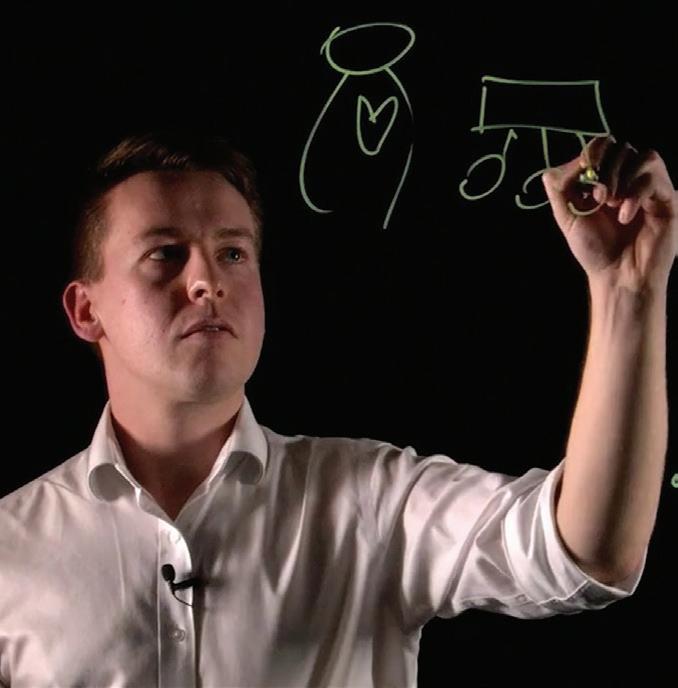
13 minute read
LITHIUM: THE SHORTAGES AHEAD
Recycling will be essential to the EV battery supply chain, but as OEMs use lower-value materials to cut costs, this could force recyclers to ship black mass overseas for processing — racking up more air miles for so-called green batteries.
Recycling not the solution as black mass value falls
Digging up more of the planet for raw materials is currently the only way to help satisfy soaring demand for electric vehicle batteries, according to recent analysis by Wood Mackenzie and the International Energy Agency. Wood Mackenzie research analyst Max Reid told the June AABC conference in Mainz, Germany that existing lithium supply chains would not be able to meet demand and that battery makers and OEM are going to be “hugely reliant on virgin materials” and will need to invest in new mines.
Reid said a ramping up of recycling could relieve some pressure from the supply deficit of battery raw materials, but with the recycling market still in its infancy in large parts of the world, recyclers too could start to come under pressure as ‘beyond lithium’ next-generation battery technologies are introduced.
“Recyclers need to be aware that they might need to be retrofitting equipment and processes in five or 10 years’ time, for example with silicon anode technology coming in,” Reid said.
“At the moment it is less clear what the economics are and recycling is not really viable in general, but in the future we can expect recycling to become part of the ecosystem.”
However, Reid raised the prospect of battery materials clocking up thousands of air miles by being shipped around the world for reprocessing before being returned for use in new batteries — further denting EVs’ environmental credentials.
“There is huge potential for recycling, but we see a tough situation for recyclers in terms of the proportion of metals contained in battery packs,” Reid said.”
“We are seeing what is a natural progression from high-value cathode material to the use of lower-value cathode materials, containing iron and manganese, which is a natural course for OEMs to follow to produce lower cost EVs for the mass market. There are also technologies like sodium ion opening up toward 2035, for the stationary storage market too.”
What’s in the black mass?
So while recyclers will face consistent levels of material arriving as feedstock, the value per kilogramme is decreasing. This in turn could lead to some recyclers simply shredding battery packs and shipping the black mass off for processing elsewhere, such as in Asia.
“It will be difficult to know what is in that black mass and we don’t want materials that already have so many air miles returned to markets for use in new batteries,” said Reid.
