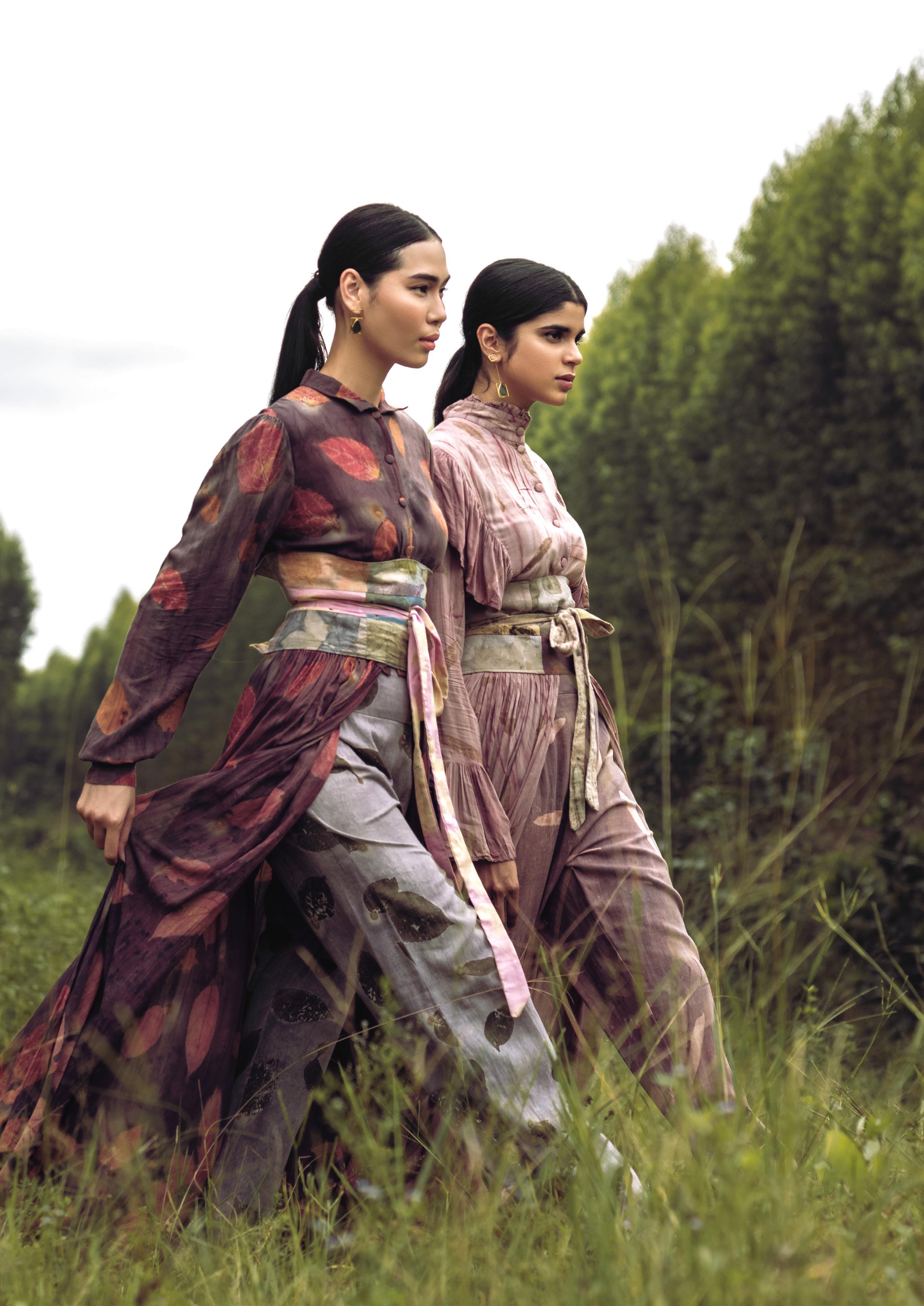
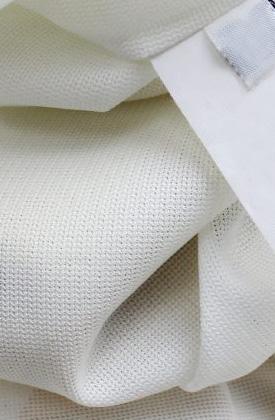
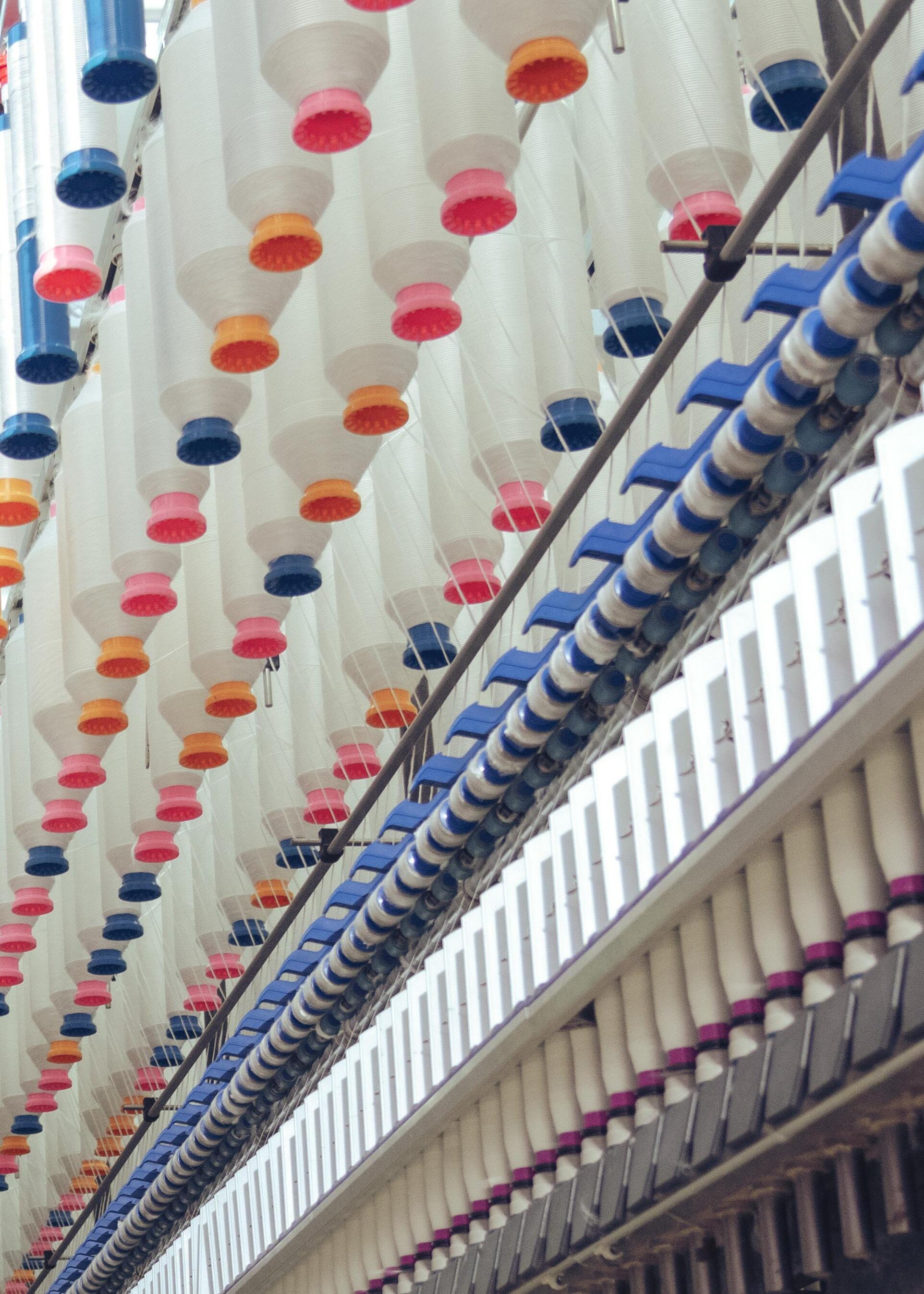
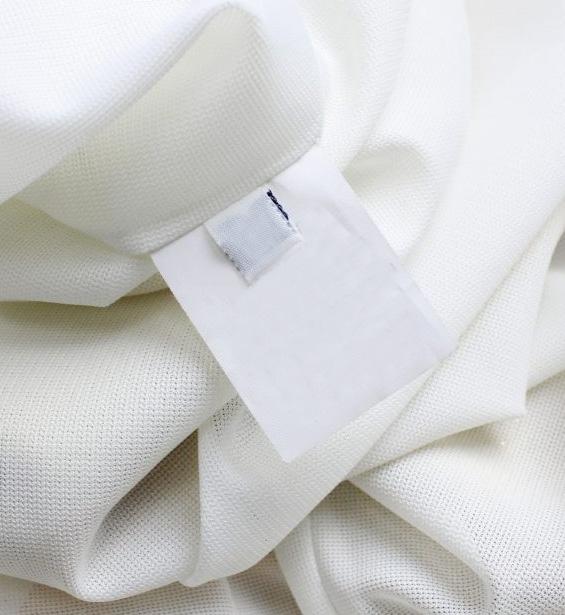
RGE is a group of resource-based manufacturing companies with global operations. Founded in 1973, our purpose is to improve lives by developing resources sustainably.
