
10 minute read
Electrifying Progress: Heat pumps considered
from CPM July 2022
by MediaEdge
ELECTRIFYING PROGRESS
Technology and Carbon Pricing Advance Fuel-Switching
By Barbara Carss
CLIMATE, COST AND CAPACITY
pose fuel-switching challenges for building owners looking to curb greenhouse gas (GHG) emissions in line with Canada’s target for a 40 to 45% reduction below 2005 levels by 2030. Industry panellists contemplating the electrification of mechanical systems during a recent Canada Green Building Council (CAGBC) conference in Toronto acknowledged that the leap to net zero comes with varying degrees of difficulty from region to region across the country.
For example, British Columbia’s lower mainland enjoys the twin advantages of a clean electricity grid and milder winter temperatures that generally don’t compromise the effectiveness of air-source heat pumps. Elsewhere, the arrival of new technologies and ongoing replacement of fossil-fuel-fired power generation with renewable sources are expected to ease the transition to low-carbon heating and domestic hot water systems, but that’s occurring on a patchwork of timelines.
A carbon price on pace to reach $170 per tonne by 2030 and the potential for other regulatory and investment-related imperatives are now reshaping conventional cost-benefit analyses. Yet, even as the commercial real estate industry is urged to readjust priorities from incremental improvements with quick paybacks to bigticket, deep retrofits, energy efficiency continues to be a preferred gateway to decarbonization for many companies pursuing emissions reduction targets.
“One of the goals along with heating electrification is to reduce the amount of heat we need. It seems like now we’re talking about carbon, carbon, carbon, carbon, but energy efficiency is still very much the first thing that we focus on,” affirmed Ariel Feldman, Director of Sustainability with Choice Properties REIT. “You still need to take all those steps first because, from the owner’s perspective, electrification is not necessarily going to pay back. You might spend more money up front and you might spend more money on the operations side. That’s not a very good business case to start from.”
That said, he maintains business cases should no longer be anchored in the supposition that a boiler has a 30-year life cycle. Speaking at the REMI Show in early June, Jeff Ranson, Director of Energy, Environment and Advocacy with the Building Owners and Managers Association (BOMA) of Greater Toronto, hammered home the same message.
“If you’re comparing the cost of zero carbon with your current operating costs, that’s a false equivalency because your current building operations may not be possible in the future. Business as usual may not exist, and probably won’t exist,” Ranson submitted. “We’re not typically factoring in changes to the asset value whether or not your building is aligned with carbon targets. We’re not factoring carbon pricing. We’re not factoring in policy risk.”
“The sticks are coming,” Steve Kemp, a principal with RDH Building Science, warned CAGBC conference attendees.
INCENTIVES AND OBSTACLES In British Columbia, there’s now one such stick intertwined with a carrot. Since the release of the provincial budget on February 23, 2022, the provincial sales tax (PST) on gas-fired heating and cooling systems has jumped from 7% to 12%, while heat pumps are now exempt from PST.
“To qualify, it must be a heat pump for air-conditioning and heating, where your heat pump is your primary heating and cooling system,” said Pushpinder Rana, Senior Director, Commercial Products and Industry Relations, with Mitsubishi Canada’s HVAC division. “Those are huge trigger points, and we are seeing similar movements across Quebec.”
Kemp outlined some of the obstacles to adoption.
Notably, some air-source heat pumps employing variable refrigerant flow (VRF) technology function well down to temperatures of minus 30⁰ Celsius, but, predominantly, hydronic systems “go kaput” at about minus 15⁰ C, necessitating backup boilers in areas where the temperature falls below that threshold. Because heat pumps circulate lowertemperature water — at about 49⁰ C versus 82⁰ C with boiler systems — a switchover will likely also entail replacement of space heating equipment.
“Whether it’s a fan coil, baseboard convector or radiant panels, at these lower temperatures, you need a bigger physical thing to deliver the same amount of heat to that space,” Kemp advised. “We may be gutting every baseboard convector, every fan coil in the building.”
