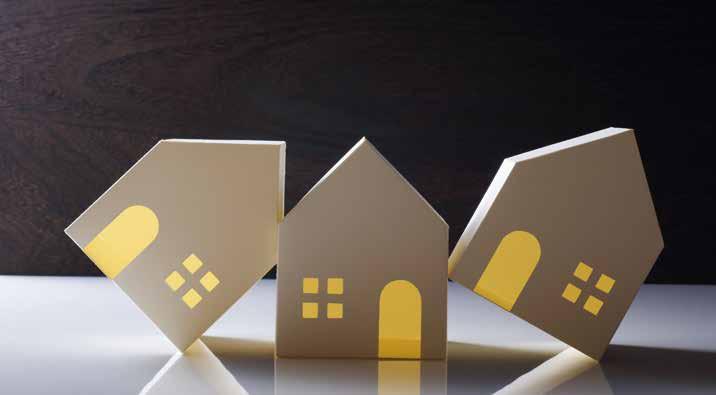
8 minute read
Heat as a Service: ESCOs tapped to shoulder capital costs of decarbonization.
from CPM November 2022
by MediaEdge
TAKING HEAT
ESCOs Can Shoulder the Capital Costs of Decarbonization
The World Business Council for Sustainable Development (WBCSD) — a CEO-led collective of more than 200 businesses worldwide working toward sustainable, net-zero outcomes — is promoting heat as a service (HaaS) as a next logical step after decarbonizing electricity supply for companies pursuing emissions reduction targets. The follow is an excerpt from the WBCSD’s recent primer on the subject – Editor.
HEAT AS A SERVICE (HaaS) is a potential option for companies with decarbonization targets. Rather than investing directly in a new renewable heat solution, companies can turn to a third party to bear the capital costs and guarantee its performance over the lifetime of the contract.
This provides an opportunity for companies to decouple capital allocation from their decarbonization journey, free up capital for core business investments and benefit from immediate operational cost savings. HaaS solutions might not appear on the company’s balance sheet, which can be a critical consideration for companies keen to keep leverage ratios low.
Electricity is often the initial focus of companies’ decarbonization plans. They have used a variety of instruments to source sustainable power, from renewable certificates through to longterm offtake agreements (also known as power purchase agreements or PPAs) that have enabled renewable power developers to attract financing and build new renewable powergenerating assets.
Heat is the next big challenge on the corporate decarbonization journey, particularly for companies in the light industrial sector, such as the food and beverage industry. Many of these companies require substantial amounts of heat for their manufacturing processes — often in the form of steam — and many have committed to decarbonizing their own asset base before 2030.
There is no one-size-fits-all solution for sustainable heat. Most companies will use a variety of commercially available technology solutions to decarbonize their thermal energy use, depending on the particular climatic conditions, market dynamics, fuel source availability and
policy environments across their asset base. Key technology solutions include: electrification through heat pumps, boilers and steam generators; solar thermal; biogas or biomass; deep geothermal; and thirdparty waste heat.
OFF BALANCE SHEET APPROACH They all face some common barriers to implementation. Competing capital needs and investments in companies’ core business often take priority. As well, many lowcarbon solutions are capital-intensive and often do not meet the minimum rate of return on an investment that will offset its costs, especially in jurisdictions where there is no significant cost attached to emitting carbon.
HaaS connects investors looking for long-term, low-risk investment opportunities with companies that need to decarbonize and prefer to do so through their operating expenses rather than through their capital expenditures. Akin to power purchase arrangements, HaaS sees a third party invest in a low-carbon asset and sell the energy generated through a long-term offtake agreement.
HaaS is not just attractive from a financial perspective. Technologies providing low-carbon heat are evolving rapidly and thus need specialized expertise to design, operate or maintain. Having a third party provide that expertise and deliver an optimized, reliable service can be highly valuable.
The opportunity for corporate carbon and cost savings within heat is huge. Almost half of total final energy consumption globally is associated with heat, and the vast majority is consumed within industrial and commercial facilities. The biggest HaaS opportunity is within companies willing to enter into longer term supply agreements, with predictable future heat demand, and in locations where heat service providers can leverage technological and power market developments to deliver immediate savings.
TRANSFERRING NON-CORE FUNCTIONS In a business-as-usual solution, the company owns the heat facilities and has full control over the design process, as well as its operation and maintenance. The company can elect to perform elements of the design, construction or operation or use selected contractors to perform them.
It can also tailor the construction process to its risk appetite, from taking on all the capital investment and associated risks versus a low-risk, fixed-price, datecertain, turnkey engineering, procurement and construction contract. The company is also free in its financing approach, such as through corporate lending, no or limited recourse finance or through various leasing options.
However, moving to low-carbon heat solutions often requires expertise that companies may not have. Taking ownership of a technology solution unrelated to the company’s core business might be inefficient. Companies are often not set up to operate things like biomass boilers or secure feedstock over a 15-year contract term.
