
3 minute read
Alumínio reciclado oferece economia de energia, emissões e bateria de veículos elétricos
from Amazônia 117
OLaboratório Nacional do Pacífico Noroeste do Departamento de Energia, em colaboração com a empresa líder em tecnologia de mobilidade Magna, revela um novo processo de fabricação que reduz mais de 50% da energia incorporada e mais de 90% das emissões de dióxido de carbono, eliminando a necessidade de minerar e refinar a mesma quantidade de minério bruto de alumínio. O alumínio leve também pode ajudar a estender a autonomia do EV.
Este processo patenteado e premiado de Processamento Assistido por Cisalhamento e Extrusão (ShAPE™) coleta pedaços de sucata e restos de aparas de alumínio da fabricação automotiva e os transforma diretamente em material adequado para novas peças de veículos. Agora está sendo dimensionado para fabricar peças leves de alumínio para veículos elétricos.
Advertisement
O avanço mais recente, descrito em detalhes em um novo relatório de pesquisa da Manufacturing Letters, elimina a necessidade de adicionar alumínio recém-extraído ao material antes de
A microestrutura dentro de um trapézio de alumínio mostra um tamanho de grão altamente refinado e uniforme, a chave para alcançar um produto forte e confiável (Imagem cortesia de Nicole Overman; aprimoramento usá-lo em novas peças. Ao reduzir o custo da reciclagem do alumínio, os fabricantes podem reduzir o custo geral dos componentes de alumínio, permitindo que eles substituam melhor o aço.
“Mostramos que as peças de alumínio formadas com o processo ShAPE atendem aos padrões da indústria automotiva para resistência e absorção de energia”, disse Scott Whalen, cientista de materiais do PNNL e pesquisador principal. “A chave é que o processo ShAPE quebra as impurezas de metal na sucata sem exigir uma etapa de tratamento térmico com uso intensivo de energia. Isso por si só economiza um tempo considerável e introduz novas eficiências.” O novo relatório e as publicações de pesquisa marcam o ponto culminante de uma parceria de quatro anos com a Magna, a maior fabricante de autopeças da América do Norte. Magna recebeu financiamento para a pesquisa colaborativa do DOE’s Vehicle Technologies Office, Lightweight Materials Consortium (LightMAT) Program.
“A sustentabilidade está na vanguarda de tudo o que fazemos na Magna”, disse Massimo DiCiano, gerente de ciência de materiais da Magna. “Desde nossos processos de fabricação até os materiais que usamos, e o processo ShAPE é uma grande prova de como procuramos evoluir e criar novas soluções sustentáveis para nossos clientes”.
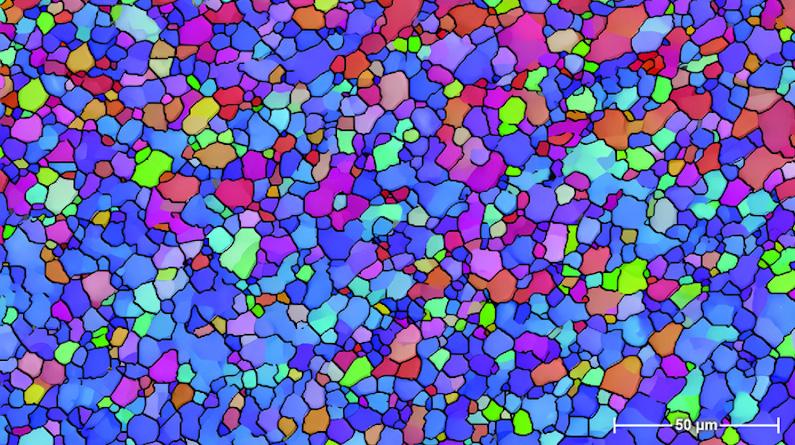
Vantagens do alumínio
Além do aço, o alumínio é o material mais utilizado na indústria automobilística. As propriedades vantajosas do alumínio o tornam um componente automotivo atraente. Mais leve e resistente, o alumínio é um material fundamental na estratégia de tornar os veículos leves para maior eficiência, seja ampliando a autonomia de um VE ou reduzindo o tamanho da capacidade da bateria. Enquanto a indústria automotiva atualmente recicla a maior parte de seu alumínio, ela rotineiramente adiciona alumínio primário recém-extraído a ele antes de reutilizá-lo, para diluir as impurezas.
