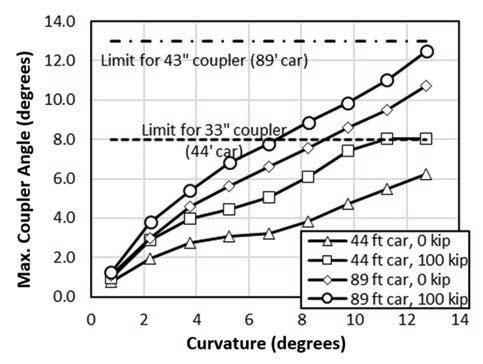
45 minute read
TTCI R&D
Revisiting study on computer program dealing with wheelrail forces
Alexander Keylin, Sr. Engineer II Benjamin Bakkum, Sr. Engineer II David Davis, Sr. Scientist (Retired) Transportation Technology Center, Inc. (TTCI)
Reverse curves are horizontal track curves that have opposite directions of curvature and are either located adjacent to each other or are separated by a very short section of tangent track. This type of track layout can lead to large coupler angles, especially when two coupled railcars have dissimilar lengths, long overhangs, or short couplers. When such railcars are under a large buff or draft load, this coupler angularity may cause high lateral forces at the wheel-rail interface, creating a risk of flange climb or rail rollover derailment.
Lengthening the tangent track section between the reverse curves decreases coupler angles and thus mitigates this problem. This can be challenging, especially when designing crossovers in rail yards, where curves are tight, space is at a premium, and tangent length is limited by track center spacing.
In 1976, the Association of American Railroads (AAR) used a computer program called Quasi-Static Lateral Train Stability (QLTS) to estimate wheel-rail forces in reverse curves and provided recommendations on minimum tangent lengths between reverse curves.1 Recently, TTCI was asked to revisit that study using modern computer simulation methods and to evaluate the American Railway Engineering and Maintenance-ofWay Association’s (AREMA) proposed new recommendations for minimum tangent lengths between reverse curves in rail yard crossovers (Table 1).
Comparison between results TTCI used multibody dynamics software NUCARS to simulate one of the scenarios from the early QLTS study: An empty 44-ft boxcar coupled between two empty 95-ft boxcars, negotiating 9° reverse curves under 30-kip buff load at a speed of 22 mph. The following three outputs were compared between the two studies:
• Maximum lateral angle between the coupler and the middle boxcar; • Maximum single wheel lateral-to-vertical (L/V) force ratio, which is used to estimate the risk of flange climb derailment; and • Maximum truck side L/V force ratio, which is used to estimate the risk of rail rollover.
NUCARS modeling of coupler movements, suspension elements’ deflections, wheel-rail forces, etc., is much more detailed than that of QLTS. In addition, QLTS assumes a quasi-static condition, while NUCARS calculates dynamic forces and displacements. Because of these differences, NUCARS showed coupler-to-car angles up to 35 percent lower, but single wheel L/V ratios up to 34 percent higher and truck side L/V ratios up to 30 percent higher than QLTS. Nevertheless, the trends in the two studies were similar: Increasing the tangent length between the reverse curves decreases coupler-to-car angles (up to a certain value) and generally decreases L/V ratios.
Minimum tangent lengths After confirming that the results of NUCARS simulations were generally consistent with the results of the QLTS study, TTCI then selected two of the worst-case railcar combinations from the QLTS study and simulated these railcars negotiating a series of reverse curves separated by the minimum tangent lengths recommended by AREMA.
Track geometry was simulated based on the numbers in Table 1. For example, a 10-ft tangent length was placed between two reverse curves whose degree of curvature was in the middle of the corresponding curvature range (2°15’) in the table for this tangent length. There were no spirals between the curves and the tangents. The simulated track geometry was nominal, i.e., no track alignment, surface, or cross-level deviations were simulated.
A total of 36 cases were simulated: nine combinations of reverse curves and tangent lengths; two combinations of car lengths (an 89-ft boxcar between 95-ft boxcars, and a 44-ft boxcar between 95-ft boxcars), and two load cases (no load versus 100-kip buff load). The 44-ft boxcar was equipped with 33-in. couplers, the 89-ft boxcar was equipped with
Degree of Reverse Curves Recommended Minimum Greater than Equal to Tangent Length (feet)
0° 1° 30ʹ′ 0
1° 30ʹ′ 3° 10
3° 4° 30ʹ′
4° 30ʹ′ 6° 20
30
6° 7° 30’
7° 30ʹ′ 9°
9° 10° 30ʹ′
10° 30ʹ′ 12°
12° 40
50
60
70
75
Table 1. Minimum recommended tangent lengths proposed by AREMA Committee 5 on Track Design.2
Figure 1. Maximum lateral coupler-to-car angles predicted by simulations.4 Figure 2. Maximum 50-millisecond single wheel L/V ratios predicted by simulations..4
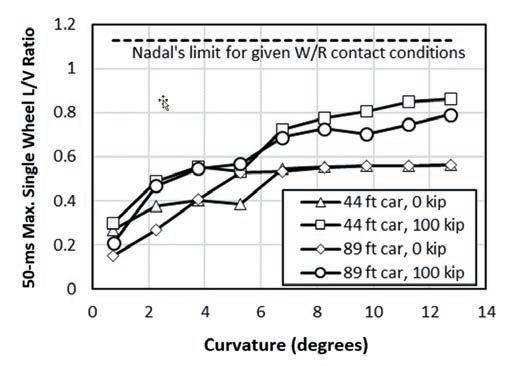
43-in. couplers, and the 95-ft boxcars were equipped with 60-in. couplers. All boxcars were empty. All simulations assumed a constant speed of 10 mph, unworn AAR-1B wheel profiles, AREMA 136-lb rail profiles, and dry rail conditions (wheel/rail friction coefficient of 0.5). The two couplers coupled together were modeled as a single body similar to a drawbar.
Figures 1-3 summarize the results of the 36 simulations. The outputs shown are for the middle boxcar (44 ft or 89 ft), because in nearly all cases it was the middle boxcar that showed the highest L/V ratios and the largest coupler angles.
Figure 1 shows the maximum angle between the coupler and the middle boxcar. The only cases in which the coupler reached its limiting angle3 were the cases in which a 44-ft boxcar negotiated reverse curves over 10° of curvature under a 100-kip buff load. In all other cases, coupler angle limits were not reached.
Figure 2 shows the maximum 50-millisecond single wheel L/V ratios5 simulated for the middle boxcar. In all simulated cases, these ratios stayed below Nadal’s limit, a widely used criterion for flange climb risk6, indicating that a flange climb derailment is unlikely.
Figure 3 shows the maximum 6-ft truck side L/V ratios simulated for the middle boxcar. It shows that when either the 44-ft boxcar or the 89-ft boxcar was subjected to 100-kip buff load, and when the reverse curves were over 8° of curvature, the maximum truck side L/V ratios exceeded 0.6 5,7 which indicates a risk of rail rollover.
Discussion Coupler angles in reverse curves depend on several factors, including the degree of curvature, tangent length between the curves, truck center spacing of the coupled railcars, their overhang lengths, and coupler lengths. The relationship between the coupler angles and the resulting wheel-rail forces is even more complex; factors like car weight, magnitude of buff or draft load, truck design, wheel and rail profiles, wheel/rail friction conditions, and track geometry irregularities all affect L/V ratios.
The simulations in this study modeled one of the potential worst-case scenarios: Empty cars with severely mismatched lengths and short couplers, under a high buff load (100 kips), in dry rail conditions. However, scenarios leading to even higher L/V ratios are conceivable: Shorter and lighter railcars exist; higher buff loads are possible; track alignment defects and/or asymmetrically worn wheels can further increase lateral wheel forces. A large parametric study would be needed to identify all conceivable scenarios.
Another limitation of this study is that it modeled simple reverse curves rather than crossovers. A crossover, in addition to reverse curves, has switch entry/exit angle, varying rail profiles at the switch rail and at the frog, and guardrails. Thus, coupler angles and L/V force ratios in a crossover would differ from those in two reverse curves of corresponding curvature.
In addition to maintaining minimum tangent lengths between reverse curves, proper train marshalling and handling methods are important for reducing the risk of derailments caused by longitudinal in-train forces.6
Conclusions The simulations have shown that under the simulated conditions flange climb derailment is unlikely but there is a risk of rail rollover for certain railcar length combinations under high buff loads due to high lateral wheel-rail forces. The results of these simulations should be used as first-order estimates of worst-case conditions in revenue service.
Additional information can be found in TTCI Technology Digest TD20-009.4
Acknowledgements The authors thank the AAR’s Strategic Research Initiative on Special Trackwork for financial support of this study. The authors also thank AREMA Committee 5 Subcommittee on Design Geometry for their technical input.
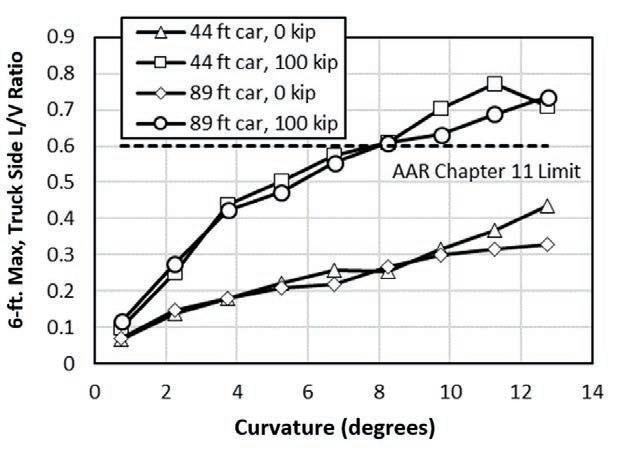
Figure 3. Maximum 6-ft truck side L/V ratios predicted by simulations.4
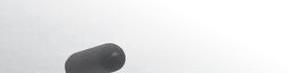
NEW

