
6 minute read
Future technologies driving the mining industry
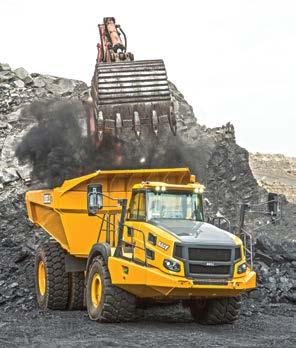
Future technologies
driving the SA mining industry
The future of sustainable and profitable mining in South Africa requires mines to embrace and adapt to ever improving and modernised mining methods.
The Fourth Industrial Revolution presents a unique opportunity for manufacturers of mining systems and equipment to collaborate with their clients on developing solutions to increase efficiencies, safety, profitability and the life of mines (LoM).
MEMSA is a member-based cluster, with a vision to position local mining equipment manufacturers as cost competitive and innovative – the preferred suppliers to local, regional and global markets. While this vision seems ambitious, the reality is that SA’s long, rich mining history has provided fertile ground for the development of an innovative mining equipment industry, with a great depth of expertise. It consists of agile manufacturers, specialised in meeting the needs of the local mining industry, as well as regional and global customers.
Supporting innovation
In this context, collaboration is key, and MEMSA is working with a wide range of partners to support innovation and technology development, including the Mandela Mining Precinct, Council for Scientific and Industrial Research (CSIR), Minerals Council of South Africa, universities, and higher education institutes and research communities.
The Precinct, a landmark collaboration between the private sector, represented by the Minerals Council of SA, and government, via the Department of Science and Innovation, aims to develop and facilitate technologies required to ensure the sustainability of the South African deeplevel, hard-rock mining industry, which faces serious safety and productivity challenges as shafts move deeper underground, and lower grades of ore are mined.
Since its inception, MEMSA has played a key role in facilitating member involvement in SAMERDI research programmes driven by the precinct. The South African Mining, Minerals, Extraction Research Development & Innovation initiative currently comprises of five research programmes: Life of Current Mine (LOCM), Mechanised Mining Systems (MMS), Advanced Orebody Knowledge (AOK), Successful Application of Technologies Centred Around People (SATCAP), Real-Time Information Management Systems (RTIMS) and the Test Mine.
“The need to enhance mine safety and increase productivity, together with revolutions in the use of data and energy technologies, are creating pressure for rapid and innovative technology development,” explains MEMSA CEO, Lehlohonolo Molloyi.
The precinct’s Test Mine programme is set to improve access to real mine testing environments. MEMSA contributed funds to the feasibility study for the establishment of an underground Test Mine facility at Royal Bafokeng Platinum’s Maseve Mine, and the CEO continues as representative on the Test Mine Steering Committee. Members are expected to commence use of the facility in 2023.
Once technologies have been perfected and proven, they must be brought to the attention of the market – and this is the key objective of another project on which MEMSA is working with the precinct. Mining TARA is an equipment database undergoing its second phase of development; the online platform will provide access to the capabilities and offerings of local OEMs while providing researchers with detailed information on available technologies.
The CSIR is an integral partner in the precinct, and MEMSA has introduced members to relevant research programmes. The CSIR Hydrogen Trackless Mobile Machines (TMM) programme focuses on hydrogen development and usage through electric vehicle (EV) enablement by converting existing TMMs and assisting the development of new TMM designs.
Local OEMs have been identified as key partners for the programme. Further focus areas for collaboration include the CSIR’s Factory Digital Twin, Learning Factory, 3-D printing and laser refurbishment facilities.
These novel technologies require new skills in engineers and artisans alike. MEMSA has recently completed a merSETA-funded research programme into 4IR-related skills needs in the industry. The study revealed SA manufacturers are selectively adopting new technologies, including IoT, 3D printing, Computerised Machine Maintenance Systems (CMMS), robotics and automation. Products manufactured increasingly include or link into data collection and transmission eco-systems.
While universities are responding rapidly to the need for new skills, it is more difficult for the under-resourced TVET system to adapt. New skills are best acquired in modular form through short courses – which digitally can be made widely available. The study recommended continued assessment and collaboration on sourcing courses for development at both artisan and engineer-level.
Safety remains a powerful driver for technology development, and MEMSA members participate in the Minerals Council-led TMM Regulatory Alignment Project in preparation for the implementation of ‘Level 9’ safety regulations – requiring trackless mining machinery to automatically slow or stop to prevent collisions.
The need for integrated sensor, transmission,
and mechanical technologies from OEMs and OTMs, ensuring a system that is safe and efficient, is demanding new levels of collaboration among mines, manufacturers and research partners. The process has involved learnings by all involved, which may underpin new technology partnerships.
Through the SATCAP programme, members have actively participated in training-exposure sessions on VR and AR skills development solutions; their application to modern drill rig operator and miner training for safer mining, VR and AR training methodologies to support a modern workforce at the University of Johannesburg’s Mock Mine and the Sibanye-Stillwater Digital Mining Laboratory (DigiMine) at the University of Witwatersrand and Virtual Reality Centre and at the University of Pretoria (UP).
Supporting innovation
In 2022 MEMSA held its inaugural Innovation Awards to celebrate local excellence in technological development and manufacturing capability supported by SAMERDI. “A lot of decision-makers in procurement tend to consider international mining equipment as superior, when in reality our local OEMs are on par with major international players. The recent acquisition of some of SA’s leading mining equipment OEMs by major international players further confirms this,” comments Molloyi.
“Global manufacturers have access to significant funding from their parent companies and have government support. This majorly impacts the investment these companies can pump into R&D. From that perspective, a local OEM might build a prototype, only to find its innovation stymied by technological advances imported from better funded and resourced global companies,” adds Molloyi.
Nevertheless, local manufacturers continue to leverage expertise and innovation to meet local challenges, to offer solutions for local and global markets.
“MEMSA thus welcomes the extension of, and refinements to, the 11D tax incentive for R&D which focuses on the development of novel knowledge and technological solutions. The nature of the industry requires more funding for prototyping and the commercialisation phase of product development,” Molloyi says.
Awards category winners
• Hard Rock Mining Equipment (the Navin
Singh Award) Hydro Power Equipment (HPE) for the development of the Isidingo Drill and
Drill Guide • Soft Rock Mining Equipment Rham
Equipment for the development of battery electric driven LHD, dump truck and land cruiser • Mining Infrastructure and Mineral Processing
AZMET Technology & Projects for the AZMET
Cyanide Removal Process (AZ-CRP®) • Safer and Healthier Mining Mine Support
Products for the Rocnet Modular Safety Net • Improved Productivity Hydropower Systems for the HV212 EOD Hydrovessel • Emerging Small Enterprise Gravitas Minerals for the Optima Classifier™
Exciting innovations are happening across the cluster’s membership including the development of: • battery electric mining vehicles by members including Rham Equipment, Fermel (personnel carrier) and Battery Electric (diesel locomotive conversion) • innovations in explosive casings (NXCO) • the development of trackless mining machinery suitable for mechanised mining, with sophisticated safety mechanisms; innovative hydro powered equipment • data sensing devices and systems for better safety and productivity
GREAT COMFORT. BETTER SAFETY.
