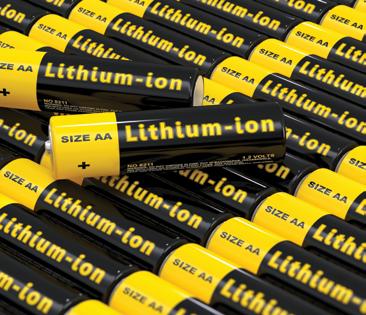
8 minute read
Uni R&D that’s revolutionising mine waste treatment
WASTE NOT
WANT NOT
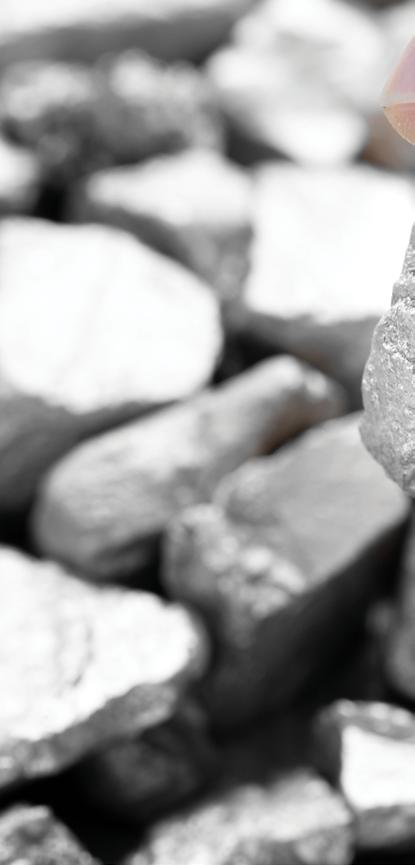
Supplying the world with critical minerals is going to require innovation in re-mining old deposits.
As the world focuses on critical minerals supply, Australian university scientists are working with industry to ‘re-mine’ deposits previously passed over as difficult or expensive to extract. Mining these deposits ethically and sustainably will open the pathway to a sovereign supply of minerals, and potentially a mine-to-factory process that could transform our manufacturing capability.
It’s a tricky path to manoeuvre, however, one that requires investment at all stages, as well as collaboration between science and industry.
Dr Andrew Tong is a metallurgist and executive manager at Cobalt Blue, which aims to be one of the world’s largest ethical suppliers of cobalt, a critical mineral used in batteries. A University of Sydney science graduate with a PhD in chemistry, Tong holds several patents in mineral extraction methods that separate precious metals from pyrite and simultaneously create a stable, elemental sulphur that can be used in farming.
He says collaboration among the university sector, research institutions, government and private enterprise has never been more important if we want to build a viable renewable tech and battery industry.
“We work with University of NSW and ANSTO through a Cooperative Research Centre (CRC) project. We also work with Curtin University and QUT as part of the Future Batteries Industry CRC.
“My own personal background includes a PhD at the University of Sydney. So, most of my industry career has had some links back to a university at some point. They’re a great source of graduates, training and facilities.”