References 1. Association of American Railroads, internal document, 1976. 2. AREMA Manual for Railway Engineering, 2020 Edition, p. 5-3-25, Table 5-3-11: Recommended Minimum Tangent Lengths Between Reverse Curves for Yard Operations, AREMA, 2020. 3. Association of American Railroads, Manual of Standards and Recommended Practices, Section C, Part II, Chapter 2: General Data, §2.1.4: “Horizontal and Vertical Curves,” AAR. Washington, D.C., 2015. 4. Keylin, A., B. Bakkum, and D. Davis. “Evaluation of Tangent Distance between Reverse Curves in Yard Crossovers.” Technology Digest TD20-009, AAR/TTCI. Pueblo, Colo., June 2020. 5. Association of American Railroads, Manual of Standards and Recommended Practices, Section C, Part II, Chapter 11: Service-Worthiness Tests and Analyses for New Freight Cars, §11.5.2: Trackworthiness Criteria. AAR. Washington, D.C., 2015. 6. Wilson, N., H. Wu, A. Klopp, and A. Keylin, “Railway Vehicle Derailment and Prevention,” in: Handbook of Railway Vehicle Dynamics, Second Edition, ed. S. Iwnicki, CRC Press, 2020. 7. United States Code of Federal Regulations, Title 49, § 213.333: “Vehicle/Track Interaction Safety Limits.”
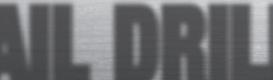
RAIL DRILL
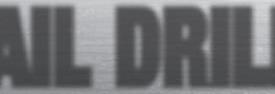

Two Speeds • Compact Size Drills Holes Fast

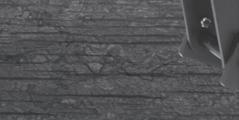
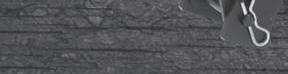
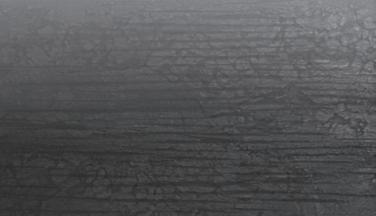
The NEW RB2SPD rail drill from Trak-Star is designed for drilling fast efficient holes. The drill incorporates a two speed gear box for using either the Carbide Tipped Twister Bits™ or the Black Twister Bits™. A more compact size makes the drill easy to get into tight spots. The RB2SPD includes an easy start 4 stroke Honda motor, high torque gearing, center balanced carrying handle, thru-the-tool pressurized coolant system, quill feed arbor, 10 point clamping and weighs only 49 lbs.
866-245-3745 www.trak-star.com



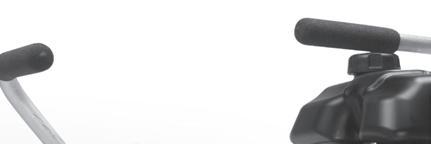
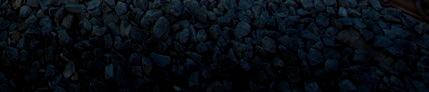


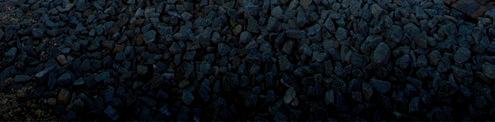


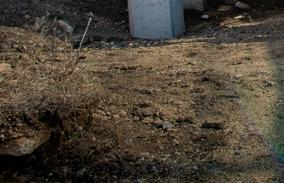
A THIRD WAY THROUGH
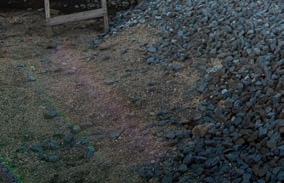

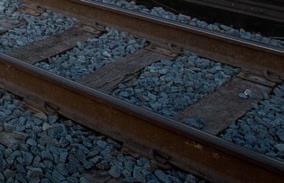

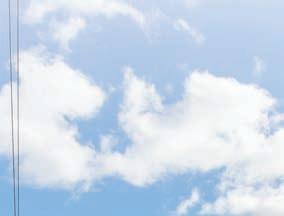
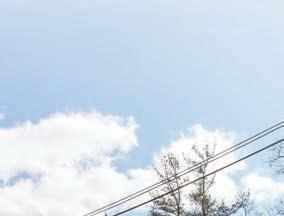
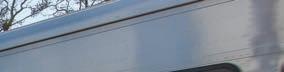
LIRR’s third track expansion project serves as a model for future work
By Bill Wilson, Editor-in-Chief
It’s not clear whether it got people to extra bar mitzvahs, weddings or 75th birthday parties, but the degree of togetherness was tighter than normal.
The productivity and comraderie achieved in the months before the Long Island Rail Road Mainline Expansion Project was even awarded was invaluable. When it came to managing through one of the worst global pandemics in modern world history, the established relationships made the building group unflappable.
“We said the only way we would be able to build something of this size ... a $2.5 billion project ... in four years pretty much of heavy construction is to really build a matrix organization to manage the job, and that’s what we have done,” Anthony Tufano, executive director of the Long Island Rail Road (LIRR) Mainline Expansion Project, told RT&S. “We worked closely before award with the contracting teams. We had pretty much four months of one-on-one meetings. So we hit the ground running once we awarded the job. So our team, their team, we knew the players, we aligned and really that prepared us for the unknown [the pandemic].”
The LIRR, considered the busiest commuter rail in the country, needed a more robust system to handle the morning and evening rush. The LIRR Expansion Project adds a third track, eliminates several at-grade crossings and includes bridge, drainage and utility work. How the project has been managed is the real story, one that the Metropolitan Transportation Authority (MTA) will use over and over again in future projects.
“The MTA’s goal is to really take the lessons learned from this project and start applying them to some other contracts we have across our agency,” Tom McGuinness, project executive for MTA Construction & Development, told RT&S.
Staying within the line Knowing each other was the easy part. Knowing how to fit in a track expansion without taking any right-of-way throughout the 9.8-mile project seemed like an impossible task. The original plan called for the takeover of a lot of property, much of it residential, but officials came up with a hard mandate for LIRR if it wanted to see the project come to life: Fit the third track in the 66-ft-wide right-of-way. The existing layout already consisted of two lines of track that were centered in the corridor, several stations, bridges and grade crossings.
“We really did our homework,” said McGuinness. “We then allowed designbuild firms to propose designs that would further simplify the alignment, which resulted in reducing the number of phases required for construction. We
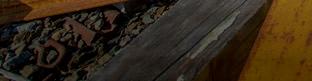
For the LIRR Expansion Project to become a reality, work had to be done within the existing right-of-way.
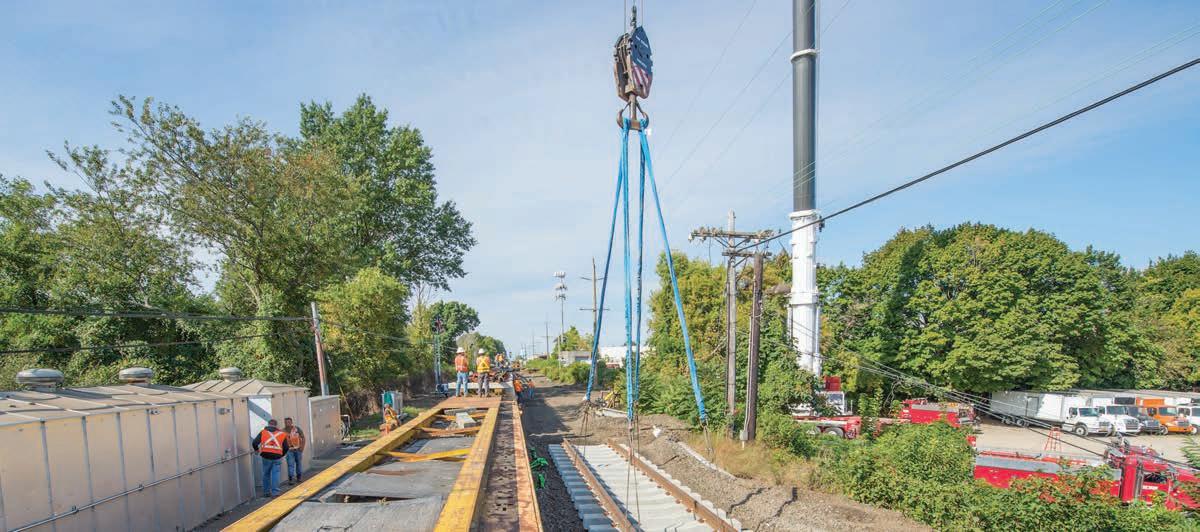

