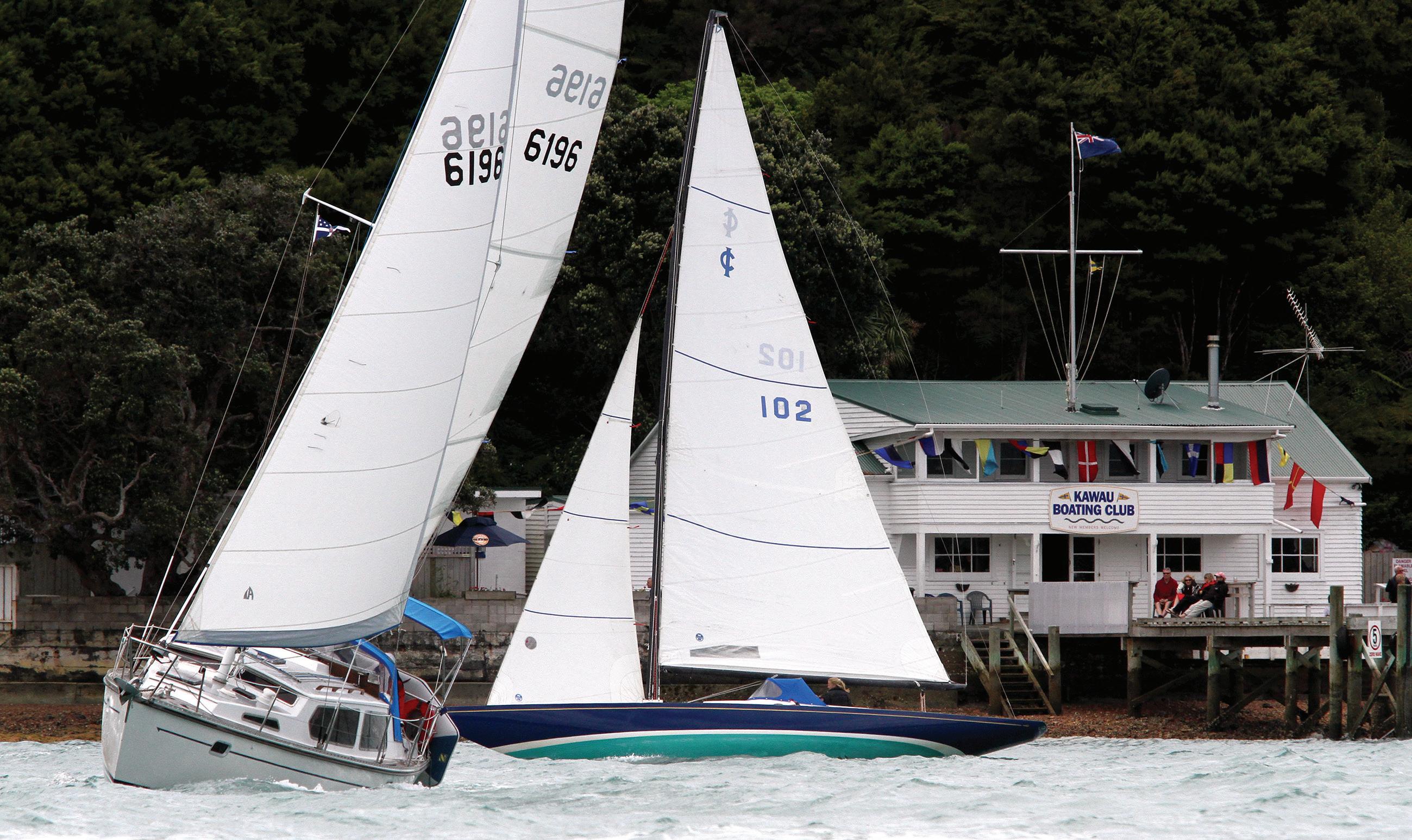
7 minute read
Stratis technology celebrates significant milestone
Kawau Boating Club launches Labour Weekend sailfest
For boaties disinclined to compete in the annual springtime ritual of the Coastal Classic, Kawau Boating Club has come up with an alternative way to celebrate the impending summer season.
The inaugural running of the Nautica Shipping and Logistics Kawau Sailing Weekend begins a race from Auckland to Kawau on Friday, October 22, starting from the Royal NZ Yacht Squadron at 1pm. This will be open to a racing and a cruising division and launches are also welcome.
