Insights
The printed circuit board (PCB) market is evolving rapidly, driven by technological advancements, shifting supply chain dynamics, and the increasing demand for sustainable manufacturing practices. According to Inkwood Research, the global printed circuit board market is expected to record a CAGR of 4.98% during the forecast period, 2024-2032.
For original equipment manufacturers (OEMs), selecting the right PCB supplier is paramount to ensuring product quality, reducing environmental impact, and achieving cost-effective scalability. In fact, the right partnership can streamline production timelines, minimize risks, and provide the flexibility needed to adapt to rapidly changing market demands.
This blog delves into the critical aspects of choosing a PCB supplier, the importance of sustainable practices in the industry, strategies to mitigate supply chain challenges, and effective ways to scale PCB production without compromising on quality.
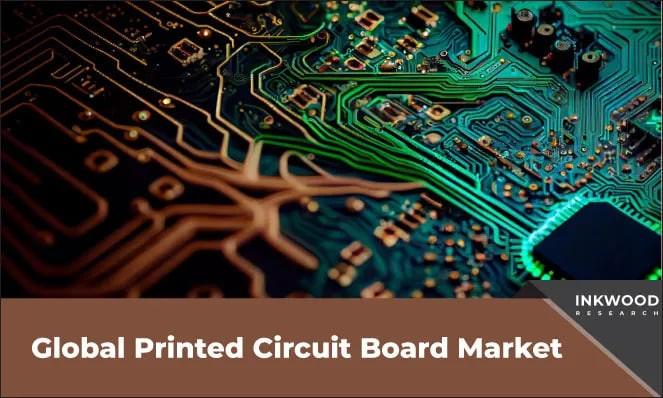
Request a FREE sample of the Printed Circuit Board (PCB) Market
Choosing the Right PCB Supplier: Key Considerations for OEMs
When OEMs evaluate PCB suppliers, it is essential to focus on several factors that go beyond price. The right supplier can make the difference between seamless production and costly delays, and their role extends from providing quality products to ensuring consistent supply chain operations.
Quality Assurance and Certification: One of the foremost considerations for OEMs is the supplier’s ability to deliver high-quality PCBs that meet international standards. Suppliers must adhere to certifications such as ISO 9001, IPC-A-610, and UL standards. Ensuring a supplier has strict quality control mechanisms, such as automated optical inspection (AOI) and X-ray inspection, is critical to detecting defects early in the production process.
Scalability and Flexibility: As product demand fluctuates, OEMs require a PCB supplier capable of scaling production efficiently. Suppliers should have the infrastructure to support both small batch runs and high-volume orders, while also offering flexible lead times. For instance, rapid prototyping services can accelerate product development timelines, while automated production systems help meet larger order volumes without sacrificing quality.
Technological Capabilities: In a market where technology evolves quickly, OEMs should prioritize suppliers that invest in the latest manufacturing techniques, such as high-density interconnect (HDI) boards, multi-layer PCB designs, and flexible PCBs. These innovations enable more complex and compact electronic designs, essential in sectors like consumer electronics, automotive, and medical devices.
Global Reach with Local Expertise: A supplier with a global presence provides greater flexibility in managing production needs across different geographies while also mitigating risks associated with localized disruptions. OEMs should look for suppliers that combine global scale with local support, ensuring timely communication and fast response times when issues arise.
Click here to get more insights about the Global Printed Circuit Board (PCB) Market
Sustainable PCB Production: Importance of Minimizing Environmental Footprint
With sustainability becoming a growing concern across industries, the PCB sector is no exception. The environmental impact of PCB production is a growing concern, driven by increasing waste generation, plastic pollution, greenhouse gas emissions, and the presence of toxic materials.
The rising demand for electronics, fueled by technological advancements and population growth, has led to a significant increase in PCB resin waste and electronic waste (e-waste). In fact, according to a 2024 study, Asia alone accounted for nearly 50% of global e-waste in 2022.
Furthermore, greenhouse gas emissions from PCBs with active elements range from 100–250 gCO2eq/g, with carbon dioxide emissions between 65–215 g-CO2/g (Source). As a result, suppliers are now adopting eco-friendly practices, driven by stricter regulations and the need for sustainable solutions. Here’s how –
Eco-Friendly Materials and Processes: Suppliers are increasingly turning to greener materials, such as halogen-free laminates and lead-free solder, to reduce the toxicity of the end product. Furthermore, innovations in water treatment processes and chemical recycling systems help minimize waste during production. OEMs partnering with environmentally conscious suppliers not only contribute to sustainability goals but also comply with global environmental regulations, like the European Union’s RoHS directive, which restricts the use of hazardous substances in electronics.
