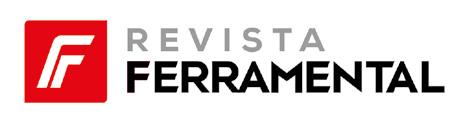
4 minute read
FICHA TÉCNICA
MECANISMOS DE FALHAS NA INJEÇÃO DE AL
HAIKAI TÉCNICO 009
Advertisement
Apesar do desgaste apresentar contribuição relativamente menor e a causa principal de descarte do molde de injeção de Al estar associado a trincas por fadiga térmica, apresentamos abaixo a descrição formal desses fenômenos. Desgaste é a perda de material de um corpo devido a movimentos relativos em sua superfície. A superfície do molde de fundição sob pressão pode apresentar desgaste associado à adesão (solda) e erosão (corrosão). A erosão é causada pelas altas velocidades com que o metal fundido colide com a superfície do molde. A “Cavitação” do alumínio no estado líquido em alta velocidade reduz a pressão, vaporiza, produz bolhas no interior do fluxo que implodem quando reduzida a pressão e cria ondas de choque danificando a superfície. A cavitação e o arraste mecânico da superfície devido a uma alta velocidade de injeção que pode chegar a 60 m/s [1] fazem com que a superfície do molde seja lavada para fora com o metal fundido. Adesão e Erosão na ferramenta se originam pela interação química decorrente da interdifusão de átomos do molde e da liga injetada que resulta na formação de compostos intermetálicos de alumínio de ferro e elementos de liga produzindo agarramento da peça durante a extração [2]. Esses fenômenos estão relacionados a [1]:
• Temperatura do alumínio muito alta; • Posicionamento (incorreto) dos canais de refrigeração; • Ciclo rápido de injeção; • Desmoldante insuficiente; • Temperatura de preaquecimento do molde muito alta; • Localização do “gate” de entrada não favorável ao melhor escoamento do metal liquido; • Acabamento superficial do molde de baixa qualidade; • Uma boa prática para o bom desempenho da superfície do molde é realizar jateamento com micropartículas antes da nitretação e nisto, interessante registrar um fato polêmico relacionado: “no início do século XXI, nadadores de elite utilizaram uma roupa desenvolvida simulando a topografia rugosa da pele do tubarão como redução do atrito com a água”.
Desgaste pode estar associado também ao desenvolvimento de trincas térmicas (fadiga térmica) que tem relação com:
• Temperatura desfavorável da superfície da cavidade; • Posicionamento e dimensão incorreta do canal de refrigeração; • Tipo e temperatura do meio de resfriamento; • Temperatura e preaquecimento do molde; • Velocidade da liga fundida muito elevada na cavidade; • Impacto da liga fundida na cavidade, machos e cantos próximos aos canais de entrada; • Microestrutura do aço inadequada associada a matéria-prima e, ou, ciclo térmico; • Ciclo de injeção rápido, ou curto
Todos os mecanismos citados acima podem estar presentes, sendo um, ou outro, em maior evidencia em razão de:
• Projeto de construção do molde; • Tipo e propriedades do aço do molde (dureza, tenacidade, expansão térmica e coeficiente de transmissão de calor); • Processos térmicos do aço do molde (têmpera/revenimentos e tratamentos de superfície); • Tipo de máquina (tamanho molde / máquina de injeção); • Tempo de ciclo de injeção do alumínio; • Temperatura da liga de alumínio; • Tipo de liga de alumínio; e • Manutenção do molde.
[1] Lindow, Horst – Eng. Metalurgista, Consultor Uddeholm [2] Mitterer, C. “Application of hard coatings in aluminium die casting soldering, erosion and thermal fatigue behavior” – Surface and Coatings Technology, p.233-239, 2000

O QUE É O PROCESSO “DUPLEX”
HAIKAI TÉCNICO 010
O processo de modificação de superfícies de liga ferrosas – principalmente para aquelas de alta liga – conhecido comercialmente como DUPLEX consiste da combinação de uma camada de difusão obtida por processo de Nitretação com outra depositada por “PVD” (“Plasma Vapor Deposition”). A camada nitretada pode atingir profundidades de 0,010, ou superior a 0,100 mm (“camada de difusão”), sem a formação de “Camada Branca” (camada de nitretos precipitados na superfície de profundidade da ordem de milésimos de milímetros, com elevada dureza e propriedades físicas similares a uma cerâmica) e sobre esta aplicar o revestimento PVD que pode ser de diversos tipos, ou combinações, de nitretos, tais como TiN; TiNAl; TiNAlCr; etc...com espessuras de 0,002 a 0,008 mm, aproximadamente, cobrindo o “expertise” das diferentes técnicas disponíveis no mercado. A camada nitretada tem dureza intermediária para bem ancorar a camada PVD de elevada dureza e oferecer boa compatibilidade para o crescimento a partir da superfície. O núcleo do aço está temperado e revenido para menor dureza, geralmente de 58 a 64 HRC. As Figuras abaixo mostram as microestruturas de superfície “Duplex” de aço AISI D2, temperado e revenido, caracterizada por microscopia ótica e aumentos 100X e 1000X. Com menor aumento (100X) podemos observar o metal base e a camada nitretada, profundidade 0,070 mm. Com maior ampliação (1000X), torna-se possível observar uma fina camada de Nitreto de Titânio (TiN) depositada pelo processo PVD com espessura de 0,0035 mm sobre a superfície nitretada sem camada branca.
