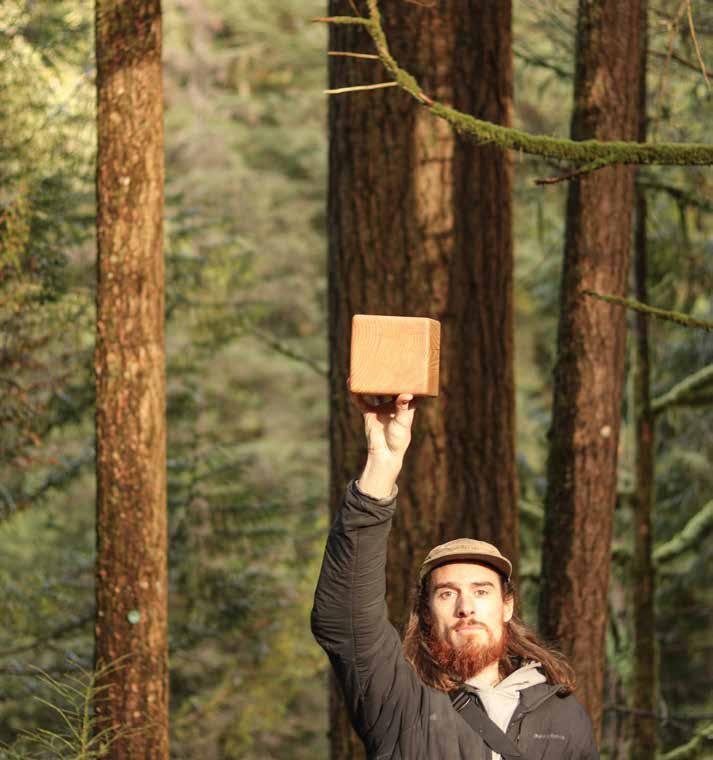
17 minute read
TWIG
by MediaEdge
AN ALTERNATIVE PATHWAY TO INNOVATION
By Patrick Christie
The Wood Innovation Group (TWIG), like many other variants across the world, emerged as a response to the global pandemic. A way to stay connected and stay engaged in topics and ideas that were meaningful in your life and work. You would have gained this value through day-to-day interactions, exhibits, conventions, kids’ soccer practices; you name it, in previous circumstances. Our lives were full of physical interactions on a macro and micro level, and we had to navigate from home to work, meeting to meeting, site to site - repeat. For a year and a half, we have been asked to do business differently, create the necessary space, and adjust procedures in our day-to-day workflow. We had to adopt new ways of working to stay connected with the people we rely on to produce products that add value to our organization and the natural resources.
The TWIG concept had its origins dating back to November 2012 in an East Vancouver bar. A group of twenty-five individuals met for the first time around the common question of how we can be doing things differently in BC concerning our valued-added and postprimary industries. We met under the name “Outside the Box Meetup Group” and did so 50+ times until March 2020. This initiative was founded by Ian MacDonald (Tall Wood Institute), who was working at CAWP, along with Jason Chui (CAWP), and Barbara Bell (formerly FPInnovations). Later, the group would be joined by Neil Godin (NG International) and me, Patrick Christie (Daly Co). This little idea was supported with assistance from the Wood First program through FPInnovations.
“Outside the Box is a forum for industrial and interior designers, artisans, furniture makers, manufacturers, builders, architects, and anyone interested in or involved in the wood products industry (broadly defined) to meet, share ideas, and identify gaps in the market and possibilities

Patrick Christie’s 312 Main Street project created with 300 wood blocks
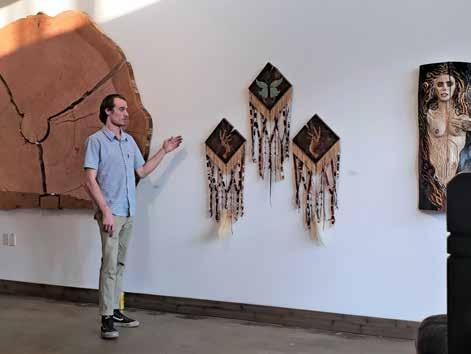
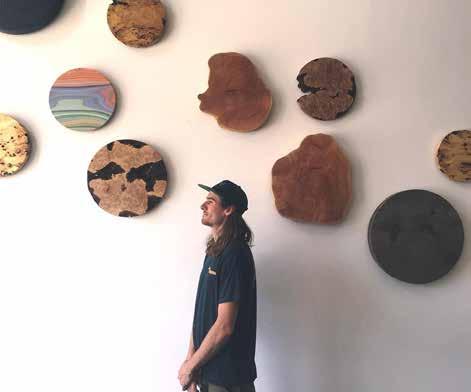
for new product development and innovation.”
