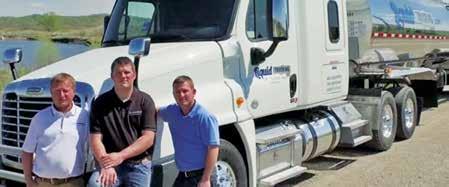
32 minute read
Innovators: Liquid Trucking
INNOVATORS
LIQUID TRUCKING Plattsmouth, Neb.
Advertisement
Roger Schmidt (left) founded Liquid Trucking. His son, Gabe (middle), is director of operations, and Josh Schmidt (right) is general manager.
Liquid Trucking rewards reconnaissance FREIGHT ‘LIQUIDITY’
BY AARON HUFF E very time a trucking company loses a tenured driver, the institutional knowledge the driver gained by working for the company walks out the door.
As a tanker and hazardous materials carrier, Liquid Trucking has many safety and customer service procedures to learn to avoid accidents and spills at thousands of locations every year. Getting drivers accurate information in a timely manner – like where to turn at each customer site, what to avoid, who to ask for and what numbers to call – always had been a challenge.
A er looking at di erent technology products to address the need, in 2015 the owners and management of Liquid Trucking decided to invest in developing a proprietary mobile application that would allow drivers to share location intelligence and access everything they needed to do their jobs. e DeliveRecon app, released later that year, gives drivers the ability to share their knowledge through editable elds to update addresses, phone numbers and instructions by adding text, photos, videos and audio clips. e uploads are approved by a safety manager and enter DeliveRecon’s database in the cloud. e app also has a two-way integration with TMWSuite, a transportation management system that Liquid Trucking uses from Trimble, to automatically export customer locations to DeliveRecon and update approved edits from drivers to the location elds in TMWSuite.
With DeliveRecon, Liquid Trucking is able to capture and redistribute all the information that previously walked out the door. When dispatched on a route, to see location information, drivers simply tap a “Near Me” function to view nearby customers, tank washes and site-speci c instructions instantly.
“We’re letting the drivers essentially train one another,” said Jason Eisenmann, human resources director for the Plattsmouth, Neb.-based eet. “Our newer drivers are able to hit the ground running.” DeliveRecon also has work ow tools for drivers to capture and index proof-of-delivery documents and le incident reports.
In January 2016, Liquid Trucking spun o a separate company, Epic Ideas, to develop a commercial enterprise version of DeliveRecon by partnering with Volano Solutions, an Omaha, Nebraska-based so ware development rm.
Epic Ideas is o ering DeliveRecon to the industry as a mobile platform that combines location-based mobile customer relationship management (CRM), automated work ow and connectivity features to the transportation industry through a So ware-as-a-Service.
A fluid business model
Liquid Trucking was born in 1994 when Roger Schmidt and Mike Beins started a new venture called OFC/Schmidt Liquid Services. Schmidt previously had founded a dry van carrier in 1989 that by 1994 had grown to 10 trucks.
A pivotal moment in the business came in the early 2000s during a mad cow disease outbreak in Europe. e disease created a scare in the United States, and shippers required carriers to wash out trailers before loading animal feed. is event caused Schmidt to research trailer wash facilities. He drove to locations nationwide before starting construction on a wash bay south of Omaha near the Missouri River in Plattsmouth. e wash facility has a steam boiler, a high-speed spinner and other tools and equipment. It is Kosher-certi ed and has washouts for all food-grade and feed-grade commodities, chemicals and
The tank carrier leverages its driver pay structure, rewards program, surveys and mobile app as it adjusts to new market opportunities.
hazardous materials. OFC/Schmidt Liquid Services also built an onsite wastewater treatment plant.
With the state-of-the-art wash bays, the company is able to haul any type of bulk liquid at any time, from food and feed-grade products to hazardous materials and chemicals, with its eet of 180 tractors and 310 trailers.
Its uid business model has adapted quickly to the economic disruption caused by COVID-19. As freight volumes for fuel and ethanol commodities declined, management shi ed capacity to food-grade products and chemicals. Alcohol has been in especially high demand to manufacture hand sanitizer.
Rewarding drivers
In 2009, the Federal Motor Carrier Safety Administration was targeting hazmat carriers for enforcement prior to rolling out the Compliance, Safety, Administration (CSA) program. Liquid Trucking adopted electronic logs and in 2010 used the technology to improve driver pay and safety by creating an hourly pay system. e pay program is performancebased and starts at $23.75 an hour. Drivers who have higher performance in the measurement areas of fuel, revenue and safety can earn up to $3 extra a er their rst 13 weeks.
“We feel like we are rewarding the right areas,” said Josh Schmidt, general manager, who credits the pay program for attracting and retaining highercaliber drivers.
During the past ve years, the company’s driver retention rate has improved by more than 50% as management has focused on increasing driver satisfaction and engagement.
Liquid Trucking uses an in-depth annual Driver Satisfaction Survey from Stay Metrics to sharpen its focus on areas of opportunity to improve the work experience. One area where survey results have proven useful is by scoring dispatchers on behaviors and skills that correlate with driver retention, Eisenmann said.