On Saturday, there is an Up the River Raid, in which tenders and dinghys will follow the river from Sandspit to Matakana for a visit to the famous Saturday market. Back on the island, revellers will enjoy a jump-up ashore with a live band.
Sunday will feature a round-the-island race, folowed by a prize-giving in the evening.
The club has ambitions to build the event into a major fixture on the sailing calendar. “KBC is a magic facility and location – we hope to emulate the Hamilton Island Race Week and develop this regatta into the signature sailing event in NZ,” says Club Captain Jon Whisker.
Club Commodore, Mike Mahoney, says the event is not intended as competition for the Coastal Classic, but to complement it. “This is for boaties who have probably done the Coastal Classic a couple of times and want something a little less demanding and more family-oriented. Particularly for the smaller boats, the Coastal Classic is a long way to go just to turn around and come back again.
“Our focus is on a family fun weekend. We are looking to mimic the casual atmosphere of the Mahurangi Regatta with no protests and not much in the way of formalities.” Notice of Race and Entry Forms are available on the KBC website kawauboatingclub.nz.
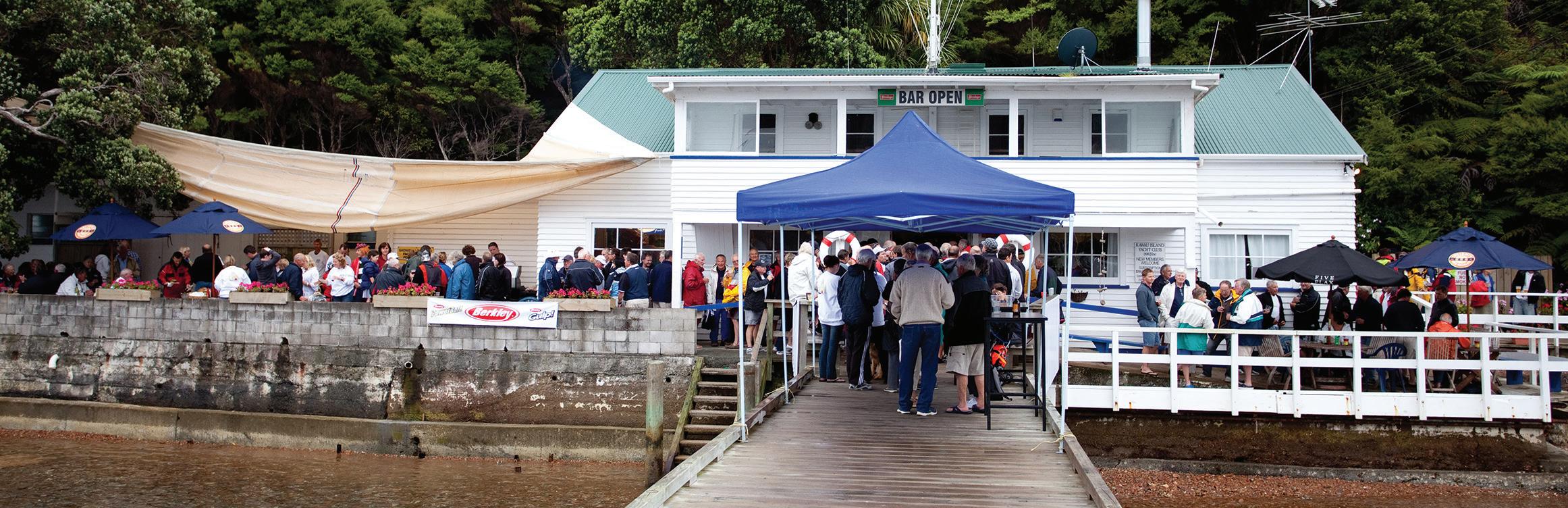
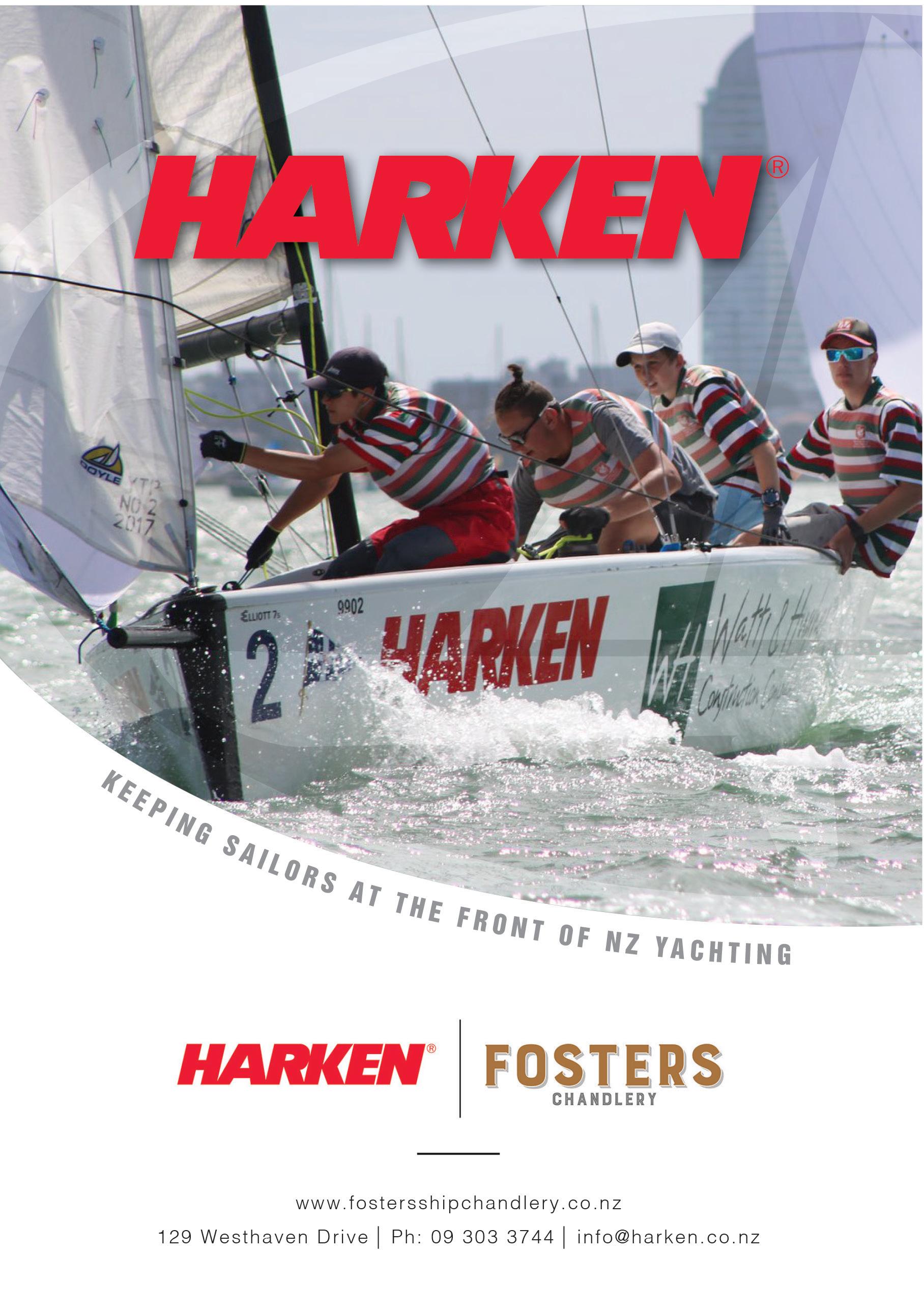
Stratis has come a long way since early experiments with a modified ballpoint pen. Inset: Richard Bouzaid.