The core intention behind this group was to use CAWP as a conduit to connect their specialists and equipment capacity to the industrial designers, artists, and architects to produce prototypes of new designs and concepts. As a recent graduate of the Industrial Design program at Emily Carr, this was ideal for me to begin my career pathway. Because of this, I’ve developed a business, found mentorship, sourced materials, spoken about my work, and tackled some highly technical design projects and art installations due to the network of support I had available to me. From Outside the Box and now TWIG, I have multiple sources of revenue that support me as an Independent wood-based entrepreneur, with my role as organizer of TWIG being one of these. Within this role, I intend to use the experience my efforts and privilege have afforded me to inspire the next generation of wood-based entrepreneurs. We have to cultivate contexts for fresh ideas and create space for them to be nurtured, refined, and then exhibited in the public realm for feedback and response. This is what I am here for, and I hope to inspire and help others do so too.
This article is the first in a five-part series exploring how TWIG offers an alternative pathway to innovation that values humans, resources, and the economy.
Osborne Wood Products has been a supplier of high quality furniture and cabinet components for 40+ years. We work hard to keep our customers supplied with everything they need for their projects, and to provide top quality customer service.
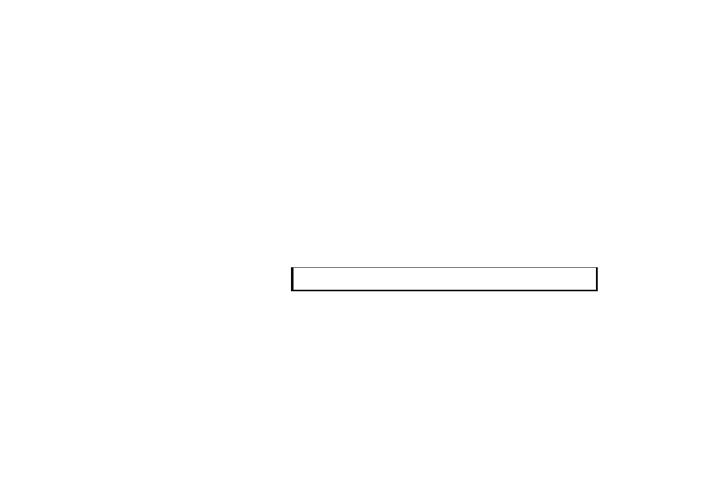
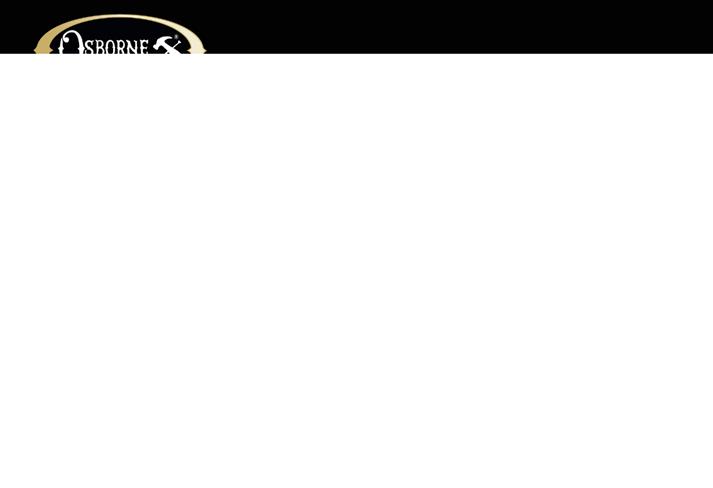
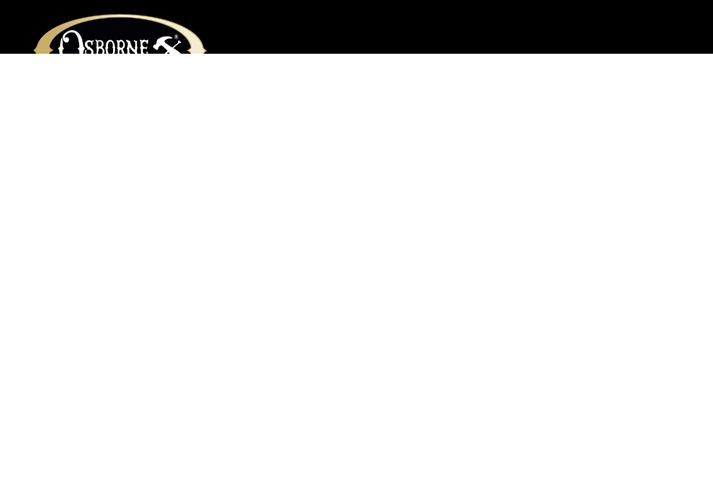
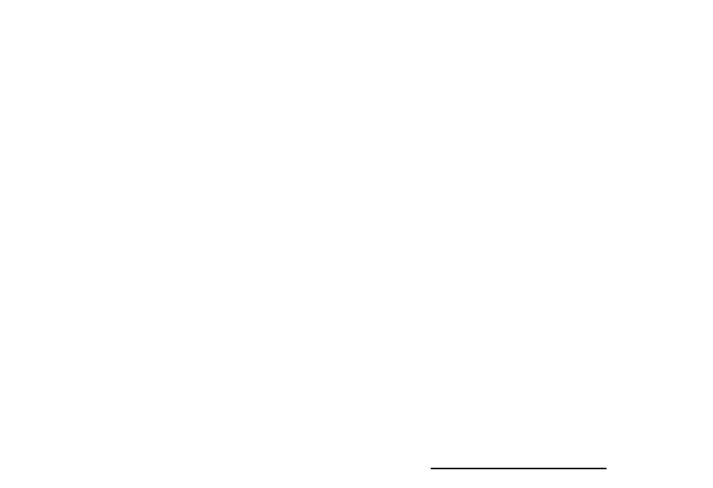
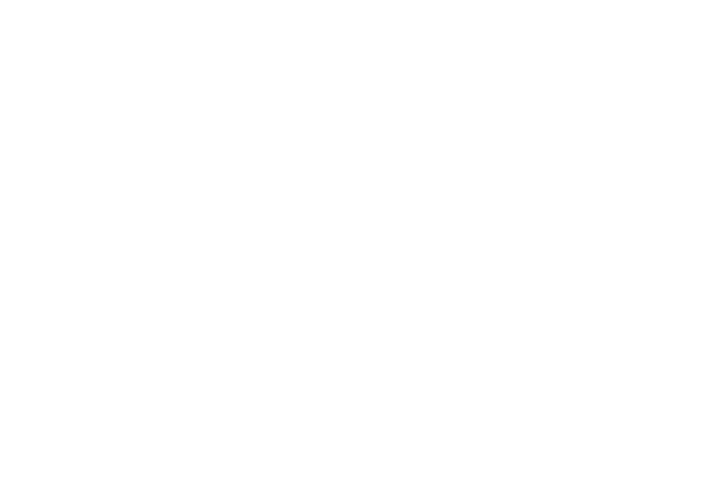