EV models could themselves be changed to accommodate new and more efficient battery designs, but new designs from OEMs are probably
We are seeing a natural progression from high-value cathode material to the use of lower-value cathode materials … a natural course for OEMs cutting costs
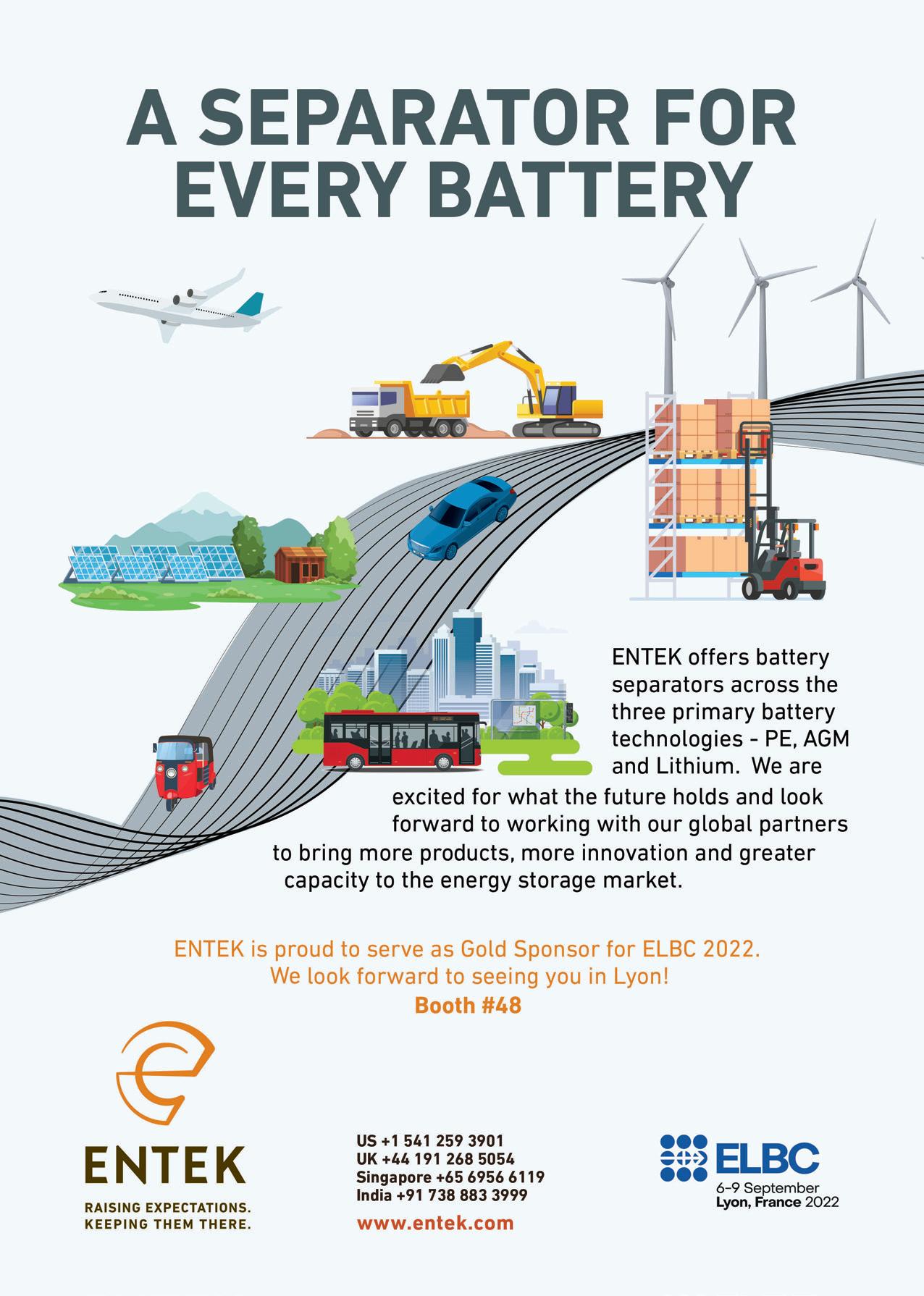
five to seven years down the line and “that’s kind of far too late” to dampen demand for raw materials, Reid said.
He said the electrification of the transportation sector had caused a boom in demand for lithium ion batteries, with global cumulative lithium ion battery capacity set to rise more than five-fold to 5,500GWh between 2021 and 2030.
The sheer rate of growth needed for raw materials for EVs and energy storage in the first half of the century was unprecedented, especially in the mining sector, Reid said.
According to the Wood Mackenzie analysis, demand for key battery raw materials currently stands at 97 kilotonnes (kt) for lithium, 186kt cobalt and 3,014kt nickel. By 2030, these are expected to grow to 318kt, 264kt and 4,273kt, respectively.