As a supplier of cellulosic fibres operating at the heart of the bioeconomy, our fibre-related businesses are vertically integrated from sustainably managed plantations to textile fibre and yarn production.
We are the world’s largest producer of viscose fibre with strong presence in Asia where textile demand growth intersects with the textile production hub, presenting a real opportunity to drive change.
Our deep expertise in the cellulosic fibre business and integrated capabilities allow us to have full control over product quality, accelerate scalable innovation through practical industry collaborations, and mitigate supply chain risks.
APRIL Group is one of the world’s largest, most productive and efficient producers of fibre, pulp and paper with plantations and manufacturing operations in Riau, Indonesia. APRIL manages over 440,000 hectares of sustainably managed renewable plantations and operates the world’s largest single-site pulp mill at 2.8 million tonnes of pulp annually.
Bracell is a leading manufacturer of dissolving pulp and specialty cellulose. From its eucalyptus plantations in Brazil, Bracell’s mills in Bahia and São Paulo are capable of producing up to two million tonnes per year of dissolving pulp. Bracell operates the world’s largest fossil fuelfree pulp mill in São Paulo.
Sateri is the world’s largest producer of viscose fibre, a natural and sustainable raw material found in everyday items like textiles, baby wipes and personal hygiene products. Its six mills in China produce about 1.8 million metric tonnes of viscose fibre yearly. It also operates a yarn spinning mill in Nanjing, and a growing lyocell portfolio in China.
Asia Pacific Rayon (APR) is the first fully integrated viscose staple fibre producer in Asia from sustainable plantations to viscose. Its 300,000-tonne mill, which is co-located with APRIL in Riau, Indonesia, uses the latest production technology to produce high-quality viscose fibres to meet textile needs.
Asia Pacific Yarn (APY) is a fully integrated viscose staple fibre yarn manufacturer located in Riau, Indonesia alongside APR. APY applies the latest yarn spinning technology to produce an annual capacity of 7,560 metric tonnes of high-quality yarn products or equivalent to a total converted capacity of 32,000 spindles with open-end-rotors, ring spindles and vortex positions.
Linz (Nanjing) is a maker of highquality viscose yarn products that are exported worldwide. Set up in 2007 and acquired by Sateri in May 2016 as part of its strategy to be closer to customers and improve quality, the advanced mill has open-end, vortex and compactsiro spinning technologies with a total converted capacity of 50,000 spindles.
Asia Pacific Rayon prioritises Indonesia as a source of textile waste for recycling following completion of study by Closed Loop Fashion and Reverse Resources.
Sateri becomes a member of the China Tourism Hotel Association to review potential for the collection of hotel linen for recycling in China.
RGE partners with the Singapore Fashion Council (formerly Textile and Fashion Federation) with the launch of its inaugural “Towards Zero Fashion Waste Market Study” sector report.
RGE launches the RGE-NTU Sustainable Textile Research Centre (RGE-NTU SusTex) with the Nanyang Technological University Singapore (NTU) in August 2022.
Sateri collaborates with the China Association of Circular Economy on the creation of standard technical specifications for the Waste Textile Sorting Centre system.
Sateri’s first 100,000-tonne per annum lyocell production line goes into operation in Changzhou, China.
When it comes to textile waste, the scale of the challenge is becoming more apparent by the day. Clothing and textiles are now being produced at a faster rate than ever. The fashion and garments industry accounts for 8-10% of global carbon emissions and is responsible for huge amounts of waste. It is also one of the main contributors of plastic mircrofibres entering our oceans due to non-biodegradable synthetic materials like polyester.
We must act immediately to move towards lowcarbon and low-waste apparel industry.
In this report, we outline the progress we have achieved over the last 12 months with our R&D efforts to accelerate the textile fibre innovations that can help advance the global sustainability agenda, both in-house and in collaboration with external partners. This is line with the increasing global momentum towards enhanced circularity in the textile value chain.