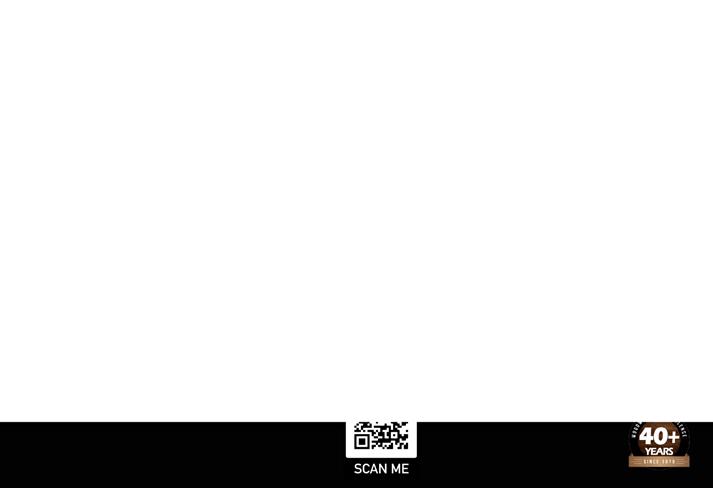


Looking for some beautiful furniture components? Osborne Wood Products has no minimum order on all of our beautiful furniture components, so you can get everything you need for your next project. Visit our website to learn more and to see our full collection of products.
Browse our inventory at www.osbornewood.com or call for more information at (800)-849-8876 Scan the QR code to view our ful collection and more!


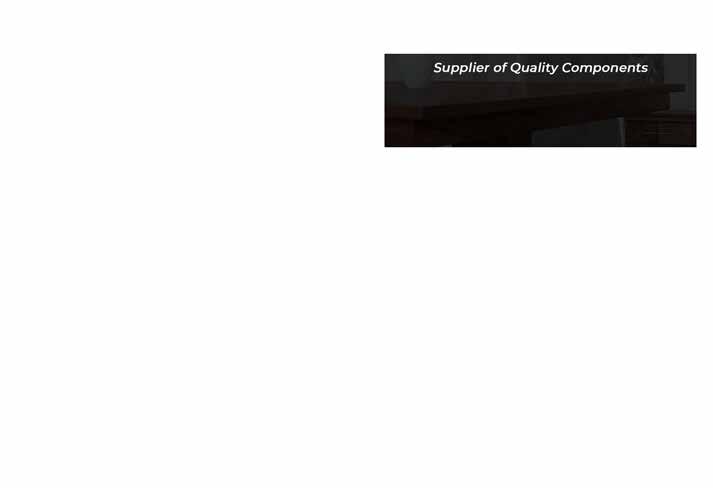
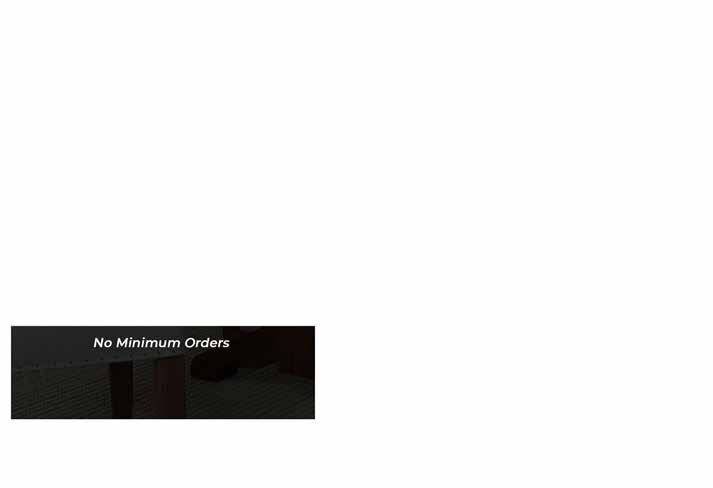
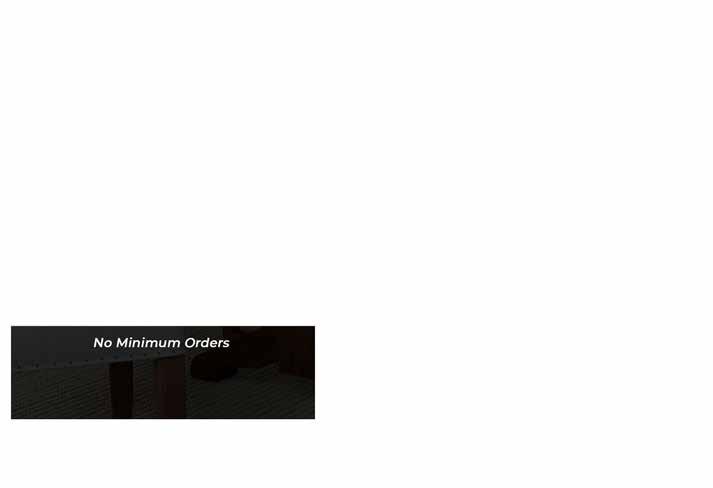
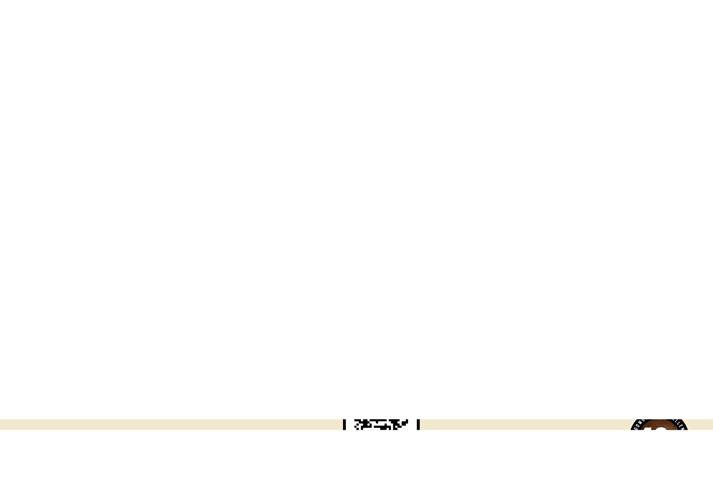
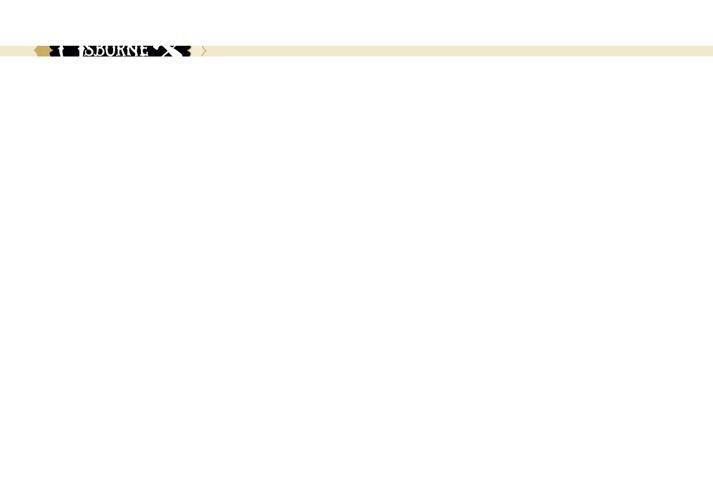

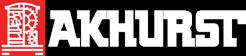
everything you need in ONE PLACE
ARE YOU LOOKING TO INCREASE PRODUCTIVITY WITHOUT INCREASING YOUR LABOUR? LOOK NO FURTHER THAN GANNOMAT’S RANGE OF DOWEL & CASE GOOD PRODUCTION SOLUTIONS.