are currently 2.5 years in and are doing a great job.”
A design-build contract, which encourages innovative thinking during design, certainly helped. The track alignment had to be figured out first, and the first two years of the job involved realigning the existing two tracks both vertically and horizontally. Property layout forced crews to cut into existing slopes and construct retaining walls, and in many places activity took place adjacent to the backyards of residential lots. Two interlockings, Nassau 1 and Nassau 3, for the third track had to be installed, which required the track to be raised up and moved horizontally. Nassau 1 is located east of the Merillon Avenue station, and work began there about a year ago. Installation of Nassau 3 started in late 2020. Switches were installed, wiring for the signals and train control is currently under way and the cutover to the new interlocking will be complete this year. According to McGuinness, the interlockings divide the 9.8-mile section into three different blocks, and create a link between the two tracks to move trains back and forth. Mobile cranes were used during the installation, and when the right-of-way was pinched a gantry crane was used.
“Putting in the interlockings is huge because all of the utilities that have to control the interlockings and huts need to be spaced out and all of the existing infrastructure that was there needed to be moved so that it is not in the way of the third track,” said Tufano.
In a number of locations the track is being raised an average of 3.5 ft, with the highest elevation change at 4.5 ft.
Five stations are being reconstructed to bring them up to current standards and to add modern amenities. Platforms also need to be moved to allow space for the third track. Staging construction for the stations, which have remained open during construction, has been challenging. Temporary platforms have been built, and ballast and some rail for the third track have been placed. More production work will begin this spring, where more track will be installed and tied into existing track.
Retaining walls needed for the third track also have been set up, and at press time crews were working on putting in drainage and runoff underneath the track bed to prep for rail installation later in the year. Around the stations, much of the track work (sub-ballast, ballast, rail) is being placed by hand, but where there are long stretches a track-laying machine will be used placing 1,800-ft-long sections of continuous welded rail on top of concrete ties and the new track bed.
“Where it really gets complex is where you put in your interlockings. Putting in the special trackwork, and then bringing all the systems in place, the Positive Train Control [PTC] and the signal systems, to control those interlockings,” said Tufano.
Seven new substations and all the systems that go with them (communications, signals, PTC) also are being worked on right now.
Utilities for both the railroad and the grid are being installed throughout the length of the project. Pole placement has been going on for the last two years, and the process will continue until everything is complete in 2022. The 90-fthigh poles come in three sections and everything is set into a precast foundation. The poles are being set 20 ft deep into the ground. High-rail bucket truck cranes are being used to lift the poles into place where space is limited, while standard cranes are used when there

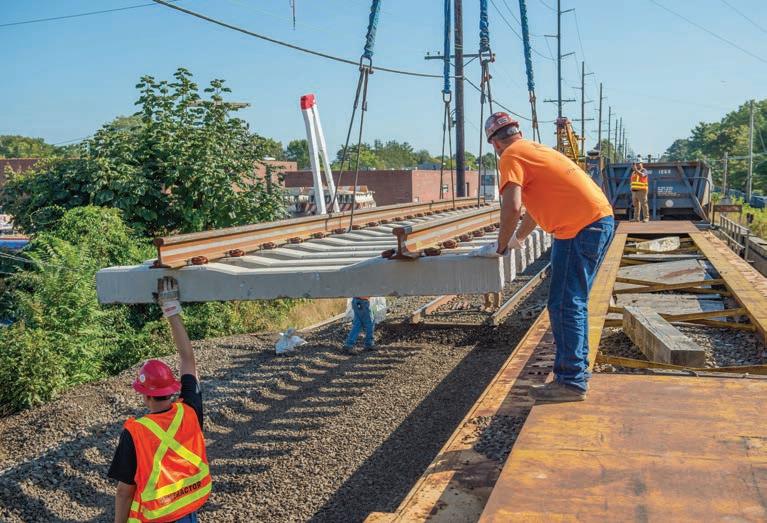
is more room. Some of the poles will be located on the opposite side of the tracks, and where feasible utilities were inserted underground.
A total of eight at-grade crossings are being eliminated and six transformed into under-grade crossings. Five of them have been changed already, with the sixth being worked on in 2021. Again, the challenges involved have been abundant, and when it comes to the grade crossings prime contractor 3rd Track Constructors, a consortium of Dragados USA, John P. Picone, Halmar International and CCA Civil, came up with an innovative method. It is essentially bridge construction involving a U-structure steel girder bridge that is built adjacent to the location of the existing grade crossing. The profile of the road is first excavated, with the track being supported by steel sheeting. During construction, trains are still running through the work area overhead while crews are building the bridge. The bottom of the bridge is a slab serving as the footing, while the top span is typically steel girders. Once the new bridge structure is constructed, a 48-hour weekend track closure takes place. The existing track is removed as well as up to 3,000 cu yd of soil supporting it. During the excavation, hydraulic jacks are put into place and the new structure is pushed into its finished alignment. Backfilling is then used for the abutment walls, and the precast concrete approach slabs for the railroad are laid down. Ballast comes next along with new rail, and by Monday morning the track is back in service.
“We pretty much sever the railroad for a few hundred feet over those weekends and rebuild it again,” said Tufano. “Both the contractor and the railroad forces work jointly to do this and it is pretty much a mad dash for 48 hours straight.”
The entire process is locked into a sixmonth road closure, and crews have not had any problems meeting the schedule.
Timetable timeliness The weekday LIRR train does not stop for anything. Some of the construction has been done with trains passing. However, there is a good amount of work that needs to take advantage of a track outage during off-peak times. Raising the existing two tracks and installing poles both have required a pause in service, and then there are the 48-hour outages for the undergrade crossings. Coordinating the work to fit into a track-outage window still takes an immense effort, and on this project it took on a new approach. By using timetables, the contractor is guaranteed access to the right-of-way for work. Track outage requests must be made six months in advance.
“So we give him guaranteed access to the right-of-way in a certain area every day, every night and every weekend,” explained Tufano. “[The contractor] plans his work accordingly with us, with our team, to see the best approach and give him the most access and production time.”
Tufano added that about 98 percent of requests have been filled for track outages.
In the past, work windows were requestbased, but there were no timetables and no guarantees.
For the 48-hour weekend rail closures, there are weeks and months of planning to make sure everything clicks. A risk analysis also is performed, and issues that could become problematic are identified and mitigation plans are developed and put into place.
“I do not think any one of our grade crossings have gone 100 percent the way it showed on paper,” said McGuinness. “But the ability to manage it throughout the weekend, have the mitigation ready to be implemented, and have all components of the team working together and communicating throughout the weekend helps us get there.”
All the preparations and advanced planning in the world cannot fend off a global pandemic, and when COVID19 took over the country those involved in the track expansion project made the right adjustments. New York State deemed the work essential, and work plans were tweaked to minimize contact between workers. If a worker does show any symptoms, the crew he or she is working with is quickly isolated.
The biggest difference-maker has been those established relationships that were formed well before the project started. The agency’s project management team and the contractor’s management team were both in the same office at the beginning, and organizational charts were aligned so decisions and conversations were taking place at the right level. When the pandemic took over, everyone was forced into their own home office. The process, however, has not missed a beat. Communication has been solid and turnaround times for submittals and documents continue to be efficient.
“It’s really one group out there,” said Tufano. “It’s not the contractor, the agency managing it, and the owner. It’s really one group tackling and managing the job, and that’s why we’re able to do what we’re doing on a daily basis both remote and when we are together in the field and in the office.”

By using timetables, the contractor is guaranteed access to the right-of-way for work.
STAY IN GEAR WITH RAIL GROUP NEWS
RAIL GROUP NEWS brings you a daily round-up of news stories from Railway Age, RT&S, and IRJ. This email newsletter offers North American and global news and analysis of the freight and passenger markets. From developments in rail technology, operations, and strategic planning to legislative issues and engineering news, we’ve got you covered.
From Railway Age, RT&S and IRJ RAIL GROUP NEWS

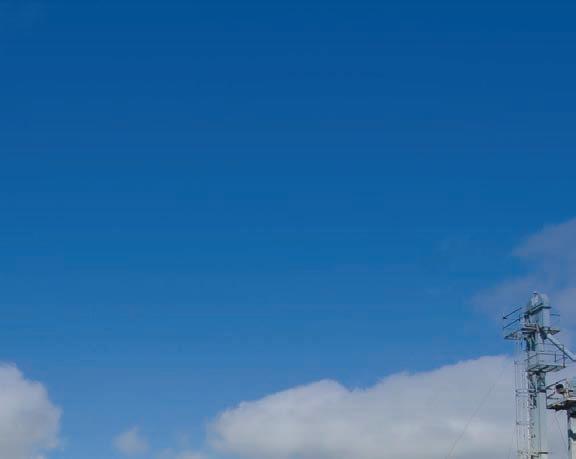
INDIANA’S
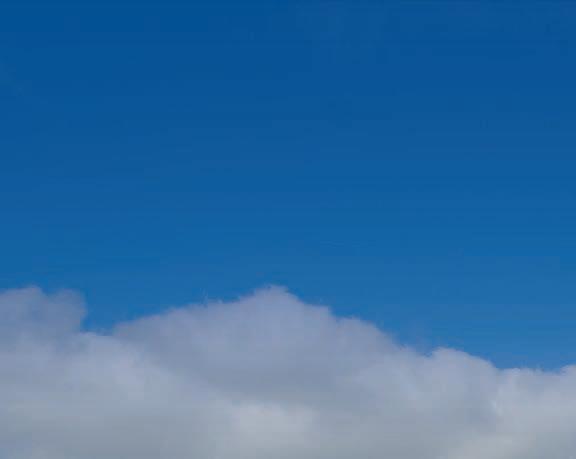
GEM OF A RAILROAD
How a successful regional railroad keeps its track in top shape