To increase driver engagement, Liquid Trucking also rewards them for their reconnaissance e orts. On average, the DeliveRecon app is getting 116 di erent location updates from drivers every month. e company is using a custombranded online rewards platform from Stay Metrics and has a reward category for DeliveRecon updates, adding to other reward categories in safety, customer service, training and other measurable areas.
Over the last four years, the company has awarded 1.5 million points to drivers for their DeliveRecon updates. Each point is worth half-a-cent, and the $75,000 spent is worthwhile for having accurate data for all locations, said Josh Schmidt.
During COVID-19, management has seen drivers send an in ux of changes such as posters, banners and handmade signs at customer locations with new delivery instructions, Eisenmann said.
From 2015 to 2019, Liquid Trucking has seen, on average, a 43% drop in accidents and incidents every year, which Eisenmann credits to DeliveRecon and ongoing safety training and initiatives.
All hands on deck
Like most carriers, management of Liquid Trucking put in place new procedures to protect employees from COVID-19. Starting March 14, the company’s o ce and shop doors were locked to restrict access to only employees whose jobs cannot be done at home, such as drivers, mechanics, the tank wash team and a handful of dispatchers.
Jason Eisenmann, director of human resources, led the development of DeliveRecon, a mobile app that drivers use to optimize their work. By using the DeliveRecon app, Liquid Trucking drivers can update information about customer sites.
Additional steps to prevent contagion include setting up exterior handwashing stations and portable toilets, installing plexiglass around o ce cubicles and enforcing the 6-foot social distancing rule.
So far, disruption from the coronavirus has been minimal compared to another crisis that happened one year ago. In March 2019, heavy rains in Nebraska and other Midwestern states caused ooding of the Missouri River and its tributaries.
Liquid Trucking had 12 hours to prepare for the imminent ooding of its headquarters. e property remained under water for several days and reached 10 feet deep in some areas.
Roger Schmidt, the company’s president, said everyone at Liquid Trucking pitched in and did whatever was necessary. He describes the company’s management structure as “ at” whenever things need to be done quickly.
“We all kind of throw our gear on and do what we’ve got to do,” he said. “Everybody gets involved, and it is really transparent to employees and everyone around us.”
Just as employees pitched in to help Liquid Trucking emerge from the ood, they have all “been out there working their tail o ” to keep the business running during COVID-19, Josh Schmidt said.
When the economy starts to re back up, “we believe it is going to have a huge bounce back, and we want to be ready when that happens,” he said.
CCJ INNOVATORS pro les carriers and eets that have found innovative ways to overcome trucking’s challenges. If you know a carrier that has displayed innovation, contact Jason Cannon at jasoncannon@randallreilly.com.
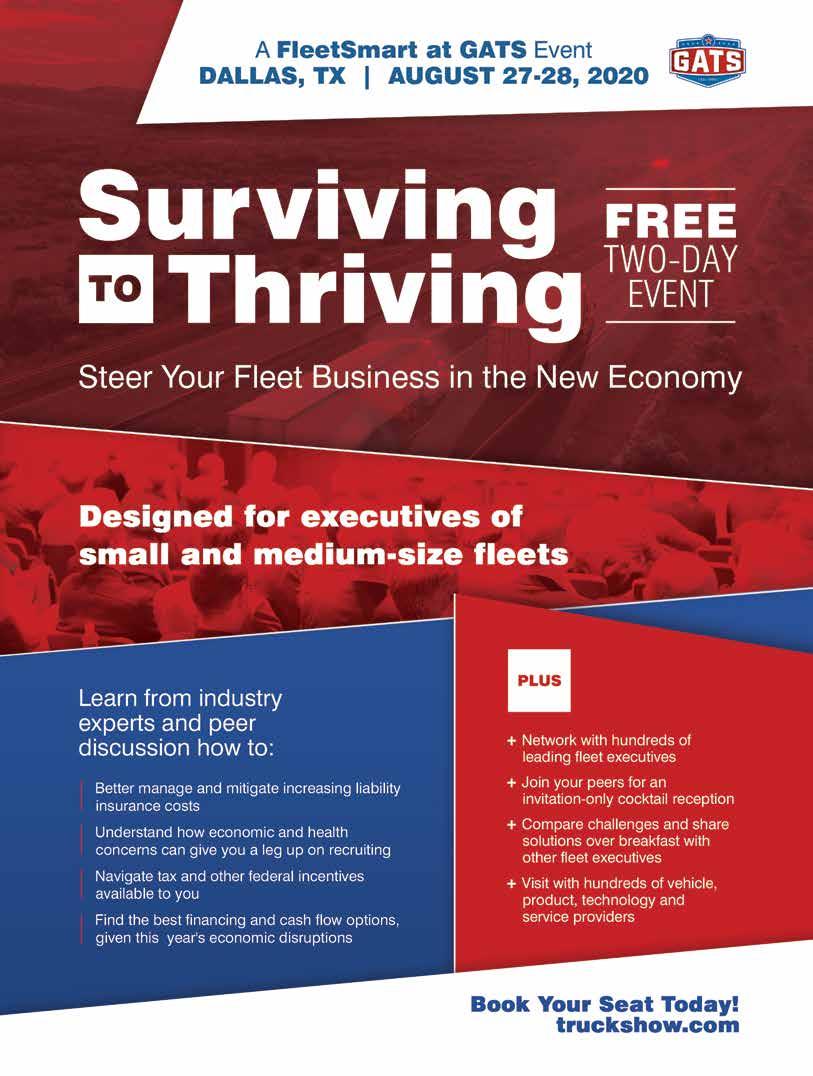
COVID-19 COPING WITH