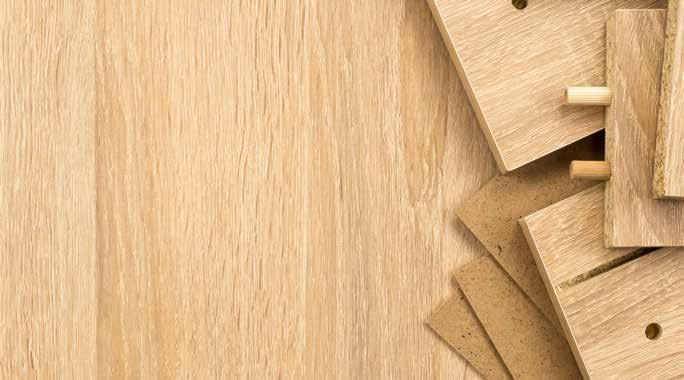
INDEX LOGIC
CNC Dowel Drilling, Gluing, & Inserting Machine
CONCEPT ECO
Lamellar Case Clamp
EXPRESS S2
Dual Hinge Drilling & Inserting Machine
@AkhurstWood @Akhurst.Machinery @AkhurstMachinery @AkhurstMachinery 1.888.265.4826 | www.akhurst.com
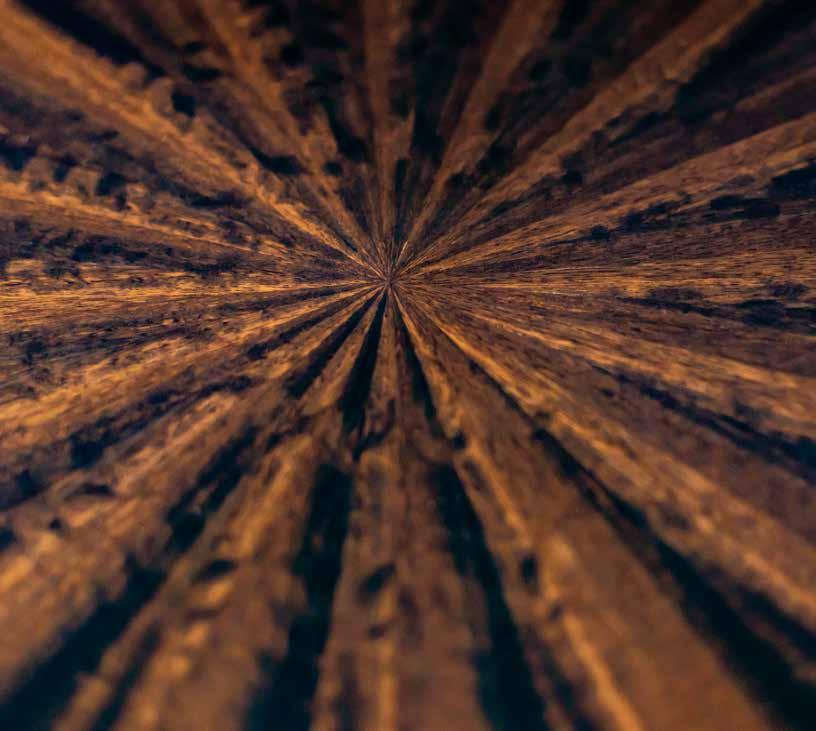
ALEXANDRE CECCHI
THE PATH AND THOUGHTS OF FURNITURE DESIGNER
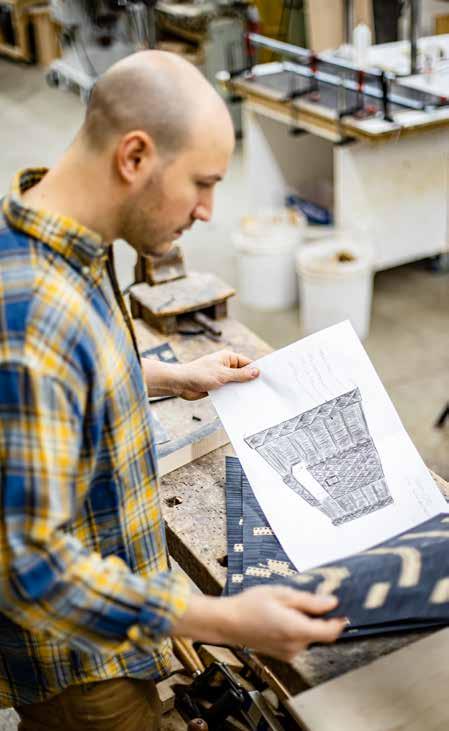
TOP: Cecchi in his workshop BOTTOM: Table designed by Cecchi Alexandre Cecchi is a woodworker and furniture designer from Belgium, now living in Quebec. Through his thoughts and works, he shares his vision of art and contributes, in his own way, to the beauty of the world. Since 2018, Cecchi has been drawing, designing, and manufacturing his own furniture. Putting his technical and artistic skills to good use, it’s a dream come true.