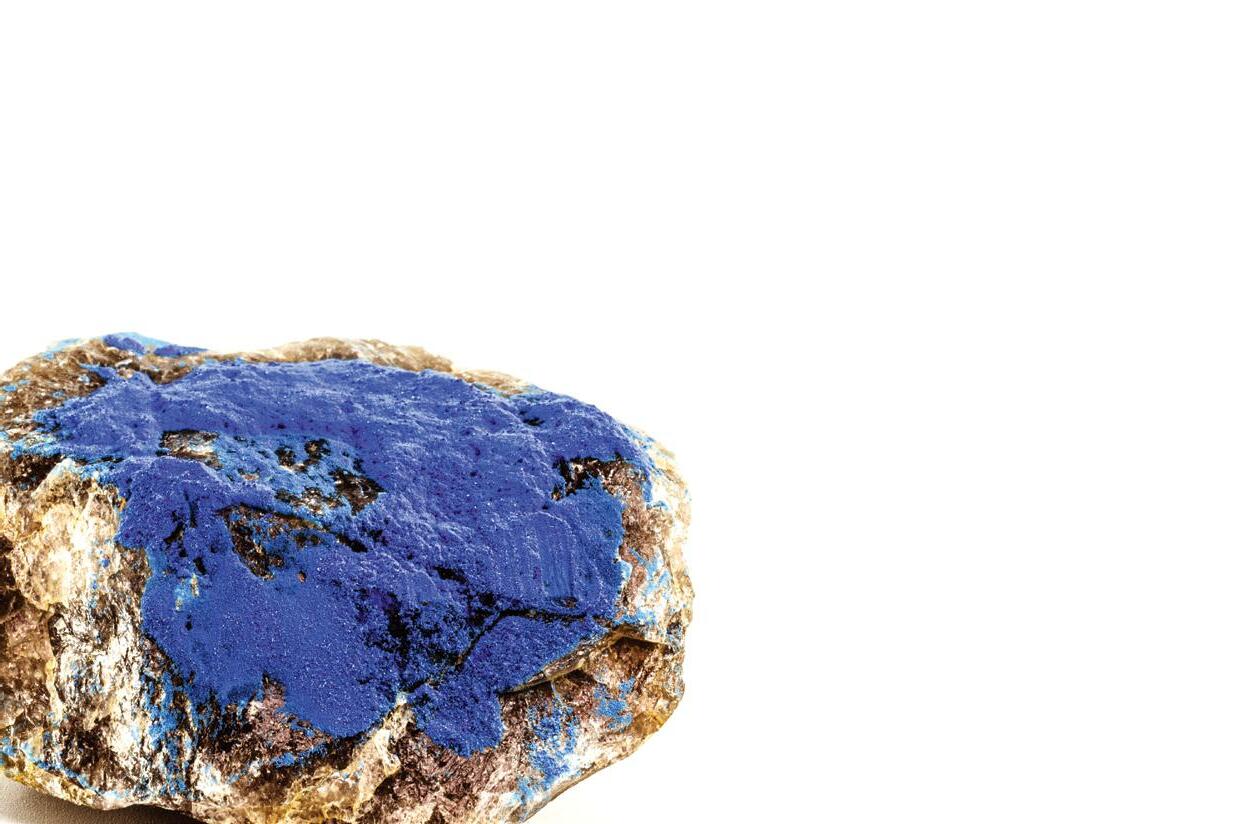
SOMETHING OLD, SOMETHING BLUE New processes to extract minerals from waste sites are highly patentable. There are several examples of these patents being licensed and/or commercialised, such as a recent agreement between Curtin University and the international mining company Draslovka (see p8).
Researchers from the University of Queensland (UQ) have come up with a method for extracting cobalt from the acidic mine tailings left over at the Old Tailings Dam at Savage River, Tasmania.
The process involves using bacteria to separate cobalt from the pyrite that was discarded when the open cut mine was originally exploited for its iron ore. Dr Laura Jackson is part of the team at UQ that came up with the extraction method. She explains that as a native Tasmanian, this kind of rehabilitation work is close to her heart.
The team was trying to work out how to clean up the old site when investigations discovered a high concentration of cobalt in the tailings.
“That led to a set of studies as to how much cobalt, and how you could extract it,” she says. The team is working towards patenting the process.
This kind of rehabilitation or remediation is often referred to as ‘re-mining’. It serves a dual purpose. Firstly, it removes and/or stabilises the sulphur commonly left over in waste products that poisons surrounding groundwater. Secondly, it opens up new, ethical sources of minerals — from cobalt to tungsten and high-purity alumina.