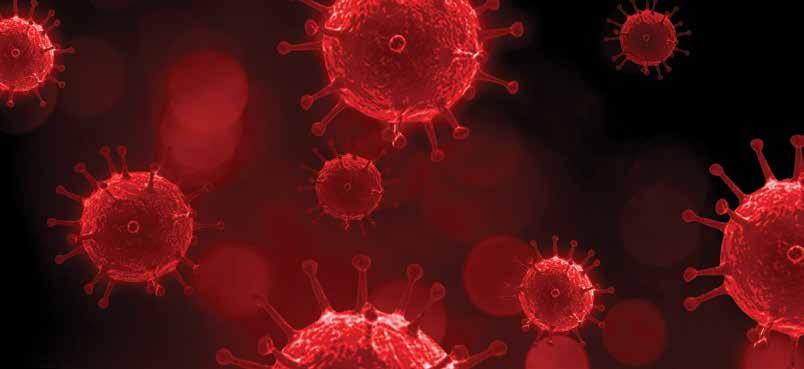
All corners of trucking industry rise to occasion, respond to pandemic’s health, economic challenges
BY JASON CANNON, AARON HUFF, TOM QUIMBY, JAMES JAILLET AND DEAN SMALLWOOD M any economic signals indicated that U.S. businesses, and the trucking industry along with them, could see a nice rebound from a ho-hum 2019 and that retail, manufacturing, construction and employment all would enjoy a beneficial environment in 2020.
No one could have predicted that a once-in-a-century contagion would bring it all crashing down.
COVID-19 sprang from Wuhan, China, in late 2019 and quickly spread around the globe, despite most nations’ desperate attempts to halt a mysterious virus that didn’t meet a political border it couldn’t circumnavigate, even across oceans. Most countries, in an attempt to corral the deadly coronavirus for which there was no immunization, issued stayat-home orders and shuttered what were deemed nonessential businesses, wrecking economies worldwide and sending panicked shoppers scrambling to the few stores that were open to snap up what they deemed were life necessities, which included toilet paper.
Trucking was not immune from COVID-19’s economic toll, as the coronavirus impacted every corner of
Trucking defense attorney Doug Marcello said COVID-19 has positively improved the public’s perception of the trucking industry, which could help win over jurors in future court cases.
MAY TRUCK, TRAILER ORDERS LOOM LARGE
What was already a bleak outlook for truck freight activity turned a little bleaker in mid-April. Forecasting firm FTR last month revised its forecast for truck loadings this year, now forecasting a 9% overall decline for 2020 compared to the previous year, down from its previous forecast of a 4% drop that had been issued in late March.
“All segments we see as being negative for the year,” said Avery Vise, vice president of trucking for FTR. Refrigerated freight was forecasted to tick upward slightly, but the forecast for that segment also trended negative.
Flatbed freight, meanwhile, was in a collapse. Hous ing starts had plummeted since the onset of COVID-19, as had other construction segments. Manufacturing activity also had fallen to an “extreme level to fathom,” said Jonathan Starks, chief intelligence officer for FTR.
Orders for trailers and Class 8 trucks were depressed in March and were expected to remain at near-record
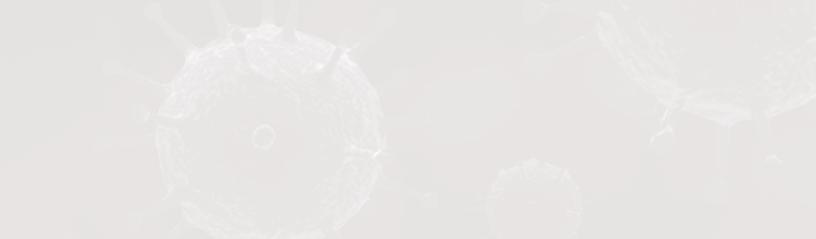
lows in April. May’s orders, however, are anticipated to provide a pivotal window into “how deep we’re in and how far we need to dig out,” said Don Ake, vice president of commercial vehicles for FTR. May truck and trailer orders were predicted to be “one of the first signals” as to whether a potential recovery could begin later this year.
Starks said FTR did expect economic indicators around truck freight to turn positive later this year, though it still would be a “very weak environment” for
FLEET CEO GETS BEHIND THE WHEEL
In early March, grocery stores began running low on inventory as COVID-19 was spreading in the United States. Randy Timms started to think of people in small towns with limited shopping options and how he could help.