In the HaaS business model, companies engage and pay an energy service company (ESCO) to provide an optimized, tailored thermal energy solution as a service. The services an ESCO renders may vary from an energy savings performance contract (ESPC), under which the ESCO will provide guaranteed performance and operation and maintenance services, to a full HaaS solution where the ESCO takes responsibility for the design, financing, construction and ownership of the facility and for the (low-carbon) energy source.
HaaS solutions are usually tailor-made business deals between the company and the ESCO based on the business needs of the company. They often involve the ESCO to outlay substantial capital based on the projected project cash flows paid by the company to the ESCO for heat services rendered.
HaaS contracts are usually long-term because the expenses paid for the heat services need to be competitive. This means the ESCO will either require a long-term contract or a higher unit price to make its desired return on the investment. If companies cannot commit to long-term agreements, they must accept that the periodic costs or unit price for the heat will be higher.
Trust in such a long-term arrangement is key. Companies also need to commit to an appropriate development process to ensure the HaaS solution is fully aligned with corporate strategic priorities, which requires the collaboration of many company stakeholders, including the executive office, operations, sustainability, legal, procurement and finance. zz
The complete text of Heat as Service: How
to decarbonize commercial and industrial heat use with third-party
capital investments can be found on the World Business Council for Sustainable Development website at www.wbcsd.org.
HOW DURABLE IS YOUR BUILDING?
Building durability is affected by many factors, exposure to the elements being the primary culprit. Moisture and decay caused by rain, heat, wind, snow, and extreme temperature fluctuations make location and the surrounding weather conditions key considerations for determining the right products and materials to use during construction or renovation.
Beyond exposure to the elements, not all products are manufactured to the same quality, and when assembled poorly, there may be weaknesses. Additionally, regular maintenance may be an important requirement to prolong your asset, particularly in fluctuating climates or regions prone to seismic activity.
If building durability and long-term resilience are the goals, those looking to build or renovate should choose their materials wisely for their specific location and design. Here, Bryan Colvin of RJC Engineers, walks us through the pros and cons of four common building materials:
MASONRY Pros: One of the oldest and most durable building materials around, masonry either in stone or brick form, has been used in construction for centuries. Known for their high wear-resistance and thermal insulation, they come in a variety of shapes, sizes, and categories including larger blocks for foundations and the classic burnt clay bricks often used in walls.
“Masonry offers numerous advantages beyond their aesthetic appeal. They have excellent high compressive strength and they are porous, meaning they are able to release and absorb moisture to regulate temperature and humidity within the structure,” says Colvin. “Another benefit of masonry is that it has a high fire protection rating.” Cons: Working with masonry can be time-
consuming, and it is not recommended for high seismic zones. Another disadvantageous is that it absorbs moisture, which can lead to mold-growth and the regular need for cleaning.
WOOD Pros: One of the great things about wood is that it comes from a natural resource abundantly found in Canada. Thanks to engineering advances, new protective treatments for lumber, and a collective desire for “greener” buildings, building codes are changing to allow for taller structures made predominantly of mass timber. As a result, we are seeing a revival of wood construction—but is wood safe and durable?
Not only is mass timber lightweight compared to other materials, but it is also incredibly durable. Wood is simple to work with and can be cut right on site, speeding up the construction process and potentially saving money.
Cons: Age, temperature, and environmental humidity are all factors that can make wood warp. Additionally, it is a plant-based substance, meaning it is more sensitive to pests. Of course, then there is the matter of flammability — wood is a material that burns unlike others. But new treatments and innovation are making these issues less of a concern.
CONCRETE Pros: Concrete has a lot going for it, largely because it is widely available and inexpensive compared to other construction materials. Made of cement, water and aggregates, fresh concrete is flowable and can be poured into various forms, making it extremely versatile and easy to work with. “Concrete can withstand water better than wood and steel, therefore it less prone to deterioration,” Colvin says. “When reinforced with rebar, concrete is an ideal material for walls, beams, slabs, foundations, frames and many other applications, and it’s also the most economical.”
Cons: Compared to other binding materials, the tensile strength of concrete is relatively low, requiring rebar, which can corrode if left unprotected with good concrete cover or other surface treatments to reduce permeability.
STEEL Pros: Steel is immensely strong and does not easily warp, buckle, twist or bend. In other words, steel buildings are highly durable, allowing them to withstand extreme weather conditions including hurricanes, blizzards, and even earthquakes. Steel is also resistant to termites, cracks, splitting, and rotting.
Cons: “The cost to produce steel may be higher than other materials, and when it comes to fire resistance steel is weaker compared to concrete,” says Colvin. “Another disadvantage is that steel is heavy and expensive to transport.”
In conclusion, Colvin says that while all building materials offer numerous advantages, ultimately location and design will have a direct effect on building durability. “Additionally, regularly maintenance will help extend the functional life of any building,” he says.
To find out more about how to improve, restore, or maintain the durability of your building, contact Bryan at bcolvin@rjc.ca or visit www.rjc.ca.
Bryan Colvin BSc, P.Eng. | Managing Principal RJC Engineers