For example, industry leaders and policymakers at the recent COP27 meetings in Egypt were clear on the need to commit to the infrastructure needed for fashion circularity, which is critical to both reduce textile waste and address the massive carbon footprint of the fashion industry.
We became an active player in the field of next generation textile fibre development back in 2019 when we announced our US$200 million investment over the subsequent 10 years to scale up proven clean technology in fibre manufacturing; bring pilot-scale production to commercial scale; and in emerging frontier solutions.
Bey Soo Khiang Vice Chairman, RGESince then, we have rolled out long-term commitments across our business groups to increase the use of textile waste in production. By 2025, 20% of Sateri’s feedstock will contain alternative or recycled materials; by 2030, 20% of the fibre used by APRIL for viscose production will be sourced from recycled textiles, while Asia Pacific Rayon (APR) will use 20% of waste composition in viscose production.
As we recover from the pandemic, we continued to build on our existing R&D programmes,
particularly in the area of using waste as a raw material in a circular economy. Our collaboration with Nanyang Technological University, Singapore (NTU Singapore) to launch the RGE-NTU Sustainable Textile Research Centre will support the development of an urban-fit pilot textile recycling plant in Singapore that uses less energy and less chemicals to produce textile fibres from textile waste that can be exported and eventually made into new apparel.
We believe that such an upcycling approach not only addresses the transboundary waste movement, but is also a compelling operating model that has the potential to be replicated elsewhere in the region and help bring the industry towards a true circular economy. Partnerships like this can have a multiplier effect, in terms of their wider impacts on society, and we believe this kind of collaboration is essential to drive positive change.
To address the textile industry’s waste challenge, we partnered with a major Indonesian retail chain on a clothing trade-in programme, as part of our wider efforts to collect textile waste for our recycling project.
In addition to partnerships, we are continuing to invest in our own R&D to help innovate new concepts and technologies At our production base in Sumatra, Indonesia, we are carrying out testing of new viscose products and production techniques at our automated viscose pilot plant, which was completed two years ago.
As the world’s largest producer of viscose fibre and a global leader in the production of dissolving wood pulp, we believe we have a responsibility to advance circular economy concepts across the industries in which we operate. In terms of our activities and investments in this area, we have come a long way in a short space of time.
As the world intensifies its focus on delivering on sustainability and climate goals, we remain unwavering in our commitment to catalyse the development of next-generation textile fibre solutions, now and in the years to come.
“
“
We are continuing to invest in our own R&D to help innovate new concepts and technologies to address the textile industry’s waste challenge
Over the course of 2022, RGE continued to explore potential collaborations in the fields of textile innovation and sustainability in the fashion supply chain, while progressing its engagement with existing partners in areas such as textile recycling, alternative cellulosic feedstock, microbial and agricultural waste, and clean solvents.
The collaboration between RGE and Nanyang Technological University, Singapore (NTU Singapore) in 2022 is an example of the kind of partnership that the company is targeting, providing successful outcomes for the participants, while also having positive impacts on the environment and society at large. Researchers at the new RGE-NTU Sustainable Textile Research Centre (RGE-NTU SusTex) will develop new technologies to recycle textile waste into fibre and create new sustainable textiles.
RGE also plans to bring the technology developed by RGE-NTU SusTex beyond proof of concept to production in the coming years by building a low carbon, chemical and effluence textile recycling plant in Singapore that can convert local textile waste into new raw material for use in, or export from, the city-state.
A key element of the company’s approach to partnerships is the principle that multi-stakeholder collaboration is required to increase momentum towards circularity in the textile sector. Only through engagement with multiple actors will it be possible for the company to support innovation in textiles at commercial scale, while maintaining or improving on consistency in quality.
As well as partnerships, RGE continued to review investment opportunities in projects that could potentially benefit from the company’s support. This approach goes back to the initial stages of RGE’s journey in the textile innovation field in 2019, when the company announced its investment in Infinited Fiber Company Oy to scale up its technology to turn textile waste and other pulpbased materials into new textile fibres.
RGE’s investment review process takes into consideration a number of variables, including scale-up risks, commercial feasibility, and overall fit with the company’s existing operations and long-term business model. The investment process combines investment discipline with industry knowledge and includes a Technology Readiness Level framework, which provides clarity on potential risks.
