
9 minute read
Leading the (ex)change
As the UK prepares to host the COP26 conference of parties to the UN Convention on Climate Change, there are some big questions the nation’s construction industry is having to address
WORDS ALEX REEVE, WENDY BISHOP AND LUCY TOWNSEND
Advertisement
A project is now under way in Cambridge that should help provide answers to some crucial questions. Can renewable energy capacity expand fast enough to meet our heating demands? How can we limit the carbon impact from construction materials? Can we adapt our existing buildings to fulfil our needs and promote our wellbeing over the long term?
The aim is to create a visionary new headquarters for the University of Cambridge Institute for Sustainability Leadership (CISL). It will be known as the Entopia Building and involves retrofitting a 1930s former telephone exchange at 1 Regent Street, Cambridge. As well as CISL’s Cambridge-based staff, the building will house a sustainability hub and accelerator supporting small businesses and start-ups.
Background
The overall project budget is £12.8m, made possible by a £6m donation from greentech leaders Envision Group and a £3m grant from the European Regional Development Fund, which is also funding the operation of the sustainability hub and start-up accelerator for three years. This will foster collaboration, capacity building and knowledge transfer between industry experts, researchers, and major companies. The University has also invested its own funds in the project alongside an internal grant from its Energy and Carbon Reduction Project.
The building name references the Entopia concept developed by Envision to shape a future where access to clean, secure and affordable energy is available to all.
Saving CO2 emissions embodied in the construction process

Brief
The project intent is to be a world-leading exemplar of sustainable retrofit. This is reflected in a brief developed by CISL Fellow Professor John French, who previously led the design and build of the award-winning Enterprise Centre at the University of East Anglia, demonstrably one of the most sustainable office buildings in the UK. Key targets include: No fossil natural gas Passivhaus standard for refurbishment (known as EnerPHit) Highest possible BREEAM environmental assessment rating of 'Outstanding' Embodied carbon at less than 300Kg CO2/ m2 over 100-year life of the building Project to form a case study for promoting the circular economy 70% of material used to be biobased Soft Landings and post-occupancy evaluation to enhance performance and provide feedback Project to be replicable Health and wellbeing to be promoted by achieving WELL Gold certification
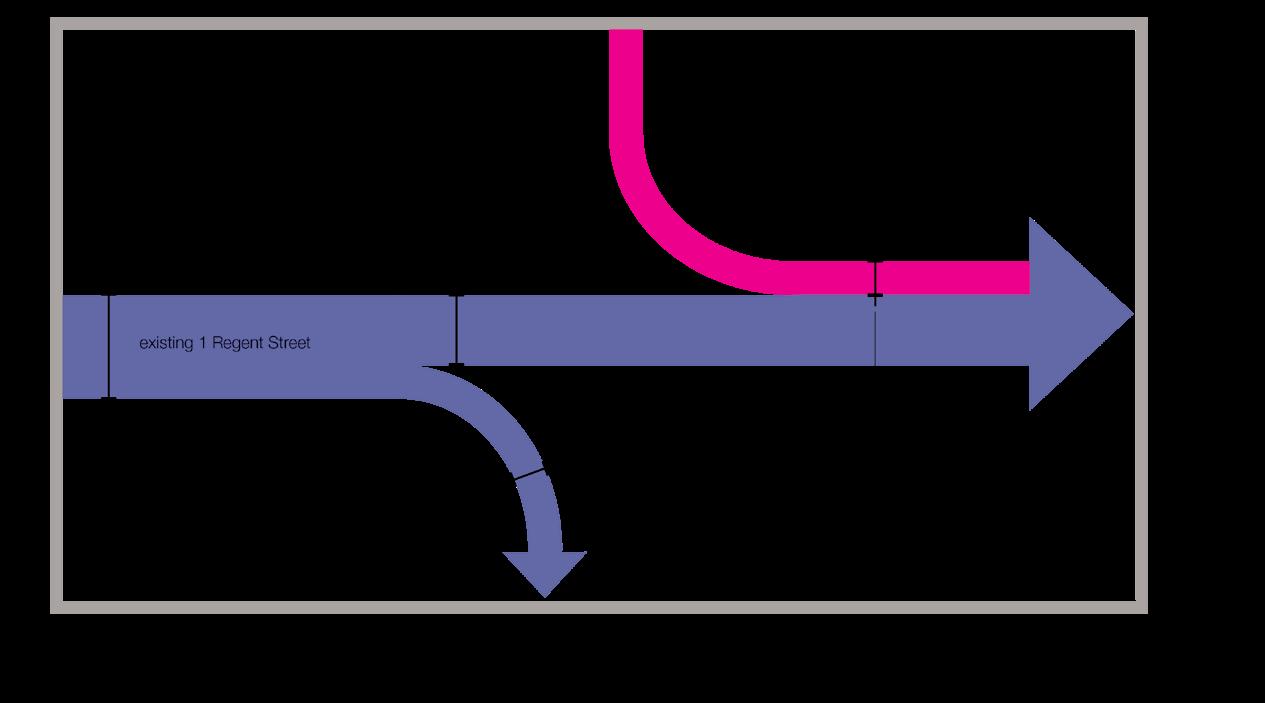
Wendy Bishop, architect at Architype, writes
The building’s existing fabric is being enhanced to meet the EnerPHit criteria of less than 25 kWh/m2 per annum heating demand, and an airtightness of less than 1 air change per hour at 50Pa. As well as exemplary energy efficiency, the EnerPHit and WELL standard offer considerable air quality, health and wellbeing benefits.
