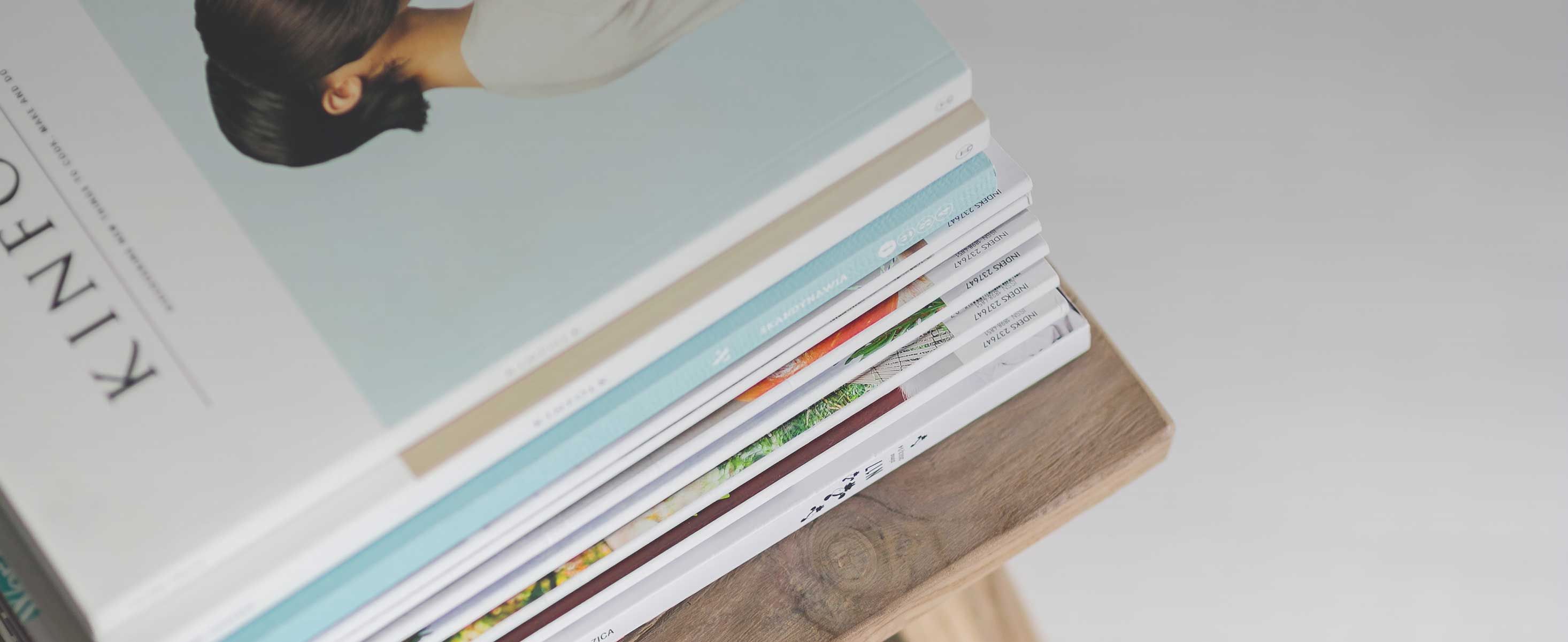
2 minute read
Battery equipment firm CMWTEC plans new factory
Battery finishing line equipment major CMWTEC Technologie will be expanding its manufacturing capacity at a new greenfield site in Germany as the company invests to meet an increasing order book, Batteries International has learned.
CMWTEC vice-president of sales, Michael Wipperfürth, confirmed the expansion plan during the firm’s latest customer open house event at its factory in Grossmannswiese in Germany on July 12.
Wipperfürth said the firm will be moving from its current factory site of up to 1,000m2 to a nearby greenfield site of 6,000m2 where construction is set to start soon. He hopes the move will be made next year. in advancing responsible recycling practices.
The new site is adjacent to the Limburg-Süd railway station, offering easy access for the firm’s customers to the country’s high-speed rail network and key destinations including Frankfurt International Airport.
New and existing customers were among those at the firm’s open days on July 12 and 13 to see and secure orders for CMWTEC’s extensive new range of machines.
Latest products include an end-of-line test machine for lead acid batteries and AGM/EFB finishing lines with proprietary data management software to record key data such as battery codes, test results, filling quantity and height control measurements.
Miksad said lead batteries continued to be key to the transition to clean energy storage in the US, with the recycling of raw materials instead of relying on newly mined minerals significantly reducing the manufacturing footprint for batteries.
“Lead batteries are critical to our low carbon future by being a critical component in many sustainable applications,” Miksad said.
“Our industry is minimizing the environmental impact of battery disposal with a highly successful circular
‘manufacture-use-reuse’ model. It has become the blueprint for newer battery chemistries, as well as other industries.”
The new study updates aggregated data for the five-year reporting period of 2017-2021. The lead battery recycling rate for that period was derived by dividing the total pounds of lead batteries recycled by the total pounds of lead available for recycling in the US.
To account for significant market disruptions during the pandemic, the study averaged BCI recycling rate studies spanning 2011-2021 to derive the sustained recycling rate of 99%.
Overall, the study confirms the exceptional achievements of the lead battery industry in perfecting recycling processes and a circular economy for lead batteries.
Details of the study and other recycling facts and figures are available on BCI’s website.
Gravita India said on July 10 that its Mundra Port lead battery recycling plant in Gujurat was back in operation after work at the site was suspended in June when a cyclone hit the region.
The company said the estimated cost of damage caused as a result of cyclone Biparjoy was about Rs2.50 crore ($300,000) although losses would be covered by insurance.
Gravita announced in April that it had increased lead recycling capacity at Mundra by 40,500 tonnes per annum, which took the overall recycling capacity at the flagship facility to 60,000 tpa.
Around 19,500 tpa of the new capacity came from switching some recycling from the firm’s facility at Gandhidham, about 60km northeast.
The company said it had also started commercial production of red lead and plastic granules at Mundra, with a capacity of 4,800 tpa and 7,500 tpa respectively.
Gravita announced the start of the first phase of battery recycling operations at Mundra in December 2021.