
5 minute read
Kitchen cabinet refinishing
MUST-HAVES & RECOMMENDED
Estimated initial expenses; cost will vary by market and equipment; larger pieces of equipment are available to rent:
Advertisement
Insurance
Liability insurance. Recommended you inform your provider when adding this service, as you may want to adjust your limits, especially if applying solventbased products.
Assorted sundries Costs will vary. (Includes foam brushes, plastic sheeting, caulk, tape, cleaning products, rags, denatured alcohol, floor protection, filters, respirator cartridges)
Strongly
By her own admission, Corrie Leister made the rookie mistake of thinking ‘how hard could it be?’ when taking on her first cabinet painting project in 2015.
“I was at a bit of a crossroads in my life when a family friend asked me to take on painting her cabinets,” she says. “I had painting experience as an artist, so I wasn’t intimidated. That was until I visited the local specialty paint shop and realized there was a LOT more to cabinets than most walls. I was fortunate that my client paid for me to take a training offered at that store. At the same time, I dug in to social media forums and found an abundance of information and people willing to share their knowledge. All that combined to flatten a rather steep learning curve.”
Today, Leister runs Inspired By U Cabinet & Furniture Refinishing in Mechanicsburg, PA that offers cabinet refinishing, markets a proprietary industrial coating line, and provides refinishing training for pros via Inspired By U-niversity. What started as a team of one operating from her garage has grown into a full-fledged business with a shop, a retail store and a team of nine part-time painters (all moms), a parttime carpenter, a shop/crew lead, plus her husband who handles sales and scheduling. The team typically completes three kitchens every 10 days.
Unlike Leister who was at the bottom of the learning curve when she got her start, Denny Jahnz of Cabinet ReNu in Mankato, MN, launched his cabinet business in 1999 after spending 2-1/2 years working for Kitchen Tune-Up, a kitchen remodeling franchise.
“I was pretty much up to speed when I went out on my own. I knew what equipment I needed and what coatings I liked to use and why,” he says. Today, Jahnz employs a team of six who split their time between custom builds and cabinet refinishing. He says his operational sweet spot involves tackling one refinishing job and one custom build a week.
Process is paramount
Leister and Jahnz have similar approaches to refinishing work that involve taking doors and drawers back to their shops for cleaning, prep, priming and painting while boxes are handled on site.
Jahnz notes they typically turn refinishing jobs around in five days or less. Here’s his process:
“Day one is dedicated to tear down and prep, including removing doors and drawers. Day two we clean, prep and prime the cabinet boxes on site. We also begin cleaning and prep of doors and drawers back at the shop. Days three and four we paint the boxes and remove all plastic and tape from the kitchen. We also finish priming and painting doors and drawers in the shop. On the last day, we install the doors and drawers and do a full cleanup.”
While that may sound like easy work, Jahnz notes there’s years of experience packed into every step of the process.
“Cabinet work is not for the lazy or disorganized,” he says. “Every door has to be labeled when it comes off. You have to pay attention to the hinges. If you don’t know how they work—and there are lots of different kinds of hinges—you’ve got to learn so that when you rehang the doors, they sit level and flush. And you have to be thorough in prepping the area. Not only to avoid overspray landing on the floor or counters but also to ensure the safety of your crew and the homeowners.”
Both pros utilize ZipPoles and plastic sheeting to tent the work area. In her workspace, Leister adds a humidifier, heaters, air scrubbers and a vent fan aimed out a door or window. Jahnz is partial to air scrubbers with a three-stage filter system that takes particulates out of the air. “We position an air scrubber with either a furnace, carbon or HEPA filter outside the tent and cut a hole in the plastic sheeting to vent directly to the scrubber.” Both setups incorporate fans to increase circulation and to hasten drying. Jahnz also utilizes infrared curing lamps when he’s looking to speed up the dry time on primer or paint.
