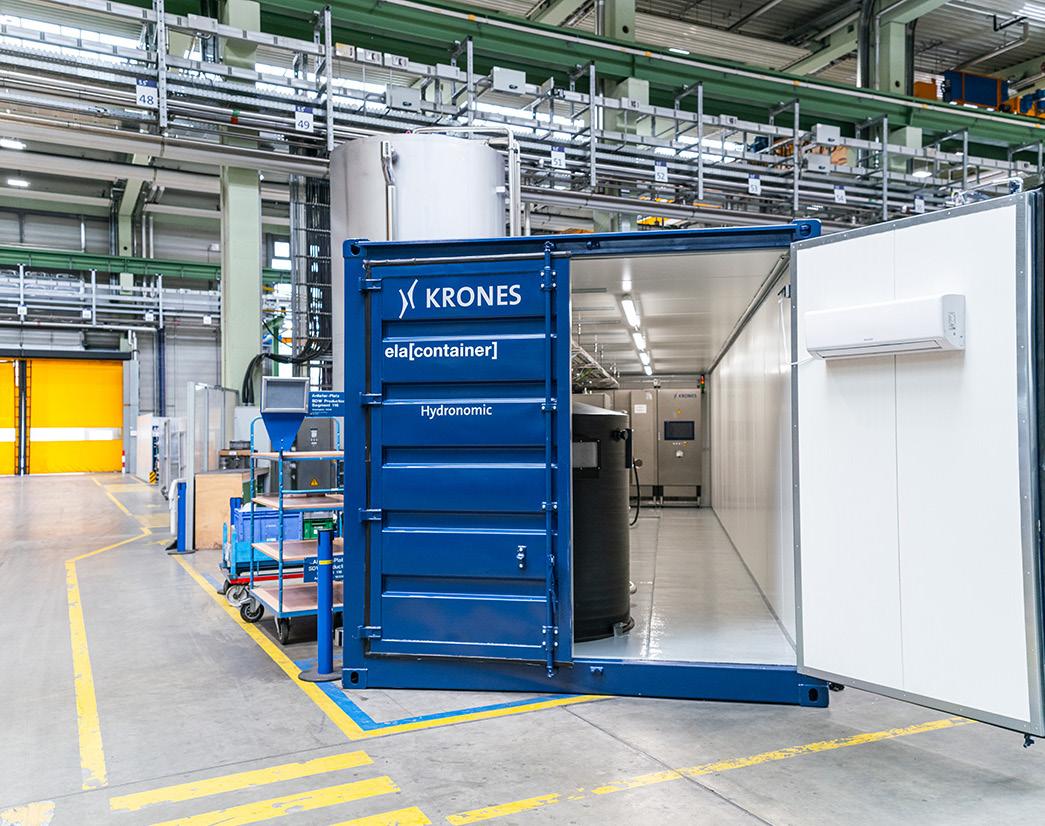
3 minute read
Utilising a container for space constraints
Since demand at Blends Flavours & Colours is going through the roof, the company had to increase its capacity for beverage production and filling, which is why it turned to Krones. “We have a water treatment system already, but it wasn’t big enough for our needs. So we spoke with Alex from the local Krones UK sales team and decided to collaborate with them, because we felt that the Krones quality was right for our customers,” says Andrew Richardson, who manages the beverage plant for Blends.
During the planning phase, it quickly transpired that a new water treatment system and a new syrup room together would not fit into the existing building. This challenge didn’t present an obstacle to Krones: If there isn’t any space, we’ll just create some more, was the approach. Krones planned the water treatment system so that all components would fit inside a single container. o nly the 20,000-litre product tank was installed outside.
The Krones team is used to installing systems into existing halls or between existing lines and having to play around, to get a precise fit. However, the only available installation space for laying out all the vessels and modules of the Hydronomic RO was a container? Even Krones had never come across this before.
Assembly TeTris
In Krones neutraubling, where the vessels and modules of the hydronomic are assembled, there was astonishment when a shipping container suddenly appeared alongside the usual vessels, tanks and components.
It had a Tetris feel about it, similar to the video game, where the coloured elements are stacked precisely and efficiently, with the components of the hydronomic sensibly arranged and efficiently coordinated. It was due to this detailed preliminary work and the necessary routines in assembly that all machine components were ready, in place on time for the Factory
Acceptance Test.
When Andrew Richardson came to neutraubling with colleague Peter Millea to see the systems operating for the first time, they were delighted by the overall outcome, planning and assembly work achieved.