Figura: Superfície de aço AISI D2, aumentos 100 X e 1000 X. Ataque nital 4%
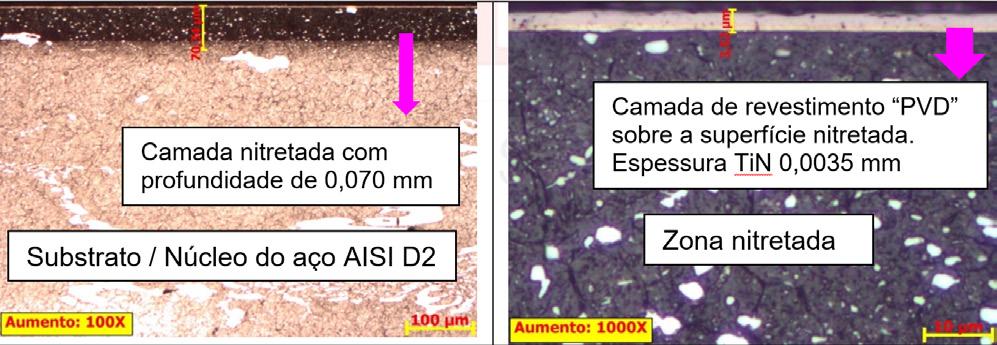
A Tabela 1 apresenta os resultados de dureza obtidos para esse aço no processo Duplex. Tabela 1 – Resultados de Dureza Vickers – aço AISI D2