In 2022, Asia Pacific Rayon entered into a collaboration with U.S. company Sustainability Ideas on a form of next generation cellulose with potential application in viscose manufacturing. Sustainability Ideas has developed a patented biotech fermentation process for cellulose extraction from food and other bio-waste. The company is also exploring testing on zinc and bio-sludge from APR to determine whether they can be turned into fertiliser or animal feed, using the patented process.
In 2022, Asia Pacific Rayon announced a partnership with Indonesia’s largest retail platform, Matahari, to launch a new textile waste management programme. The programme, which is part of Matahari’s ESG Sunrise Project, encourages Matahari’s customers to participate in reducing textile waste through a recycling programme. In the first phase, the programme has focused on the trade-in of Nevada Denim clothing at three Matahari stores located at Supermal Karawaci at Tangerang, Metropolitan Mall at Bekasi and Ciputra Mall at Jakarta.
Sateri continues to engage with Södra and is exploring the potential for joint sourcing of raw materials in China. In 2022, the two companies reached an agreement eached an agreement to conduct studies to test the quality of waste linen recycled from the hotel industry in China.
In 2022, Sateri collaborated with Renewcell on the recycling of 36 metric tons of waste material. The target is for trials to convert up to 50% of this material to recycled content. A Memorandum of Understanding was signed between RGE and renewcell in 2019 for technical cooperation and trials on production of viscose using recycled cotton, with the aim of industrial scale production by 2025.
A major breakthrough in 2022 was the launch of the RGE-NTU Sustainable Textile Research Centre (RGE-NTU SusTex). Developed in partnership between RGE and Nanyang Technological University, Singapore (NTU Singapore), RGE-NTU SusTex was set up to drive
innovation in textile recycling and to translate research outcomes into practical solutions, in line with Singapore’s Zero Waste vision, and the Singapore Green Plan 2030.
The new facility was launched in August in the presence of Grace Fu, Minister of Sustainability and the Environment, Republic of Singapore, Professor Subra Suresh, President, NTU, Anderson Tanoto, Managing Director, RGE and other senior management from RGE.
RGE-NTU SusTex now has seven research staff led by four principal investigators from NTU’s School of Materials Science and Engineering and the School of Chemistry, Chemical Engineering and Biotechnology. A high temperature gel permeation chromatograph - one of only three in Singapore -a viscose spinning machine and various textile-related analytical instruments have been installed.
During 2022, the team achieved progress a number of areas, including the development of a novel waterless method for separating polyester from cotton in army uniforms, progressing from bench experiments to litre scale reactors; a better understanding of the efficacy of using plasma to assist the decolouration of dyes
without chlorine; a promising discovery of stable micro-organisms from Singapore’s Pulau Semakau landfill which may be used decolour dyes biochemically; and a technical disclosure filed for separation of mixed fibres using density differences.
The progress achieved by the researchers will lead to larger scale experiments and/ or processing plants, as well as finding customers for the advanced materials that will be formulated. The team is also collaborating closely with researchers at the RGE Technology Centre in Riau, Indonesia, with analysis and data being shared to help further drive research outcomes.
• Cleaner and more energy efficient methods of recycling and fibre separation: looking at greener ways of textile recycling, with a focus on cellulose-based fabrics including rayon, viscose and cotton, minimising the degradation of fabric properties, and refabricating textile waste into fibre;
• Automated sorting of textile waste: using a combination of advanced spectroscopic techniques and machine learning capabilities for identifying and sorting textile waste based on fibre composition, and developing an automated system to remove accessories such as zips and buttons;
• Eco-friendly dye removal and natural dye development: developing eco-friendly methods of removing dye from textile waste using little to zero chlorinated chemicals, and formulating greener and biodegradable dye substitutes;
At present, the three main research areas for RGE-NTU SusTex are:
RGE-NTU SusTex was set up with the aim of translating research outcomes into practical solutions that can be deployed in urban settings like Singapore. How will this work in practice and complement the planned pilot textile recycling plant by RGE in Singapore? To complement RGE’s planned recycling pilot plant, RGE-NTU SusTex has already started planning for a plug-and-play demo scale pilot with multiple reactors, which not only accelerates the technology development, but also allows us to compare technologies through life cycle analysis and cost analysis.
There are already a number of textile recycling technologies in the market. How is the technology being developed by SusTex unique or different from the rest?
We have been given a worthy challenge to develop urbanfit technologies to attain better circularity in the value chain of the fashion industry. Our initial priority is to assist RGE to develop, assess and adapt textile recycling technologies that generate less wastewater and use less chemicals. New ways of recycling and reusing chemicals and solvents are also being explored.