The solid masonry walls are being insulated internally, as the building lies within Cambridge’s central conservation area. Following design development, a thin layer of Diathonite (an insulating plaster using natural cork) is being used on the existing walls, preventing moisture being trapped within the wall construction, as well as providing an effective airtightness layer. This is followed by wood-fibre based insulation and the internal finish. Roofs, the lowest floor slab, and the basement retaining walls are also being insulated, with some complex detailing to ensure continuity of the insulation line, and to minimise heat loss through thermal bridges.
The non-original, single-glazed sash windows are being replaced by Passivhaus-certified tripleglazed windows, with the frame sitting in line with the internal insulation and recessed behind the existing structural opening. Designed to maximise energy performance and daylighting, it offers the optimum internal environment solution. The window change caused debate with planners because of the historic context, but the energy efficiency and daylighting benefits, as well as the impact on wholelife carbon (operational carbon savings dwarfed the extra embodied carbon associated with extra glass) proved persuasive to the planning committee.
Architype has used ECCOlab software to analyse embodied carbon. The initial target of 300kg CO2e/m2 over a 100-year life was ambitious and the modelling is under review. The client’s brief to maximise natural bio-based materials overlaps with minimising embodied carbon, and timber, cork and sprayed cellulose acoustic insulation to soffits have been used where appropriate, although the team has been cautious of adding extra material if not needed. The