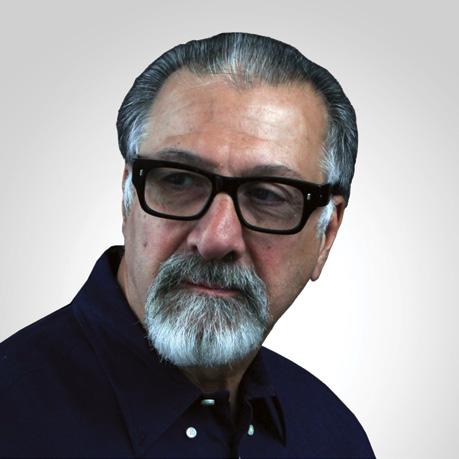
3 minute read
Design Comment
DESIGN
COMMENT
Michael Paloian, Integrated Design Systems, Inc.
Conversion: Factors to Consider
Rotational molding has historically been applied to molding tanks and containers because of its inherent ability to mold hollow water-tight shapes. Tanks and containers still represent the majority market share for this versatile plastic molding process. However innovative molders and designers have realized the benefits of this process. They have creatively applied it to hundreds of other applications, expanding its popularity as a highly desirable molding process. Today, the rotational molding process has been specified for molding products ranging from playground slides and farm equipment to medical devices. Some of these applications were initially specified for this process while others have been converted from another manufacturing process to rotational molding. What are the most important parameters one must consider when deciding if rotational molding can effectively replace another material and manufacturing process?
Cost – The unit cost has always motivated OEMs to consider switching from one manufacturing process to another. Production cost is typically based on materials and labor. However, there are other cost-related considerations to also consider such as investment, shipping costs, and part count. The rotational molding process requires an upfront investment in molds. This initial cost is typically amortized over time such as one year or several parts. Therefore, tooling investment should be included in any cost comparison. The rotational molding process is ideally suited to molding lightweight, large hollow parts. Parts such as these are typically costly to transport since their bulk density is so low. Designers should therefore consider packing density as an important factor when designing parts. Packing density can be increased by nesting or designing parts to be shipped as knock-down. On-site assembly should be weighed against parts consolidation and part count.
Investment – Designers should estimate tooling costs during the very early stages of any conversion project. Tooling costs can be estimated quickly by CAD modeling a basic overall size and shape of the product which can be distributed to a few mold makers for ballpark pricing. Molders need to understand features that could complicate the mold such as undercuts, tolerances, and intricate features.
Performance – Product performance is another important reason OEMs convert from one process and material to another. Improving performance can be attained by changing materials or design. Material-related properties might include improved corrosion resistance, impact strength, or molded-in color. Design improvements might include consolidating parts, reducing weight, or extending product life.
Productivity – Molders and designers must consider productivity another important parameter when converting from one process to rotational molding. Processes such as injection molding are highly efficient versus sheet metal fabrication which may require a high labor content for complex parts. Although rotational molding has effectively competed with both of these processes, complex sheet metal parts are easier to convert versus injection molding. Processes with high labor content are easier to convert. These include hand-laid fiberglass, sheet metal, casting, fabricated weldments, wood, and thermoforming.
Quality – Rotational molding part quality varies depending on the molder, tooling, equipment, and process control. Part quality and consistency are critical factors to consider during a conversion assessment. Designers should emphasize details such as parting lines, tolerances, and surface finish in any comparison assessment. Rotational molding may be the ideal process or may not be suitable, depending on the application.
Aesthetics and Appearance – The last and very significant consideration is appearance. Many products have been converted to rotational molding because of aesthetics. Rotational molding allows designers to cost-effectively replicate almost any shape they can imagine. This single benefit has popularized this process into unending markets ranging from recreational products to high-end furniture. The horizons have proven to be endless.
I hope this brief editorial has enlightened and inspired you to pursue new markets for this process. The future looks bright for rotational molding as long as designers and molders use their imagination. I welcome your comments. Please feel free to contact me at paloian@idsys.com.
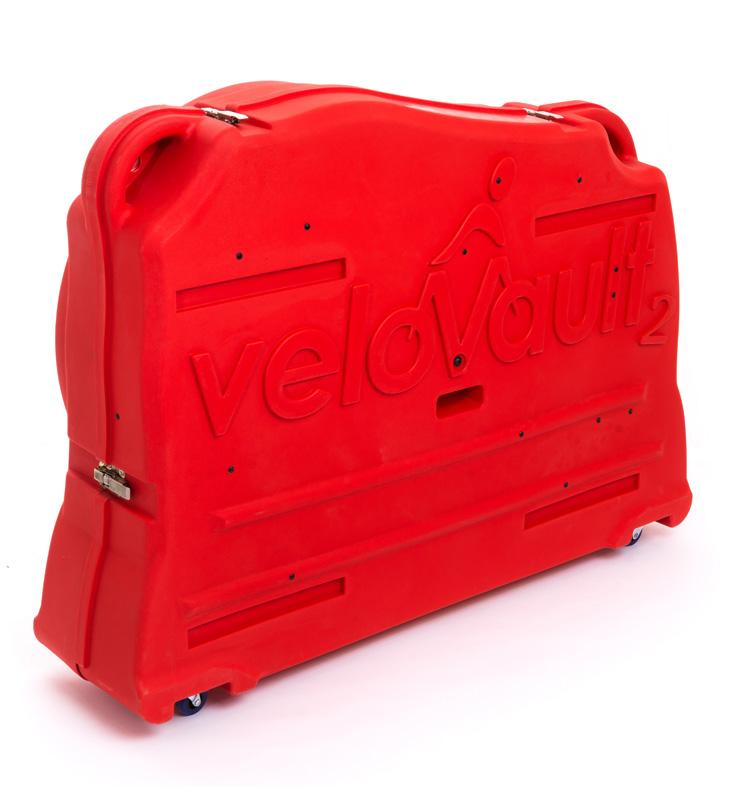