The current textile recycling technologies in the market have largely been focused on the chemical and mechanical processes. Has SusTex looked into bio-based processes and why?
RGE-NTU SusTex adopts an open and yet critical mindset in assessing and exploring all possible approaches, and these include mechanical, chemical, and biological processes. While we focus our resources on developing indigenous innovative technologies, SusTex is also establishing partnerships with industrial and academic leaders to expand our horizon and outlook.
For example, RGE-NTU SusTex has already attracted collaborative proposals, ranging from mechanical recycling to enzymatic processes, even though they may have very different levels of sophistication and technology readiness. There is already an ongoing effort on microbial assisted colour removal from textile waste.
What are the challenges involved in deploying textile recycling at scale?
Textile waste is intrinsically complex because of the blended fibres, which not only may contain cotton, polyester and spandex, but also a variety of dyes, pigments and surface finishings. There are both technical and non-technical challenges in deploying textile recycling at scale - i.e. collection and steady supply of textile waste, accurate and effective sorting, availability of cost-effective upcycling technologies and maximizing the values of the main products and both the main by-products.
What are the key success factors for scalability to become a commercial
Forging the right partnerships and having a sound business model are critical factors for commercial
Approximately 45% of the textile produced In China is wasted, ranging from waste generated during production to waste created by the enduse. It is expected that textile waste in China will exceed 100 million tonnes annually in the coming years.
In 2022, Sateri played a leading role in the development by the China Association of Circular Economy (CACE) of a standard technical specifications for the planned Waste Textile Sorting Centre system. This followed the move in early 2022 by the National Development and Reform Commission to issue a new policy to accelerate the construction of the recycling system of waste materials.
The policy proposed that by 2025, a waste materials recycling network system will be established, and more than 1,000 green sorting centres will be built. The new standard will help to progress textile waste recycling and sorting technologies in China, and will ultimately address the country’s need for waste material recycling systems. The standard is expected to be finalised in 2023.
China National Textile and Apparel Council Sateri remains closely engaged with the Textile Recycling Innovation Research Project initiated by the China National Textile and Apparel Council and H&M Group. The project is aimed at advancing research into the recycling of textile materials, including cotton, polyester, cellulose fibre, nylon, acrylic fibre and elastane. Sateri participated in the project’s MMCF (Man-Made Cellulosic Fibre) group to share its experience with the production of FINEX™, Sateri’s cellulosic fibre containing recycled content derived from a mix of recycled pre and post consumer textile waste, and of other certified-wood pulp from renewable plantations.
In July 2022, Sateri became a member of the China Tourism Hotel Association. This has provided a significant opportunity to better understand the potential for textile waste recycling in China’s hotel industry.
A study published by the China Association of Circular Economy (CACE) in 2022 highlighted the scale of the opportunities involved in collecting and using hotel textile waste linen for recycling.
The study highlighted the large volume of post-consumer cotton textile waste - commonly referred to as ‘linen’generated by the hotel industry, up to more than 170,000 tonnes per year prior to the COVID-19 outbreak. Despite the pandemic, collected volumes of post-consumer cotton textile waste in the hotel industry in China still reached 100,000 tonnes in 2020, which is only a very small portion of collectable volume overall.
The volume of post-consumer textile waste generated by hotels has steadily increased over the years. Most of this waste is white cotton or high cotton content without need for decolorisation, according to the study. Not only is the process more environmentally-friendly and shorter, but also the collection process more centralized, making it an ideal raw material for regenerated cellulose fibres, said the report.
International dissolving pulp producers have made headway in pulp-making technology, so that the raw materials for regenerated cellulose fibres are no longer limited to preconsumer cotton offcuts, and have expanded to postconsumer textile waste. However, restricted by factors such as insufficient supply of textile waste and unstable quality, the supply of dissolving pulp produced from textile waste limited.
China’s hotel industry is able to sustainably supply postconsumer cotton textile wastes for the production of dissolving pulp both in terms of quality and quantity, if the correct infrastructure is in place. The study found that China’s hotel industry is looking for opportunities and partnerships for sustained utilisation of its large volume of textile waste.
The study also indicated that there are few policy barriers between China and the European Union (EU) countries for the import and export of used hotel linens. Our strategic supply partner Södra Group is ready to use linen acquired from the China hotel industry as raw materials for trial production of recycled dissolving pulp. If successful, this will be a noticeable breakthrough and best practice for coordinated development in circular economy in textile industry across continents.
