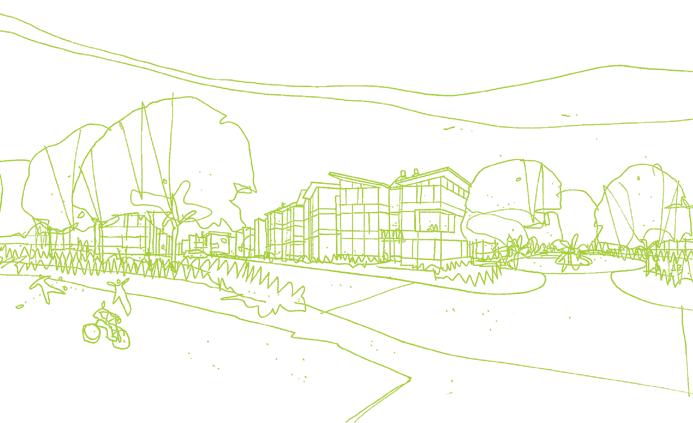
6 minute read
FOREWORD
Design for Manufacture,our challenge to the housebuilding industry to build high-quality,welldesigned and sustainable homes for a construction cost of £60,000,has shown everyone that the housebuilding industry in the United Kingdom is capable of delivering a world class response to the challenges of 21st Century living.
By using public-sector land and lower construction costs,English Partnerships has also been able to deliver higher than average levels of affordable homes within mixed communities on these sites.
Advertisement
The schemes that have come forward on the nine sites where preferred developers have been selected have set new standards of excellence.The competition also suggests further opportunities to cut costs and improve the design of housing,making it possible to build more affordable homes.
The competition has also led to a greater understanding amongst those involved about the value of teamworking and how different skills and knowledge can complement each other and enhance the end product. Housebuilders have worked closely with architects to maximise the design potential of sites and house type designs.Architects have been talking with the supply chain about the opportunities and constraints of working with different materials or build systems. The end results speak for themselves.
Everybody that has taken part can be immensely proud of what this competition has already achieved,but the prime objective of this document is to share what we have learnt.This document sets out not only the
10 main lessons from the competition,but also gives a wealth of detail about the individual schemes.
But the story doesn't end here.We will continue to follow and report on the progress of these schemes, and the views of the people who live in these homes when they are completed.And,later this year,we will be producing a manual that sets out in detail how other public-sector landowners can run their own competitions to deliver the next generation of affordable high-quality £60,000 homes.At the end of the document,we also outline how we will be taking the competition to the next step and work, together with industry,to tackle the wider climate change agenda and deliver affordable and more environmentally sustainable homes.
Creating sustainable communities can be a complex and difficult process.It is vital that we build on what has been learnt from the Design for Manufacture Competition and bring the lessons from this project through to mainstream housebuilding.Many housebuilders are already taking up our challenge to deliver affordable,quality homes in sustainable communities.We hope the results from this competition will be an inspiration to the rest to aim higher.
WHY ARE CONSTRUCTION COSTS OUTPACING LAND PRICES? WHY ARE THERE SO FEW NEW HOMES FOR SMALLER HOUSEHOLDS AND SMALLER MORTGAGES?
In September 2004 at the Labour Party Conference The Rt Hon John Prescott MP set out a challenge to build homes for £60,000 (£60k). Sceptics said it could not be done and cynics said that it was a gimmick. But the challenge was followed through within the Office of the Deputy Prime Minister, hereafter referred to in this document by its new name of the Department for Communities and Local Government (DCLG), and English Partnerships was asked to turn the vision into a reality. Within just over a year of the formal launch of the competition, nine sites have been allocated to the six final winning development consortia. At the time of writing this, four have even won planning consent and two are actually on site with development. The whole industry has responded with enthusiasm and innovation to the challenge. The legacy will be long lasting. This is the story of how it was achieved.
The UK is unique among EU states for relying on a small number of publicly-quoted housebuilders to supply most new housing. In 2004 the 10 largest companies built more than half of all supply for the first time, doubling their market share since 1990. When the 1980s’ housing boom ended in bust, these quoted housebuilders had to revalue their land holdings bought in expectation of ever-rising prices. This led to legendary losses in 1991 for some of the largest housebuilders, leaving shareholders smarting. So City analysts focused attention on who buys land at what price. They trusted housebuilders’ cost estimators to manage build prices.