Surface and product considerations
“The biggest mistake you can make when taking on a cabinet project,” says Jahnz, “is treating it like any other
Heat Gun
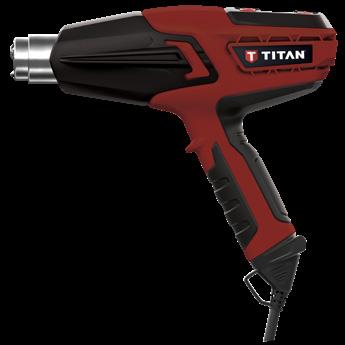
“If you get a spot sprayed surface, especially in the prep process. Honestly, you never know what people have used to clean the surface … it could be Pledge, it could be Murphy’s Oil Soap. And you can’t make assumptions about the existing topcoat or what’s underneath it. It’s really a bit of forensic work to get things figured out and prepped properly. But if you don’t do it right, you’ll be doing the whole job again.”
Leister agrees and notes that getting the prep right alone doesn’t guarantee success. “You absolutely have to be on top of what you’re painting,” she says. “There are a lot of substrates out there and you have to understand their quirks and qualities. For example, an open-grain substrate can take three times longer to complete than a closed-grain one. If you charge a flat linear square-foot rate, you can lose a lot in labor costs.”
She adds there are always new substrates coming out so the learning never stops. “I love the learning, but the constant change is a challenge every pro in the business has to be prepared to endure.”
When it comes to product preference, Leister’s a big fan of the Milesi Waterborne Polyurethane Coatings.
“The oils in skin will break down traditional enamels so you’ve got to choose your product wisely. I’ve found Milesi’s formulation stands up to the repeated handling, plus the products go on like a dream and look great.”
Jahnz isn’t as brand loyal as Leister, happily working with Envirolak, Ilva, Milesi and General Finishes, but he is committed to water-based, two-component paints. “In my opinion, they offer the best durability, adhesion and performance. And being water based, they’re safer to deal with and easier to dispose of.”
Training and tool talk
For pros new to water-based coatings, Jahnz strongly encourages training. “Everyone—including those with sprayer experience—can benefit from training specific to