Energy Efficiency in Manufacturing: Reducing energy consumption during PCB production is another important aspect of sustainability. PCB manufacturers are adopting more energyefficient production methods, such as utilizing energy-saving machines and optimizing plant layouts to lower energy costs. According to Inkwood Research, the global PCB market is projected to reach $xx billion by 2032, and much of this growth is expected to be driven by eco-friendly innovations that enable OEMs to meet their sustainability targets.
Circular Economy and Recycling: PCBs contain valuable materials like copper, gold, and palladium, which can be recovered and reused. Companies are now investing in closed-loop systems that recover these metals, thus reducing the need for mining raw materials. For instance, Excir’s innovative, patented technology uses advanced chemistry to recover over 99% of the gold found in e-waste, specifically from circuit boards in discarded laptops and mobile phones. This breakthrough process selectively targets and extracts precious metals from circuit boards within seconds, providing an efficient solution to the rapidly growing global issue of electronic waste. OEMs can significantly benefit by partnering with PCB suppliers that offer recycling programs, ensuring the responsible disposal and recovery of used PCBs.
Kindly click here to view the LinkedIn post related to this market
PCB Market Supply Chain Guide: Turning Roadblocks into Opportunities
The global PCB market, like many other sectors, has been hit by supply chain disruptions, exacerbated by events such as the COVID-19 pandemic. These disruptions have led to extended lead times, component shortages, and increased costs, making it crucial for OEMs to adopt strategies that enhance supply chain resilience.
Diversification of Suppliers: One key strategy is to diversify the supplier base. Relying on a single supplier can be risky, especially during global crises. Working with multiple suppliers across different regions can help OEMs mitigate risks such as factory shutdowns, political instability, and shipping delays.
Inventory Management and Forecasting: Implementing robust inventory management systems and demand forecasting tools can help businesses stay ahead of supply chain disruptions. OEMs should work closely with suppliers to develop accurate forecasts and buffer stock strategies that ensure materials are available even during times of scarcity.
Supply Chain Transparency and Collaboration: Real-time visibility into the supply chain enables OEMs to respond to potential disruptions swiftly. Investing in digital solutions, such as blockchain technology or integrated supply chain management platforms, can provide greater transparency and enable more efficient communication with suppliers. Collaboration across the supply chain—from raw material suppliers to logistics providers—is also crucial in identifying and resolving bottlenecks early.
Concluding Insights | Printed Circuit Board (PCB) Market
As demand for electronic products grows, OEMs can scale PCB production efficiently by leveraging automation and Industry 4.0 technologies. Automation reduces labor costs and boosts production efficiency, while IoT-driven smart factories enable real-time monitoring, reducing errors and increasing output.
Additionally, OEMs can also outsource non-core activities, such as assembly or testing, to specialized contract manufacturers, benefiting from their economies of scale. Optimizing PCB designs for manufacturability, by simplifying designs and collaborating with suppliers early, further reduces costs and ensures efficient production.
In essence, the PCB industry presents both opportunities and challenges for OEMs. Selecting the right supplier, prioritizing sustainability, navigating supply chain complexities, and adopting costeffective scaling strategies are all essential components of success.
By focusing on these areas, OEMs can not only ensure the quality and availability of their products but also align with broader industry trends, such as the push toward greener manufacturing and the integration of advanced technologies. As the global printed circuit board market continues to grow and evolve, these considerations will remain critical in driving long-term business success.
Explore the market insights in this YouTube video by clicking here
Can’t find what you’re looking for? Talk to an expert NOW!
FAQs:
1. What are the benefits of outsourcing non-core PCB activities?
A: Outsourcing tasks like assembly or testing to specialized contract manufacturers allows OEMs to focus on their core competencies while benefiting from the third party’s economies of scale, leading to cost savings and more efficient scaling.
2. How does optimizing PCB design reduce manufacturing costs?
A: By simplifying PCB designs, reducing layer counts, and choosing standard components, OEMs can lower production complexity and material costs. Early collaboration with suppliers ensures the designs are optimized for cost-effective, high-quality manufacturing.