contractor (ISG) has been able to identify lots of opportunities for sourcing reused materials, so the completed building can demonstrate the principles of the circular economy through extending the life of the building structure, as well as with the reuse of light fittings, reclaimed steel sections, recycled paint, and repurposed furniture, among others.
second
first
ground
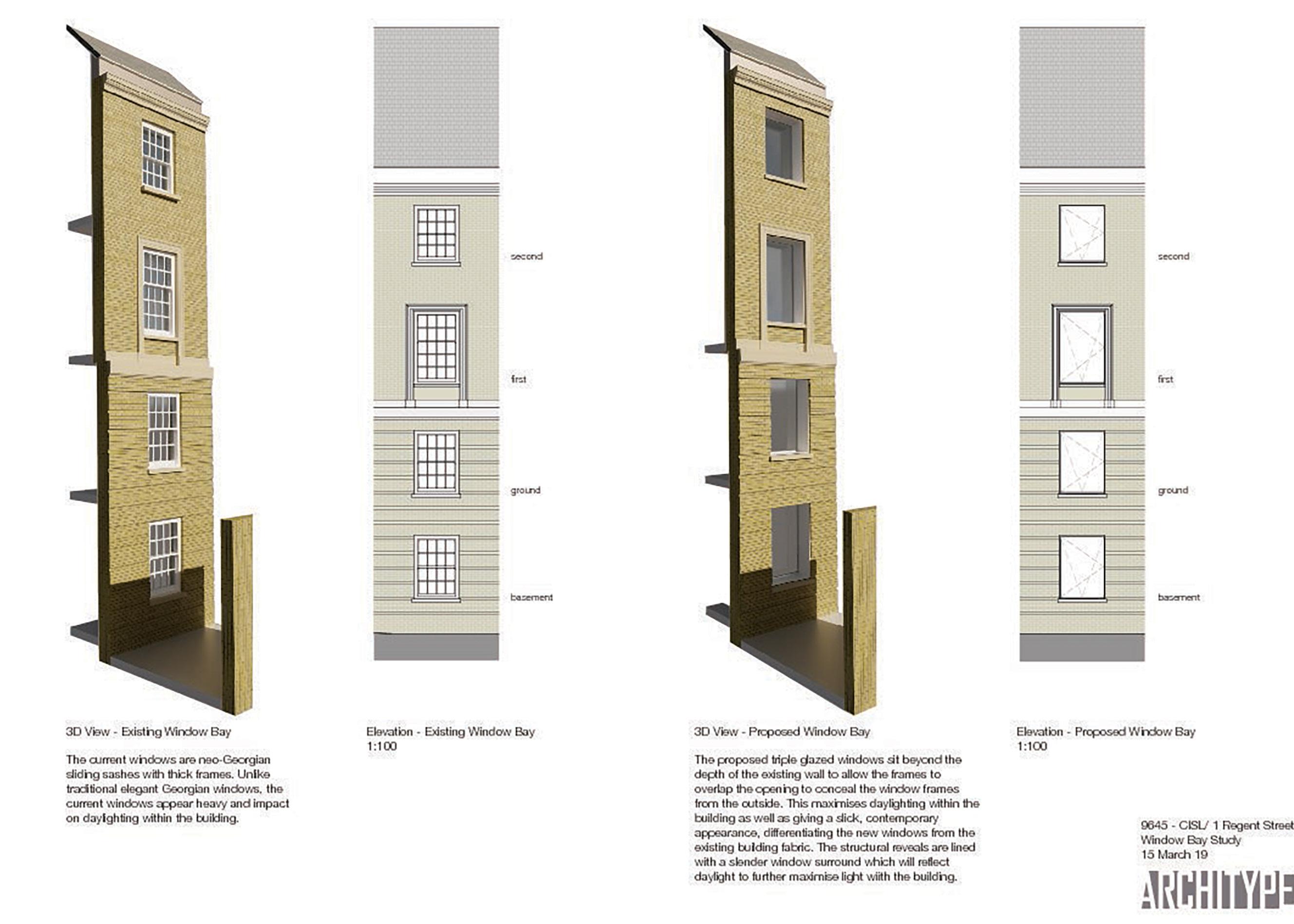
basement second
first
ground
basement
3D view – existing window bay The current windows are neo-Georgian sliding sashes with thick frames. Unlike traditional elegant Georgian windows, the current windows appear heavy and impact on daylighting within the building.
Exploring sustainable window design
Elevation – existing window bay 3D view – proposed window bay The proposed triple-glazed windows sit behind the existing wall line, concealing the window frames from the outside. This maximises daylight within the building as well as giving a contemporary appearance, differentiating the new windows from the existing building fabric. The structural reveals are lined with a slender window surround which will reflect daylight to further maximise light within the building. Elevation – proposed window bay

Smith and Wallwork Ltd
50 St Andrews Street, Cambridge, CB2 3AH www.smithandwallwork.com 01223 750 249 contact@smithandwallwork.com
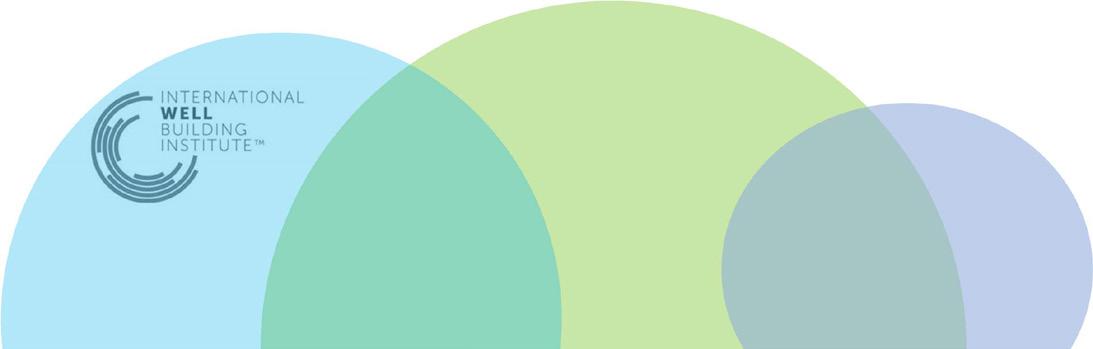
Lucy Townsend, sustainability associate at BDP, writes
Energy Efficiency Passive Design

Conventional retrofits tend to focus on isolated system upgrades (in other words, lighting, windows or HVAC equipment). These retrofits are generally quick and simple, but often miss opportunities for larger and more cost-effective energy savings, increased comfort and durability.