Little value in recycling
Supply from recycled materials, though paling in comparison, is expected to reach 130kt for lithium, 112kt cobalt and 377kt nickel, respectively, by the end of the decade, the analysis says.
“At present, the challenges of recycled battery raw materials seem insurmountable. Most of the discussion has been around the collection and recycling of end-of-life EVs, but the process is plagued with challenges,” Wood Mackenzie says.
The analysis includes a stark assessment of current recycling options: First, the cathode, which contains critical metals in the EV pack, “is overpackaged with pack materials such as casings, interconnects, cooling channels and others — and the result is a tedious recycling process with little value”.
Second, EV packs have long warranties and lifetimes, meaning the recovery of critical metals from them will be a long-term affair. In addition, the emergence of second-use applications, such as residential or industrial energy storage systems, will also keep end-of-life EVs from entering the recycling system.
As such, Wood Mackenzie says recycling production scrap will be the main source of recycled material this decade.
Meanwhile, China, Europe and North America will see huge increases in battery and cathode manufacturing to meet demand for batteries.
Globally, Wood Mackenzie expects battery manufacturing capacity to grow 3.5 times to more than 4,621GWh by 2030, “with China leading way ahead”, presenting “an increasing market for production scrap”.
Battery research lead at UK-headquartered consulting company Rho Motion, Ulderico Ulissi, told AABC that as battery designs evolve, their individual characteristics could impact recycling methods.
He urged a full, independent assessment to be conducted into the value of end-of-life EV batteries, saying existing data was insufficient.
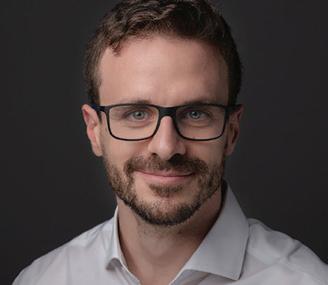
Ulderico Ulissi, Battery research lead, Rho Motion
‘CLIMATE PLEDGES’ REQUIRE 50 NEW MINES, SAYS IEA
Around 50 new mines will need to be built around the world to satisfy soaraway demand for EV battery materials expected within the next eight years, according to new analysis — Global supply chains of EV batteries — published by the International Energy Agency in July.
The Paris-based agency bases its calculation on the fact that the supply of some minerals, such as lithium, will need to rise by up to one-third by 2030 to satisfy pledges and announcements for EV batteries made by governments and accounted for in the IEA’s ‘advanced pledges scenario’ (APS) published last October.
According to the APS, which takes account of all climate commitments made by governments as of last October, demand for EV batteries will increase from around 340GWh at present to more than 3,500GWh by 2030.
Lithium, says the IEA, is the commodity with the largest projected demand-supply gap and demand is forecast to increase sixfold to 500kt by 2030 — “requiring the equivalent of 50 new average-sized mines”.
In addition to the dozens of mining projects needed to enter the market and reach capacity on schedule, the IEA says tens of new mineral processing and precursor plants will have to be commissioned.
“And to translate this into EV deployment, tens of cathode and anode plants, gigafactories and EV production plants are required.”
However, the supply of raw materials still threatens to be the Achilles’ heel of the EV dream, because the longest lead times in the battery supply chain process by far are for the extraction of raw materials.
According to the IEA, after an extractable resource is identified through exploration, it can take from four to more than 20 years for a mine to start commercial production. Four to 16 years can be required for the necessary feasibility studies, and engineering and construction work.
In addition, long lead times are often needed to secure financing and permits for which the latter can take up to a decade.
The IEA says there is some evidence that, over the years, the time required to bring mines online has increased and “this can be partially attributed to longer permitting and feasibility study lead times”.
Then once a mine is commercially operational, it often requires around 10 years before reaching nameplate production capacity.
Given “sufficient investment”, the IEA believes downstream stages of the EV battery supply chain can ramp up to meet even rapid increases in demand by 2030.
However, it warns upstream mineral extraction can cause major bottlenecks unless adequate investments are delivered well in advance.
As EV battery makers scramble to source new supplies of raw materials and step up research into cheaper chemistry options, the International Energy Agency warns price increases are inevitable.