Local Dureza [HV]
Substrato do aço (Revenido 3xs a 520° C) 674 Na camada nitretada (Nitretação 480° C) 1214 No revestimento PVD (450° C) 2400
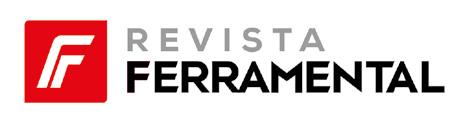

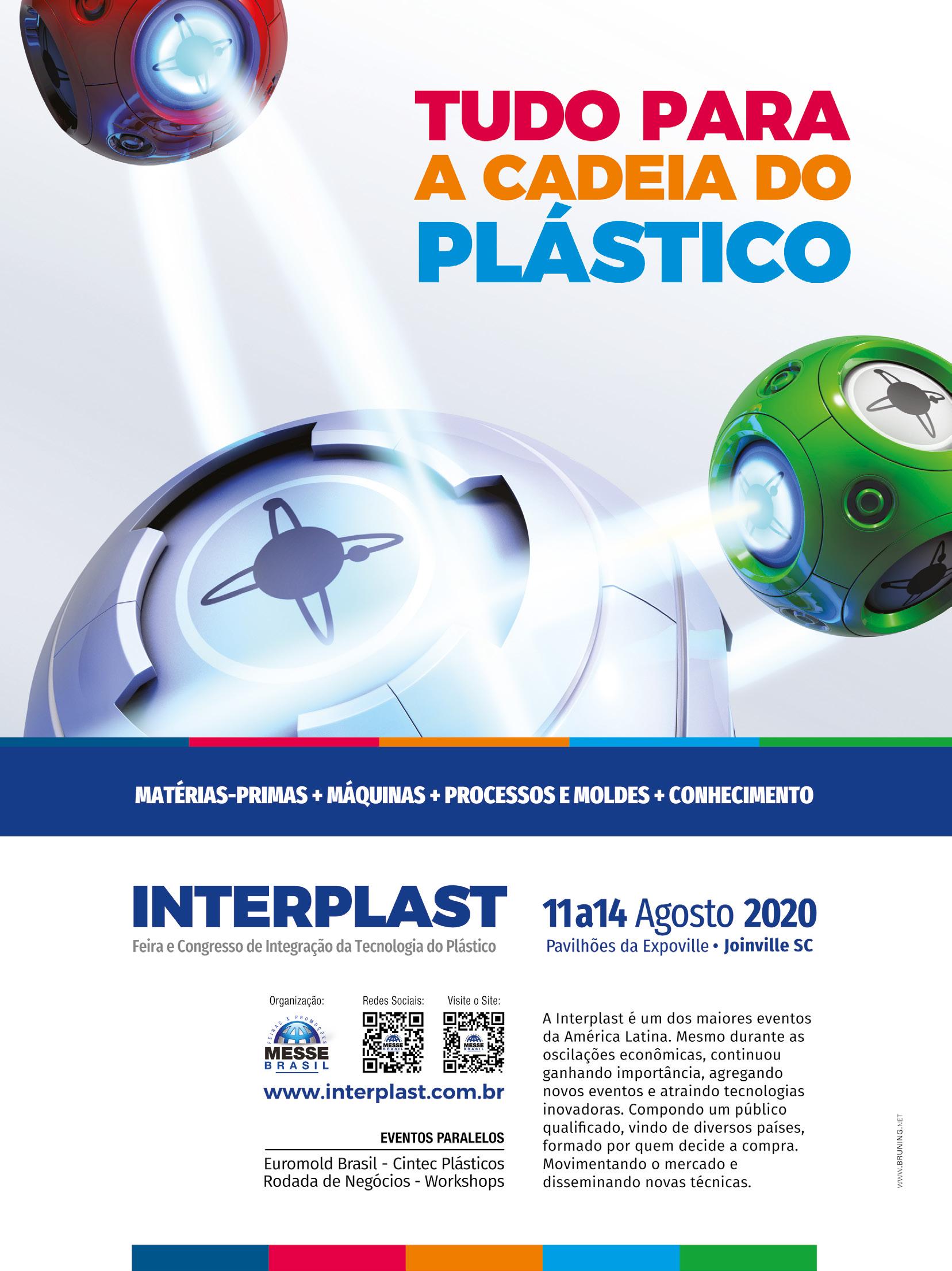
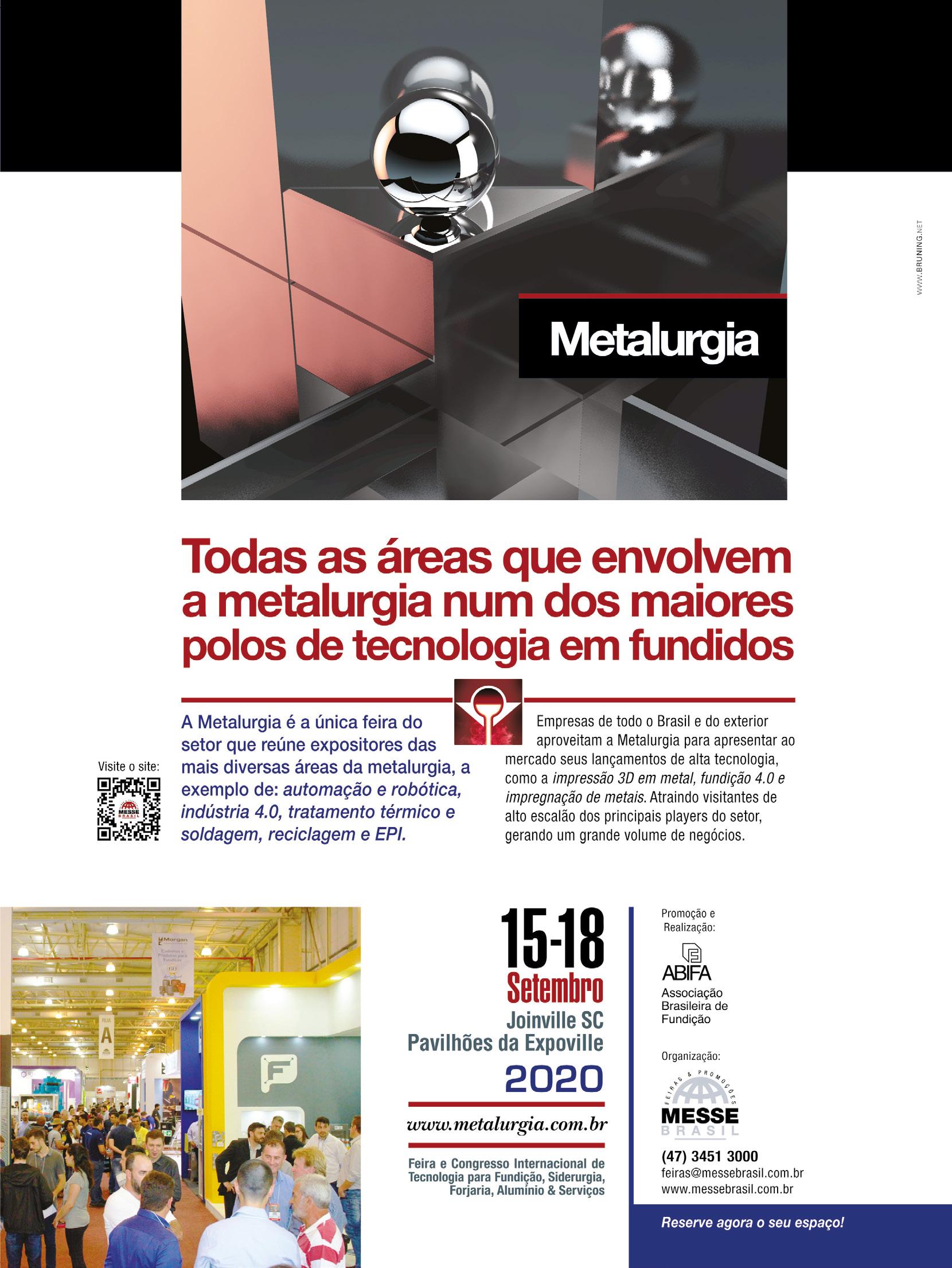