By David C. Lester, Managing Editor
The Indiana Rail Road (INRD), service, the railroad grew to today’s thriv- Special projects founded by Tom Hoback and ing company. The line runs south from While most track work on any railroad his associates in 1986, is a great Indianapolis, then turns west and travels focuses on routine maintenance, signifisuccess story around the prolif- through Linton, Ind., and continues west cant special projects occasionally arise. eration of short line and regional rail- to Newton, Ill. A line runs from Crane This work involves building new lines to roads brought about by the Staggers Act. to Terre Haute, then INRD has trackage serve new customers or complete a more To begin the INRD, Hoback purchased a dilapidated Illinois Central branch line that was in such bad shape, the Federal Railroad Administration decided to shut it down because the number of derailments nearly equaled the number of train movements. Through a continuous and robust focus on giving customers outstanding Photo Credit: Steve BarryROUND-UP of NEWS STORIES FROM: WAY AGE, RT&S and IRJ rights from Terre Haute to Chicago. INRD is a Class 2 railroad with a majority of its track maintained to Class 3 standards. Main line timetable speeds range from 25 mph to 40 mph. A few passing tracks have 25-mph timetable speeds. The railroad connects with all Class 1 roads except for Kansas City Southern. efficient routing to improve train movement flow. “One of the most significant line extensions constructed on the INRD was the extension of the Midland Subdivision by 5 miles to include the Bear Run Coal Mine near Dugger, Ind., completed in 2012,” Peter Ray, vice president of Engineering,
Installation of a new bridge over the White River in Elnora, Ind.
told RT&S.
Peabody owns the mine and load out which are accessible via the constructed Indiana Rail Road main line. This work included a main line track and two loops at the mine itself for the management of empties and loads in and out of the mine. A new interlocking at Dugger was built, which allows for the crossing of the INRD main lines for the Midland Subdivision and the Indianapolis Subdivision. This interlocking did not require the installation of a new crossing diamond.
“The railroad has recently completed some other significant changes,” said Ray. “For example, the removal of two crossing diamonds in Terre Haute, Ind., the Belt Junction Crossing Diamond and the Springhill Crossing Diamond.”
A change in operation patterns and the cooperative relationship INRD has with CSX required removing these two diamonds. The removal of these diamonds (in 2017 and 2019, respectively) eliminated the frequent maintenance work needed. Indeed, the railroad saved 3,000 personhours per year for welding and track section crews. In addition to saving the maintenance costs, the capital expenditure required to replace the diamonds every 25 years remains in the bank.
Removing these diamonds required adjacent trackwork and realignment of the main line in conjunction with CSX. The signal configurations within the interlocking were changed, as well. After all was said and done, CSX dispatch took over control of both interlockings, along with the maintenance of signals and communications within them. CSX assumed responsibility for maintaining the track at Belt Junction and Springhill Crossing.
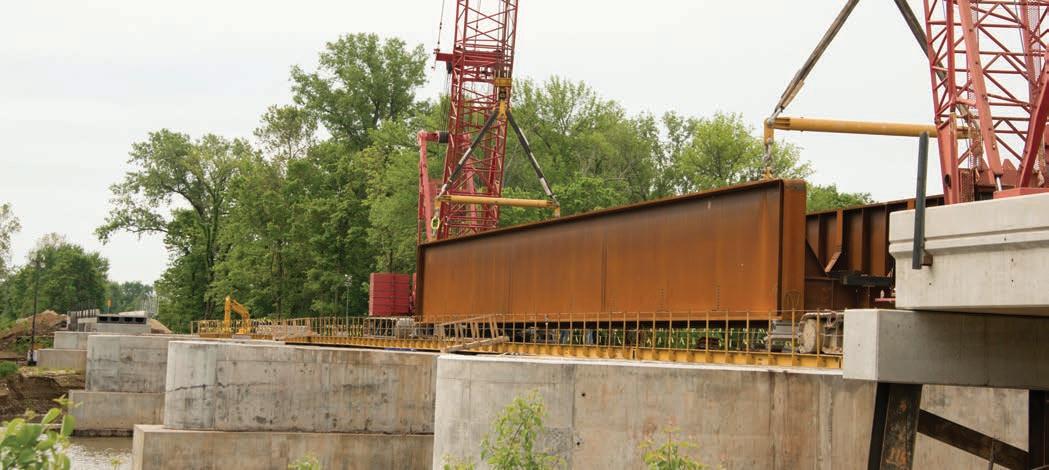
Routine maintenance All railroads, short lines and regionals must be diligent about keeping their track in shape, and INRD is no exception. A robust routine maintenance program helps eliminate surprises and unplanned repairs.
Ray pointed out that, “With active railroad lines, maintenance and rehabilitation are ongoing. Since 2009, INRD has replaced over 200,000 ties, including switch ties. Many of INRD rail/highway crossings have been totally renewed along these tie-installation sections from the ground up, including ballast, ties, rails, as well as the surface crossing materials.”
Others have been re-tied and received new ballast. INRD has been very aggressive in closing public and private crossings across the system, but this work is challenging.
Tie projects are completed with a combination of AREMA Grade V and industrial grade ties, as the railroad has not found concrete or composite ties to be affordable nor very useful in their climate and with their annual tonnage. Their equipment and workforce are best suited for wood ties, not only for maintenance by INRD Maintenance-of-Way personnel but also
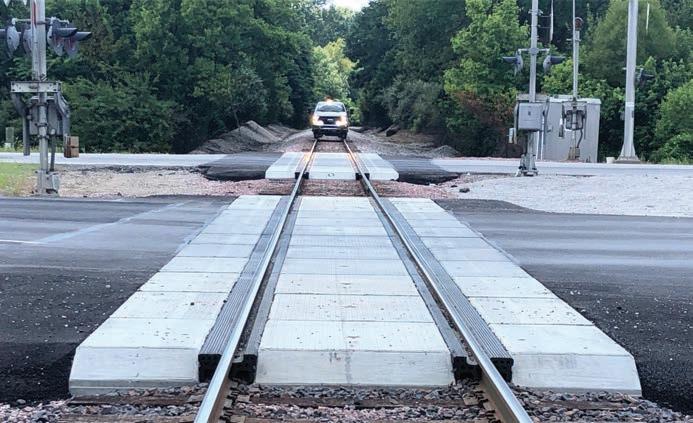
The Springhill Crossing Diamond in Terra Haute, Ind., before it was removed. Removal saved both maintenance and capital costs.