Western Flyer Express (WFX) had a new contract with a grocery distributor to deliver to small towns in Oklahoma and Texas. As the company’s chief executive offi cer, Timms saw an opportunity to join the front-line response to the pandemic and to “show everyone within my company that, at end of the day, the most important people we have are drivers.”
Timms founded WFX in 1991 with his father. As a business owner, he always had a commercial driver’s
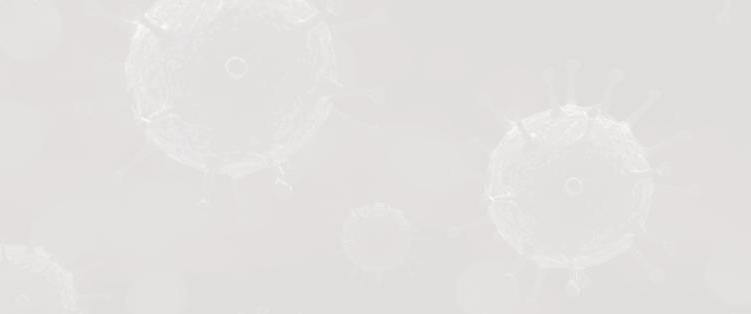
license but never drove for an extended period of time as the Oklahoma City-based fl eet grew to operate more than 1,000 trucks with company drivers and contractors.
On Saturday, March 21, Timms stepped out of the offi ce and into the driver’s seat to make urgent grocery deliveries to out-of-stock stores for the customer.
“It’s important, in this time of crisis, for our drivers and contractors to know the entire WFX team is behind them as we execute,” he said. “We couldn’t be more appreciative of them and their incredibly important role in supporting America.”
With few exceptions, drivers at WFX did not express concerns about working during COVID-19.
Randy Timms, CEO for Western Flyer Express, made timely deliveries to small grocery stores in Oklahoma and Texas.
“They are out there doing their job,” he said. “It’s been pretty great to see. I anticipated it was going to be challenging.”
Timms didn’t go alone. He returned home for three nights, and each time he picked up a diff erent family member to come along. His wife joined him for an extended trip, and his son and daughter joined him on shorter trips.
“I wanted them to be involved,” he said.
the industry, from eets of all types – truckload, reefer, less than truckload, atbed, nal mile, even hotshot – to truck makers, repair shops, dealers, truck stops and all their customers. While some truckers decided to sit COVID-19 out, many risked their own health to do the jobs they knew were vital to keeping the nation’s supply of essentials moving from supplier to consumer.
As a result, the industry has seen a noteworthy boost in positive opinion among an American public who normally sees it as not much more than big dangerous vehicles speeding down the interstate driven by unshaven washouts.
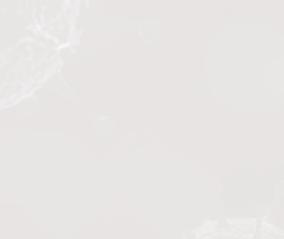
trucking activity.
A potential bright spot? Though the economic trough could be as harsh as the 2008-09 recession, it could play out in a much shorter time span, Starks said. A recession more than a decade ago that unfolded over four to fi ve quarters could play out in just one to two quarters this time.
“Moving forward, we see positive numbers,” Starks said. “We just had such a rapid destruction. … We won’t make up all those lost results for at least a year and a half.”
Drivers reporting symptoms
In the days and weeks following the outbreak, eets were faced with an unsettling and mostly unprecedented task: Navigating the humanitarian and logistical questions surrounding drivers reporting symptoms of or testing positive for COVID-19 while on the job.
Drivers’ inability to self-isolate, the job’s mobile nature and the need to go into public places such as truck stops put them at a higher risk of infection than those who quarantined inside their home.
If a driver did exhibit symptoms or test positive, eets faced a myriad of immediate and disconcerting challenges, including, most importantly, helping the driver nd medical care or nding a place for them to quarantine.
“ ey can’t be stuck out there by themselves,” said Brian Fielkow, chief executive o cer for Jetco Delivery, a Houston-based 130-truck eet and part of the larger Montreal-based GTI Group. “It’s our job to support them if that would happen.”
Secondary to helping care for or quarantine drivers was considering retrieving equipment and loads that might be stranded and, in accordance with Centers for Disease Control (CDC) guidelines, notifying employees at shippers and receivers with whom the driver may have come into contact.
Fleets needed to get drivers “home and out of the truck as soon as possible,” said Travis Vance, an attorney for the rm Fisher Phillips, and have them “avoid interaction with customers and cargo, because [the virus] can live on surfaces for three to four days.”
If a driver reported they were feeling too sick to drive, “you don’t want him operating anymore,” said Jack Finklea, a partner and attorney for Scopelitis, Garvin, Light, Hansen & Feary. If a driver did feel OK to operate, eets could send a replacement truck to retrieve the driver’s trailer and load and have the driver either return to a terminal to get home or nd a safe place to park.
If a driver did exhibit COVID-19 symptoms or test positive, fl eets faced a myriad of immediate and disconcerting challenges.