RGE has built up its R&D capability in the textile fibre field across its different business groups in Brazil, China and Indonesia in recent years. The group’s key advantage is its expertise across dissolving pulp, viscose, lyocell and yarn spinning, which allows for the harnessing of synergies along the cellulosic fibre production value chain.
RGE has continued to build its R&D capability across its various business groups to drive the Group’s commitments help drive the Group’s commitments to invest in the development of next-generation cellulosic textile fibres that are closed-loop, circular and climate-positive.
Sateri continues to focus on the R&D of Lyocell development at its R&D Innovation Centre in
Shandong, China. Opened in 2020, the Centre focused on production and operation technology innovations, differentiated new product development, and fibre application technology development. The R&D team has also developed and optimised a variety of Lyocell dissolving pulps to support increased production.
Located within APR’s and APRIL’s manufacturing complex in Pangkalan Kerinci, Riau, Indonesia, the group uses its automated viscose pilot plant, built in 2020, to explore the development of new products. In 2022, the plant was also used to test new sources of fibre from recycled textiles and agricultural residuals. The plant was designed to simulate the entire viscose manufacturing production cycle on a much smaller scale, enabling more efficient testing of new products and production techniques.
Over the last three years, RGE R&D teams carried out trials, mixing pulp with 50% recycled textile content into regular dissolving wood pulp for viscose production.
These trials will be further enabled by the rollout of a fully automated textile recycling pilot plant in Kerinci, Riau, Indonesia which models the entire viscose manufacturing process. The new pilot plant is likely to be operational in the next 18-24 months.
At the same time, in the development of differentiated fibre products, the unique crosslinked fibre development has also achieved good pilot results and will soon be put on the market. Based on the development tasks and needs of the previous stage, the R&D team has completed the necessary key support tasks in the past two years.
The R&D teams have also carried out tests using Stardust, a metal oxide-based material that can be used as a tracer element for fibre. Preliminary studies were done at the viscose pilot plant to produce Stardust-containing fabric. The tracing element was detected in the fabric and it shows potential implementation for tracing purpose and brand protection. However, further optimization is required to improve the uniformity of the tracing element throughout the fibre.
The R&D team in Indonesia is are also investigating the reuse of other process additives, such as zinc, to enhance recovery and recycling of chemicals. Initial trials by solution providers in 2022 yielded positive results and the team will continue to study the feasibility and potential to scale the technology to further support circular integration in manufacturing.
FINEX™ was introduced by Sateri as its leading brand for textile fibres containing recycled content. The company has obtained the Recycled Claim Standard (RCS) certification which provides verification of recycled materials through the supply chain. Sateri has successfully produced FINEX™ viscose fibres with up to 50% recycled content.
Sateri’s capability to produce FINEX™ using a 35,000-tonne per annum commercial production line means that the company can scale up production in line with market demand. FINEX™ fibres are also compatible with existing spinning technologies, ensuring stable yarn production without the need to adjust existing processes or parameters, and delivering excellent spinning efficiency, yarn evenness and tenacity.
What inspires you about your work?
I am responsible for Sateri’s research & development and one of the major upside of working with innovation is that life is never boring. There is always a new challenge waiting, and an opportunity to make a better product. At Sateri’s R&D centre, we draw our motivation from the fact that every single improvement that we make in our fibres ultimately helps consumers and the environment. We strive to maximise the value of the resources by keeping them in use for as long as possible. This includes circulating materials and keeping their intrinsic value as components and raw materials, which not only help the company save costs, but also reduce environmental pollution and carbon footprint. The value our work brings to the environment and consumers inspires me and my team to create new and differentiated products to the marketplace.
What were the challenges in developing FINEX™?
We always strive to maintain a high quality standard for our produced fibre, and for recycled fibre, the expectations are the same. Since the feedstock for FINEX™ is different from regular raw material, we faced some challenges to maintain the high fibre quality standard as well as finding the right efficiency for the production process. we overcame these challenges and launched FINEX™ which is not only of superior quality but also cost-efficient. We are now capable of scaling up production to respond to market demand.
What market dynamics do you see in the sector?
I really like how the MMCF (Man-Made Cellulosic Fibre) sector is focusing on product and process innovation, and I think it will only get better. The increasing interest and demand for circular products made with recycled and alternative feedstock as well as innovative and alternative production process is quite encouraging. The demand for circular and carbon-efficient fibres is also gaining traction and we are happy to contribute with our products. A steady market demand is necessary to help scaling up the production of innovative products.
