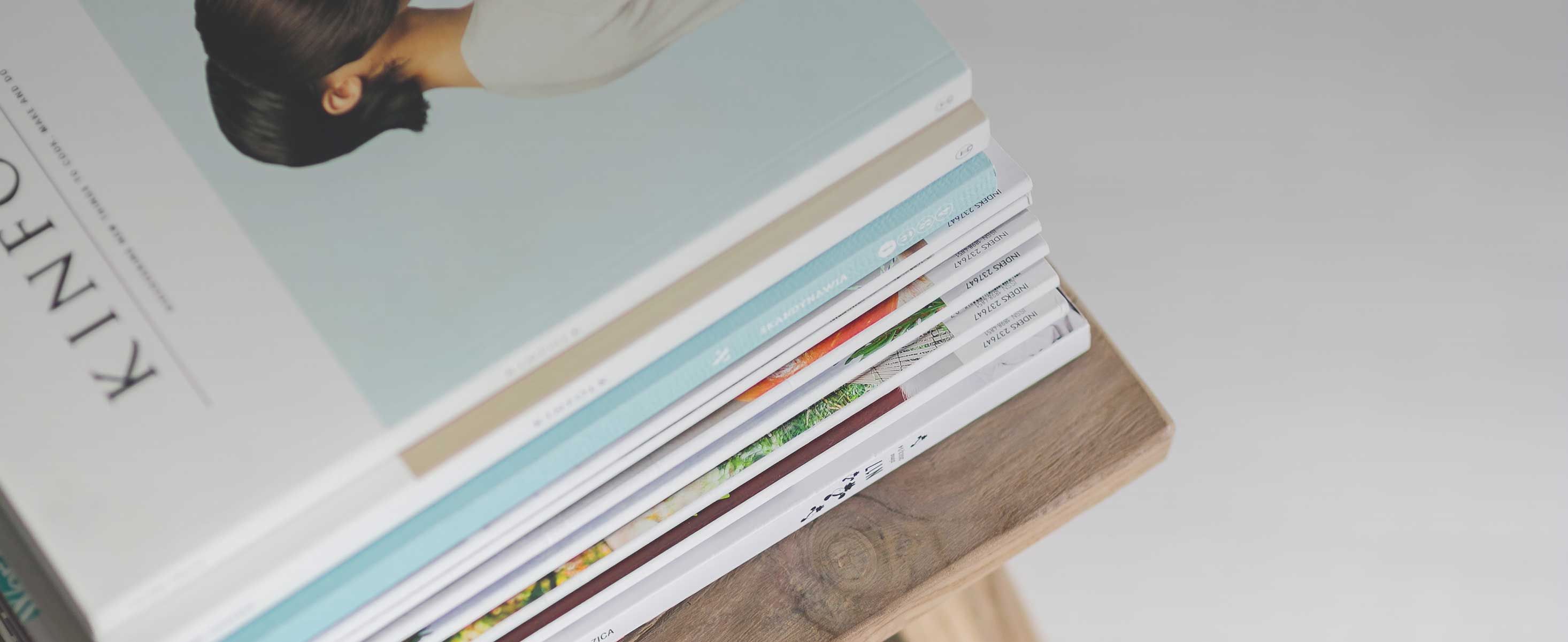
5 minute read
Looking WE’VE GOT YOU COVERED!
ProVia’s Metal Roofing System is thirdparty tested and approved in Florida, meeting TAS 100, 110, and 125 requirements. Our stamped panel metal roofing system is certified for High Velocity Hurricane Zones in Miami-Dade and Broward counties and for Non-HVHZ regions in the entire state, withstanding wind speeds up to 180 mph.
ProVia’s metal roof panels are constructed with 26-gauge steel—up to 30% more galvanized steel than competitive stamped metal roofing products. Our 4-Point Locking System includes a top lock, under and over locks on the sides, and our exclusive WaveLock™ ribbed feature on the bottom that increases the rigidity and strength of the panel.
surface for two materials with the same reflectivity. The relationship between emissivity and roof temperature is complicated by factors such as conductivity of the roof surface and wind speed that will allow some lower emissivity surfaces to shed heat energy more efficiently.
What type of coating is more energy efficient: black, aluminum or white? The answer depends upon climate and the percentage of energy used heating and cooling a structure. In hot climates white is most efficient; in temperate climates, aluminum coatings with high reflectivity and lower emissivity yield the best result; in extreme northern regions, dark-colored roofs will save the most energy as air-conditioning is uncommon.
What’s the difference between asphalt and coal tar? Asphalt is derived from crude petroleum. It’s an aliphatic or straight-chain hydrocarbon resin. Coal tar is derived from the destructive distillation of coal. It is an aromatic ring shaped hydrocarbon resin. The two are different and generally incompatible. Asphalt is normally lower in cost, can be used on pitched roofs to vertical, has fair resistance to UV degradation and can be left bare or surfaced in a variety of manner, but it has poor resistance to ponding water. Coal tar can only be used on near to dead level roofs and has poor resistance to UV degradation so it must always be surfaced with a layer of gravel, pavers or vegetation. Coal tar has good resistance to ponding water and exhibits cold flow or self-healing characteristics.