Another 15% hike in battery pack prices ‘may be on way’
Despite the recent commodity price surge, the International Energy Agency (IEA) says lithium battery prices still declined in 2021, with annual battery price data from Bloomberg New Energy Finance recording a sales-weighted average price of $132/kWh, down 6% from 2020.
This was much less than the 13% decrease from 2019 to 2020, but the IEA says in its Global supply chains of EV batteries analysis, published in July, that several factors partially insulated the average battery price from the commodity price rises last year.
First, the rising prices incentivised chemistry substitutions, which made many automakers switch to lower cost cathode chemistries with less commodity price exposure, such as lithium ion phosphate, which saw a significant increase in adoption compared to nickelrich chemistries.
Second, commodity prices were relatively low for the first half of 2021, which helped the average price decline.
Third, the use of higher nickel chemistries such as NMC811 (where there are eight parts of nickel, one of manganese and one of cobalt) reduced the use of cobalt, which the IEA says is the most expensive metal constituent in batteries per kg (around 5% of NMC811 cell price based on the 2021 average price), also offsetting some costs, particularly in the first half of 2021.
The IEA believes that a “key reason is the impact of rising commodity prices has yet to fully materialize” — because while automakers increasingly use contracts in which material costs are linked with commodity prices for high volume battery orders, there is a time lag.
“Therefore, these automakers did not feel the result of the exceptional commodity price rises from the last three months of 2021 until the firstquarter of 2022.
The IEA estimates that if metal prices are to remain at levels experienced in the first three months of 2022 throughout the rest of the year, then battery pack prices might increase by up to 15% from the 2021 weighted average price, all else being equal.
Limited deployment
OEMs could mitigate the impact by substituting other more cost-effective chemistries, but such price increases would still pose major challenges for automakers, increasing battery costs, reducing manufacturer margins and raising costs for consumers.
Meanwhile, the IEA says the future of battery chemistries is not set in stone and that they will become more diversified by 2030 as manufacturers select chemistries to serve specific vehicle characteristics.
Premium vehicles can be expected to use the highest energy density batteries available, likely higher nickel content chemistries such as NCA95, NMCA (where aluminium is included) and NMC9.5.5, or potentially those with even higher energy density, such as lithium nickel oxide (LNO) or lithiummanganese-rich NMC (LMR-NMC). However, the IEA says again that this will only be possible if “research challenges can be solved and a commercially viable cycle life is achieved”.
For lower end, high volume and principally urban vehicles, LFP (lithium iron phosphate) is forecast to be the primary chemistry because cost will be the key consideration rather than driving range. The IEA says due to high commodity prices for nickel and cobalt
The critical advantage of Na ion over Li ion is that it relies on abundant and low-cost minerals. The cathode material for the CATL battery consists of low-cost elements sodium, iron, nitrogen and carbon.
SODIUM-ION TECHNOLOGY: THE WAY AHEAD
While researchers across the world are working to develop battery chemistries that do not use lithium, the IEA says the closest most viable option today is sodium-ion technology. China batteries giant CATL is among those developing the technology and plans to form a basic industrial supply chain by 2023.
The critical advantage of Na ion over Li ion is that it relies on abundant and low-cost minerals. The cathode material for the CATL sodium-ion battery is Prussian White, this is made of low-cost elements sodium, iron, nitrogen and carbon. Sodium-ion batteries cannot use graphite anodes, so instead uses hard carbon. In addition, less copper is required as sodium-ion batteries can use aluminium anode current collectors, unlike Li-ion.
The performance of sodiumion batteries is already looking impressive. CATL says the energy density of its own battery cell is up to 160Wh/kg, and the battery can charge in 15 minutes to 80% SOC at room temperature. Moreover, in a low-temperature environment of -20°C, the sodium-ion battery has a capacity retention rate of more than 90%, and its system integration efficiency can reach more than 80%.
But while Na ion has advanced beyond the research stage with a demonstration of commercially viable performance, there are no supply chains today for its cathode and anode materials, says the IEA.
“The main uncertainties around the deployment of Na ion is the scalability of the production processes for these materials and the time required to develop an industrial scale supply chain.
and the expiry of key patents, LFP is set for major growth in volume models in Europe and the US.