Hydronomic ro wATer
TreATmenT sysTem
• Method of operation: reverse osmosis (Ro)
• Output: 15,000 litres per hour
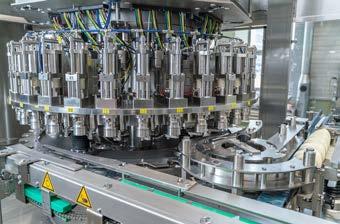
• Components installed in shipping container:
- dosing station for cleaning media
- 2,000-litre break-water tank
- hydronomic UV module for removing all the ozone or chlorine
• Also: adjacent product tank with a capacity of 20,000 litres

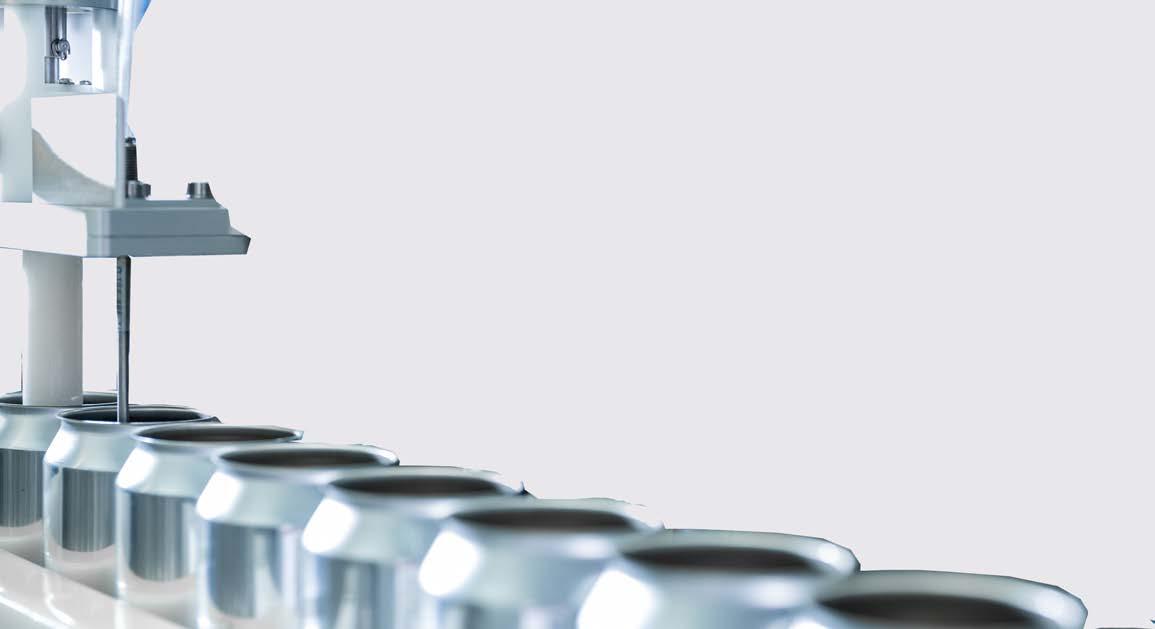
syrup room: milkron
The hydronomic, though, is not the only new process technology equipment that Blends ordered. Krones subsidiary Milkron, has installed a new syrup room at Blends’ Knowsley factory.
The aim was to produce as broad a range of beverages as possible. That’s because alongside various CSDs and water, Blends have mixed alcoholic drinks in its portfolio. “For canning specifically, we have a customer in the sports and nutrition sector who wanted to release a range of cans. We struggled to find canning capacity in the UK and europe to get the product right at the quality they wanted. The new syrup room and the canning system now enables us to offer the diversity required,” says Andrew Richardson.
The syrup room contains various dosing stations, such as for flavourings, high-proof alcohol, sugar dissolving plant and two blending tanks, each with a capacity of 15,000 litres. There is also a CIP system.
including cAn Filler And dry end From krones
While its portfolio and expertise may suggest something different, Blends’ main business is not in the production of beverages. In fact, the roots of the company lie in the food industry: The family-owned business has been supplying bakeries with a variety of additives since 1994. Its portfolio grew year on year, and the company now creates over 20,000 products such as flavourings, dyes, plus other ingredients for the baked goods and beverage industries.
o ver the last few years, Blends has made a name for itself as a co-packer, who offer canning and bottling in glass. Demand in this segment has grown enormously: “We’ve seen a lot of customers that were switching from bottle to can because of sustainability, so we took the opportunity to strengthen our position in that market,” says Andrew Richardson.
The Modulfill VFS-C can filler achieves an output of up to 15,000 cans per hour but is actually capable of 19,200 cph should the need arise.
“We try to offer 50 ml up to 500 ml if possible and we do the same for bottles, where we go from 20 ml to 5 litre, so we have to be very flexible depending on customer requirements”, Andrew
Richardson adds. The new system matches this flexible approach: It can process both slim and sleek cans, in sizes between 150 and 330 ml, as well as still and carbonated beverages. These are mixed with the aid of a new Krones Contiflow. For sensitive beverages such as milk alternatives, Krones also installed a VarioFlash J flash pasteuriser for preservation.
“so FAr, THe experience HAs been brilliAnT” one of the arguments in favour of Krones was their overall expertise in process technology. The Krones group is, after all, the only player on the market to offer the full range of technology, from water treatment to finished product, from a single source.

“It’s our first time working with Krones. So far, the experience has been brilliant. Probably the best supplier we have worked with. The team has been helpful regarding any questions raised with prompt answers” Andrew Richardson concludes.
Krones UK Ltd. | 00 44 (0) 1942 845000 Westregen house, great Bank Road, Wingates Industrial Park, Westhoughton, Bolton, BL5 3XB.