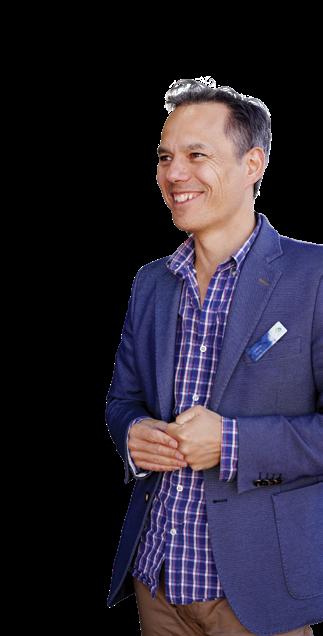
GOING CRITICAL Critical mineral extraction and advanced manufacturing have been big-ticket items on the agendas of successive federal governments in recent years and university science is front-and-centre of these efforts at innovation. For example, the ARC Centre of Excellence for Enabling EcoEfficient Beneficiation of Minerals, based at the University of Newcastle, boasts 16 participating partner unis, including eight in Australia, and four industry partners.
Presently, most of the world’s critical minerals processing happens
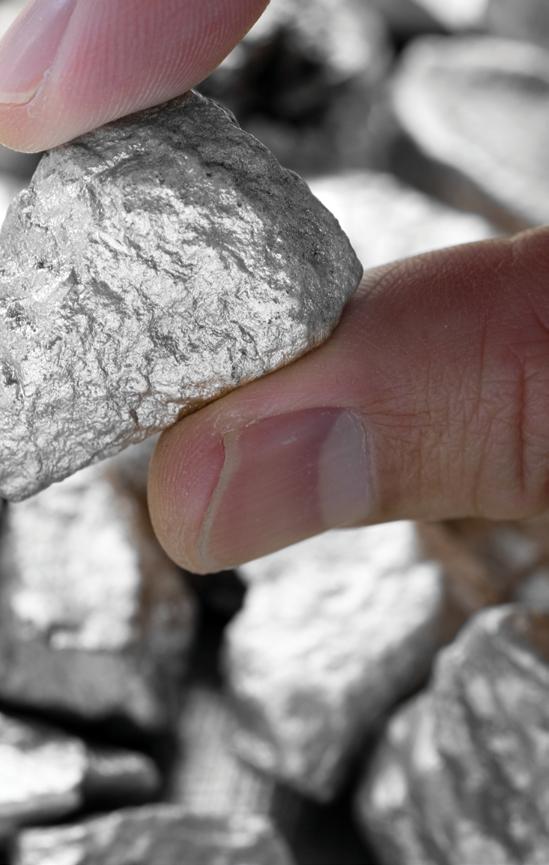
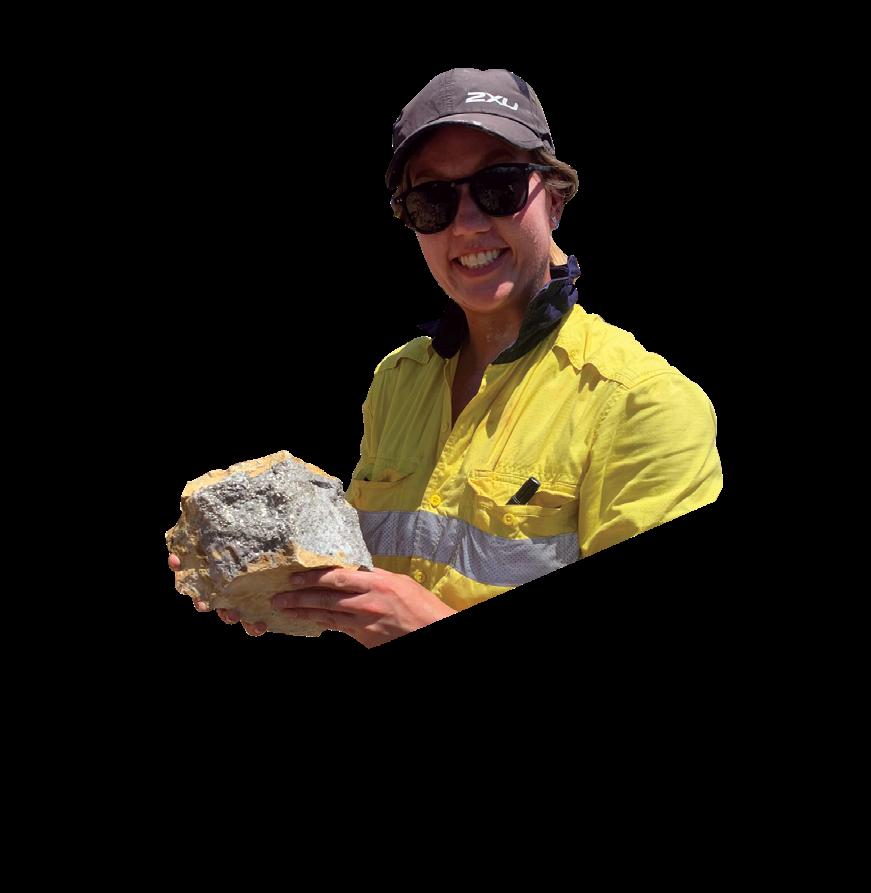
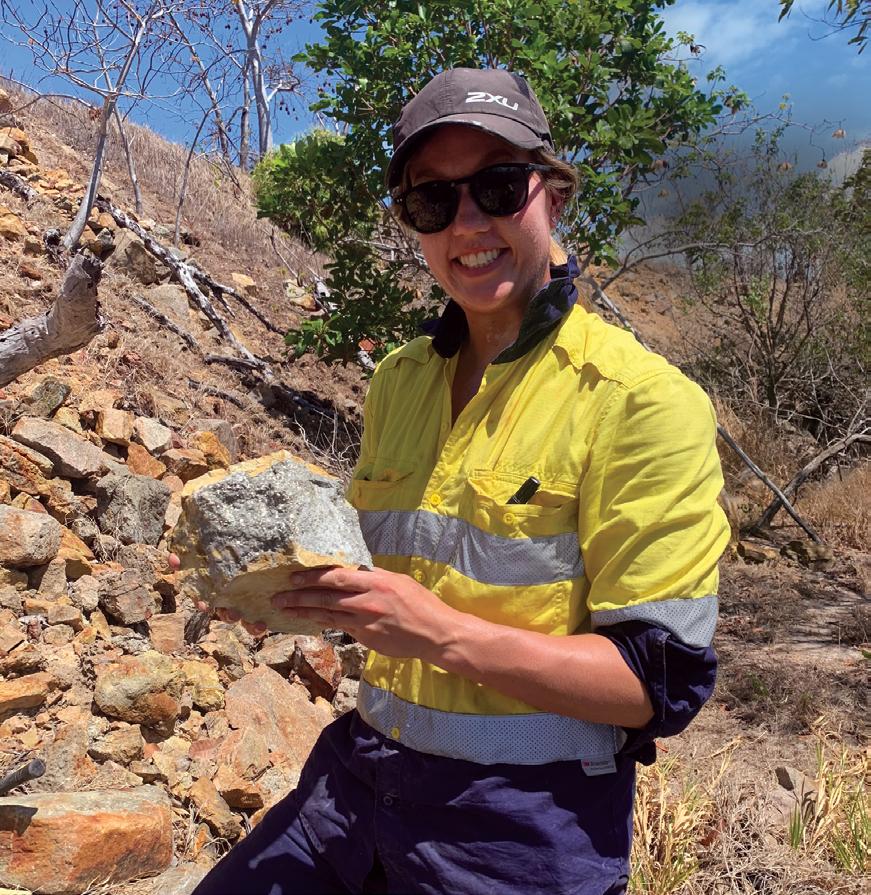
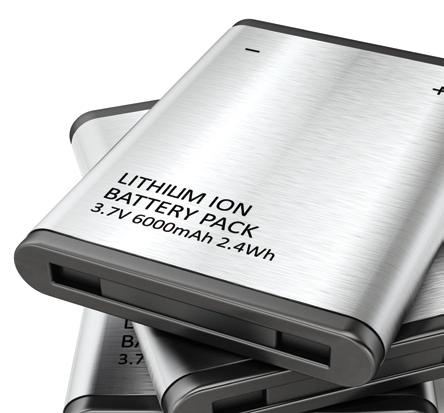
in China. Increasing our critical mineral extraction and processing capacity is both an economic opportunity and an environmental, social, and governance (ESG) opportunity.
