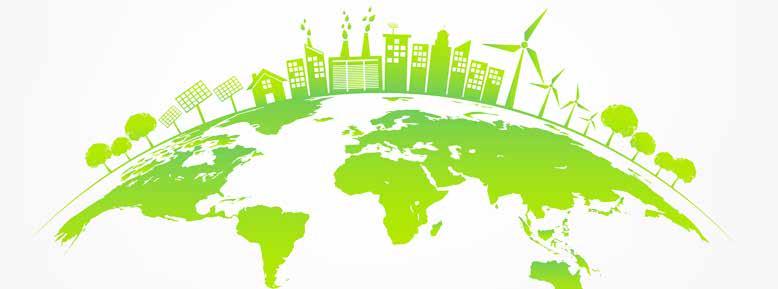
14 minute read
Climate Change
The Urgent Need For Change
BY JASON F. MCLENNAN
Buildings and construction are the number one causes of the climate crisis, accounting for 39 per cent of global emissions. The industry is continuing to grow at an alarming rate; by 2060 the world will be adding the equivalent of New York City monthly — in new construction. With the magnitude of impact the industry has on the world there is an immediate and urgent need to make a fundamental change to how we design and build everything. We don’t have a choice but to move to a place of disruption in the industry.
The recent extreme weather events around the world — heat waves and increasing forest fires, rising sea levels and global droughts — is proof of the now, evident runaway climate effects of the way we have been living our lives for the past century. We must realize these crises are no longer in the future for other generations to solve. We need to disrupt the industry and look to deep green construction methods to make positive changes through innovation and technology.
Compared to other industries, the construction industry has been slow to change. There have been incredible innovations in the airline, automobile, telecommunications and computer industries over the past 50 years, but the building and construction industry has stayed largely the same. We are still mainly building buildings using the same on-site processes that we have used for the past 100 years.
If we really want to make significant change and combat the damaging effects the industry has on the planet, we need to start doing things differently and push back on the resistance coming from within the industry — from typical developer mind-sets and from individual attitudes that have resulted in the industry being hugely risk averse and preferring to stick to established minimum codes rather than looking at innovative new approaches.
Companies such as Nexii, a green construction technology company, have to prove that it is ok to do things differently. They have started their journey, but there is still a way to go to break down the attitudinal resistance and convince the industry that we need to design and build with the end goal of creating a truly sustainable building.
The pandemic allowed us to have more clarity on the big issues going on in the world. It gave us time to pause and think differently about everything. Many issues that were not being properly addressed in the world started to get a lot of attention such as social justice, political issues, and climate change. Hopefully, while the world starts to go back to a new kind of normal, people will not forget the importance of addressing these key issues and we will still be able to see significant changes in industries around the world. In 2006, I created the Living Building Challenge Program and a few years later launched the Living Future Institute to provide a vision and direction to the design and building community and hopefully inspire them to move towards a healthier, greener future. We have seen some progress in this space, but we need to do much more to make a real difference.
This is where my collaboration with Nexii comes in, creating buildings that are more resource and energy-efficient with less waste, less embodied carbon, and a smaller carbon footprint. Often innovation is impacted by the price of a project because each building is essentially a bespoke process, even when it does not make sense to be. If you treat a building more like a product in terms of how it is built and its build components, you can take out a lot of the risk while enhancing performance.
My vision is to transform the world to support the health and well-being of every person and all living things. And I’m doing that by instigating and implementing new models in design and construction. By working with Nexii as their impact architect, I will be able to provide advice on ways to maximize the environmental benefits of Nexii architecture, using its breakthrough proprietary material, Nexiite, which has comparable properties to concrete, but contains no Portland cement or lime, significantly reducing end-to-end carbon emissions.
This work with Nexii is critical. However, it will take substantial innovations from many entities to truly disrupt the construction industry. If it were just one thing we would have already changed our direction. It’s a lot of things — some little and some immense. Certainly, building standards are important and regulations can help. And the market is slowly starting to shift to make it economically easier for builders to justify making substantive changes. Things that used to be expensive are now cheaper, and when something is costcompetitive, it is easier for people to adopt them. For example, the economics of scale for products such as photovoltaics, LED lighting, batteries, and advanced window systems are now more substantial, so these items are being used more frequently due to cost-effectiveness.
There’s also familiarity and habits to change. The more buildings that are made using leadingedge technologies, the more likely they are to be adopted.
Jason F McLennan is CEO of McLennan Design and founder of the International Living Future Institute. He is also impact architect at Nexii.
The Path to Zero Emissions
BY CHERYL MAH
As the urgency to act on climate change continues to grow, cutting carbon emissions for new buildings through regulations and policy is critical. Climate policy, specifically focused on reducing green-house gas emissions (GHGs), is driving some of the biggest changes in the construction industry.
By 2030, all new construction in Vancouver will be zero emissions buildings. To achieve this ambitious goal, the city introduced the Zero Emissions Building Plan (ZEB) and most recently the Climate Emergency Action Plan. Both have specific targets and actions that will be phased in, changing construction standards of all new buildings.