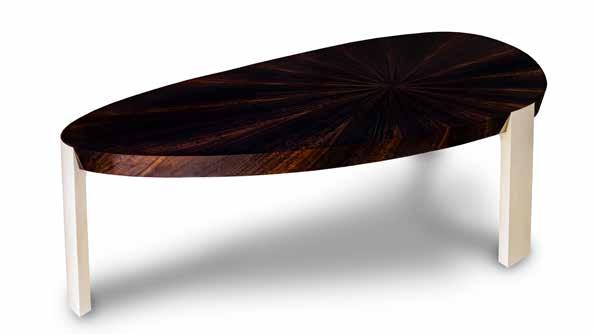
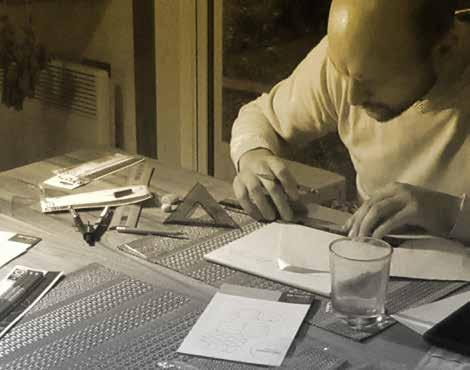
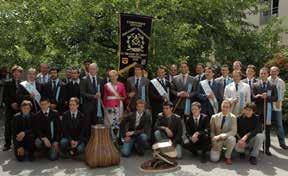
TOP: Cecchi designing a piece LEFT: European Training Institute of the Companions of the Tour de France RIGHT: Cecchi at IEF-CTF ceremony
AN UNUSUAL LEARNING PATH
Cecchi was born into a Belgian family of Italian-Dutch origin. After high school, he entered the European Training Institute of the Companions of the Tour de France (IEF-CTF) to study traditional woodworking. He then traveled around France for eight years to work in various renowned workshops and to train with well-established cabinetmakers.
This companionship is an unusual apprenticeship that began during the construction of the first cathedrals in France. The master taught the apprentices his knowledge so that these exceptional works, sometimes requiring more than 200 years for their construction, could be built. This tradition has been perpetuated from generation to generation until today. It allows the young people who start today on the Tour de France to ask essential questions, acquire a lot of specialized knowledge, and develop invaluable human qualities.
For Cecchi, these years were deeply significant and enriching. To contribute to this long chain of transmission, he invested himself in managing this association for several years. Since his move to Quebec in 2017 to join the Ébéniste d’art workshop, he offers young woodworkers the opportunity to deepen their training across the Atlantic by working alongside him.
A DISTINCTIVE APPROACH TO THE CRAFT
According to Cecchi, a great woodworker is, above all, a great technician. Someone who masters the technique and knows how to systematically use the right methods depending on the work to be done. Since Cecchi only offers unique pieces, each piece of furniture is different and has its own challenges. At all times, he gives his all to meet them as perfectly as possible.
Of course, Cecchi’s extensive technical knowledge allows him to give free rein to his creativity. He can sketch ambitious curves, define harmonious volumes and select the best materials without worrying about assembling them. By constantly refining his art and science, Cecchi follows traditional French woodworking footsteps while undeniably standing out as a furniture designer.
THE CREATIVE PROCESS
Behind each work, there are many hours of conception, reflection, and research to arrive at a coherent project. The starting point can be a specific request from clients or a carte blanche. The emphasis is on aesthetics, creativity, and harmony.
Once the design is attractive, Cecchi engages in technical design. At this stage, it is a question of materializing the original idea in the most perfect way possible. For him, the travel from the 2D plan to a 3D work, made of tangible matter, contains an element of magic.
Once finished, the work is delivered with a certificate of authenticity and carefully installed at the client’s home.
WHEN FURNITURE BECOMES ART
One only has to look at Cecchi’s creations to understand how he sublimates wood and the craft of cabinet making. Each piece is unique, intriguing, and of timeless class. Art enthusiasts and collectors alike will benefit from discovering the world Cecchi offers. He believes that when people buy a piece, they are buying a period in the artist’s life. They are buying concerns. They buy a lot of thoughts. They are also buying years of learning and experience. Finally, they are buying, eventually, a share in the concept of perfection. And you, will you be charmed?
MAKING COMPONENTS AN ART FORM
Old school skill and new school tools
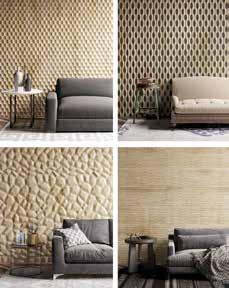
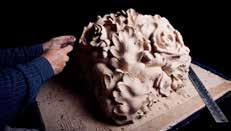
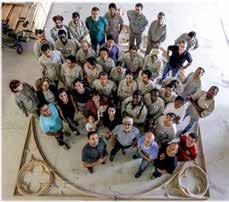
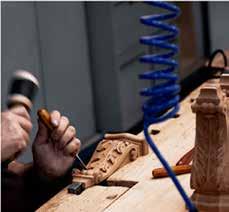
TOP LEFT: Texture panels TOP RIGHT: Art for Everyday artisans BOTTOM LEFT: Custom sculpture BOTTOM RIGHT: Master carver at work
Manoo Mahmoodi started Art for Everyday in his garage with a neighbour back in 1998. Today, Manoo’s son Soroush runs the family business as the president while his father, easing towards retirement, remains CEO.
“We actually still make a lot of things from our very first catalogue,” explained Soroush.
Art for Everyday has a huge catalogue of architectural millwork components. They have about 450 to 500 items in nine different wood pieces, allowing for approximately 5,000 different combinations. Lumber is stocked in alder, hard and soft maple, white oak, red oak, walnut, pine, mahogany, cherry, and hickory. About 1,200 of their components are ready to ship. In terms of their most popular items, their corbels are at the top of the list.
“I would say our five most popular items are all corbels,” he explained. “Besides these, our mouldings and appliqués are quite popular.”