for installation by track gangs.
In addition to replacing ties, the INRD upgrades the main line jointed track to continuously welded rail (CWR). The programs are typically installing new rail or utilizing existing jointed rail by performing a cut-and-slide operation. These techniques both use electric flash butt welding processes that build a stronger joint than traditional thermit welds. In 2021, the railroad will install 6,200 ft of new 136-lb rail north of one of INRD’s longer trestles (Shuffle Creek Trestle), as well as a section on INRD’s recently acquired “Newton Connection,” eliminating the same length of jointed and CWR rails that have met their serviceable life.
The INRD has a unique undercutting program because it can’t contract out extensive undercutting gangs and ballast trains. Instead, it leases a Balfour Beatty smaller switch undercutter and use this as a main line undercutter, covering up to 1,000 ft per day and still having the track back in service for overnight train traffic. They utilize the undercutter with the Balfour Beatty two-person crew working alongside their MoW foremen and workers. INRD also performs the necessary surfacing to get the track back in service. INRD utilizes its fleet of ballast cars to replace the undercut spoiled ballast, and it has a limestone quarry on the line that makes repositioning cars relatively quick and predictable. In 2020, the railroad undercut nearly 17,000 ft of track.
“We have a unique ability to work inter-departmentally. For example, our engineering and Maintenance-of-Way departments work collectively with the operations and mechanical departments to get the ‘biggest bang for the buck’ and minimize track time so trains can run to generate the revenue necessary for our infrastructure work,” Bernie Guerrettaz, INRD’s general manager of Maintenanceof-Way, told RT&S.
Bridge repair/replacement The INRD has several bridges on the road and has been very aggressive with its bridge replacement program. Guerrettaz pointed out that “most of the structures replaced have been on the former Illinois Central portion of the line, which begins at Milepost 0.0 in Indianapolis and ends at Milepost 155.0 in Newton, Ill.”
In earlier years, coal was a large percentage of INRD’s haul at each end of this line, namely Indianapolis Power and Light and the former Dynegy plant in Newton. The wear and tear on the timber-framed structures carrying these loads for 30 years under INRD ownership and formerly with the Illinois Central became evident. Ray said, “the company handles the monitoring of bridge degradation with annual inspections of each railroad bridge structure.” Guerrettaz emphasized, “additionally, the INRD Maintenance-of-Way and engineering teams keep close eyes on them throughout the rest of the year.”
During the past 12 years, INRD has replaced over 25 bridges or completed bridge-to-culvert conversions. A major accomplishment of the bridge program is the bridge over the White River in Elnora, Ind., on INRD’s Chicago Subdivision,
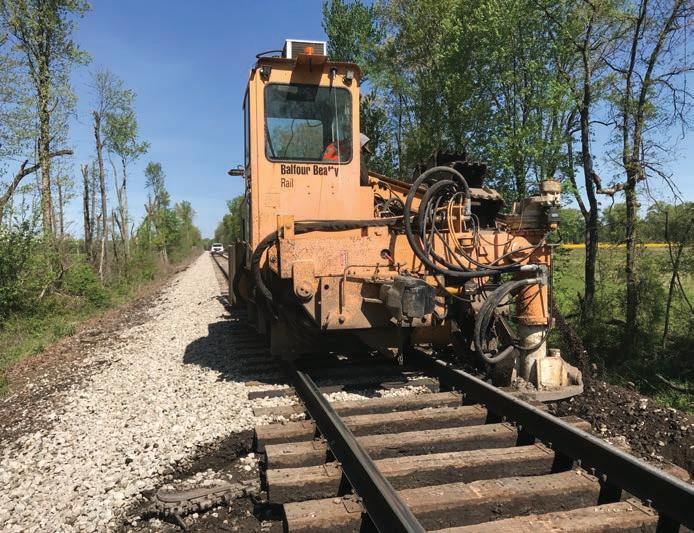
INRD leases a small switch undercutter to do work on the main line. This undercutter can cover up to 1,000 ft per day. completed in 2015. Besides the company’s direct investments, it also looks to partners that it serves and regional community leaders to generate support for investment in the road’s infrastructure. For the White River Bridge project, INRD worked with the Indiana Department of Transportation to receive funding through the TIGER grant process. The railroad has received letters of support from many of their customers and community leaders between Palestine, Ill., and Newton, Ill., to obtain funding from the FRA CRISI Grant Program to reconstruct and repair nine bridges of varying sophistication along this line. The bridge replacement started in 2020 with completion set for 2022.
While INRD doesn’t have the large capex budgets that Class 1s do, there is no shortage of due diligence in maintaining track in top shape, thereby maximizing the life of rails, ties, and ballast. Moreover, maintaining good track avoids costly derailments. The skilled leadership and crews are focused and enthusiastic, and carry on what Tom Hoback envisioned for the Indiana Rail Road.
SIGNAL INTERFERENCE-FREE TRACK MAINTENANCE IS HERE!
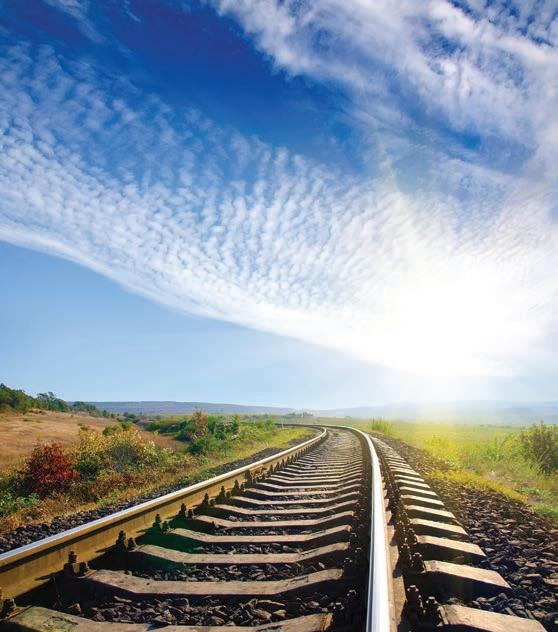
506-320 Track Jumper STRAIN RELIEFS NOW AVAILABLE!
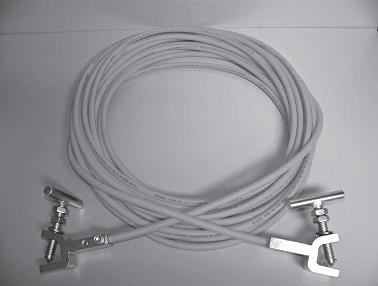
Our Track Jumpers facilitate track maintenance operations and keep crossing warning systems from being unnecessarily activated. Extended lengths (to 200 ft) allow the bypass of insulated joint and frog replacement work.
No. 6 AWG welding cable is highly conductive & fl exible
(even in extreme cold)
Choose S&C railroad grade base-of-rail or head-of-rail clamps Wire insulation available in black, red, safety orange or bright yellow
Reliable Tools for the Long Haul
7225 Duvan Dr. • Tinley Park, IL 60477 • Email: info@sandcco.com Ph (708) 444-4908 • Fax (708) 444-4962
GET THE INSIDE SCOOP ON & OFF THE TRACK
RAIL BRIEF
The Weekly RT&S Email Newsletter
Subscribe at: www.rtands.com/RailBrief
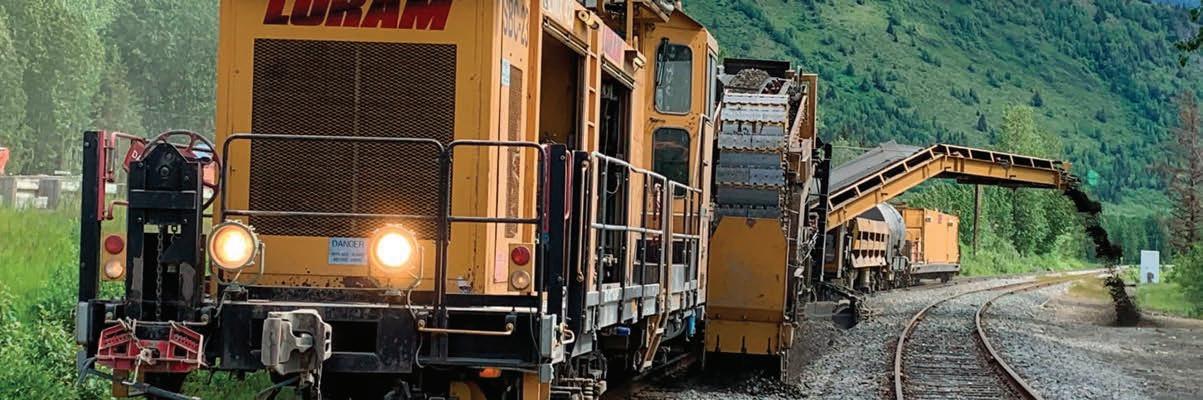
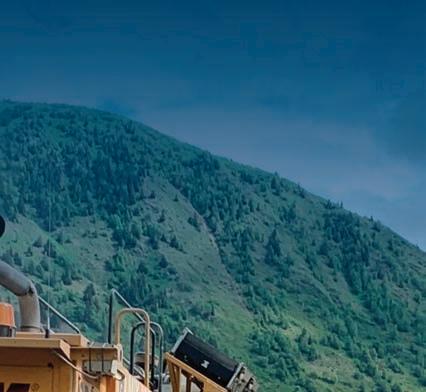
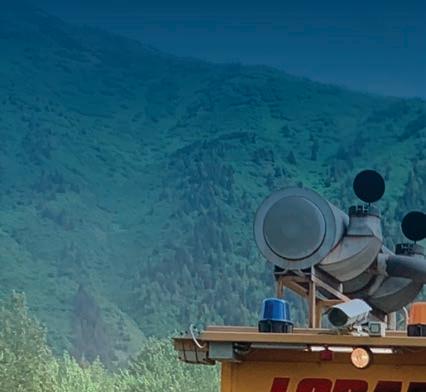
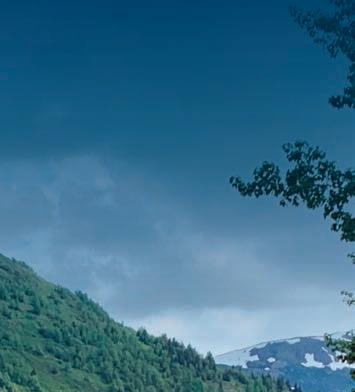
WHEN WILL THE GOOD REPLACE THE BAD?

