grated process, like with grinding, where the surface temperature can reach 800-900 degrees Celsius, causing some unwanted material transformation.”
“Milling allows for a variable metal removal capability, so we can remove very little material in one milling pass, like 0.1 mm,” Stock says. “Depending on the milling machine, you can remove up to 5 mm in one pass, measured from the highest point at the top of the rail. If you look at the gauge corner, depending on the position, you can even remove more. But then again, these are very general numbers. It depends on the specific condition that you have.
“With milling, you create a very precise profile over the relevant area. You can go from the field side to the gauging point or even further down if you need to do some gauge-widening. Milling also creates a very precise longitudinal profile. Any longitudinal deviation can be corrected to a high-quality level. The result is a high-quality surface.
“The chips that we generate are collected onboard the machine, which is equipped with a suction system that removes them from the rail and stores them on the machine. This adds environmental value.”
Stock adds that in a fire-sensitive environment, milling is still possible. Also, he says milling can extend the life of tracks by anywhere from seven to 10 years before more work is needed. “For example, when the brushfire season in Australia was at its peak, all the grinding trains had to stop, but our milling machines were still allowed to operate despite a total fire ban,” he says.
According to Stock a few things need to be considered with rail milling. One is that “for the rail profile that you generate, it’s fixed by the milling tool. One set of milling tools will create one specific rail profile, very precisely. If you need to change from one rail profile to the other you can just switch the milling tools, which can be done in less than 10 minutes. Main line rail milling machines are equipped with multiple tools per rail, allowing a profile change on the fly.”
As well, the passing speed is slower compared to other maintenance technology, “which can be something between 400m an hour up to 2km an hour, depending on machine size and how much and what you need to do,” Stock says. “It comes down to your specific defects: how much metal you need to remove, do you need to remove steeper defects, etc.”
WELDING Laser welding has been developed to repair surface defects of special trackwork, namely manganese steel components such as frogs and crossing diamonds, Holland LP, an engineering-based company servicing the railroad and related industries, tells Railway Age.
Keep your rails perfectly maintained with
LINSINGER high performance rail milling technology
Trust the Inventor www.linsinger.com

Linsinger Maschinenbau GmbH Dr. Linsinger Straße 23-24 4662 Steyrermühl Austria
Tel: +43 7613 8840 E-Mail: office@linsinger.com
Traditional repairs of manganese trackwork use wire or stick MIG welding. Thermite welding is used for joining rail and for internal head defects, so their applications are very different, Holland says. Laser welding has the potential to repair surface defects on rail but has not yet been proven. The advantage of laser welding over MIG welding is significantly lower heat input, which allows for faster repairs, at the same time protecting the base material from damage by excess heating. Laser welding is also robotically controlled, providing significantly better interpass layers for lower porosity. The result is not only faster repairs, but also longer-lasting repairs.
Flash butt welding (FBW) is another option. Used in many different applications because of its productivity and reliability in achieving a reliable welding result, “you basically use a metal pairing to make the weld,” Chuck Ewing, VP International Track and Track Services, Progress Rail, tells Railway Age. “We’re not introducing any external metals, any inserts, any powder, any mixture to make our weld. We’re heating the rail into an almost liquid state and then we’re forging the rail together. Its pros are speed: A FBW cycle is about three minute. Our closest competitor would be thermite welding, which is about a 15- to 20-minute process just to complete one weld; whereas you can complete basically 10 to 15 welds an hour depending on how fast you can get the weld. An FBW will last basically the lifetime of the rail.”
Progress Rail’s welding division offers a full suite of equipment that services the rail welding industry, and in North America it manufactures and provides service for both fixed-plant and mobile welding. And it provides equipment on a global scale as well.
Holland provides thermite, flash butt and laser welding solutions for customers. The company manufactures its own mobile FBW equipment with its proprietary Intelliweld™ control system that “has low-consumption weld capability, real-time weld monitoring, control and diagnostics, and real-time automated data collection, weld parameter

certification, charting and archiving.”