In pursuit of those goals, Tong says Australia has an advantage in the quality of its university research and partnerships.
He says situational and compositional differences between mine locations can have a big influence on the type of process you might need to find or invent to exploit specific resources of mine sites. For that reason, innovation in this sector is both necessary and highly collaborative.
This position is echoed by Allison Britt, director of mineral resources advice and promotion for Geoscience Australia (see p5).
GA is part of the National Critical Minerals R&D Centre with the CSIRO and ANSTO. It is performing a stocktake of critical minerals research in Australia across all sectors — commercial, government and university research.
“We want to work out who’s doing what, who has done what…and where our capability gaps are, because there’s further opportunity there to concentrate our efforts,” Britt explains.
“One of the critical minerals activities that’s close to my heart is the national mine waste assessment, which Goescience Australia is doing in collaboration with UQ, RMIT and the geological surveys of Queensland and NSW.”
These programs highlight the importance of university research in every step of the re-mining process, from mapping to investigating mine waste sites for possible sources of valuable metals, and developing new technologies to extract those minerals.
ENSURING ETHICAL SUPPLY CHAINS On a global scale, the demand for environmentally responsible and ethical human labour practices has never been higher. This is a trend that affects all production and manufacturing industries and mining is no exception.
Companies will need to ensure the raw materials needed for modern tech are being sourced in a manner that is sustainable and avoids inhumane working conditions. Recent changes to the EU’s battery standards also mean that more battery components will have to come from renewable and recycled sources — which is a challenge, as the demand for new batteries is expected to outstrip the retirement of old batteries.
These regulatory changes present an opportunity for Australian university science and industry partners. As a country with some of the most stringent standards for occupational health and safety and the environment, Australia is a safe place for companies to source their raw materials, from an ESG standpoint. By providing green sources for critical minerals, research partnerships play a vital role in filling the recycling gap. — Rachael Bolton DIFFERENT MINING ENVIRONMENTS MEAN INNOVATION IN THIS SECTOR IS NECESSARY AND HIGHLY COLLABORATIVE.
outcomes UNIVERSITY SCIENCE & INDUSTRY PARTNERS IN CRITICAL MINERALS
TECH: HIGH-PERFORMANCE ALLOYS AND BATTERIES
MINERAL: COBALT
PARTNERSHIP: UNIVERSITY OF QUEENSLAND + COBALT BLUE Cobalt is a critical mineral often associated with its bright blue colour. It has historically been used in relatively small quantities to produce lightweight but durable alloys like those used in aircraft. It’s a potential boom mineral, with uses in satellite and space travel projects, and in high-performance batteries where rapid charge and discharge is key — think top-end car batteries. Cobalt Blue and the University of Queensland are working together to investigate and rehabilitate old copper mines where the tailings contain cobalt.