Retrofitters are installing larger convectors and fan coils, multiple-row fan coils or fan-assisted baseboard convectors. However, reinforcing Feldman’s argument for prioritizing energy efficiency, Kemp also cited an example of a major retrofit where his firm derived sufficient savings from building envelope improvements to cancel out such required investments.
“There, we basically cut the heating demand by 75% and theoretically could have kept the same mechanical system,” he noted. “Sometimes you can get lucky.”
In the future, hybrid hydronic-VRF heat pump systems are expected to improve coldweather performance and mitigate uncertainty around pending phase-downs of some hydrofluorocarbon (HFC) refrigerants. (See story, page 28.) Rana sketched out a range of existing and emerging VRF heat pump and heat recovery products he predicts will increasingly capture market share, including hyper-heating technology for coldtemperature performance and a water-source format.
“There is a huge gap between what a heat pump or heat recovery solution provider can offer to the market and the understanding and the knowledge the market has,” he asserted. “We have training for consulting engineers. We have training for contractors. The objective is to educate the market.”
Alternatively, geo-thermal systems promise consistent output everywhere the required wells can be accommodated.
“If you’ve got space on your site for geothermal, you can do it across the country and we’re seeing really good paybacks even on a 15-year assessment,” reported Cara Sloat, Senior Engineer with the mechanical and electrical engineering firm, Hammerschlag and Joffe. “It’s worth looking at that technology even if you’ve previously been worried that you can’t afford it. Some of the big banks are financing that now also, so that can take it off your project’s books and get it somewhere where it’s easier to deal with.”
STRATEGIES TO 2030 AND 2050 She suggests the timing is right to convert to a heat pump in any building with a cooling system approaching the end of its life cycle, but also highlighted potential for capital planners to stretch the expenditure over a longer period.
“There are a variety now of quite good heat-only heat pumps on the market so you can get something that is optimized for heating only that would do your domestic hot water plant and directly replace a boiler,” Sloat said. “So maybe you do half the plant now and you think about phasing. That is available.”
Meanwhile, a portfolio primarily consisting of open-air retail and industrial warehouse buildings has given Choice Properties more flexibility for a phased approach to its 2050 net-zero target. Feldman projects rooftop HVAC units will need to be replaced at least twice in that period and, for now, that means dual-fuel gas and electric systems in some cases.
It’s an approach he aims to minimize given the extra costs of two systems, but it’s a necessary contingency to address concerns
AIR-SOURCE HEAT PUMPS ADDED TO TAX BREAK LIST
Air-source heat pumps have been added to the list of clean energy equipment that qualifies for special tax treatment through Canada’s accelerated capital cost allowance (CCA) program. Businesses that acquire qualifying systems for indoor space heating/cooling or water heating between federal budget day on April 7, 2022 and December 31, 2023 will be eligible to deduct the full value in the first year of ownership.
Other clean energy equipment — which is designated in class 43.1 or 43.2 for CCA purposes — already eligible for accelerated deductions includes: ground-source heat pumps, including those used to heat swimming pools; active solar heating equipment; heat recovery equipment; photovoltaic electrical generation equipment; geothermal energy equipment; equipment related to district energy systems; electrical energy storage equipment; and electric vehicle charging equipment.
As announced in the 2022 federal budget, the following components associated with airsource heat pumps can be claimed: refrigerant piping; energy conversion equipment; thermal energy storage equipment; and control equipment and equipment designed to enable the system to interface with other heating and cooling equipment. Purchasers may also be able to be claim feasibility studies, engineering and design costs as allowable Canadian Renewable and Conservation Expenses (CRCE), which could be claimed in the year incurred, carried forward or transferred to investors.
“As a means to displace the use of fossil fuels for heating, or of providing a more efficient means of heating with electricity (e.g., compared to electric baseboard heaters), air-source heat pumps can play a role in reducing emissions of greenhouse gases and air pollutants associated with heating buildings in Canada,” the budget document states.
Concurrently, manufacturers of air-source heat pumps will be eligible for new tax credits, which were announced in the 2021 federal budget, but are available to claimants for the first time in 2022. That program provides a 50% reduction in the corporate tax or small business tax rate until 2028 for manufacturers of designated zero-emission technologies, with a continued tax credit at incrementally lower rates in the 2029-2031 period.