“Our FBW technology and trained welders provide the highest level of quality welds, demonstrating an unequaled quality performance of 5.5 sigma,” Holland says. “In addition to laser welding, Holland has developed a carbide, spark-free cutting saw that distresses the rail to eliminate torch cutting and eliminates the risk of fires from abrasive saw sparks.”
THE FUTURE Grinding, milling and welding’s future is ripe for further development. Holland notes that it is in the process of developing other new technologies aimed at improving safety and quality, and reducing operating costs for the railroad industry. Stock tells Railway Age that Linsinger will put a strong focus on the North American market in the coming year.
Harsco’s Bartz thinks the market “has been going in the direction of more and more measurement and more and more data. I think 20 years ago when you talked about rail grinders, you talked about
TRUCKS AND EQUIPMENT FOR ALL YOUR RAIL AND TRANSIT NEEDS.
RENTAL SYSTEMS, INC.
PHILADELPHIA 800.969.6200 DENVER 800.713.2677
horsepower, metal removal and its speed. All of those things are still very important. However, it isn’t all about just taking a whole bunch of metal off the rail. We can grind it off, but we can’t put it back on.”
Jacob Alexander, Director of OperationsMobile and Track Welding, Progress Rail, notes that his company is currently in the final stages of engineering and testing a 200-ton AC weld head that does not require an external puller. “We think there are a lot of benefits to having an external weld head that doesn’t require a puller. It reduces pinchpoints and takes the operator out of the line of fire between the two pieces of equipment.”
Orgo-Thermit says that its latest technological offering—DARI (Data Acquisition for Rail Infrastructure)—is “a first-of-itskind, cloud-based service used for storing weld data that is created from the use of digital products such as the SmartWeld Record, SmartWeld Jet and RailStraight Compact. The result of using these tools is a weld report that contains information about all aspects of the weld itself—its
Holland manufactures its own mobile FBW equipment with its proprietary Intelliweld™ control system.
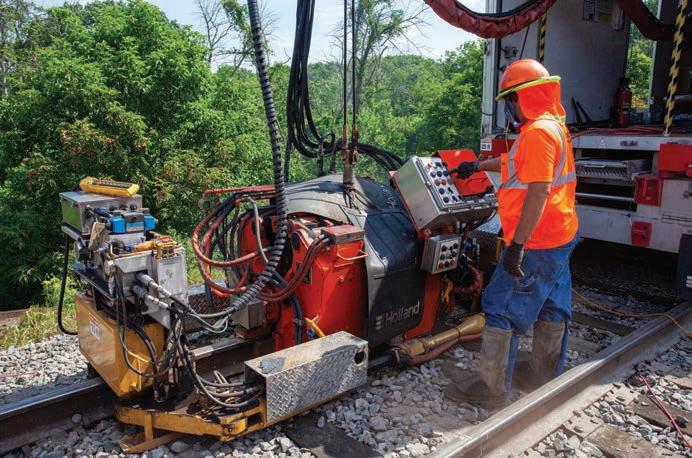
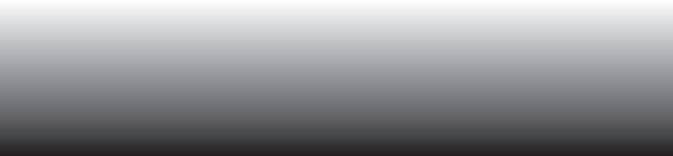
location and those who were involved with the rail maintenance. This information is stored within the cloud solution and visible to welding supervisors, project owners and anyone else who may have a vested interest in the outcome of the project … The database generates a map of the project so field welds can be easily identified, and respective information pertaining to each weld can be revisited in a matter of seconds.”
Put advanced communications and IoT to work for your railway
Make rail travel safer, more efficient and more dependable with networking, cybersecurity, IoT and analytics solutions that are trusted by mainline and metro operators worldwide.