New tech helps LTL giant Saia work from home
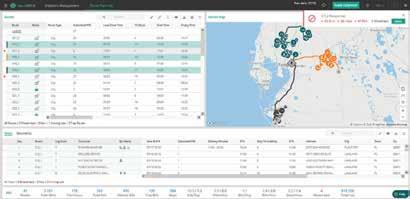
Last year, less-than-truckload carrier Saia (CCJ
Top 250, No. 24) began implementing a technology across its terminal network to pre-plan routes for pickups and deliveries. That decision to use Optym’s RouteMax paid extra dividends with COVID-19 causing disruption.
“The network is changing,” said Rohit Lal, vice president and chief information officer for Saia. Among those changes were shippers and receivers shortening their business hours and moving appointments, as well as greater fluctuations in load volumes.
To complicate matters, Saia’s load planners and other front-office employees were working from home. Lal said that without the software, it would have been difficult for the Johns Creek, Georgia-based company to manage the rapid changes to its network during the pandemic.
Saia’s load planners were able to update appointment times for shipments, plan routes further in advance and respond more quickly when pickups and deliveries need to be rerouted on the fly.
RouteMax is replacing Saia’s legacy route planning application that the fleet developed internally. During the rollout’s initial stages, Optym worked “very closely” with Saia’s engineering, operations and IT departments to “look at our processes,” Lal said. Optym employees went on rides with drivers and gathered feedback from dockworkers.
Saia’s legacy application was short on graphical tools, and users relied on tribal knowledge to finalize plans for routes that were organized by ZIP codes. RouteMax’s optimization engine and visualization tools have made it possible for planners to be more productive, make real-time adjustments and perform “what-if” simulations as Saia’s business changes throughout the day, Lal said.
After plans are finalized, RouteMax sends proactive notifications to Saia’s planners about pending issues based on realtime data changes from linehaul and dock operations, such as heavy traffic, new bills, reweighs and more.
Saia is using Optym’s RouteMax software to optimize pickup-and-delivery routes for its nationwide terminal network.
TRUCKS SPEED UP
Mass quarantines and mandatory remote work policies designed to limit the spread of COVID-19, while inconvenient for legions of homebound motorists, meant the lack of vehicles on U.S. highways skyrocketed the productivity of many truckers in areas historically plagued with the worst traffic congestion.
“Huge metro areas still have traffic, but nothing like the normal,” said Jamie Hagen, owner/driver for Aber deen, S.D.-based bulk hauler Hellbent Xpress. “Literally cruising right through without slowing down.”
Data from transportation analytics firm INRIX showed that in the span of one week, from March 13 to March 20, traffic went from “reduced congestion” to “free-flow” in America’s 25 largest metropolitan areas. Chicago and Los Angeles saw afternoon travel speed increases of 35% and 38% above average to 74% and 75% above average in one week as the scale of containment expanded.
Trucks sped up due to a dramatic reduction in commuter traffic and their continuous 24/7 operations that generated higher average truck speeds across nearly all hours of the day.
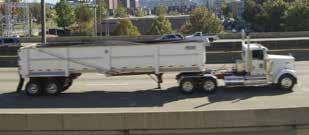
Driver Jack DeRubeis said traffic through Dallas was “flowing smoothly compared to stop-and-go traffic.” The I-45/I-30 interchange in Dallas is No. 18 on the American Transportation Research Institute’s (ATRI) bottleneck list. U.S. 75 at I-635 is No. 43.
ATRI pulled real-time GPS data from more than a million trucks to analyze freight flows. According to ATRI’s data, at the northeast intersection of I-85 and I-285 in Atlanta, known locally as “Spaghetti Junction,” afternoon rush hour truck speeds typically are under 15 mph due to congestion.
INRIX data pegs Atlanta as the 10th most-congested

urban area in the United States with 82 hours lost sitting in traffic last year. The week after the outbreak went big time, ATRI showed truck speeds averaged 53 mph.
The states hit hardest by COVID-19 – New York, California and Illinois – also saw some of the largest gains in overall truck speed.
“As other traffic dissipates, trucks continue to move, delivering much-needed relief supplies to markets, hospitals, gas stations and other essential businesses,” said Rebecca Brewster, ATRI president and chief operat ing officer.
P&D PONIES UP
At a time when the nation’s unemployment rate was soaring, Amazon was hiring.
Major players in the pickup-and-delivery segment such as Amazon faced several changes amid COVID-19, including shifts in delivery volume as millions of people across the United States sheltered in place and avoided going out in public to work or shop. Instead, they worked and shopped from home, which kept P&D companies on the move.
The company temporarily prioritized household staples, medical supplies and other high-demand products coming into its fulfillment centers so it could receive, restock and ship those products more quickly.
To help meet the surge in demand, Amazon opened 100,000 new full- and part-time positions within its delivery network and at fulfillment centers nationwide. The company also offered pay raises and switched to
Amazon handles deliveries for roughly half of its online orders and leans heavily on the U.S. Postal Service and UPS to handle the rest.

video-based interviews for most of its applicants.
Amazon handles deliveries for roughly half of its on line orders and leans heavily on the U.S. Postal Service and UPS (CCJ Top 250, No. 1) to handle the rest.