The budget document states that adding the new category to the original list of designated manufacturers — including those producing solar, wind, hydroelectric and geothermal equipment, as well as equipment related to ground source heat pumps, electrical storage of renewable energy, and electric vehicle charging systems — will “support job creation and growth in clean technology manufacturing in Canada”.
It’s estimated the Canadian government will forego about $53 million in tax revenue over five years by extending the two measures to air-source heat pumps.
– REMI Network
Washington state is the first in the United States to incorporate building electrification mandates into statewide energy codes. Beginning in 2023, builders will be required to install electric heat pumps for heating and cooling in new commercial and multifamily buildings.
That comes with a last-minute amendment from the Washington State Building Code Council to establish that only 50% of water heating must be derived through electric heat pumps. There is also an exception for hospitals and research facilities. The new rules leverage the state’s clean electricity grid for a projected 8 million ton reduction in carbon emissions by 2050. The updated energy code also includes improvements to building envelopes and other new efficiency measures.
“This stronger energy code is absolutely time-critical to continue to proactively move the design and construction industries toward achieving netzero carbon buildings,” maintains Todd Stine, a partner at ZGF Architects. “The market is already going there, but more clarity and support in policy and codes will be key for the building design and construction industries.”
–REMI Network
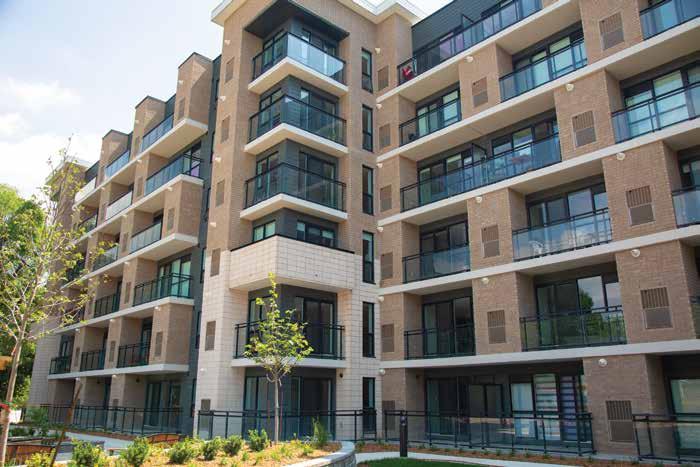
about pass-through utility costs to tenants and capacity of the electrical grid. The latter can be a particular vulnerability when landlords have little ability to control tenants’ energy use.
“That was a limiting factor at one of our sites where we decided, even though we would have ideally liked to go all-electric, we’re doing dual-fuel for now while the grid is improved,” Feldman recounted. “We’re hoping with the next iteration in 15 years, we’ll go all-electric at that point. We have a little bit more leeway than you have on a multi-unit residential building or an office where you’re replacing a boiler that lasts 30 years.”
“We find that trying to retrofit heat pumps into existing buildings with limited space for additional transformers is very challenging,” Sloat concurred. “Doing a study on a high-rise building, we saw we were adding maybe 3 megawatts to back it up with an electric boiler, which is the same as a whole new building.”
Regardless of complications, with a the carbon price now at $50 per tonne, Kemp calculates electric heat pumps are already more cost-efficient than natural gas systems in British Columbia, Manitoba and Quebec. That pool should expand rapidly as the price takes its ordained trajectory to $170/tonne over the next eight years, and on up to possibly as high as $300/tonne by 2050.
By 2030, Kemp foresees Saskatchewan and Nunavut will be the only areas of Canada where fuel-switching may not be a money-saving proposition. Feldman concludes it’s best to get proactively ahead of that curve.
“British Columbia, Manitoba, Quebec, where the grids are clean and the electricity is relatively inexpensive, that’s where you want to focus at the start. Start with the ones that are a bit easier and then build your experience,” he urged. “As the technology improves and the supply chain improves and costs start to come down relative to the existing technologies, you will get to a point where it starts to look better and better in other provinces as well.” zz