Beyond these, they carry components in a wide variety of categories, everything from textured panels and tiles, to legs and posts, to spools and half-rounds. Each piece goes through a multi-step process, beginning with programming, moving on to blocking, and CNC machining.
These are all processes that Soroush pushed for as he moved up through the company. With an academic background in computer science, he always pushed the company towards technological advancements while never forgetting the importance of hands-on expertise and artistry.
“Half of the work used to be hand done by our master carvers, but now approximately 95% is done by machines, but our master carvers hand finish each piece,” said Soroush. “We can do pretty much anything with wood and a CNC.”
What differentiates Art for Everyday is that post-machining, every piece is hand-finished by carving, chiseling, and sanding by expert sanders and master carvers. And of course, the last step is quality control. It’s this expert touch that brings their pieces to the next level.
All their manufacturing is performed in a 50,000 sq ft. facility located in Toronto with about 50 employees, most of whom are friends, family, or community members. The largest portion of their staff used to be their master carvers, but many of them retired, leaving them with just four, all of whom have been with the company since the beginning.
“Our custom capabilities have garnered the attention of designers, architects, DIYers, kitchen cabinet makers, etc., worldwide,” said Soroush. “Our clients mainly work in kitchen design, but we also cater to interior design and architectural firms.”
They have an extensive list of over 10,000 clients, going far beyond these typical customers. They also have a history of working with places of worship and governments, creating unique, intricate pieces. Their range is incurably wide, everything from solid walnut benches, like something you would find in a courthouse, to animal carvings. Their creativity and intricacy are limitless, and their work lives up to their name.
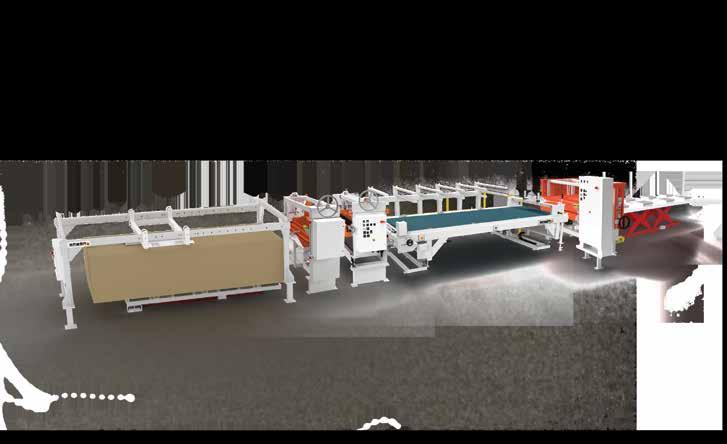
Scan for Video

Introducing


MANUAL AIRSPRAY GUNS
FPRO G FPRO GSP
FPRO G WITH SMART CUP
3 atomization & aircap technologies High spraying quality for viscous products Ergonomic and robust design
UNBUILDING TO BUILD SOMETHING
NEW By Grace Tatigian
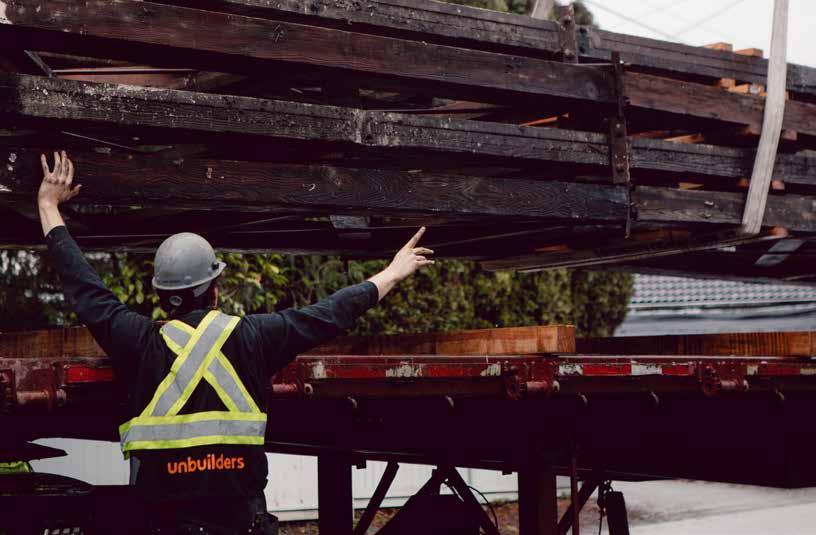
The cost of materials — lumber in particular — has been staggering for the last year or so. While it looks like it’s finally starting to drop, this has negatively impacted many businesses. One business that it benefitted, however, was Unbuilders. Unbuilders is a team of salvage experts. They are former carpenters, roofers, framers, and tradespeople who have made the switch from construction to deconstruction.
“Our vision is a construction industry where deconstruction and remanufacturing replaces demolition and disposal,” explains owner Adam Corneil.
Corneil flipped his first house at the age of 16 with his dad, and his love of construction stuck with him all his life, and now that he’s a father himself, it’s his full-time job.