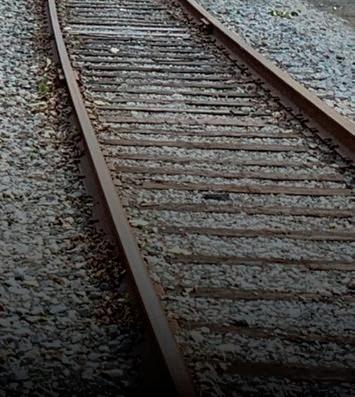
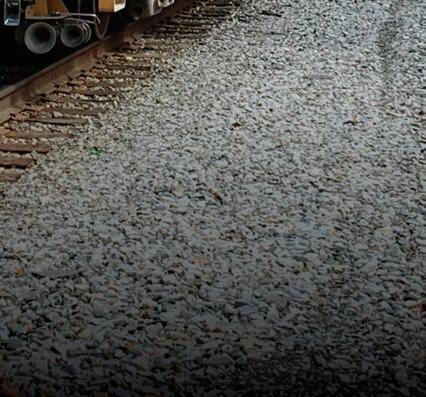
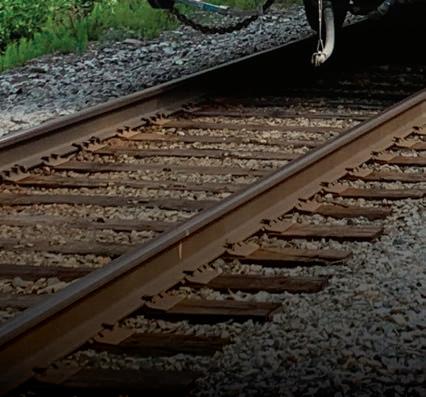
Like all other sectors, the ballast maintenance market faces challenges in 2021
By Bill Wilson, Editor-in-Chief
The ballast maintenance sector is known to take care of foul underlying conditions. In terms of the rail industry as a whole, 2020, which was spoiled by a global pandemic, was as bad as one could imagine.
Players in the ballast maintenance field remained vigilant, but the market as a whole was soft.
“The ballast maintenance market was down in 2020, but not to the extent originally expected at the outset of the pandemic,” Loram told RT&S. “Budgets were tightened and less work was performed than originally forecast.”
The pandemic still rages in business sectors across the country, and that includes the rail industry. There appears to be a carryover affect from 2020, and many are not sure if conditions will turn around this year.
“Total rail traffic is still sluggish compared to previous years and will impact the amount of degradation the track structure incurs,” said Loram. “It is anticipated that 2022 will see ballast maintenance back to prepandemic levels.”
Balfour Beatty agrees with the slow start to the new year due to the COVID-stricken economy, and also wants to get back to more traditional business practices.
“The loss of in-person social interaction continues to make doing business a little more difficult, but we continue to embrace the alternatives such as web-based conferences to bridge the gap,” Balfour Beatty told RT&S.
RCE Equipment Solutions The RCE Equipment Solutions Rail Division—previously Rail Construction Equipment Co.—has been busy enhancing the Railavator product line and under
cutter bars. RCE can supply the full range of models—from compact excavators to 35-metric-ton excavators—with under cutter bars ranging from 9 to 15 ft in size. By increasing these options, RCE customers can perform under cutting with all the RCE models of hi-rail or standard excavators. The largest machine, the 350G, has more hydraulic power to perform in hard conditions and the longer bar is beneficial for switch under cutting. Most recently, the smallest under cutter bar at 9 ft has been well received as an alternative to the larger machines and bars. For their contracting customers, the smaller machine and under cutter bar has made mobilization an easier task.
Herzog In 2019, the Midwest experienced substantial flooding particularly along the Missouri River and its tributaries, washing out stretches of nearby track and making the area difficult for many railroads to traverse and impassable for some. In such instances, the railroads deployed an arsenal of trackhoes, dump trucks, and personnel to rehabilitate the most severely affected areas. Track bed restoration efforts lasted for nearly a year before some lines were operable again.
As the snow melts and precipitation increases this spring, Herzog stands ready to respond to these unforeseen challenges and remains equipped for routine ballast maintenance. Railroads need equipment that can accelerate track bed reconstruction and ensure personnel are out of harm’s way. Enter Herzog’s Automated Conveyor Train (ACT)—the industry’s most versatile delivery solution for ballast placement. The ACT can unload its 30-car consist anywhere up to a 13° curve, including S-curves without any downtime. Its belt system and conveyor arm discharges ballast at a rate of 2,000 tons per hour up to 50 ft from track center. With this much speed and flexibility, the ACT can quickly stockpile ballast in areas of severe washouts or even fill the trackbed in areas of new construction. As ballast is off-loaded directly in front of the machine, the ACT’s automated plow can strike off material in the center of the track.
A significant benefit of the ACT is that all operations are controlled by a single Herzog operator within a climate-controlled cab. No additional workers are needed on the ground-adjusting flow gates, exposing them to harmful silica dust or adverse weather conditions. With the push of a button, the operator can quickly pause unloading, head to a new site, and resume unloading with no additional setup time.
Brandt For nearly three decades, Brandt’s Road Rail division has served the rail industry with a range of mobile material handling and Maintenance-of-Way equipment, from multi-purpose railcar movers and specialized on-track cranes to custom railcars or repair and maintenance equipment.
The company’s proven R4 Power Unit meets the most demanding expectations, helping to ensure that Class 1 rail operators are able to meet their revenue ton-mile objectives.
The R4 has been the No. 1 truck-based heavy-hauler in the rail industry for over 25 years, according to the company, consistently delivering the power needed to safely and efficiently move up to 16 fully loaded ballast cars on the mainline at speeds up to 25 mph (forward/reverse), optimizing ballast transportation and placement operations.
Utilizing both rail and road infrastructure, the R4 gets to the jobsite quickly and converts from road to rail in less than three minutes with a hi-rail system that is the most robust, reliable and safest system on the market today, minimizing track time and overall cost.
The unit delivers up to 600 hp and 50,000 lb of tractive effort (without additional

