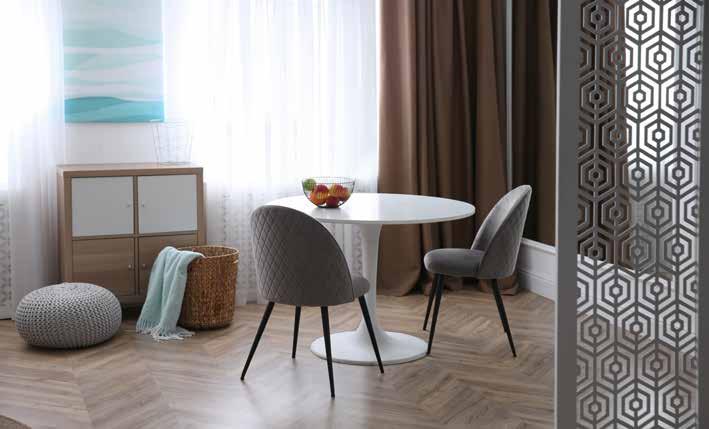
5 minute read
A New Generation of Wood
by MediaEdge
What to know about composite/hybrid floors
By Don Finkell
Studies show that wood is the overwhelming preferred flooring of consumers today. Its natural beauty and practical performance are both highly desirable. But despite being the most favoured flooring choice, wood only enjoys approximately 12 per cent of the total flooring market. The reasons for this attrition are many. Price is a big factor, as is its perceived vulnerability to moisture. This has provided an opportunity for composite/hybrid wood flooring to shine. wood flooring was three-quarters of an inch thick. Afterward, multilayer wood flooring (engineered) came into use. The cross-ply lamination and waterproof glue that allowed patrol torpedo boats and amphibious landing craft to stand up to the rigours of seawater resulted in the creation of a wood floor that was stable enough to be glued directly to a concrete slab. For the next 60 years, engineered wood went from a small percentage of the North American flooring market to the majority, accounting for more than two-thirds of market share now. During this time, wood flooring steadily gained a market hold over other choices like carpet and laminate. However, with the advent of vinyl plank flooring in the last 10 years, wood, along with all other flooring categories, has rapidly lost market share. Vinyl now captures more than 24 per cent, largely because of its claim to be waterproof.
Seeing a decline in business, wood flooring manufacturers started innovating floors that had the realistic appearance of a real wood surface bonded to a waterproof core. The success of these early composite/hybrid wood floors was mixed. Most performed like vinyl and, unfortunately, looked like vinyl, too, because of the high amount of water-resistant finish. With some trial and er-
ror, though, the right mix of performance and appearance was eventually found. In fact, Canada was one of the earliest markets to accept this new category of wood floors.
COMPOSITE WOOD FLOORING
Composite/hybrid wood floors are comprised of a thin wood veneer — 0.06 to 1.2 millimetres (mm) thick — bonded to a waterproof core like stone plastic composite (SPC) or magnesium oxide (MgO). The wood veneer is topped with a hydrophobic coating, which is brushed in to protect the surface from water. The hydrophobic coating is then overlaid with several layers of scratch and wear-resistant aluminum oxide impregnated, ultraviolet light cured urethane finish. Generally, there is a backing layer (1 to 2 mm) of an acoustic material, usually an IXPE synthetic pad or natural cork. If a locking profile is preferred, a SPC core must be used; a MgO core is too brittle to accept a locking profile. Of course, all or any of this is subject to change as new innovations are constantly being brought to market.
While it is not a requirement, most composite/hybrid wood floors are waterproof. The exact definition of waterproof depends on the core. With SPC, it means that the boards do not absorb moisture or change shape when submerged in water for many days. Waterproof may also be defined using a ‘three T test’ wherein a collar surrounding water is glued over the side and end joints of the floor. It is then timed to see how many hours it takes for the water to leak from the vessel through the joint to the backside of the floor and onto the subfloor.
WEIGHING THE PROS AND CONS
The National Wood Flooring Association recognizes three categories of wood floors: solid, engineered and composite/hybrid wood. Each has its advantages and disadvantages.
Solid wood floors can be factory finished or sanded and finished on-site. Optimal flatness is achieved from a site finished floor. Wood can also be sanded and re-sanded multiple times. However, because wood expands and contracts perpendicular to the grain, solid wood floors are less stable than engineered or composite/hybrid floors. The boards must be narrower (less than five inches wide) to prevent objectionable seasonal cracks from developing between them during winter. This makes solid wood less than ideal for below grade applications or installation on a concrete slab. The three-quarter of an inch thickness also makes replacement of thinner floor coverings with solid wood more awkward because a transition strip is necessary.
Engineered wood floors are made up of real wood. Plus, because of the cross-ply lamination, this flooring can be glued directly to a concrete slab, allowing it to be installed on, above or below grade. Engineered flooring is also more stable than solid wood, so it can be manufactured in wider widths without having to increase the overall thickness. This makes it an ideal choice for remodelling projects. On the downside, most types of engineered flooring can only be sanded and refinished once since the surface hardwood layer is relatively thin.
Composite/hybrid wood floors are thinner than solid and engineered wood floors. But unlike its counterparts, it can be wider and manufactured to be waterproof. A disadvantage of this flooring type is the solid surface cannot be resanded to change its colour. However, it is possible to resurface and recoat the finish.
Don Finkell is vice-president of AHF Products. He is responsible for the American OEM brands, including Hearthwood Floors, Emily Morrow Home and Raintree Floors. Don is the former CEO of Anderson Hardwood Floors, Shaw Hardwood and American OEM Wood Floors. He is also past chair of the National Wood Flooring Association, the Decorative Hardwoods Association and the Hardwood Federation.

MEETING THE INDUSTRY STANDARD
In the last two years, the National Wood Flooring Association (NWFA) and Decorative Hardwoods Association (DHA), formerly the Hardwood Plywood and Veneer Association, both promulgated industry standards for composite/hybrid wood, giving legitimacy to this new category of floors. Much like the adoption of standards covering engineered wood floors in the 1960s, this inclusion of composite/hybrid wood floors is not without controversy. Some feel it is not a real wood floor.
The NWFA recognizes three categories of wood floors: solid, engineered and composite/hybrid. The requirements of solid wood floors are that it must be solid wood from top to bottom. The National Oak Flooring Manufacturers’ Association (now part of NWFA) has published standardized grading and milling rules since 1905.
The NWFA adopted the DHA’s American national standard for engineered wood flooring, ANSI/HPVA EF, in 2012. Some of the requirements for engineered wood floors were that it contain real wood from top to bottom, normally made up of veneer or slats turned at 90 degrees to each other.
The NWFA recognizes composite/hybrid flooring when it contains real wood on the wearable surface only. The backing and core material may be made up of any type of composite material.
In 2020, the DHA revised its ANSI/HPVA EF standard to include composite as a component of engineered wood floors. Hybrid flooring products that utilize a composite platform with a wood surface are now covered by the standard.