Although deliveries for UPS had grown in some areas, they didn’t look to bulk up their workforce, citing a mixed bag for business depending on the region. The company leaned on the Coyote Logistics freight brokerage to help with deliveries when needed, said Dan McMackin, public relations manager for UPS.
Some deliveries proved exceptionally vital during

the pandemic. FedEx (No. 2) transported COVID-19 test specimens from drive-through testing centers at major retailers. FedEx dedicated dozens of flight legs and specialized pickup-and-delivery operations that were aided by the U.S. Department of Health and Human Services.
“We have a great responsibility in these unprec edented times to do what we do best — mobilize our network quickly to help the communities where we live and work,” said Raj Subramaniam, president and chief operating officer for FedEx Corp.
Specialized carriers turn to SBA for help
Allen Farms in Norman,Oklahoma, became a lot more popular during the pandemic, since retail sales of sod were soaring.
“Before the weather even broke a little bit, the phone was ringing off the hook,” said Allen Farms owner Kevin Andrews, who also owns an automobile-hauling business that saw roughly half its revenue wither during shelter-in-place directives brought on by COVID-19.
While commercial sales also were underway at Allen Farms, the record retail sales stood out. Plenty of grass spread out over 90 acres was a sight for sore eyes for homebound yardwork warriors itching to get outside.
“We’re seeing people with masks and gloves on that are completely stir-crazy,” Andrews said.
For Andrews’ car hauling business, Dave Meeker Auto, business was the polar opposite.
“What we’re finding is that we’re running about 50%,” Andrews said in mid-April. “Last Monday morning, we billed out about maybe 60% to 65% of our norm. This week we billed out about 45%.”
Car dealerships weren’t selling as much, which idled trucks. Based in Purcell, Oklahoma, Dave Meeker Auto has a dispatcher in Branson, Missouri, and a brokerage office in Pensacola, Florida.
Most of Andrews’ drivers are owner-operators based in Branson, where the business originated. Normally, 20 to 25 trucks would have been hauling for Andrews. Some were waiting out the pandemic at home, while others still hit the road, where Andrews said the used auto market had enjoyed more business over new sales.
“We haul primarily used cars,” he said. “We’re not hit as hard as the new car carriers are. We’re also limited to a lot of our auctions that we haul out of, because they’ve either shortened hours or are closed on the weekends.”
To help make ends meet, Andrews turned to the U.S. Small Business Administration’s Paycheck Protection Program for help and was approved for a loan.
Chris Olson, owner of SOS Transportation in Carlton, Oregon, has been hauling for special events such as concerts, plays and trade shows since the 1970s. For the first time, he saw all his trucks and those of his competitors come to an abrupt stop.
“It’s weird parking all the trucks,” Olson said. “They’re just parked.”
Unlike during the Great Depression in the 1930s when people flocked to the movies to escape their woes for pennies a show, movies theaters had rolled up their red carpets, as had concerts, plays, trade shows and other special events. A niche market for carriers was completely dead with nationwide shelter-in-place directives.
Kevin Andrews, owner of Allen Farms and Dave Meeker Auto, with his daughter, Emma, picking up a truck he bought in Kansas about a year ago.
Olson’s dry vans, like others in his line of work, are specialized. Still, he considered hauling freight to help pick up the slack until he was offered a paltry rate of a dollar a mile to haul from California to Iowa and New York.
For the first time since hitting the road as a truck driver in the early ’70s, Olson turned to the government for help. Like Andrews, Olson’s company also was approved for an SBA loan.
As it turns out, Andrews and Olson applied for and received their business loans just before they dried up in mid-April. SBA’s first-come first-serve $349 billion Paycheck Protection Program ran out of cash in less than two weeks.
Olson, who favors Kenworth trucks, had hoped to put his 10 rigs back to work in July for a major concert. So far, the event hadn’t been canceled.
“We’ll see,” Olson said. “I’m old. I would go to work if I get the chance. If I get the stuff (COVID-19) and it kills me, then it kills me. We need to start the country back up.”
The 2021 Ram ProMaster with additional safety features was unveiled recently at the Work Truck Show in Indianapolis.
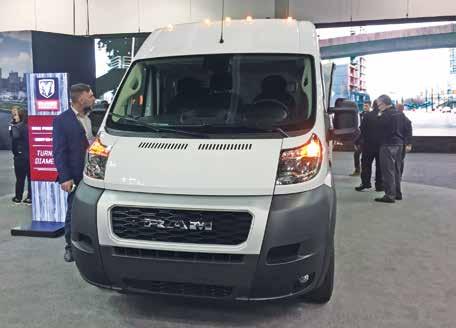
E-commerce, P&D spur demand for light vans
While COVID-19 brought production freezes and huge sales losses for major auto manufacturers, two industry giants reported increased demand for vehicles that don’t exactly play starring roles at local dealers.
Both Ford and Ram saw higher demand for vans that support pickupand-delivery operations, which got a nice boost from increased e-commerce sales through growing shelter-in-place directives.