The Herzog ACT in action during the 2019 Midwest flooding.
Noise & vibration issues? We’ve got your fix
Our Under-Ballast Mats greatly reduce the maintenance requirements of your railway over its lifetime.
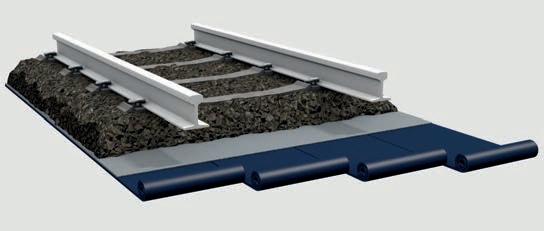
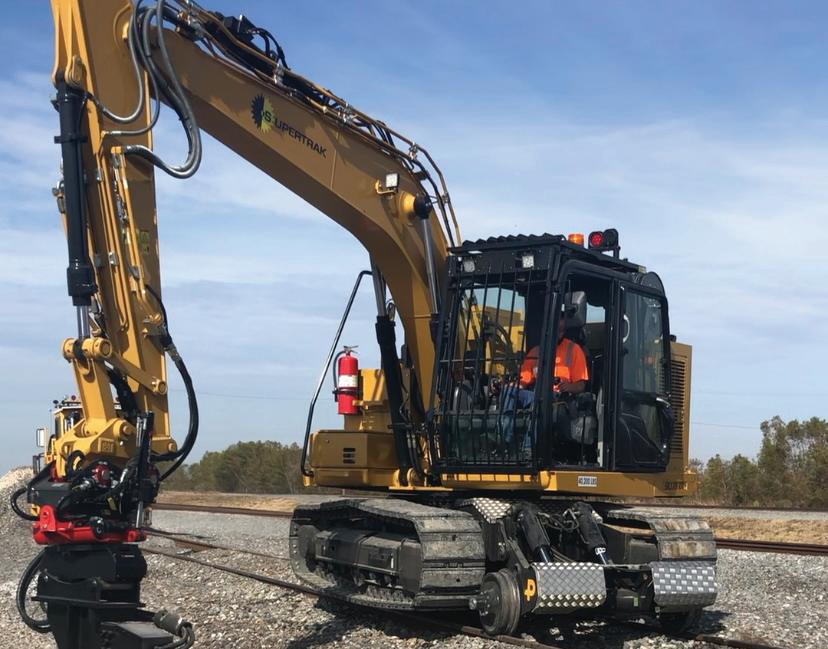
Industry-Rail Suppliers’ Supertrak SK170RR Hi-Rail Excavator. weight added to the deck) and can pull heavier loads up steeper grades at higher speeds without losing traction. The R4 achieves maximum stopping power with a 26C brake system ensuring positive control of the trailing railcars, in addition to its own independent brake that controls the rubber drive tires and steel rail wheels.
Brandt has designed the R4 to meet all FRA and DOT regulations (under 8 ft 6 in. wide and 40 ft long, inside of Plate C).
To maximize its effectiveness as a ballastcar mover, Brandt has employed a built-forpurpose compressed air system that meets the requirements for railcar brakes and pneumatic car controls for both bottom- or side-dump ballast cars. The use of a pivoting bolster box with swing arms and airride, shock-absorbed suspension ensures maximum stability and comfort on the rails while standard 28- to 70-tonne axles and 6 x 11 bearings ensure reliability and long life.
Industry-Railway Suppliers, Inc. Industry-Railway Suppliers, founded in 1966, is the distribution representative of
210016
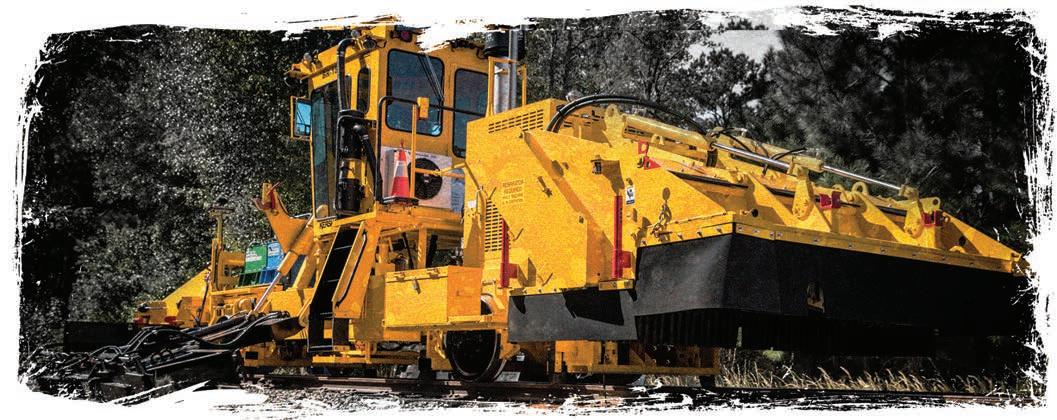
Every day, one Kershaw® Ballast Regulator sweeps through track maintenance operations. We keep you rolling.
Contact our team to find out how.
210008
Kershaw® Ballast Regulator 4600
+1-800-476-8769 • progressrail.com
@progressrail • @ Progress_Rail
180098
Supertrak machines, and a leading North America distributor of AREMA track tools, abrasives, heavy railroad equipment, work equipment wear parts and mechanical shop tools. Supertrak is a 30-year Cat-authorized OEM building custom machines for vegetation management, heavy-duty trenchers, custom utility trucks, cable retrieval equipment, and monorail work tractors. Supertrak specializes in small footprint yet high-performance, upfitted machines.
The Supertrak SK170RR Hi-Rail Excavator is based on a Cat 313 hi-rail platform. It has a single 170-hp engine, dedicated high flow with reversing fans and multi-functionality. The hi-rail is equipped with 4-wheel drive and 4-wheel brakes. The SK170RR maintains huge power in a small package with zero permit required for transportation due to its compact size, making it well suited for land clearing, vegetation management and ballast maintenance in remote places. This excavator meets national railroad safety specifications.
When the SK170RR is upfitted with the heavy-duty, hydraulic-powered SK10RR undercutter bar, it becomes a powerful ballast and mud regulator. This 10-ft bar is designed to quickly remove mud and fouled ballast from beneath the track with its replaceable teeth. The chain offers a variable controlled reverse for easy cleanout, and there also is a direct coupler mounted to use with or without a rotator option. The undercutter bar fits 8- to 15-ton class machines.
Loram Loram focuses on targeting ballast maintenance and remediation projects at the root cause of issues that are impacting track geometry and infrastructure life. This starts with making data-driven decisions to understand what underlying issues exist. GPR is used to identify how fouled ballast is and where the ballast layers are located below top of tie.
LiDAR is used to identify ditch locations and ballast deficiencies. With this data in hand, Loram works with customers to determine if there are internal or external drainage issues within a track section or if there are issues with the subgrade material that is supporting the track structure.
Once root cause issues are identified, Loram can tailor a ballast maintenance program that maximizes the customer’s budget and maintenance resources. After creating the plan, Loram brings industryleading equipment to execute ballast cleaning and remediation projects, excavate material from sensitive track locations, and clean/dig ditches.
With track maintenance windows at a premium, Loram’s customers expect equipment will be ready to work regardless of when it’s needed.
To meet this expectation, Loram’s shoulder ballast cleaners, ditchers, material-handling equipment, undercutters, and LRV specialty excavators consistently operate at or above 98 percent availability. To ensure equipment is ready to work whenever the railroad calls, Loram annually invests millions of dollars to maintain and renew its fleet of ballast equipment. This investment keeps Loram’s equipment operating at the same performance and reliability levels year over year to meet customer expectations.
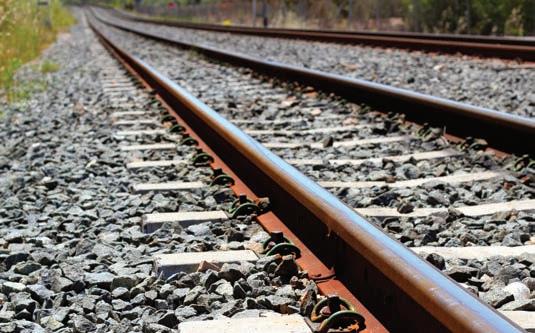
RAIL BALLAST
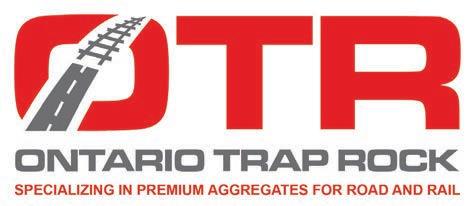
Serving the Ports within the Great Lakes
Illinois: Chicago
Ohio: Ashtabula • Cleveland • Toledo Ontario: Windsor • Sarnia • Port Colborne • Hamilton • Toronto • Owen Sound Michigan: Detroit • Saginaw • Cheboygan • Ludington • Muskegon • Benton Harbor
AREMA Compliant
Meets all North American railway applications and AREMA specifications
FRANK HURKMANS REGIONAL SALES MANAGER – CANADA (519) 709-4377 // fhurkmans@tomlinsongroup.com BILL SANDERS REGIONAL SALES MANAGER – US (219) 775-5783 // bsanders@tomlinsongroup.com
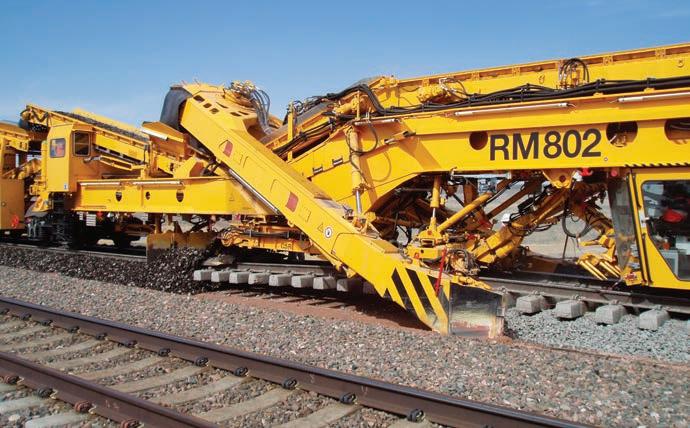
Plasser American’s high-capacity double screening unit, the RM802.
Knox Kershaw Inc. Knox Kershaw’s KBR 860 Ballast Regulator is a powerful track-dressing machine. It comes standard with a one-pass type plow, reversible side wings, and a broom attachment. The machine features a sturdy, comfortable cab with unique window placement for optimum visibility. The overall length and height is specifically designed to be shorter in order to facilitate transport to and from the work site.
The cab tilt feature and clean roof design promote safety and ease of maintenance by providing easy access to major machine components without having to go under or climb on top of the cab. Featured options of the 860 include a hydraulically driven AC with pressurizer, joystick controls on an ergonomic operator’s seat with easy access to all controls, tinted windows, additional rider seating and a 6-speed powershift transmission.
The KBR 925 Ballast Regulator, which was redesigned for 2019, is a robust machine designed for ballast work on all types of track. Quality visibility, especially in the wing areas, makes it the ideal machine for final profiling. The 925’s plow and wing work together to transfer ballast from shoulder to shoulder in one pass while leaving one shoulder profiled. The insulated broom box has excellent service life, and the standard reversing valve allows ballast to be swept away from switches and road crossings.

New features for the KBR925 include a Danfoss Plus One control system, frontmounted Visionaire hydraulically driven AC with high-capacity pressurization, and increased fuel and hydraulic fluid capacities.
The Plus One controller includes a 12-in. color touch screen monitor to display machine functions and diagnostics. When fully developed, the controller will aid operators in processes such as joystick functions, transmission shifting, wing deploy/ store and brooming speed control, as well as self diagnosis of performance issues. Clogged filters, inoperable coils or wiring, fluid pressure warnings, engine diagnostics and on-screen trouble-shooting guides will enable operators and mechanics to diagnose issues and quickly resolve them.
The new design increased fuel tank capacity by placing dual tanks on either side of the cab and moving the hydraulic tank to the front of the machine for added weight and balance. Side access steps are configured for easy and safe access to the cab and all maintenance points are easily accessible from the ground.
All of these new features improve productivity by increasing capacity and decreasing machine down time.
Plasser American Ballast maintenance is a key factor in maintaining long-lasting track quality. Plasser understands this very well and offers several products and services to help the customer achieve the required results. These areas of ballast maintenance include ballast undercutting/cleaning, shoulder cleaning, subgrade renewal and ballast management.
Clean ballast is extremely important to maintain track geometry. Plasser offers several machines for cleaning ballast. The workhorse of this fleet of machines is the RM80 and RM80-800, which undercuts and cleans plain track, as well as switches. High-capacity double screening units such as the RM2003 and the RM802 are available. In addition, Plasser also offers shoulder ballast cleaning machines.
The BDS100/200 Ballast Distribution System is the ideal machine to accompany high-speed multiple tie tampers such as the 09-3X and 2X Dynacat tampers or used alone to reposition existing ballast along the right-of-way using existing valuable assets. The machines are equipped with plows to profile the ballast, hopper, and conveyors to distribute ballast and double brooms to sweep up and store excess ballast, with all work performed in a single pass. MFS Hopper/Conveyor cars can be added for additional ballast storage.
Plasser’s PBR2005 Ballast Profiling machine has the ability to plow, profile and broom in one pass. The unique design of the shoulder plows allow the machine to reach out and pull in ballast, which was previously beyond the reach of conventional ballast regulators.
Vancer With Vancer’s continued focus on developing solutions to improve customer Maintenance-of-Way operations, Vancer developed the patented Ballast Cribber attachment. The Vancer Ballast Cribber is designed to efficiently remove compacted