Os fabricantes de metais também contam com um processo centenário de pré-aquecimento de tijolos, ou “tarugos”, como são conhecidos na indústria, a temperaturas acima de 1.000°F (550°C) por muitas horas. A etapa de pré-aquecimento dissolve aglomerados de impurezas como silício, magnésio ou ferro no metal bruto e os distribui uniformemente no tarugo por meio de um processo conhecido como homogeneização.
Por outro lado, o processo ShAPE realiza a mesma etapa de homogeneização em menos de um segundo e transforma o alumínio sólido em um produto acabado em questão de minutos, sem necessidade de etapa de pré-aquecimento.
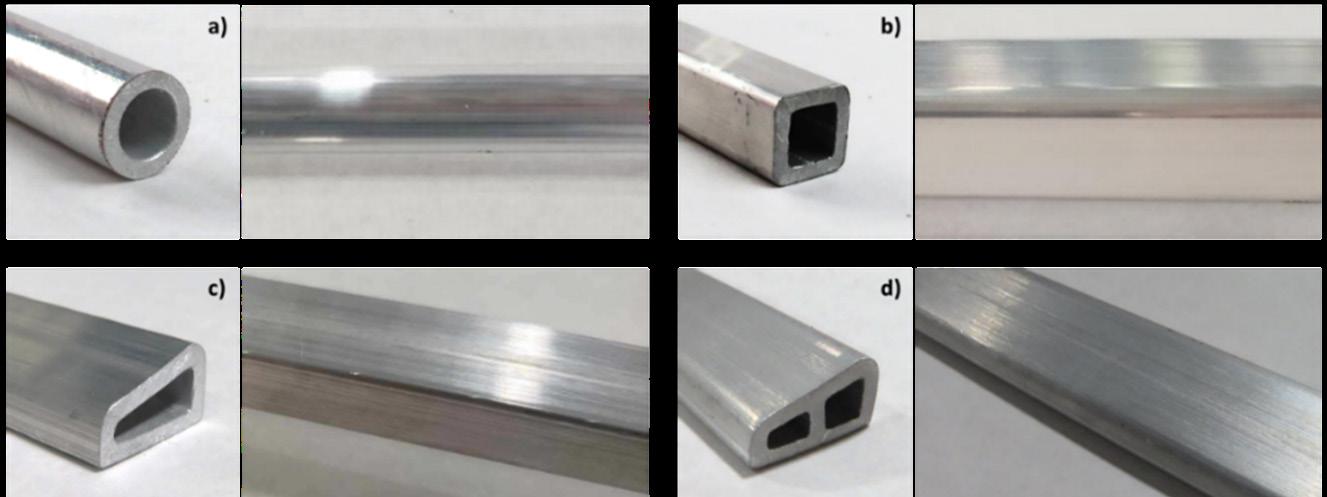
“Com nossos parceiros da Magna, atingimos um marco crítico na evolução do processo ShAPE”, disse Whalen.
“Mostramos sua versatilidade criando peças quadradas, trapezoidais e multicelulares que atendem aos padrões de qualidade de resistência e ductilidade.”
Para esses experimentos, a equipe de pesquisa trabalhou com uma liga de alumínio conhecida como 6063, ou alumínio arquitetônico.
Esta liga é usada para uma variedade de componentes automotivos, como berços de motor, conjuntos de pára-choques, trilhos de estrutura e acabamento externo. A equipe de pesquisa do PNNL examinou as formas extrudadas usando microscopia eletrônica de varredura e difração de retroespalhamento de elétrons, que cria uma imagem da colocação e microestrutura de cada partícula de metal dentro do produto acabado.

Os resultados mostraram que os produtos ShAPE são uniformemente fortes e não apresentam defeitos de fabricação que podem causar falhas nas peças.
Em particular, os produtos não apresentavam sinais de grandes aglomerados de metal – impurezas que podem causar deterioração do material e que dificultaram os esforços para usar o alumínio reciclado secundário na fabricação de novos produtos. A equipe de pesquisa agora está examinando ligas de alumínio de resistência ainda mais alta, normalmente usadas em compartimentos de bateria para veículos elétricos. “Esta inovação é apenas o primeiro passo para a criação de uma economia circular para o alumínio reciclado na fabricação”, disse Whalen. “Agora estamos trabalhando para incluir fluxos de resíduos pós-consumo, o que pode criar um mercado totalmente novo para sucata secundária de alumínio”.