For mid-range vehicles, the IEA says manganese-rich chemistry (lithium nickel manganese oxide — LNMO) is a strong contender because it has a higher energy density than LFP, yet does not reach the levels of the highnickel chemistries. But while the larger proportion of manganese in LNMO reduces material costs and commodity exposure considerably, compared to high-nickel chemistries, LNMO is still under development.
For medium and heavy-duty vehicles, LFP will account for the vast majority of installations as cost and reliability will be more important for the early applications of electric trucks, according to the IEA.
LFP has the best cycle life of the leading chemistries which suits frequent, short trips and being recharged often. However, longer range electric trucks are likely to use nickel-based chemistries with the highest energy density, but their deployment before 2030 is limited.
“Electric car sales powered through 2021 and have remained strong so far in 2022, but ensuring future growth will demand greater efforts to diversify battery manufacturing and critical mineral supplies to reduce the risks of bottlenecks and price rises,” the agency says.
In the short term, the greatest obstacles to continued strong EV sales will be soaring prices for some critical minerals essential for battery manufacturing, as well as supply chain disruptions caused by Russia’s attack on Ukraine and by continued Covid-19 lockdowns in some parts of China.
And even if those challenges are addressed, the IEA points out that much more work needs to be done by countries to roll out enough charging infrastructure to both encourage and cope with EV sales growth.
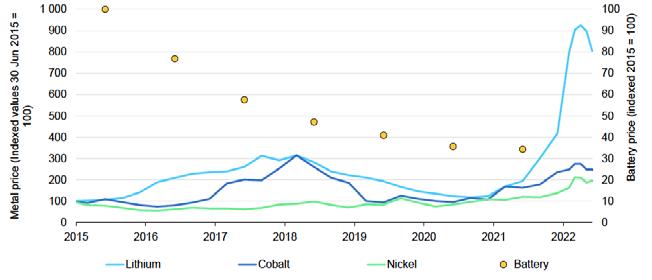
Battery metals prices, 2015-July 2022
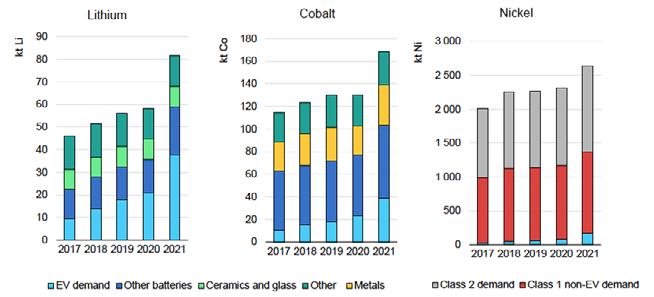
Battery metals demand, 2017-2021
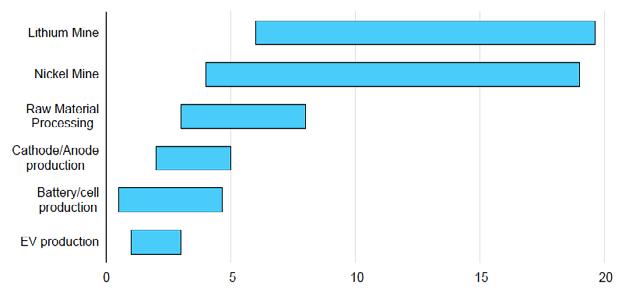
Range of typical lead times to initial production for selected steps in EV battery supply chain
Sources: IEA analysis based on S&P Global
NEXT STEP CHANGE: THE ALL-SOLID STATE-BATTERY
According to the IEA, all-solid-state batteries (ASSBs) are the “anticipated next step-change improvement in battery performance”, because they can enable the use of a lithium metal anode. This can result in battery energy densities around 70% higher than the current “best” Li ion batteries with graphite anodes, dramatically improving driving range capability, opening other applications and eventually driving down costs.
Nissan is starting pilot production in 2024 and aims to produce EVs with ASSBs in 2028, having just opened a prototype production facility in Japan, the IEA says. Other initiatives include a joint venture of QuantumScape and Volkswagen, which plans a pilot production line to start in 2024.
However, the IEA analysis cautions that “despite the activity and announcements, major technical challenges remain to be solved before ASSBs can make significant impacts”.
Current state-of-the-art performance often relies on impractical pressures to solve the contact problem, or on currently unscalable, expensive production processes to reach viable performance. But ASSBs are not expected to have a significant impact until after 2030, the IEA says.