How does your work contribute to a climate positive future?
Our recycled fibre will effectively contribute to reduce the use of virgin resources and furthermore, our high efficiency EcoCosy® BV series fibres are able to increase the efficiency of the spinning process of the downstream partners. We will continue our efforts to offer new innovative products that will benefit consumers and the wider textile industry.
Lyocell is a natural and biodegradable fibre made from wood pulp sourced from sustainable plantations. Lyocell is manufactured by Sateri using closed-loop technology, requiring minimal chemical input during the production process. The organic solvent used in the manufacturing of lyocell is nearly fully recoverable and reusable.
In May 2020, Sateri completed its first 20,000-tonne per annum line and commenced Lyocell production in Rizhao, Shandong, China. In October 2022, the company’s first 100,000-tonne per annum line went into operation in Changzhou. Sateri’s lyocell products are manufactured in line with the EU’s ‘Chemical Registration, Evaluation, License and Restrictions’ regulations. Sateri regards Lyocell as a key product for the company’s future development, with a total planned annual capacity of up to 500,000 tonnes by 2025.
In July 2022, APR made a strategic decision to proritise Indonesia to source textile waste for recycling. This followed the completion of a study by Closed Loop Fashion Consulting and Reverse Resources to survey, map, and identify potential sources of pre-consumer textile waste supply from textile factories in Indonesia, Bangladesh and Sri Lanka. All three are major textile and apparel producing countries.
Researchers for the study conducted interviews at 106 factories, waste-handling facilities, and recycling plants in Indonesia, Bangladesh and
Sri Lanka to understand their sources. The study assessed different types of recovered waste, including landfill gas, and repurposed waste. At the same time, researchers worked to identify the best textile waste for recycling efforts. The study also focused on the availability of high-value waste, like 100% cotton, and low-value waste, like blended textiles such as polycotton.
The study found that Bangladesh and Indonesia are excellent sources of recyclable material. Together, the two countries produce 340 kilotonnes per year of 100% cotton and 286 kilotonnes per year of polycotton. Bangladesh is home to a robust but informal textile scrap market, with large producers already separating and selling their waste. The country is also a producer of pure white cotton that is ideal for high-quality recyclate. Indonesia, on the other hand, is not a cotton-producing country.
Indonesia requires further development of waste segregation systems at factories, better local logistical infrastructure, and a pricing structure to support a local waste resale market.
Based on the findings of the study and a number of other factors, such as the location of the company’s operations and priority markets, APR’s focus for 2023 is to develop local frameworks that support small businesses and improve livelihoods, and to invest in infrastructure to allow for the processing of recycled textiles locally. The company also plans to progress collaboration with a number of different sorting partners, while mapping the viability of different types of preconsumer textile waste.
“The tight integration of APR’s and APRIL’s operations from plantation fibre to sustainable viscose fibre is a testament to our innovative spirit. Our Kerinci complex produces pulp, paper, viscose and yarn. To identify and operationalise opportunities and drive efficiencies across the board, we continuously invest substantial sums in R&D to improve yields at APRIL’s plantations and optimise operations at our processing plants.
APR has set a target of using 20% recycled textiles in our operations by 2030. Our R&D team possesses the requisite expertise, so this target is well within our reach from a technological standpoint. Our team is focused on finding solutions to current barriers by rethinking and understanding the costs involved in sourcing, collecting, and separating raw materials, among other things.
These solutions are within reach, but we have to scale them across the value chain. To this end, our tight integration and cradle-to-gate oversight put us in a unique position to promote sustainability and circularity locally and internationally. Unlike our competitors, we can build the capacity to process and source recycled materials internally.
We can then mainstream the use of recycled material by sharing our expertise with our entire value chain. However, to truly advance the industry’s sustainability targets and circularity vision, manufacturers cannot shoulder the burden alone. All industry players, including fashion brands and consumers, must collaborate to integrate circularity into the textile sector.
We must jointly rethink manufacturing, marketing, and design decisions to improve the collection and sorting of recycled materials, leading to true circularity. APR is exploring partnerships across the value chain and textile markets to learn from our peers, adapt our processes and work together towards our shared sustainability goals”.
1. Investment amount in Infinited Fiber Company is bound by agreement confidentiality
2. Total expenditure for 2021 is restated due to reclassification of partnership with Textile & Fashion Federation