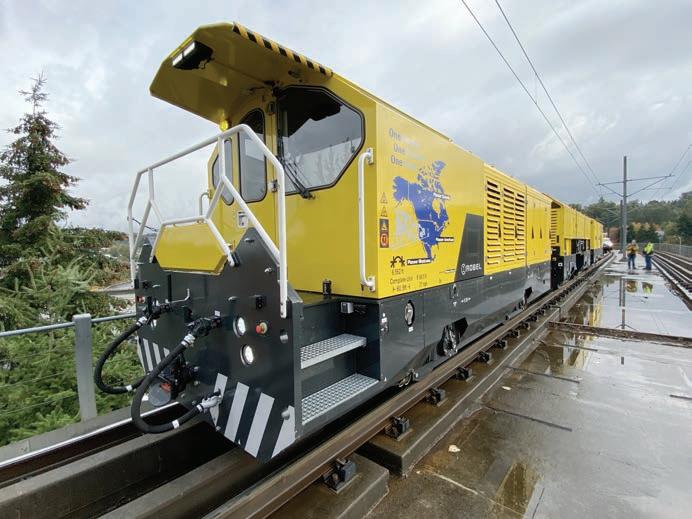
5 minute read
SPARKS FLY WHEN
Grinding and Milling Keeps Your Rails in Good Shape.
By: David C. Lester, Editor-in-Chief
While watching a rail grinder round a curve, particularly at night, it’s hard to imagine the scientific and precise process that goes into this work, with sparks lighting up the sky and surrounding area and smoke from the process filling the air. Yet the grinding vehicles, carrying different numbers of grinding stones, are performing such exacting work that if the grinding plan contains movements that will not result in the optimal grind, the rail will not perform as expected. And the main “performance” of rail is minimizing wear. A grinding plan is generally developed based on where the problem areas on the rail are, such as rolling contact fatigue, along with the wear pattern as trains roll along the tracks. For example, wear can be excessive in some areas while too little in others. The goal of grinding is to maintain the balance of wear to extend the life of the rail, as well as to remove small surface cracks and other anomalies that could cause a rail to crack and break in two, possibly causing a major derailment.
Software technology associated with rail grinding is becoming increasingly sophisticated. For example, Loram introduced Rail Pro® Infinity for production grinding. This software controls the position of grind stones used by Loram’s rail grinders, allowing for the precise removal of damaged or fatigued metal and shaping rails to desired profiles. Implementing the new software has improved conformity to desired rail profiles with less grinding effort, resulting in reduced energy and fuel consumption.
Loram also reports the company was recently recognized for these contributions to sustainability through recognition by the Norfolk Southern Thoroughbred Sustainability Partner Awards in January. Rail Pro Infinity enabled Loram to grind more miles for NS than ever before while achieving a 30% reduction in fuel consumption per finished mile. Moreover, in 2021, Loram customers using Rail Pro Infinity helped reduce over 225,000 gallons of fuel consumption, thereby reducing 2,530 tons of CO2 emissions.
Customers have also benefited from reduced rail head loss up to 15%.
Another way of maintaining track profiles is rail milling. While Europe uses milling, it’s a relative newcomer to the United States. The rail milling process is different from rail grinding. According to Interface , the Journal of Wheel/Rail Interaction, “rail milling is a non-abrasive cutting process where material is cut from the rail surface in the form of chips. A typical milling machine utilizes one to four cutting tools per rail, depending on the size of the machine. A subsequent polishing unit is used to create a smooth, high-quality surface. The removed chips are collected in the machine and can be recycled.”
Plasser American has recently introduced the rail milling machine Romill Urban 3 E3 (in collaboration with Robel) into the North American market. This globally first hybrid rail milling machine can operate for up to three hours on battery. The hybrid milling concept provides energy source flexibility – the batteries can be charged externally (if charging infrastructure is available) or can be quick-charged (<2h) through the integrated diesel generator (Tier 4 final) even while working.
The milling process is free of sparks and dust, and this Romill machine can operate completely emission-free. This is especially useful in closed environments like tunnels and stations. Operating electrically also significantly reduces noise, and carriers can use the machine on transit and freight systems.
Considering the massive size of grinding operations, it’s impressive that handoperated machines can be used in certain situations. According to Robel, the operator’s experience is paramount when using these machines. The result should be a high-quality grind with the lowest possible material removal and a profile restored true to form.
Robel offers lightweight and compact 13.45 rail profile grinders with gas or electric motors that can be used for all common rail types and switches with tool-free spindle adjustment and quicklock cup wheel change. Battery operation is also available for emission-sensitive urban areas or tunnels.
Due to its hybrid electric drive solution, the modular 13.49 high-frequency grinder is easy to handle, has low hand/arm vibrations, and creates a top surface pattern while producing significantly less exhaust gas, heat, and noise.
The 13.63 modular grinder works builtup welds on switch blades, frogs, stock and check rails and removes burrs from rail heads on frogs and in switches. It just takes the base frame and one of the eight grinding modules, swapped without tools, to perfectly reprofile the rail.
Rolling contact fatigue can be difficult to spot. The arrival of Eddy Current, a relatively new technology that’s been in testing for years, has made RCF easier to see, enabling grinding machines to grind just the right amount of rail to remove it.
Orgo-Thermit, a Goldshmidt company, uses a proprietary Eddy Current System and the Trackscan Mira with up to eight probes on each rail to provide a complete picture of the RCF in customer track optimize a grinding or milling program accordingly. The probes measure from the gauge corner, where most RCF originates, over the head of the rail to ensure a complete analysis.
This analysis enables the company to ensure that grinding focuses on the most affected areas of the railroad instead of a strategy where a complete system is ground. This saves the customer both money and track time and ensures the area with the most need receives attention.
Orgo-Thermit can grind track with a 12-stone Hi-Rail vehicle which offers strong performance for embedded track with its unique ability to get on and off track in less than a minute at crossings. The company’s trucks are equipped with a profile measurement to support grinding operation and guarantee the work achieves the required rail profile.
PortaCo, also a Goldschmidt company, offers a range of grinders to support all Maintenance-of-Way activities and has developed both lightweight and heavyweight profile grinders. The lightweight grinder has an ergonomically designed halo handle that allows the user to quickly maneuver the grinder around the rail. For the heavyweight grinder, the operator does not have to apply as much downward force to grind the rail, and it has an adjustable handle, so the operator is always upright when using it. Both grinders share hydraulic components, so even if different people on the same railroad prefer a different grinder, the spare parts are the same across both.
Vossloh o ers several options for pro ling rail. e VTM-compact is a highly exible, cost-e cient milling machine designed to t even the tightest of clearances. It will remove up to 2 mm in one pass, saving rails with serious defects and transverse pro le deviations from cost-intensive rail replacement. e technology is ideal for re-restricted areas with no re or dust hazards. e VTMcompact can be on track and ready for operation within a few minutes, maximizing even short track windows.
Vossloh also offers its proprietary High-Speed-Grinding technology that can prevent the onset of rolling contact fatigue, with operating speeds of over 40 mph without preparing the track.
Developing a maintenance strategy based on local conditions and individual circumstances of a specific network is very challenging. Vossloh has enhanced its rail maintenance machines into digital diagnostics vehicles to address this. Their SMART technology, which can be added to all existing machines, allows measurements to be taken during normal scheduled operations to determine the condition of rails and turnouts. This visually displays where, when, and which machining procedures are required.
Winter weather makes tough jobs even harder
By David C. Lester, Editor-in-Chief