water-based coatings. Hands-on training with plenty of practice opportunity will help get your pressure and technique dialed in before you start tackling jobs.”
To that point, the Cabinet ReNu team participates in three to four trainings a year.
Jahnz encourages pros to tap both their equipment and coatings manufacturers for training. “They’re interested in you having the best possible experience with their product and do what’s necessary to ensure it,” he says. “In my experience, SurfPrep and TriTech reps offer some of the best hands-on training. All you have to do is ask.”
As a trainer herself, Leister makes sure her team is trained in industrial coatings handling, customer contact, teardown, prep sanding and masking, application of primer and topcoat, setting up an on-site spray booth, and unloading doors. “There’s a system to everything,” she says, “and it pays to make sure everyone is following it.” -
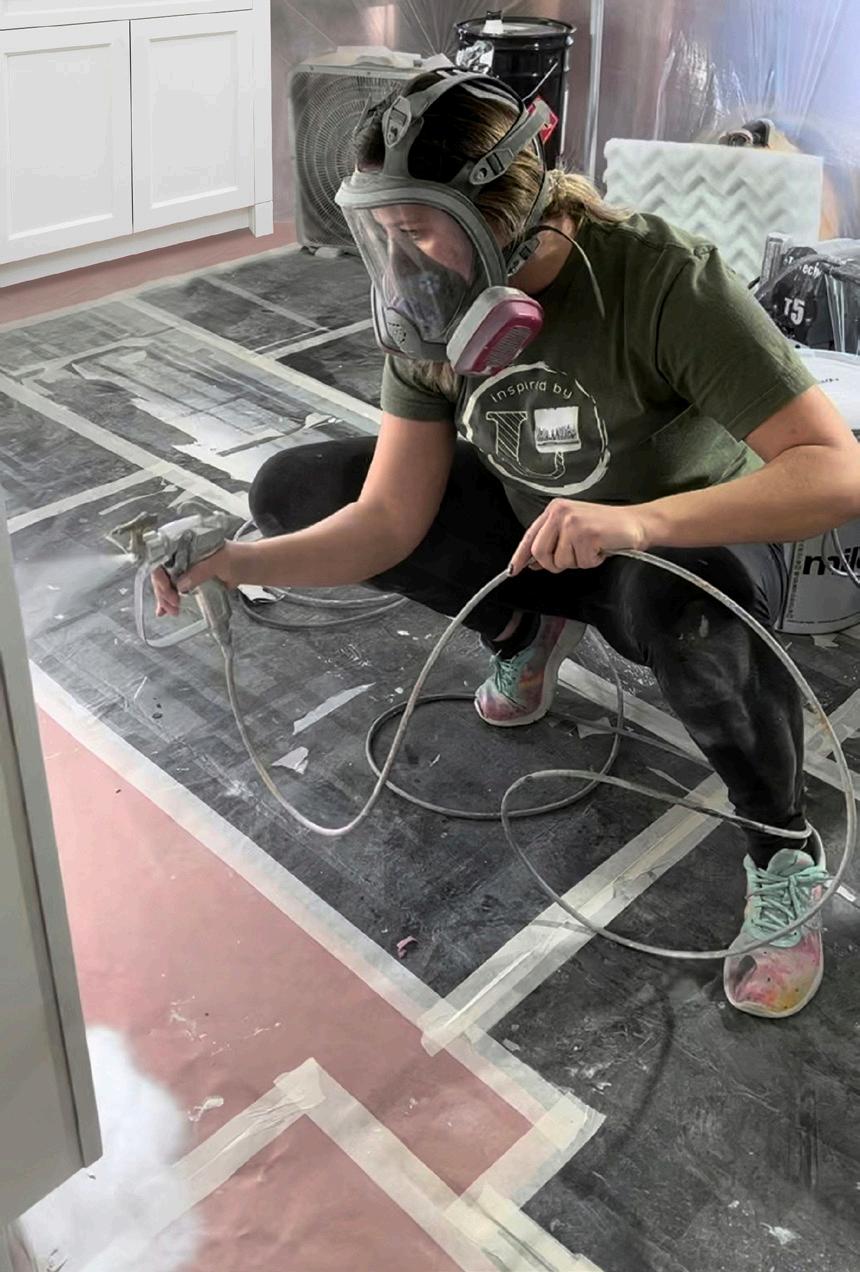
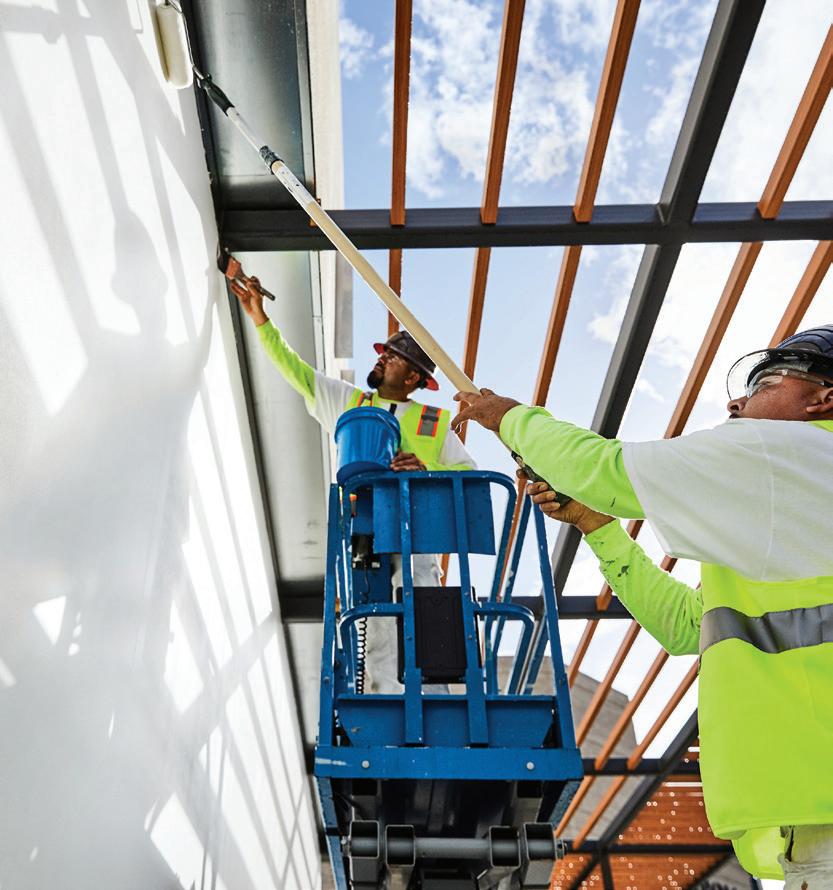
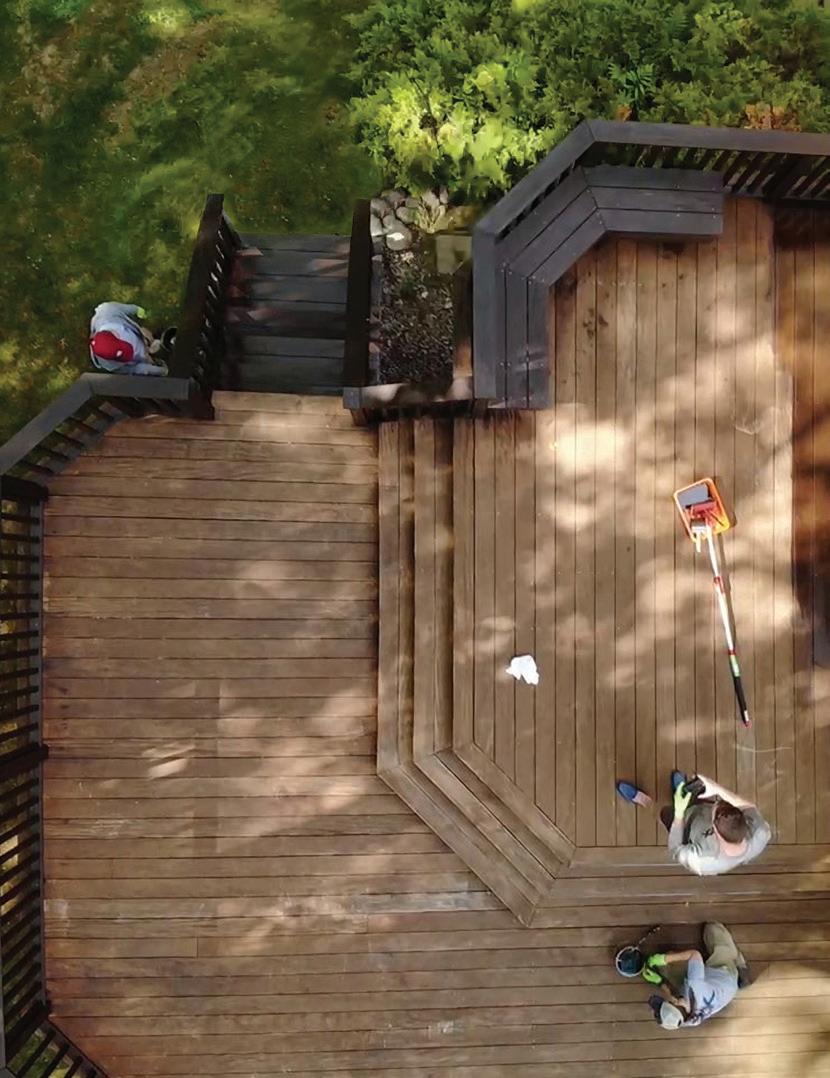