“I felt like I was watching every other house get demolished, and I just kept thinking, ‘this is insane,’” he said. “Demolition just isn’t sustainable. So Unbuilders will have work until they learn how to make buildings that will last forever.”
Part of what contributes to longerlasting buildings is higher-quality materials, which is exactly what Unbuilders is pulling out of these deconstruction sites.
“It’s better wood,” he explained. “Most of what’s used today is lower quality spruce, whereas we’re pulling Douglas fir out of these buildings to be reused. We’re recovering irreplaceable lumber.”
And so what are they doing with this wood? In the past, they’ve partnered with artisan companies that make furniture, cutting boards, garden boxes, and more, but they’re working on growing internally.
“We actually just leased a facility where we can start remanufacturing the wood ourselves,” he told me. “It’s an acre of land that will have 10,000 square feet for showrooms, offices, and shops. We’ll also have a receiving yard and landfill space.”
They had started out searching for a warehouse, but that kind of real estate in Vancouver is hard to come by at a reasonable price. This ended up working out perfectly, checking a whole bunch of boxes they didn’t realize they had. Now




Unbuilders team organizing salvaged materials
they’re getting set up to better supply building materials to companies looking to build green. I was curious how the cost of lumber had impacted the sale prices of their reclaimed wood.
“Typically, 2X4s and shiplap are the hardest to move, so we price them cheaper, but now we can’t even keep 2X4s in stock,” he told me. “We sell out before we even have the chance to remove the old nails.”
So one good thing to come out of the lumber price spike was that it closed the gap between the cost of reclaimed wood and new wood, encouraging more companies to greener building materials.
“There’s half as much embodied carbon in these old building materials,” explained Corneil.
That comes not only from the kind of wood but also how it was harvested and how it was constructed. Most of the sites that they’re unbuilding are pre-1950s, building dates averaging out to around 1930. These are also the cases that have the highest value of lumber. There’s a good mix of residential and commercial buildings throughout the Vancouver and Victoria area that they work on.
“I’m torn a lot of the time. Often the buildings we’re taking down have a lot of cultural significance; there’s a lot of heritage there,” explained Corneil. “But it’s not my call as to whether the building gets removed or not. We can remove the building in a way that’s environmentally friendly, socially conscious, and communitydriven. Then the materials can be reused and respected instead of just demolishing it and everything ending up in a landfill.”
Corneil has always been an environmentalist, but this side of him was nurtured in university when he studied philosophy and anthropology. While it might not seem like these topics have a lot to do with deconstruction, they helped to shape his worldview.
“Having a building torn down can be an emotional event for a community. We ensure that we respect the stories and neighbours to whom these structures play an important role,” said Corneil. “We save these histories by giving materials a new life, typically turning negative experiences into positive ones.”
Corneil also pointed out that Vancouver is the demolition capital of the world.
“The industry shift to deconstruction has massively positive environmental & social impacts. Currently, 4 million tonnes of waste are diverted annually,” he told me. “But we can’t expect people to shift their perspective and budget when it comes to deconstruction just because we say so.”
As such, their approach takes a ton of factors into account to show their customers that this is the best option for everyone.
“Deconstruction generates six jobs to every one demolition job – creating the potential for 75,000 new jobs nationally,” Corneil explained from the social perspective. “The jobs Unbuilders provides allow young workers to contribute meaningfully to lessening waste in our society.”
But if ethical reasoning isn’t enough to convince their customers, the numbers speak for themselves.
“It can actually cost less to use us than a typical demolition service,” he explained. “Once you factor in the provincial and federal tax credits, it can cost about $12,000 less to deconstruct than it can to demolish a 2,400 square foot home, for example.”
It’s a setup that benefits everyone: the building owners, the builders, the Unbuilders, the community, and the environment. And if that isn’t sustainable, then I don’t know what is.
2021
Nov. 4 - Nov. 6, 2021 | International Centre | Mississauga (Toronto), CA
WMS is the professional woodworking show for all of Canada WMS has connected Canada’s professional woodworking industry with the world’s most prominent machinery manufacturers, material suppliers, hardware companies and other services and products for more than four decades. 86% of 2019 attendees said they plan to attend WMS 2021!
Can’t miss WMS 2021 programs: • WMS Live – On-the-show-floor presentation stage offering free education sessions to attendees on a range of timely manufacturing, technology and other hot topics. • Off Campus Tech Tours – Attendees will have the opportunity to register to tour local facilities in the Toronto area to see the latest technologies in action. • New App – WMS attendees can take advantage of a sophisticated mobile/web app to optimize their experience before, during and after the event. Utilizing the robust Whova platform, the app will facilitate planning, networking, logistical considerations, and a host of other features that can be accessed. • Happy Hour Events – The first two days of the show will conclude with an opportunity to unwind with a drink and talk shop with fellow attendees.
Registration Opens Early August Nov. 4-6, 2021
WMSCanada.ca
To reserve exhibit space: Rich Widick | WMS Sales wms@heiexpo.com (630) 434-7779 For general conference and show information: Harry Urban | Woodworking Network harry.urban@woodworkingnetwork.com (708) 373-4344