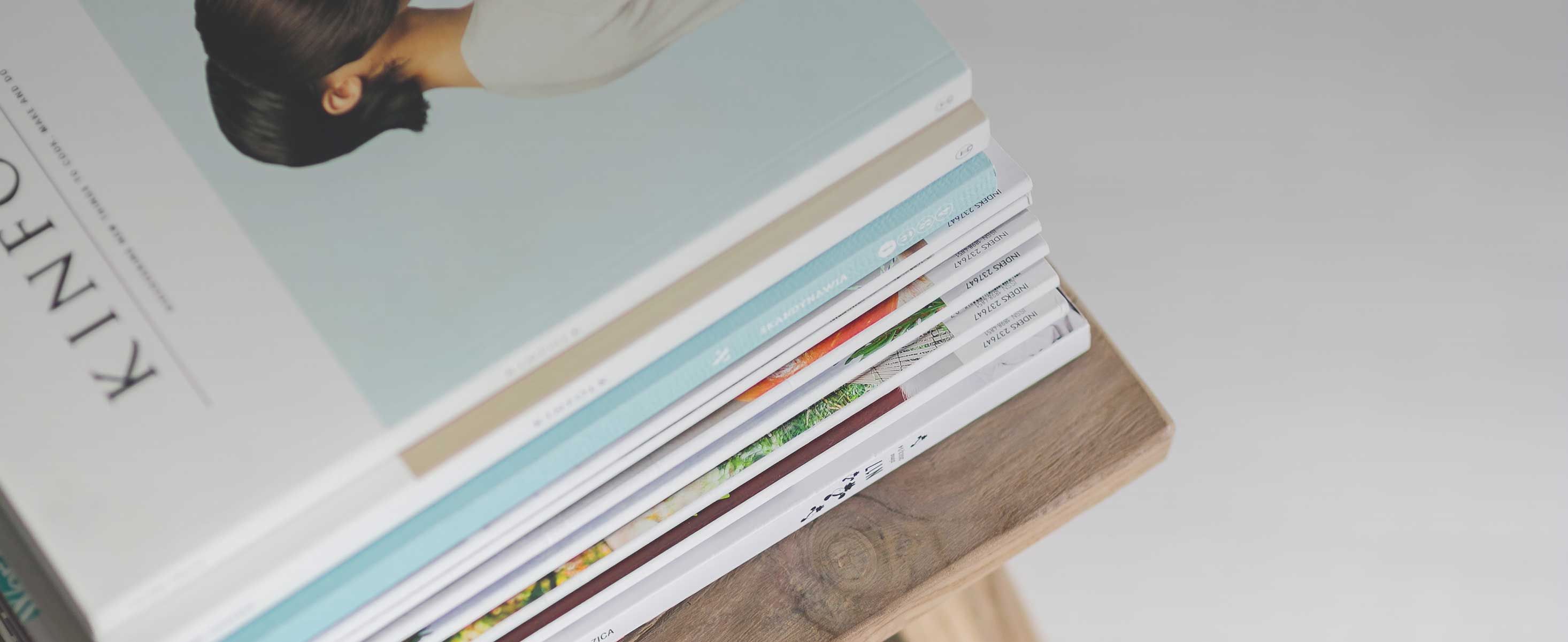
3 minute read
Global grid storage to feature prominently in 2023
Battery energy storage is to accelerate in 2023 due to market demand and government policies to enable renewables to provide baseload power. A good example is the Sacramento Municipal Utility District in Northern California where, through a partnership with ESS, the utility plans to deploy up to 200 MW/2GWh of storage alongside renewable energy sources to provide power to some 60,000 California homes.
In 2023 we will see microgrid deployment increase, long-predicted solar interconnects to become a reality, while the world starts looking at renewables as strategic reserves.
Utilities are increasingly focused on the resilience and reliability of solar and energy storage systems as much as cutting carbon emissions. With increased climate-driven natural disasters and increasing unreliability of grids reliant upon centralized generation in some parts of the world, microgrids will play an increasingly important role to deliver reliable, sustainable energy.
Adrian
Long distance HVDC transmission will forge new connections between regions with substantial renewable resources and areas of high demand. For example, the Xlinks project between Morocco and UK will provide 3.6GW of reliable energy for an average of 20+ hours a day by 2030, equivalent to 8% of the UK’s electricity needs.
Similarly, a 2027 project in Australia will see a combination of the world’s largest solar farm and battery system in the north of Australia connected to Singapore via 4,200 kilometres of HVDC submarine cables.
The interconnects from clean energy-rich regions to demand centres will provide new energy sources that will cut costs, improve energy security and cut carbon emissions.
The so-called “strategic reserve” will become an integral business strategy for IPPs, utilities and large C&I players seeking to deploy renewable energy projects.
Ongoing geopolitical issues, trade barriers and the pandemic have contributed to a disparity between
Dry electrode processing, a key trend for next generation manufacturing
Traditional electrode manufacturing relies on slurry mixing, slurry casting, solvent evaporation, and compressing. The wet coating process is costly, energy and timeintense and on the cathode side relies on hazardous organic solvents.
Even though this process is wellestablished and has a track record for safety and reliability, battery experts from all over the world are investigating various strategies to optimize electrode manufacturing.
In Bühler’s view, the most promising strategy is to completely skip the solvent in this process and implement a fully dry process, aka dry battery electrode (DBE): electrode raw materials (active material, conductive additives) are mixed with a polymeric binder.
The most widely used binder is PTFE for a very good reason: PTFE fibrillates under shear which in turn results in a network of micro- and nanoscale fibers — this network immobilizes the powder materials and generates a soft composite structure.
Bühler is a process solution provider to many different industries. Apart from a major footprint in the food industry, Bühler is an important partner for equipment and technologies in the automotive industry (aluminum die casting, vacuum deposition, wet grinding and mixing solutions).
For more than 10 years Bühler has actively shaped the LiB electrode manufacturing by introducing a fully continuous mixing process for
Alan Greenshields ESS
global energy demand and available supply. As the demand for renewable energy grows, the strains on global supply chains will become difficult to manage.
Renewable energy infrastructure producers are already sold out over the next few years with solar panel producers and inverters accepting new orders from 2026. Due to this, the competition for securing equipment for long-term supply agreements and manufacturing capacity is set to increase, as project developers look to mitigate resource scarcity.
The coming year will see “strategic reserves” established to ensure equipment access is possible to meet demand going forward.
electrode slurries. This process is based on twin-screw extruder technology. Opposed to traditional batch mixing processes, major advantages are the high productivity per line as well as consistent product quality.
Over the past years, the twin-screw extruder technology has proven to be the adequate tool for DBE. Raw materials are continuously dosed into the mixer, unit operations such as homogenization, dispersing and fibrillation of the polymer are combined in one machine.
The discharged composite material is of flaky and soft nature — it is subsequently calandered into an electrode film and laminated to the current collector.
As DBE is equally interesting for conventional LIB cells as well as future battery generations, such as all-solid-state batteries, DBE could very well be the next revolution in electrode manufacturing.
Adam