In 2005 the development plot cost, among the quoted companies, averaged 19.2 per cent of the selling price; housebuilders had won back the City’s confidence about land deals. But conversely, there were new worries about the cost of build, the reliability of labour supply and its impact on build programmes. So serious is the challenge that leading companies have diverted substantial funds away from land to investing in modernising their build. In some cases this has led to the use of factories to manufacture a major portion of new homes off-site. These housebuilders have secured the potential to increase output, as demand for new homes rises.
As there is concern about cost, so too is there about supply. The Bank of England’s 2005 Housing Supply Review written by Economist Kate Barker showed that recent volumes had already risen by more than 15 per cent, but Barker was calling for much faster growth. She set out different targets for growth in supply, to stabilise house prices at different long-term trends. This anticipated several scenarios with volumes increasing by between 40 per cent and 100 per cent. Government responded on 12 December 2005 by committing to make sure additions to the UK’s housing stock rose by one third to 200,000 net units by 2016.
CAN IT BE DELIVERED WITHOUT CHANGE?
Skilled trades in market hot spots can pick and choose jobs on price. There are too few available, so site managers can’t fire those who don’t keep to agreed programmes. Build prices are also increasing at two and a half times the rate of the Retail Price Index. This all means that attempts to meet housing demand with increased volumes of supply could backfire in the short term by stretching the capacity of the industry without tackling build costs. The industry needs more new capacity.
The Challenge
The Design for Manufacture Competition aimed to support industry investment in building more, smaller units in a way that sidesteps traditional methods hampered by build cost inflation. It has promoted research and development in new products and processes. Ten sites were chosen for the competition based on their unique features, such as established Design Codes or other developments already underway. The brief specified that a minimum of 30 per cent of the homes in the winning proposal for each site should be: a two-bedroom home with of at least 76.5 sq m built to a build cost of £60k or less. The build cost of £60k included builders’ overheads, profits and design fees, but not abnormals such as bad ground or site infrastructure such as highways.
The competition has exceeded expectations for the level of industry involvement, the depth of press interest and the potential of the lessons learnt. When The Rt Hon John Prescott MP said he would challenge the industry to build for £60k, some pointed out that smaller less profitable houses were of little interest in any boardroom. But within months companies were unveiling homes that could be constructed more cheaply than the level sought by the competition and by the time the first winning schemes were seeking planning permission, three major housebuilders had announced sites where they were building their new lowbuild-cost, low-sales-price homes.
In 1905 there was a competition to provide low-cost housing for working class newcomers to the world’s first garden city at Letchworth. Many Letchworth homes were built using prefabricated methods and are listed buildings today. The Design for Manufacture Competition is a modern equivalent but with far greater significance for the future.
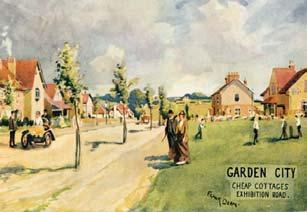
Key Objectives
■ To design and construct 1,000 high-quality homes cost efficiently.
■ At least 30 per cent of the new homes developed on the competition sites were to be provided at a construction cost of £60k or less.
■ Remaining homes on the competition sites to be produced using equivalent processes and cost efficiencies.
OTHER IMPORTANT OBJECTIVES:
■ To demonstrate efficiencies can be achieved by re-engineering the design, procurement and build process to mitigate and reduce the impact of construction costs.
■ To demonstrate that it is possible to build good quality, cost-effective homes without sacrificing sustainability standards and land values.
■ To act as a catalyst for change in direction in the construction industry in the way projects are designed, provided and delivered.
■ To reduce waste/defects and accidents.
■ To embed change into the supply chain to deliver ongoing continuous improvements.
■ Units to contribute to English Partnerships’ First-Time Buyers’ Initiative.
■ BREEAM EcoHomes Very Good award to be achieved as a minimum.
■ Approach is to be replicable on sites outside the competition.
■ To deliver through partnering arrangements.