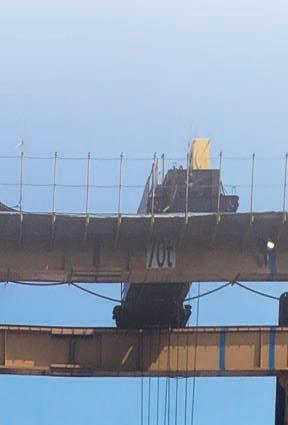
3 minute read
Business Solutions

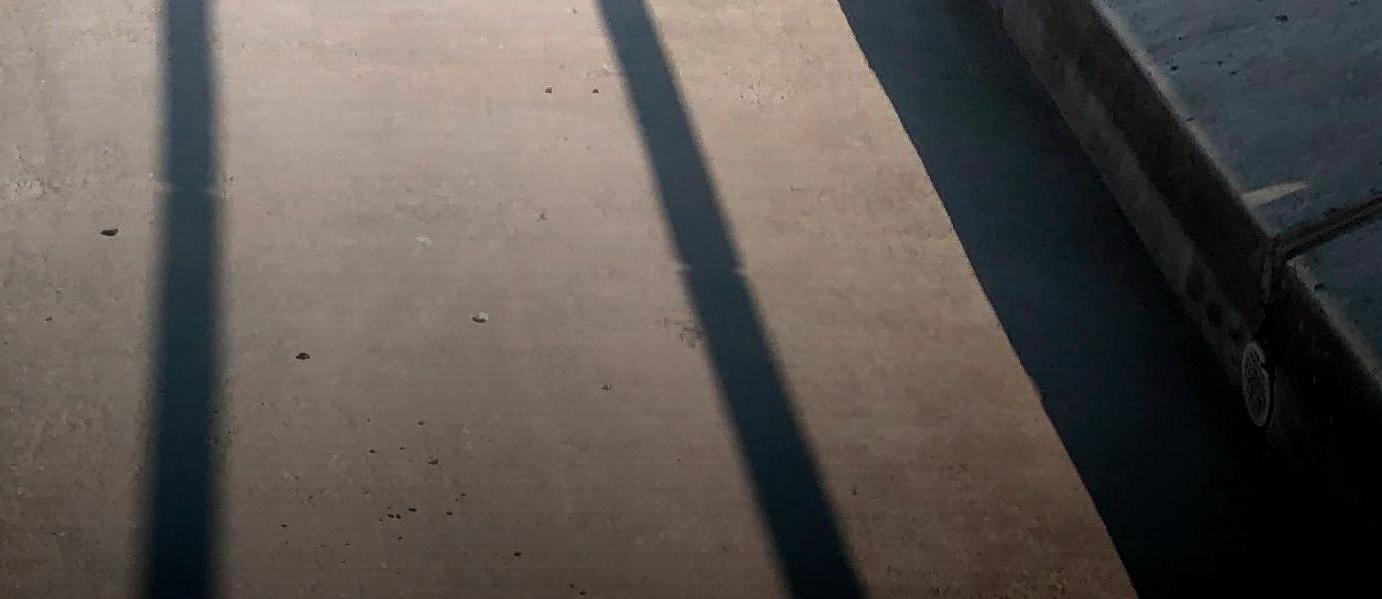
WATERPROOFING
A PRECAST CONCRETE RAIL BRIDGE IN LOUISIANA



Last year Canadian National replaced a wooden trestle bridge with a precast concrete bridge in the state of Louisiana.
The scope of the waterproofing work was as follows: • Seal longitudinal and transverse
joints in the precast concrete panels; • Fill longitudinal joint between panels to avoid collection of moisture and debris; and • Waterproof the bridge deck to meet owner expectations without a completely lined monolithic coating system.
The scope was chosen because the proposed systems offered a very fast return to service and allowed for making up time in the midst of a hurricane season in Louisiana, which was fully expected to impact the project’s schedule.
A pre-formed geo-membrane utilizing P480 and a woven textile fabric was placed over the peel-and-stick and tacked into place.