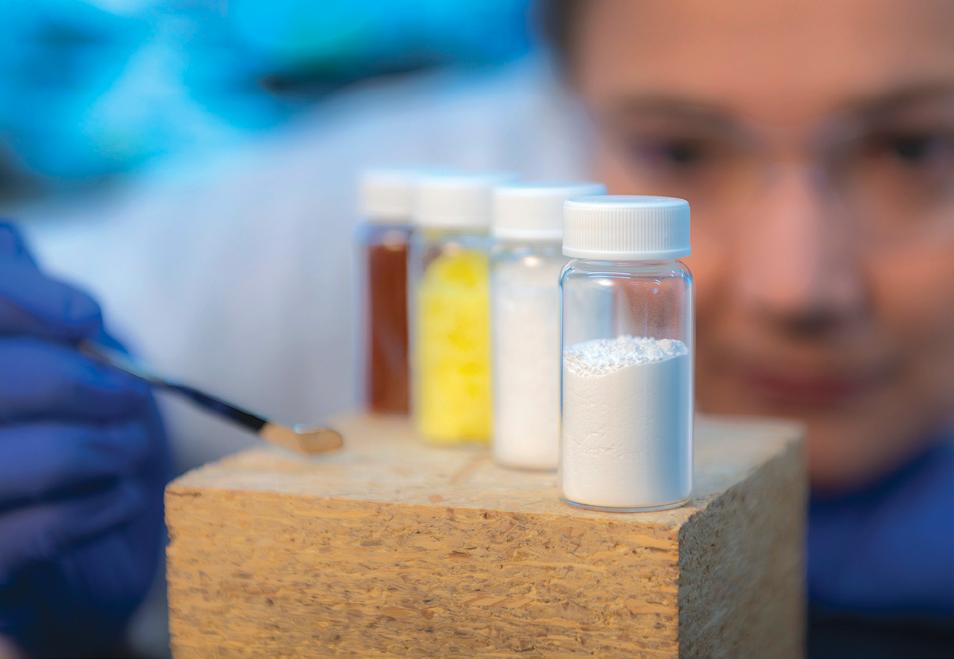
TECH: CIRCUITS AND COOLING
FOR ELECTRONIC DEVICES
MINERAL: TUNGSTEN
PARTNERSHIP: UNIVERSITY OF
QUEENSLAND + EQ RESOURCES Tungsten is a rare mineral used to make alloys that are extremely durable against both heat and wear. Tungsten alloys are some of the hardest metals around, almost as hard as diamond, making them good for things such as heavy cutting blades, armaments and aeronautics. But tungsten is also used in many electronic components, for filaments, electrodes and heat sinks. In January 2022, EQ Resources received a co-investment from the Advanced Manufacturing Growth Centre to re-mine waste product at the Mt Carbine tungsten mine site, supported by the Sustainable Minerals Institute at UQ.
MINERAL: TUNGSTEN
PARTNERSHIP: UNIVERSITY
OF TASMANIA + GROUP 6
METALS Tungsten is also a critical part of much modern circuitry as a heat sink: essentially a piece of metal that sits inside your phone, laptop or other electronic device that transfers heat away from the processor so that the delicate circuitry stays cool and doesn’t overheat or melt. China is currently the dominant global producer for tungsten, which brings with it some environmental and social governance concerns. Australia has tungsten deposits in Western Australia, the Northern Territory and along the eastern seaboard, presenting an opportunity for Australia to step up its tungsten production and deliver a more ethically produced metal in this space. The partnership between the University of Tasmania and Group 6 is built around research into ecologically sustainable production of tungsten at King Island.
TECH: BATTERIES
MINERAL: ALUMINA, MAGNESIUM, VANADIUM
PARTNERSHIP: QUT + LAVA BLUE High Purity Alumina is a product used in the energy-efficient lights of today — LEDs — as well as for separators for lithium-ion batteries. QUT Associate Professor Sara Couperthwaite’s research alongside industry partner Lava Blue has shown this valuable mineral — as well as critical minerals magnesium and vanadium — can be found in kaolin clay. In April 2022, the collaborative project received $12 million in funding to scaleup operations at Redlands Research Park in south-east Brisbane. “This investment is helping Queensland become not just a mining state but a high-tech developer of the future energy needs for the world,” says QUT Vice-Chancellor Prof Margaret Sheil.
TECH: ELECTRICAL CONDUCTION
MINERAL: GOLD
PARTNERSHIP: CURTIN
UNIVERSITY + DRASLOVKA More than just a luxury metal used in jewellery, gold, while not a critical mineral, is a key element in many electronic devices important to the renewable energy economy. Its high conductivity makes electroplating in gold an important part of circuit boards. Curtin University scientists have developed technology that uses amino acids such as glycine to leach gold and other minerals from ore, including waste tailings. The method removes the need to use cyanide in the extraction of gold, making it a much more environmentally friendly process. The Curtin Uni-developed technology was commercialised when Czech multinational chemical supplier Draslovka purchased it in May this year.
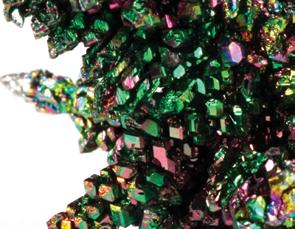