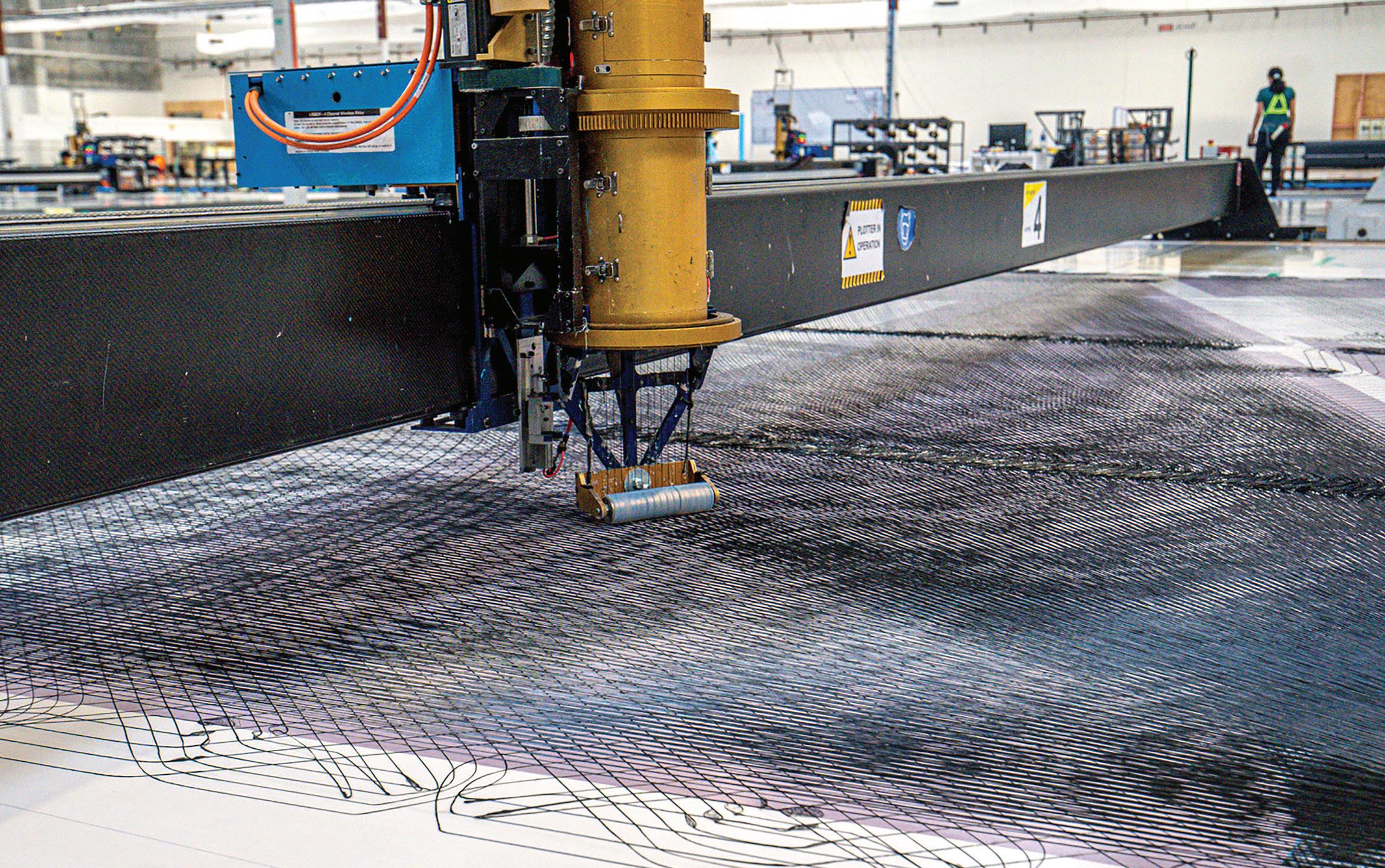
Stratis technology celebrates significant milestone
Twenty years ago, in an old-school Auckland sail loft, Richard Bouzaid began experimenting with a new way of building sails utilising an adapted ballpoint pen to direct single fibres onto a substrate in line with the predicted loads.
“We could only lay one Kevlar fibre at a time through an adapted ballpoint pen,” Bouzaid recalls. “It was a very typical Kiwi way of doing things.
“We were using a heatset glue on prepreg fibres with a plotter that was only 1.4m wide, so the sail panels had to be very narrow. We had this little laminator we ran the panels through.
“A young Spanish kid was working for us at the time. He ended up writing our original software to do the fibre layouts and generate files for the shapes.”
Although this was a decidedly small beginning, Bouzaid had big ambitions. New Zealand’s superyacht industry was fast gaining global recognition and the country had also just staged its successful defence of the America’s Cup, the first nation outside of the United States to achieve that.
At the start of a new millennium, with New Zealand riding a wave of success, Richard was eyeing the lucrative superyacht market. “Obviously, laying one fibre at a time wasn’t going to work for superyachts, so we had big strides to make.”