“All heating and hot water systems in new buildings should be zero emissions by 2025,” said Sean Pander, green building manager for the City of Vancouver. “The other thing that is going to really start impacting the construction industry is moving towards low carbon materials and construction practices.”
Pander was a speaker during a climate policy webinar organized by the Vancouver Economic Commission, Vancouver Regional Construction Association, and the Zero Emissions Building Exchange.
The Zero Emissions Building Plan and the B.C. Energy Step Code are the two most important regulatory tools for buildings and carbon pollution. Through increasing levels of energy efficiency, all new buildings must eventually meet a zero emissions standard.
Pander provided an overview of the ZEB plan along with what’s next in the green building policy for rezoning in Vancouver.
He explained some of the initial goals of the plan include obtaining real and reliable greenhouse gas reduction, future proofing buildings and clarity of requirements near and long term. Both ZEB and the energy code start by focusing on reducing net heat loss through the envelope and ventilation, which reliably reduce energy use at the time of construction.
Understanding that 70 per cent of greenhouse gas emissions in Vancouver were from space heating applications, it was important for the plan to focus first on these two areas and get it right, said Pander.
Phase 1 of the ZEB plan established greenhouse gas limits and thermal energy demand intensity (TEDI) along with window/wall ratio, envelope and mechanical requirements.
This led to design and construction changes such as more efficient heat recovery ventilation and moving space heating to electric baseboards in more budget developments or air source heat pumps in condos, said Pander, and more attention to glazing transitions and moving insulation outboard of the slab edge.
“What we’re seeing is the glazing industry, locally especially, is leading the way within North America and really coming up with these improved glazing systems for window wall and curtain wall assemblies,” he said.
Looking ahead at Phase 2, the focus is moving to zero emissions heating and hot water, which tar-gets 3 kilograms of carbon per meter squared per year.
“It allows gas use for peaking… allows some gas use for cooking but really what it starts to do is drive to the electrification of domestic hot water and make up air unit systems,” said Pander.
Improving climate resilience and reducing overheating limits will require an even greater focus on fixed shading to address solar heat gain in the summer, operation windows for natural ventilation and lower solar heat gain coefficients and more mechanical cooling solutions.
“The climate is getting warmer so we’ve had a history of overheating in the buildings as the envelopes get tighter. It could be exacerbated without better passive design measures,” said Pander. “We know the temperature is going to increase and we want to make sure that these buildings remain desirable places to live and work into the future.”
A significant change will be moving from reporting embodied carbon to meeting embodied carbon reduction targets (currently under consultation). Pander said embodied carbon goals can be met by measures such as low carbon concrete mixes, mass timber, using off-site assembly and reducing the use of spray foam and foam plastic insulation materials.
Other areas of opportunities include reducing concrete parkade spaces, and to not just reuse buildings and preserve buildings but also to reuse the materials — to facilitate deconstructability.
By 2030, Vancouver expects to reduce the embodied emissions from new buildings and construction projects by 40 per cent compared to a 2018 baseline.
To support market transformation, Pander said the city is committed to leading by example and sharing lessons learned, with all new city facilities and affordable housing required to be built to the Passive House standard.
“We’ve also created development incentives for Passive House constructions in multifamily buildings — five percent density bonus in areas with defined density,” he said, adding wall thickness and heat recovery ventilation space exclusions in buildable floor areas are also available.
He recognized fostering industry buy-in is key to the transition to zero emissions. Institutions like the Zero Emissions Building Exchange allow the industry to learn from leaders on what works and what does not.
“We’re policy makers. We don’t know the challenges and opportunities and we realize industry learns best from each other,” he said.
The ZEB plan requirements are now the minimum in the city’s building bylaw effective June 2021. Pander noted the requirements apply to multi-family, high rise office, retail, hotel and mid-rise MURBs.
As of January 1, 2022, the building bylaw will require zero emissions equipment for space and hot water heating in new low-rise residential buildings (up to three storeys).
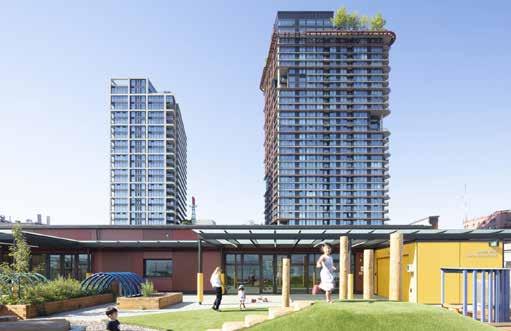
Opened in 2021, the City of Vancouver’s Gastown Childcare Centre is a Passive House zero emissions project by Acton Ostry Architects. Photo credit: Michael Elkan
Rethinking the Way We Build
BY HARDY WENTZEL
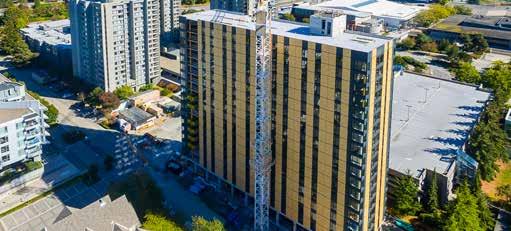
The National Building Code of Canada is due for an update in 2025, and we already have a pretty good idea of what changes to expect. The National Research Council has said that the next edition of the code will include new standards to protect buildings and their occupants against floods, wildfires, and extreme weather events that result from climate change.