How do I tell the difference? There are a number of factors that indicate the type of built-up roof. The first is that coal tar is always surfaced with gravel, pavers or vegetation. If it’s bare, coated or surfaced with sprayed-in granules, it’s asphalt. If it is a gravel roof, the simplest method to determine the type of roof is to wipe the roof with a clean rag soaked in mineral spirits paint thinner. Mineral spirits is an aliphatic solvent and is only capable of dissolving asphalt, which is aliphatic as well. Asphalt roofs will leave a black or dark brown residue on the cloth while coal tar will leave a yellow or slightly green residue. Several passes with a clean cloth may be necessary if the roof is dirty.
How should I evaluate the relative quality of different aluminum roof coatings? Unfortunately, there is no clear standard beyond the minimum requirements of ASTM D-2824. The reputation of the manufacturer is paramount. The simplest method to sort out aluminum coating is by aluminum pigment content. Some people object to this standard by claiming that a coating with 2 lbs of ground up aluminum cans would rate the same as a coating with 2 lbs of high-quality leafing aluminum paste. For this reason, we recommend that users ensure that, when aluminum coatings are graded by pigment weight, the aluminum paste is quoted as meeting ASTM D-962 type 2 Specification for Aluminum Powder and Paste Pigments for Paints. Another excellent source of information is the EPA’s Energy Star Program, which lists reflectivity values of various roofing materials.

5,000 Industry Professionals 100,000 Industry-focused Digital Impressions monthly
When should aluminum roof coating be applied to a new asphalt or modified bitumen roof? As soon as possible or after the roof has cured? The best time to apply aluminum roof coating to a new built-up roof is after the roof has fully cured. This will take at least six weeks. Application of aluminum roof coating to uncured asphalt will likely result in sulfur and oil bleedthrough and sometimes severe cracking or splitting.
SBS modified bitumen should be coated as soon as practical. APP modified bitumen is the most challenging roof to coat with aluminum roof coating. Applying the coating immediately will reduce exudation or bleed-through, but it will not be eliminated: expect temporary discoloration. Waiting until the membrane has cured will allow most of the exudate to bleed out. If the roof has positive drainage, the exudate will wash off the roof and the modified bitumen will present a clean and stable substrate. Roofs with ponding water may retain exuded oil and sulfur compounds in low areas. This retained contamination will interfere with adhesion, discolor the coating and can cause the coating to crack. This contamination should be removed with a suitable power washer and detergent. It is the prerogative of the roofing contractor to examine the conditions present on a particular roof and choose the appropriate action.
Are all rubberized roof cements elastomeric? Not necessarily. Rubberized means that rubber has been added to the mix. Elastomeric implies that the material has the rubberlike properties of elongation and recovery. Some rubbers such as butyl, neoprene and SBR will not impart elastomeric qualities on an asphalt mixture. Rubbers such as SBS and SEBS will, but only if added in sufficient quantities to an asphalt that is suitable and not overly corrupted with economizing fillers.
What is the difference between water-proofing and damproofing? Damproofing will resist penetration of moisture through a foundation into the interior under normal conditions. Waterproofing will do the same even in the presence of hydrostatic pressure.

What are the advantages and disadvantages of applying coatings by brush, roller and spray? Brush application allows the coating to be worked into the surface. This will ensure an adequate bond, particularly if the surface is less than ideally clean and smooth. Brush application is the most time consuming method and will often result in visible brush marks.
Rollers are faster than brushes and still allow a measure of mechanical assistance in adhesion to the surface. Rollers also eliminate brush marks but may still leave a textured surface. Applicators should be aware that rollers will lower the natural rate of coverage below the recommended rate.
Spray application is the fastest method of coating application and generally leaves the smoothest surface. Total lack of mechanical assistance in adhesion, difficulty in assessing coverage rates and the danger of over-spray limit the suitability of spray applications.
What is the difference between silanes, siloxanes and silicone? All three are silicon-based molecules with masonry waterproofing applications. Silanes are monomers, the smallest and most simple of the three molecules. Silanes are best suited for dense surfaces like concrete and cultured stone. High concentrations of about 40 percent are necessary because of silane’s volatility.
Siloxanes oligomers are larger and more complex molecules than silanes. At lower concentrations, they provide excellent moisture protection to more porous surfaces like split face concrete block. Siloxanes can be blended with silanes to produce a treatment with the advantages of both materials.
Silicone polymers are large functional molecules that are used in caulks and sealants. Silicones can be useful for protecting porous natural stone that has a neutral pH. For concrete and masonry applications, silanes and siloxanes penetrate farther and preserve the surface’s original appearance.
Coatings are considered restoration and not a new roof system installation. Therefore, they can usually be expensed in the fiscal year during which they are applied instead of amortizing the cost over the life of the roof (as in a new membrane installation). This can be a huge tax benefit to some building owners.
FRM
R.M. Lucas manufactures coatings for roofs, walls, pavement and below grade applications. For over 100 years they have produced everything from asphalt materials to the most advanced modern moisturecure and reactive formulas.
RCMA is a leading industry voice, promoting the benefits of roof coatings and providing its membership with up-to-date information on building codes and standards, technical developments and other industry topics of interest.