“We have seen some additional requests for additional Transit production
HOTSHOT TRUCKING: FREIGHT DYNAMICS SHIFT
Prior to COVID-19, hotshot haulers in Oklahoma and Texas already had been hit with a drop-off in work owed to sinking oil prices. Then came the pandemic, which cut prices even further, along with load demand among oil companies and supporting businesses.
“As soon as oil gets below $40 or $50 a barrel, everybody quits pumping, which means that everyone working in the oilfield is out of work, and everybody who delivers to them is out of work, and anyone who works in the area is out of work, because there’s no other freight really,” said Aaron Hammer, owner of Eagle Hot Shot, based in Jenks, Oklahoma.
With oilfield work all but dried up, dispatchers were calling with loads related to pandemic relief. “Almost all of the stuff we’re hauling right now is COVID disaster relief stuff,” Hammer said last month. “We hauled sanitation tanks for companies to make hand sanitizer. We hauled a bunch of masks the other day. We hauled some tractor equipment for farms that are growing produce as they try to keep everything stocked.”
Ben Thompson, founder and chief executive officer of HotShot 107, said his company saw an uptick in work that’s wasn’t directly related to COVID-19 relief efforts. The Ohio-based company offers startup as sistance and dispatch services to small and mid-sized trucking companies.
“We’ve seen an increase in available loads and an increase in some of the rates on the things we’re haul ing,” Thompson said last month. “A lot of what we haul is steel, light loads of lumber, agricultural equipment, light mechanical industrial components.”
Indiana-based Wave Express, specializing in hotshot RV hauling, was among some actively recruiting drivers to work a new freight source: Transporting RVs to be

Hotshot companies asked interested pickup owners to turn to them for work hauling RVs for healthcare responses to COVID-19.

used for mobile medical offices, testing facilities and sleeping quarters.
As for Hotshot 107, Thompson said, “Maybe for us so far, it’s just been the availability of trucks where some guys may be taking off or getting home or being nervous about the coronavirus.”
in the package delivery vocation,” said Elizabeth Kraft, Ford’s commercial vehicle communications manager.
Ram also reported more sales for vehicles that support online shopping. “As for P&D, we have seen an uptick in vans and chassis applications for support,” said Trevor Dorchies, Ram spokesperson.
Some bargains were to be had during the pandemic. For qualifying buyers, dealers stepped up zero-down interest-free loans for 72 and 84 months.
“Nearly 20% of all loans in March were 84-month compared to 8% last month, so its acceptance as a mainstream option has exploded on the scene,” said Tyson Jominy, a J.D. Power vice president who leads the company’s data and analytics consulting division.
“Not only are there great deals in the market and will be in the future, we are also seeing a shift to online sales from this event, making buying a vehicle easier than ever,” Jominy said. “Dealers are willing to do all the negotiating over email or phone, and the vehicle can be delivered to your home or place of business. You need not ever step in a dealership if you don’t want to or can’t.”
While encouraging, it’ll take a lot more than a promising P&D market to get auto sales back on target. Stay-athome directives may lead to about an 80% drop from initial forecasts and could result in 2 to 3.5 million lost vehicle sales this year, Jominy said.
Positive test, attitude for fleet executive
It could have been a much different story for Bob Reese and Packer Transportation if he and others he was traveling with had not followed instructions to self-quarantine after returning from Europe in March.
Reese, general manager for Packer – a Reno, Nevada-based flatbed and brokerage company – said he, his girlfriend and two friends who traveled with them to Ireland were told by the U.S. Centers for Disease Control (CDC) to stay home for at least two weeks and note any symptoms that might be related to COVID-19, including an increase in body temperature.
Good thing, too. Reese, his girlfriend – a registered nurse – and their two friends began showing symptoms not long after touching down in the States.
“It was just a couple of days later that the fever and the cough started developing,” said Reese, who was the first in his group to get tested for the virus. “They jab that swab up there (in your nose) pretty far. It makes you shudder a little bit.”
He was tested March 23, and the test results came back positive that night. His girlfriend also tested positive for the virus, along with their two friends. Quarantine continued through late April, which was fine with Reese, who no longer was exhibiting symptoms and credited the CDC for keeping him and his friends away from others, particularly those with health issues at work.
Though some COVID-19 patients have reported severe symptoms requiring hospitalization, Reese said that wasn’t the case for him and his friends. He and his girlfriend stuck to an over-the-counter regimen that included vitamin C, echinacea, turmeric and ibuprofen.
“The symptoms were very manageable,” Reese said. “There was a little congestion — some nasal and chest congestion. There were a couple days of mild fever. We were
Bob Reese has been GM for Packer Transportation since 2004.
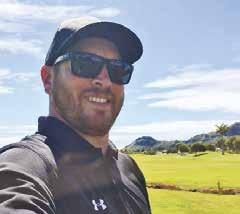
monitoring our temperatures, and it never got over 100 degrees. Took some Advil and got lots of sleep, drank lots of water and actually worked from home the whole time.”
Remaining symptom-free, however, is only part of the battle. COVID-19 testing through the Washoe County Health District was another.
“The tests have kept coming back positive even though we were symptom-free,” Reese said. “When we asked the health department why that would be, the senior immunologist said particles of the virus can still reside in your airways or sinuses for up to six weeks.”