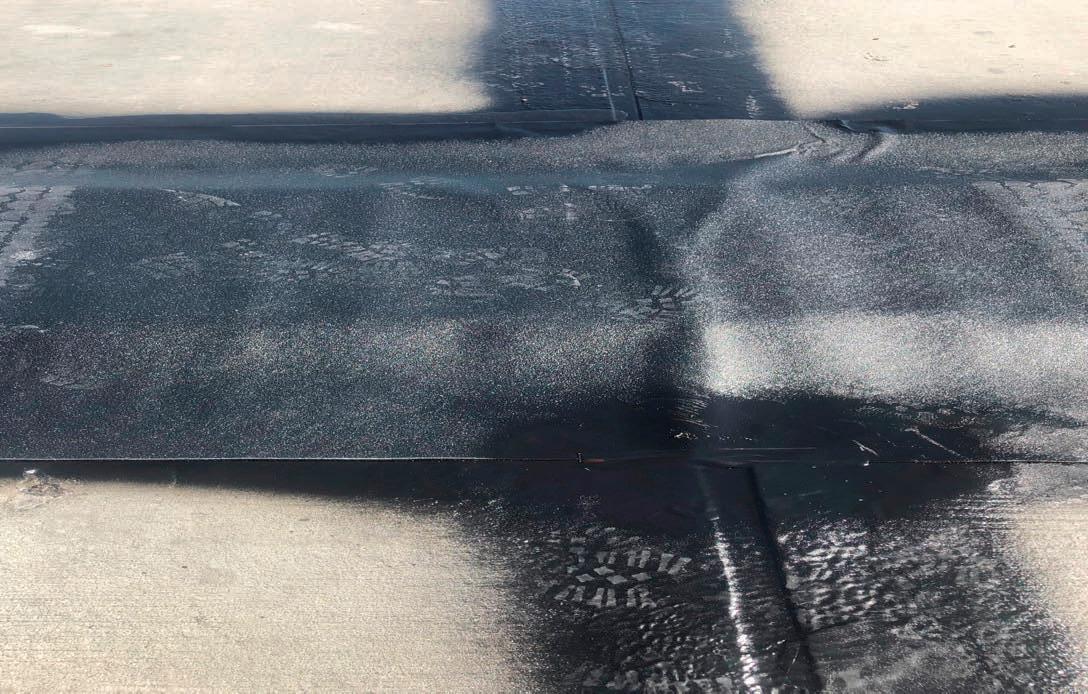
The concrete deck was pressurewashed to remove all laitance, debris and oils and grease. The longitudinal joint was primed with PolyPrime LV, a twocomponent urethane primer that can be sprayed or roller applied. PolyPrime LV sets within 20 minutes and has an eighthour open time. Using the WVCO Railroad Solutions meter for a clean, efficient and labor-saving method, FastPatch 5000, a two-component polyurethane with a high compressive strength (to match the precast panels) and a low tensile strength to offer movement capability between the two rigid panels, was installed. By filling this mile long, 3-in. x 3-in. channel, the ingress of debris and water was avoided. FastPatch 5000 cures within 10 minutes and so was not impacted by sudden rain squalls that were always a threat on this project. This process was created by the contractor, Protective Coatings, with the manufacturer, WVCO Railroad Solutions, and is known as a Weld Joint procedure. Numerous spalls in the precast panels that were adjacent to the joints (typical corner breaks) were instantly repaired using the same FastPatch 5000 material. P480, 100% solids and VOC-free polyurea, was sprayed over the FastPatchfilled channel with an overlap of 1 ft on either side of the channel, providing a completely waterproof barrier over the seam between the concrete panels. P480 gels within seconds and cures within a couple of minutes allowing almost instantaneous return to service and the re-entry of other trades. P480 and FastPatch polyurethanes are compatible chemistries.
The transverse joints were treated by applying a peel-and-stick membrane over the steel cover plates to provide a base that the waterproofing system would not adhere to, thus creating a slipsheet that would continue to allow for extreme movement without compromising the expansion joint design. A preformed geo-membrane utilizing P480 and a woven textile fabric was placed over the peel-and-stick and tacked into place onto the surrounding concrete using P480. The P480 polyurea embedded the membrane into place forming another waterproof protective barrier. The advantage of using pre-formed membranes is that they are easier to manipulate into place and provide a consistent thickness in the vulnerable joint areas. No protection board is necessary when using P480 at 120 mls thickness as it is ballast resistant.
Normally specifications call for completely coating the concrete bridge deck. This modified specification highlights the areas of the maximum potential weakness that are often left unaddressed. The contractor used both attention to detail and creative detailing to overcome present and potentially future challenges ensuring that the bridge deck is waterproofed where it matters most.
In-depth discussions about the products, systems and procedures were held between the engineers, contractors and the manufacturer to reach a comfort zone with the proposed applications.
Full details and pictures can be viewed at www.fastpatchsystems.com.