Those early crude experiments were the beginning of big strides towards what eventually became Doyle Sails’ Stratis system and structurally engineered sails.
Utilising multiple fibre types and membranes, Stratis tailors a precision product for specific applications, from weekend warriors and club racers, through grand prix round-the-buoys machines, to round the world campaigners and luxury superyachts.
At the time of those first small steps with Kevlar fibres, Bouzaid was in a Doyle franchise loft in partnership with Chris McMaster, who became a big driver in the development of the new system. In 2017, the ownership of the entire Doyle Sails International brand was acquired by a partnership of Mike Sanderson, Richard Bouzaid and David Duff.
All 50 Doyle lofts around the world rely on the New Zealand operation for their supply of Stratis, ensuring consistent quality in every product. Almost all the custom design is also done in New Zealand with approximately 70% of the Stratis output exported in kitset form for the other lofts to assemble and finish.
“Two things are incredibly important to our manufacturing process,” Bouzaid continues. “They are high pressure laminations and a predictable environment. Everything is humidity and temperature controlled. We also deploy significant heat sensing monitoring and instrumentation, so that when we laminate, we have an incredible degree of control over the product’s consistency.”
At Doyle Sails’ 11,000m2 purpose-built headquarters in Auckland, the Stratis operation takes place in a separate climate-controlled area, where the sail fabrics are built on three flat platforms, 46m, 50m and 65m long, all at 11m wide.
The construction process involves laying down a complex matrix
of fibres under a combination of vacuum, direct pressure and heat. Fibre combinations of carbon, Technora, Ice, or Polyester are applied in varying ratios depending on the application.
“Each sail is designed and engineered for the customer’s yacht and application, whether it is intended for cruising, club racing, or grand prix campaigning. Every time the Stratis machine runs a path of fibres, it’s entirely custom-made for that sail.”
Computer-controlled machines lay down the precise arrangement of fibre threads as they pass backwards and forwards across the panel. Laminating machines exert 12 tonnes of downward pressure and infrared heat on the surface, fibres and adhesives, which, together with extreme vacuum, ensure void-free lamination of the membrane.
It is highly automated and very efficient. On average the CAD fibrelaying machines travel 150,000 metres a week, laying down 1.3-million metres of fibre and consuming nearly 150kg of carbon and 190kg of para-aramids. The flat beds mean a whole range of different size sails, or sections of sails can be built simultaneously, maximizing the production capacity at all times.
It is a modern, high tech production system, although a fair dose of Kiwi number 8 wire ingenuity went into building it. Much of the machinery was modified from other industries — some from carpet manufacturing, some from laminating industries and some of the heating and sensing equipment came out of the food industry.
As part of its drive for quality control, Doyle Sails continues to devote resources and attention to research and development. “We are always investigating new technologies and looking at new products and refining what we do. That could be process-driven, design-driven, or related to mechanical componentry.”
In the past 10 years, with the weight-saving benefits already embedded in the process, attention has focused more on performance and how the sails work. “A great deal of what we do now is about how we can manipulate our membranes to do more. It is not just about sails retaining rigid shapes. Our structures are designed to be manipulated, hence the evolution of Structured Luff and Cableless sails.
“This ability to manipulate the shapes means you no longer need five codes of each sail locked into a narrow working range. Our inventories provide flexibility.”
Advances in sail technology also feed back into broader areas of performance and design. On their own, lighter, stronger sails reduce weight aloft, which improves performance, but Structured Luff and Cableless sails also reduce loads, placing less demand on rigs and supporting structures.
“We are able to take load away from the mast and stays and carry more load in the sails,” says Bouzaid. “There are big gains being made there.”
As to the future, Bouzaid says tools developed in-house and the ongoing research into how all aspects of rig and sail systems interface are revealing things operators and designers could never see before and will lead to significant improvements in aerodynamics and all areas of performance.
“Increasingly, sails are going to be a lot more intelligent and provide a great deal of information through monitoring systems, fibre optics and data-streaming, much of which is coming from grand prix race programmes.
“Sails will probably look quite similar, but they will be doing much more than they are doing now.” Just as the technology has made astonishing strides in the past 20 years, Bouzaid predicts there will be no let-up in the pace going forward. “You will be staggered by the progress,” he says.