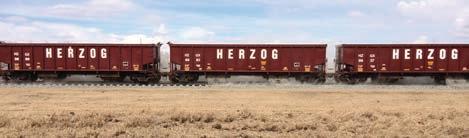
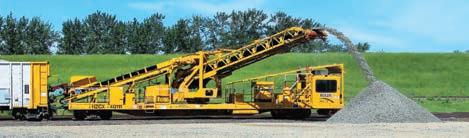

Mitchell Rail Gear’s Ballast Regulator.
and cemented ballast in a single swipe—six times faster than traditional methods so operations can quickly spot-treat sections of track that need work.
The Ballast Cribber is ideal for immediate spot repair in any location when paired with a Vancer hi-rail machine. The Cribber’s versatility includes removable buckets for different crib widths allowing for ease of replacement, and adjustable rail clamp heights for different rail profiles. Built-in rail wheels keep you aligned as you move to the next crib.
In addition to speed and versatility, the Vancer Cribber attachment, with a weight of 4,600 lb and a clearing depth under rail of 12 in., promotes safety. Rail clamps that hold operators to the rail while cribbing keep the operator safe. Service-wise, the Cribber has been designed with heavy-duty cylinders for durability and long life. Removable teeth allow for easy replacement.
Mitchell Rail Gear There are two separate markets for ballast maintenance that require two different solutions. The first is high production, which requires a single purpose dictated ballast regulator machine. The second is for spot maintenance or lower production, which requires a Ballast Regulator Attachment system that can be installed on an excavator or loader backhoe.
The Ballast Regulator attachment has some flexibility whereas it can be mounted on the loader backhoe front loader arms of a backhoe or on the backhoe boom. The
The Railway Educational Bureau Track Resources
The Art and Science of Rail Grinding
Rail grinding saves millions of dollars every year! The Art and Science of Rail Grinding is the first book dedicated exclusively to the subject.
BKGRIND Rail Grinding
$145.00
Railway Geotechnics
Railway Geotechnics covers track, track substructure, load environment, materials, mechanics, design, construction, measurements, and management. It is written primarily for professionals and graduate students. BKGEOTECH Railway Geotechnics
$220.00*
The Track Data Handbook
Reprinted by popular demand, this book is a valuable reference for roadmasters, track supervisors, track foreman, surveyors and others involved in the planning and execution of track maintenance and construction work. Fold-out diagrams. Softcover. 301 pages.
BKTDH Track Data Handbook
$48.50
The Railway Educational Bureau
Your Guide to Railway Signals
Your Guide to Railway Signals is an excellent guide for training signal personnel especially railway cross-function managers, supervisors, and support personnel. High-quality graphics and diagrams have been used throughout. Complies with all standards and commonly used practices.
BKYGRS Your Guide to Railway Signals
$99.95
Design and Construction of Modern Steel Railway Bridges, Second Edition
This new edition encompasses current design methods used for steel railway bridges in both SI and Imperial (US Customary) units. It discusses the planning of railway bridges and the appropriate types of bridges based on planning considerations. BKDMSRB2 Design & Const. of Mod. Railway Bridges $169.95*
The Railroad What it is, What it does
The fifth edition of The Railroad: What It Is, What it Does is even more valuable than before. Inside you’ll find a comprehensive look at how today’s railroads function—from equipment to procedures and marketing to maintenance. BKRRNN What it is What it does
$46.95
800-228-9670
Add Shipping & Handling if your merchandise subtotal is: U.S.A. CAN U.S.A. CAN 25.01 - 50.00 12.00 20.05 100.01 - 150.00 18.25 42.50 50.01 - 75.00 13.50 25.05 150.01 - 200.00 21.40 56.75 75.01 -100.00 16.06 32.70 200.01 - 300.00 26.00 70.40 Orders over $300, call for shipping
Ballast Regulator attachment mounted on the front of a loader backhoe has a fixed width the same as a single-purpose dictated ballast regulator machine that also can be configured for third-rail transit applications.
The backhoe-mounted Ballast Regulator attachment can tilt side to side for contouring the ballast outside to the ties. A loader backhoe can be equipped with both a front mount and a boom mount to reduce ballast maintenance time and increase efficiency.
Balfour Beatty Balfour Beatty continues to invest in the advancement and integration of ballast and track bed inspection solutions, which includes Zetica’s Advanced Rail Radar autonomous multichannel high-speed GPR system which now includes an integrated track bed surface imaging system for a holistic view of subsurface track bed condition linked to visible surface issues, e.g., mudspots. Integration of this data with synchronously measured track geometry provides unique insights into the root causes of failures and deteriorating track conditions. This cost-effective approach helps to optimize track bed maintenance planning and reduces the commercial and safety risks associated with slow orders and derailments.
When placed in combination with Balfour Beatty’s autonomous track geometry measurement system TrueTrak and the automated vision-based track inspection system OmniVision, a comprehensive track inspection solution can be provided.
Automated data capture of above- and below-ground data streams allows integrated exception reports to be generated in near real time based on external trigger events such as a track geometry exception or based on pre-programmed location waypoints.
Independent studies also have shown that GPR is sensitive to measuring ballast quality degradation from the point of renewed ballast. The benefit of monitoring the rate of change of ballast fouling levels (BFI and FDL) using recently cleaned track as a reference would be to plan the timing of appropriate maintenance interventions and to predict the remaining life in ballast material using a combination of track geometry, vision and ballast-fouling metrics.
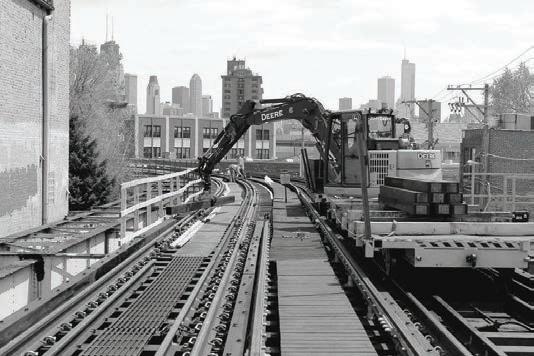
Miner Last year proved to be a very active year for the ballast maintenance market for Miner. A major passenger railroad built 375 new ballast cars and retrofitted over 40 more cars, each outfitted with Miner’s innovative new solar-powered, stand-alone AggreGate ballast outlet gates, featuring new LED work lighting systems. These innovative solarpowered, battery-operated LED lights attach to the undercarriage and enable safer, more efficient nighttime ballasting operations.
Miner is always working with the railroads and track crews to continuously improve ballast unloading and efficiency. They are asking for safe, durable, maintenance-free systems that can be applied to new or existing cars. The Miner AggreGate provides all that, and can effectively ballast inside, outside or both sides of the rail simultaneously. Large guillotine door openings stop ballast flow with minimum effort. Easy-to-operate toggle linkage systems and tapered doors improve ballast shutoff at switches, crossovers and bridges.
Plus, Miner’s stand-alone, solar-powered AggreGate enables independent operation of the car from anywhere within the ballast train. No more need for grouping manual and automatic cars, since each gate and car can ultimately be operated without connection to another car for power. The solar-powered system is battery operated for stand-alone operation.
An Innovative Approach to Railroad Maintenance Equipment
Lower Operating and Maintenance Costs with the World Wide Support of the John Deere Dealer Network PURCHASE—RENT—LEASE
Customizable and Emissions Compliant
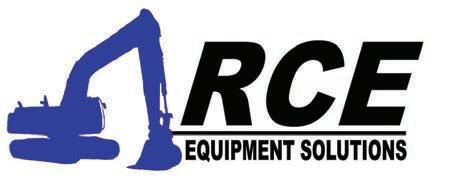
866-472-4570
High Rail and On Track Equipment NEW SERIES RAILAVATORS— 210G, 245G, 250G Models Excavators—Swing Loaders—Carts Railavators—Brushcutters—Rail Clips Third Rail Applications—Mag Cranes—Tie Cranes All-Makes High Rail Gear
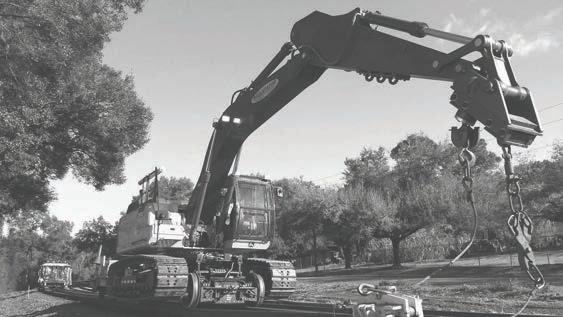