Deep energy retrofits achieve much greater energy efficiency by taking a whole-building approach, addressing many systems at once. For buildings with particularly poor energy performance, with multiple systems nearing the end of useful life, the most convenient and economical approach can be to upgrade everything at once.
When Entopia is completed, it will provide estimated annual energy savings of up to 80% a year when compared with the existing baseline energy use (calculated using utilities meter readings consumption). An Energy Performance Certificate of ‘E’ is expected to become an ‘A’.
The heating strategy for the building is based on fabric first principles that have become synonymous with the Passivhaus standard. A wellinsulated, airtight approach is used to reduce heat demand, meaning a small-scale, all-air system can be used effectively.
The primary heating and cooling to the building is provided via the central ventilation systems air handling unit (AHU), which is fitted with an integral reverse cycle heat pump that operates in heating or cooling modes. This type of all air system on a smaller scale is really only possible when utilised in conjunction with the exacting fabric efficiency measures and quality assurance required by the Passivhaus/EnerPHit Standards.
Secondary heating and cooling is provided in the form of electric panel radiators and variable refrigerant flow fan coil units (FCUs). This offers some additional control trimming or supplementary cooling when required, though generally limited to cellular offices, meeting spaces and designated conference spaces.
Demand-control ventilation is used for an element of zonal control, while optimising the individual flowrates required for each space and this ultimately leads to a reduction in fan power and energy consumption. The central ventilation AHU is operated and controlled by variable air volume

Energy consumption
Pre-refurbishment based on 2017 and 2018 utility bills Prediction
Air Quality Thermal Comfort Commissioning
Mental & Physical Health Materials Circadian Lighting Amenities Drinking Water Active Travel Responsible Food Visual Comfort Lighting Ergonomic + Active Furnishing Water Conservation Restorative Spaces Site Selection Access to Nature Acoustics Community Waste Nutritional Standards Consultation New Parent Support POE Responsible Construction Whole Life Costing Durability Safety Material Optimisation Functional Adaptability Security Flood Risk Light Pollution Noise Pollution Material Reuse/Recycling Lifecycle Carbon CIRCULAR ECONOMY
BIO-BASED MATERIAL
Protecting Ecology Impact of Refrigerants Adaptation to Climate Change EMBODIED CARBON
Intersections between the sustainability standards targeted
(VAV) mechanical control dampers, linked to room temperature and CO2 sensors.
Although active cooling is via the AHU's integrated heat pump and supplementary FCUs, these are modestly sized. The building has not been designed to supply full air conditioning to maintain temperatures at 21°C, instead a peak lop strategy is deployed in conjunction with other passive measures; such as using the buildings exposed ceiling soffits for thermal mass, night- purge ventilation and natural ventilation via openable windows.
Because of the relatively small domestic hot- water demand the project will use electric showers, and a mix of instantaneous and point-of-use water heaters for basins and sinks, respectively. This aligned with the project aspiration to do away with mains gas, and going to an all-electric building.
A rooftop photovoltaic canopy will offset some of the demand.
Entopia is on track to gain world-leading sustainability and wellbeing certification from BREEAM (Outstanding) and the WELL Building Standard (Gold), demonstrating how an existing office building can be made highly energy efficient in its redevelopment and use, while supporting the enhanced wellbeing of staff and visitors.
The project is also applying ‘circular economy’ principles to minimise the volume and impact of resources used in the building. A practical example of this involves the contractor (ISG) sourcing existing lighting from another building refurbishment that has involved the re-testing and the re-issuing of warranties of more than 350 LED lights.
Gas (KWh/m2 GIA /yr)
223
Zero Electricity (KWh/m2 GIA /yr)
140
57.5

Providing leadership
A key question will be how replicable various aspects of the project will be? To help promote this, CISL and the University’s Estates Division will be working to provide detailed case-study information on energy, material choices, and health and wellbeing targets as works progress.
Keep an eye out for articles in the trade journals and on the CISL website: https://www.cisl.cam.ac.uk/about/ entopia-building
Key members of the project team Primary funder: Envision Group Co-funder: European Regional
Development Fund Co-funder and building owner: University of Cambridge Primary user: Cambridge Institute for
Sustainability Leadership Architect: Architype Buildings Services Consultant: BDP Project Manager: 3PM Cost Manager: Gardiner & Theobold Passivhaus Consultant: Mead Consulting BREEAM & WELL Assessment: BDP Main Contractor: ISG
www.fgould.com @fgouldconnect Faithful+Gould

World leading project and programme management consultancy
Cost Management Programme Management Project Management Project Controls Building Surveying Health & Safety Services Sustainability