Like so many other companies, Packer implemented new procedures, including social distancing, to help lower the risk for exposure to the virus. They’ve also been handling paperwork electronically to reduce foot traffic in the office and person-toperson contact.
“Anybody that has to (manually) process paperwork is using gloves and masks, and we have eliminated drivers from coming into the office,” Reese said. “We have a person who goes out to collect paperwork.”
Though Packer was feeling the pinch from the shutdown of construction sites in neighboring California, Packer had not laid off any employees as of late April and was hiring drivers.
Dealers under pressure to maintain service
Montgomery, Alabama-based truck dealership Four Star Freightliner followed Centers for Disease Control (CDC) recommendations for the cleaning of hard surfaces and installed sanitizer dispensers in all its shops at its seven locations.
“All incoming trucks are wiped down to protect our technicians in order to maintain a healthy workforce,” said Scott Dixon, operations manager. “After maintenance or repairs are completed, the trucks are again wiped down before being released back to the customer. We want to make sure the drivers are healthy and able to keep the vital freight moving.” Dixon said truck volume initially increased nationwide by 18% in response to COVID-19.
Four Star Freightliner also extended its hours at many of its locations. “We feel we are a small cog in the vital wheel that is keeping our nation together by doing everything at our disposal to keep transportation flowing but being mindful and responsible to always keep our employees and customers safe and healthy,” said Jerry Kocan, dealer principal.
Bob Acker, general manager for Bruckner Truck Sales – Oklahoma City, said his dealership was delivering parts throughout the state at no charge and that the dealership group’s network increased the utilization of drop boxes to limit personal contact. The company also expanded its mobile fleet service coverage area for customers impacted by employee absences and offered labor discounts through the end of the month.
Montgomery, Ala.-based truck dealership Four Star Freightliner was following CDC recommendations for the cleaning of hard surfaces and installed sanitizer dispensers in all its shops.
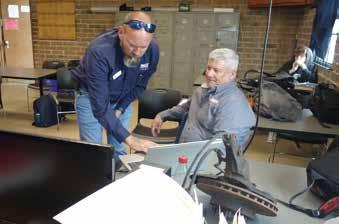
“We consider trucking and transportation vital to overcoming this historic event, and we are here to help truckers do what they do,” Acker said.
TTN Fleet Solutions, which operates a 24/7/365 technical contact center in Argyle, Texas, said that its breakdown coordinators remained busy assisting fleets during the pandemic’s onset. Jeff Pierre, president and chief executive officer, said TTN’s backup contact center services could operate 100% remotely if the need arose.
Several of TTN’s fleet partners that provide maintenance consulted with the company to replicate its best practices in redundancies and disaster recovery (DR) planning, Pierre said.
FOR TECHS, THE SHOP MUST GO ON
Truck drivers were scrambled like fighter jet pilots nationwide under loosened hours of service restrictions to get consumer goods back on store shelves, but as trucker appreciation campaigns spread across social media, life back at the shop tolled on.
“The freight must move on, so we are keeping our shops open,” said Brent Hilton, director of maintenance for Little Rock, Arkansas-based Maverick Transportation (CCJ Top 250, No. 75).
One thing that’s wasn’t quite as usual was the company’s concerted effort to keep technicians out of the truck as much as possible by having drivers perform their own minor and routine inspections.
“We are making an effort to keep our technicians out of our truck cabs and having the drivers perform all light checks and in-cab inspections, brakes … with the technician standing outside the vehicle,” Hilton said.

“We are simply trying to distance everyone from each other as much as possible.”
Glen McDonald, director of maintenance for Mem phis, Tennessee-based Ozark Motor Lines (No. 137), said company management monitored daily guidance from the Centers for Disease Control (CDC) and encour aged all employees to be vigilant in practicing good hygiene and social distancing.
“We are making every effort to supply all employees with necessary supplies and keeping them as informed as possible,” he said. “As far as shop operations, we still have to touch the trucks.”
Ozark incorporated new cleaning and sanitizing procedures for its equipment and asked technicians to stay in their bay and keep their work area clean.
“I’ve never walked into a shop and smelled bleach before,” added Nick Forte, vice president of
The National Security Council listed vehicle maintenance and mechanic workshops as “essential services,” and they were not subject to the sweeping coronavirus closures being mandated coast-to-coast.
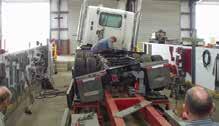
maintenance for Dubuque, Iowa-based Hirschbach Mo tor Lines (No. 65). “Normally, it smells like diesel fuel.”
The 1,900-truck fleet took steps to keep its technicians from being exposed to the virus. “By nature” of their work, Forte said, “technicians are generally socially distanced. One person is working on one truck. They don’t gather in groups.”
In challenging times.

While much of the planet has stopped in place, we’ve been working tirelessly to keep the critical machinery our world relies on moving. Our hundreds of formulations for thousands of applications are lubricating behind the scenes, making every on and off switch and turn of the key more reliable at a time we depend on them most.