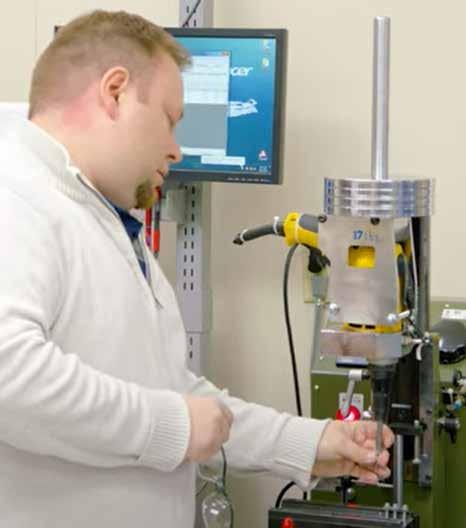
2 minute read
Selecting the Right Fastener to Resist Corrosion
Since a completely corrosion free fastener does not exist, select a fastener that is as durable as the members it is fastening.
Corrosion can be placed into two categories, general corrosion and galvanic corrosion. General corrosion is caused by air and moisture. We know that it is accelerated by salt and harsh chemicals. The second category is galvanic corrosion. There is a little more chemistry involved with galvanic corrosion and it can be a little confusing. Putting two incompatible metals together, even if they are both corrosion resistant on their own, can lead to galvanic corrosion.
First, work on mitigating general corrosion. Think about where the fastener will live. The environment in which a fastener is exposed affects the rate of corrosion immensely. Corrosion is accelerated in coastal regions or highly industrial areas. The vast majority of fasteners are steel and have a protective finish applied. Different finishes have different levels of corrosion protection and we cannot accurately predict when corrosion will develop. What we can do is compare different finishes and materials using the common ASTM B117 salt spray test. Test pieces are placed in a salt spray chamber and observed to see when the first sign of red rust or corrosion is visible.
Unprotected steel is quick to rust under normal environmental conditions. Metals like zinc, aluminum and stainless steel can protect themselves from general corrosion. For a dry, indoor application, a black oxide or phosphate finish might be enough to protect a steel fastener but if you need a little more protection, a zinc plated finish will help. The longevity of a zinc plated fastener depends a lot on the thickness of the zinc plating and how it was applied. We might expect a zinc plated fastener to reach anywhere from 15-120 hours to red rust in the salt spray test.
If a fastener is going to be exposed to the elements, it will need more than zinc plating. Hot dip galvanized (HDG) finishes have been a workhorse for corrosion protection throughout the years but it is not ideal in all situations. You won’t be able to find a self-drilling or self-tapping fastener in HDG and it is not recommended in coastal applications. There are other options for long-life fasteners. A number of companies offer proprietary organic coatings and finishes that do well in normal environments and reach 500-1000 hours in salt spray testing. Harsher environments like industrial and coastal areas require fasteners that can go beyond a 1000-hour threshold. You can also choose a fastener with a zinc or stainless steel cap. The exposed caps are highly corrosion resistant. For the harshest environments, 304 or 316 stainless steel offer the highest corrosion resistance.
Now, let’s discuss galvanic corrosion. Galvanic corrosion occurs when two dissimilar metals are immersed in a conductive solution and are electrically connected. That means that if you have two different types of metals, they have direct contact and there is a salty liquid present, galvanic corrosion may occur. If you can eliminate any one of those three components, you prevent the galvanic reaction.
To help in your selection, fastener suppliers publish compatibility guides for fasteners and various metal panels. Ask your favorite fastener supplier for their guide. These guides are a great way to help you select the best fastener material for corrosion protection for your application and to put your mind at ease.