Making buildings more resilient in the face of high winds, and basements more resistant to flooding? These are excellent ideas, and this seems like a sensible starting point for addressing the effects of global warming. What our building codes should be addressing, though, is the causes of climate change. To do that, we need to think bigger — and taller.
It all starts with wood. Mass timber is a renewable building material that can be regenerated through sustainable forestry practices, and harvested timber helps mitigate climate change by storing its carbon throughout the life of the building. Mass timber construction can help move the needle on carbon emissions, but for that to happen we need to modernize our building codes to allow for wood structures taller than the currently mandated 12 storeys.
HOW WE BUILD IS HURTING US Under the 2015 Paris Agreement, Canada committed to reducing its greenhouse gas emissions by 30 per cent below 2005 levels by 2030. According to the World Green Building Council, buildings are currently responsible for 39 per cent of global energyrelated carbon emissions. Operational emissions — from energy needed to heat, cool, and power buildings — account for 28 per cent, with the remaining 11 per cent from materials and construction.
Efficiency Canada, a research and advocacy organization at Carleton University, released a report last year that noted a disconnect between Canada’s climate targets and our building codes. The organization called on various ministers to issue a joint directive clarifying the role of building codes as “a tool for market transformation”. Efficiency Canada hopes to see building codes that “encourage the construction of new buildings more likely to mitigate emissions” as well as “incorporation of embodied and operational carbon to help Canada meet its climate objectives”.
WE KNOW IT CAN BE DONE Several years ago, my company supplied materials for a project called Brock Commons Tallwood House. When Tallwood House opened in the summer of 2017, it was the tallest mass timber structure in the world, standing 53 metres high. The 18-storey student residence at the University of British Columbia is exceptional — literally, in that it was an exception to the B.C. building code, which at the time limited wood buildings to six storeys. Getting it built required special permission and two structural reviews.
Although it was built on a concrete podium and does contain some steel elements, the frame of Tallwood House was built of engineered wood, with cross-laminated timber floors supported on gluelaminated timber columns. The amount of avoided and sequestered greenhouse gases from the wood used in Tallwood House is estimated to be equivalent to taking 511 cars off the road for a year. Using wood products over other materials reduced carbon dioxide emissions by 2,432 metric tons.
Tallwood House is a major reason that both B.C.’s code and the National Building Code of Canada were amended to allow construction of wood buildings up to 12 storeys.
THE POLITICAL WILL EXISTS In recent years, Tallwood House has had to relinquish its “world’s tallest” title to Mjøstårnet, an 85.4 metre, 18-storey mixed-use building in Brumunddal, Norway, completed in March 2019. That’s due to be nudged out of the top spot next year by Ascent, a 21-storey building in Milwaukee, Wisconsin, that will soar to 86.5 meters.
What’s stopping us from reaching similar heights here in Canada? We know that the political will exists, especially here in B.C. This summer, the provincial government announced that it will invest an additional $2 million in its Mass Timber Demonstration Program. This follows up on the commitment Premier John Horgan previously made to expand the use of mass timber as a means to drive economic growth and achieve the province’s own sustainability goals.
CONFIRMING WHAT WE ALREADY KNOW Our provincial and federal governments are certainly to be commended for the progress they have made in approving the construction of wood buildings up to 12 storeys. To get even taller projects into the codes, however, will require government-sponsored research to confirm what the industry already knows about mass timber’s properties in several key areas, including:
• Fire resistance: When exposed to fire, the outer layer of mass timber chars and acts as a protective coating, which insulates the wood underneath. Cross-laminated timber (CLT) was first recognized in the 2015 International Building
Code (the standard followed by most jurisdictions in the U.S.) after a test of a five-ply CLT wall. The wall was exposed to a fire that reached over 980 degrees Celsius. The building-code provisions required a two-hour fire rating, but the test specimen lasted just over three hours. • Earthquake safety: Mass timber structures weigh approximately one-fifth of equivalent concrete buildings, and that lightweight nature helps reduce seismic forces, which are proportional to weight. Wood-frame construction also exhibits ductile behaviour, which essentially means it can bend without breaking.
DEMAND WILL MOVE THE NEEDLE That research is not likely to happen, however, unless architects, engineers, and developers demand it. In particular, it is up to architects and designers to break out of their concrete-and-steel comfort zones and embrace wood.
Public education will also be important, with the main takeaway being that, from an environmental and safety standpoint, wood is good. Developers will make the buildings that consumers want, and if those consumers start asking more questions about sustainability in design and construction, that’s what will really move the needle.
If we expect to live up to our Paris Agreement commitments and hit our ambitious climate targets, we clearly need to rethink the way we build, and especially what we build with. Renewable materials such as mass timber are the future of construction, and the future is looking up — way, way up.