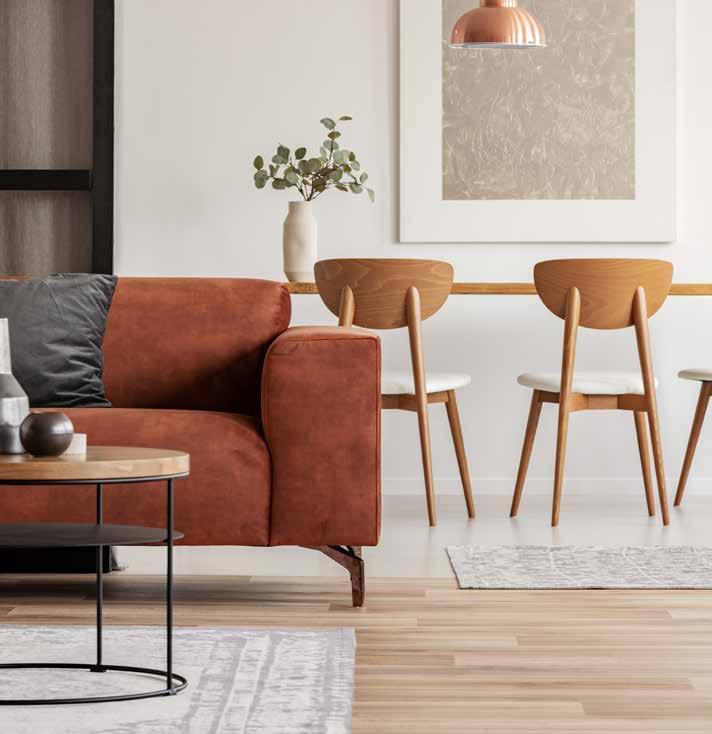
4 minute read
Installation Matters
from Coverings Fall 2022
by MediaEdge
MAKING THE RIGHT CONDO FLOORING CHOICE
Ideal materials, common problems and mistakes to avoid
By Steve Vasconcelos
Flooring is one of the most important design elements in a condominium. The first thing people generally notice when they enter a unit, the choice of flooring impacts the ambiance and mood, as well as sets the tone for the rest of the space. Plus, it can affect resale value.
Selecting the right flooring material is not always a simple task, though. Unlike the 70’s and 80’s, when the main options were wall-towall broadloom or parquet, there are an endless number of products available in the market today, from laminate to luxury vinyl plank (LVP) to herringbone and chevron wood flooring.
Laminate flooring has always been an affordable option that’s easy to install, durable and comes in a wide range of styles and colours. LVP has seen a huge spike in popularity in recent years because it’s sturdy, easy to maintain and worry-free for investor homeowners who rent their units. Making its way into the mainstream is herringbone and chevron wood flooring, which offer a unique look with its diagonal patterns. What’s more, it can be installed on any type of surface, including concrete substrates found in condos.
Regardless of which material is being installed, the flooring project begins long before the first box is cut open and ready to rack out. Be sure to follow the manufacturer’s pre-installation instructions and ensure job site conditions are met. As obvious as this may seem, this step is often overlooked.
To begin, confirm the subfloor is flat and within the manufacturer’s recommended tolerance. This will restrict vertical movement of a floating floor. In extreme cases, the floor’s locking mechanism can break or separate, which is not a quick fix and may affect the original manufacturer’s warranty should the flooring mechanism need to be altered in order to correct the issue.
When installing a double glue-down product, uneven subfloors offer a unique set of challenges. The popular hollow sound complaint during final walk-through is never comfortable. Although hollow sounds are not necessarily considered a deficiency unless there is vertical movement present, they cause problems when trying to collect final payment.
In today’s highly competitive market, it’s surprising that with all the information and technology at the industry’s fingertips, many flooring contractors have still not invested in a wood moisture or relative humidity (RH) meter. In Canada, it’s imperative to measure RH in a highrise condo between January and March. It’s not uncommon for the meter to read between nine and 25 per cent RH. (Industry standards and guidelines typically recommend 35 to 50 per cent RH.) If this occurs, a waiver should be signed by the customer acknowledging they understand their condo conditions do not meet the flooring manufacturer’s guidelines. This will protect the installer’s reputation and bank account. Proceeding to install the floor under these conditions without a waiver could end very badly down the road.
One of the most common errors made by installers relates to acoustical sound control underlayments. Underfloor treatments are
normally recommended or required by code in new condo projects. Many condo corporations also require them in existing buildings to help reduce impact sound transmission between units.
A lack of quality sound control underlay has caused frustration and anger among residents and management of condominium communities across Canada. The issue became even more pronounced during the Covid-19 pandemic with the move to remote work to limit the spread of the virus, and has remained at the forefront as many people continue to work from home.
Flooring contractors would be well-served to put some thought into selecting an appropriate acoustic membrane for installation under the floor. Never take claims printed on packaging at face value. Alone, they are not enough to confirm a product meets a project’s criteria. A common error is installation of an acoustic membrane that was tested with a suspended ceiling assembly in a unit that does not have this type of ceiling system. Although not a flooring deficiency, shared accountability may fall in the flooring contractor’s lap should noise complaints arise and a simple inspection determines the wrong acoustic sound control underlayment was installed.
It’s also important to consider the performance of the material used to achieve acoustic sound control. Rubber is a high-performance material that’s ideal for reducing impact and vibration noise. It can have a field impact insulation class (FIIC) rating as high as 70. One of the main factors that sets rubber apart from other materials is its high shear modulus. Products with a high shear modulus value are very rigid. In other words, a large force is required to deform the rubber underlayment. (A low shear modulus value indicates the underlayment is soft or flexible and little force is needed to deform it.) This means rubber can endure the constant loads that come with installing laminate, LVP and hardwood floors.
Steve Vasconcelos is owner of The Floor Studio Inc., a supplier of specialty hardwood, engineered flooring, luxury vinyl tile and sound attenuation products. Steve is also an accredited National Wood Flooring Association inspector with more than 25 years of experience in the flooring industry that includes analyzing acoustic test reports and membranes. He can be reached at 416-533-2855 or steve@thefloorstudio.ca