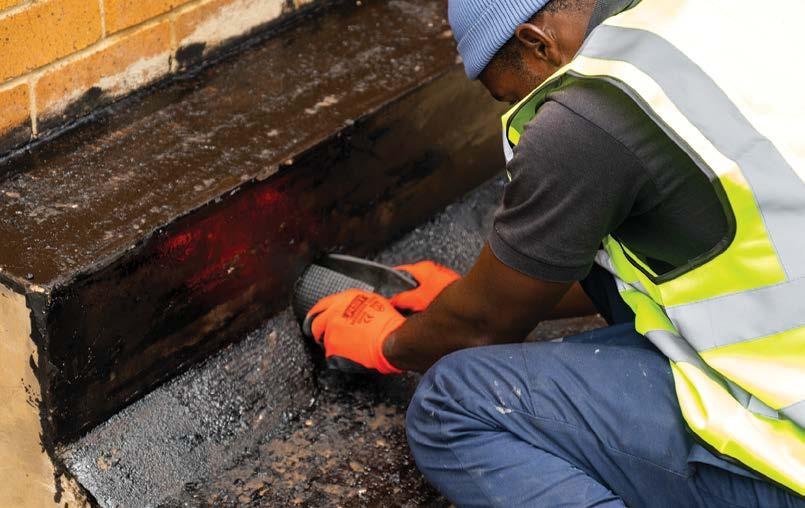
4 minute read
Beware: Substandard torch-on waterproofing
With autumn around the corner, some regions will be expecting rain while others will still be recovering from the downpours of summer. That is why waterproofing around the house, apartment or commercial building is so important. Hence, some very important words of advice received from the Professional Roof Repair and Waterproofing Association (PRAWA).
PRAWA
According to PRAWA, as long as it's undertaken correctly by a competent “roofer”, torch-on membrane waterproofing systems can provide many benefits. These include high tensile and tear strength, as well as fatigue resistance. They are also robust and impervious to vapour pressure.
Considering the high UV-reflective properties of the system, environmentally conscious consumers are also increasingly requesting this waterproofing solution because it helps to lower the energy footprint of a building.
Lack of skills and experience in the correct application
However, there is a very high failure rate of these systems in the country. The association has been overwhelmed with complaints from property owners, financial institutions and insurance companies regarding the quality of torch-on membrane waterproofing systems. This can be attributed to a lack of skills and experience in the correct application of these systems and, in other instances, the use of inferior quality materials.
With no barriers to entry, there has been an influx of unskilled and inexperienced contractors and, in the worst-case, “fly-by-night” operators who set out to deliberately fleece property owners. This includes scant observance of approved health and safety practices for their workers.
A recently held industry day hosted by BMI Coverland Roofing Academy included, among others, Browns Roofing Systems and Yolikamp Trading & Services, both with a solid reputation in the industry. Materials were supplied for the industry day by Continental Waterproofing & Protective Coatings.
Gordon Brown, owner of Browns Roofing Systems, says many obvious mistakes are being made in the application of torch-on membrane waterproofing systems. Property owners are often concerned to learn that their torch-on waterproofing membrane systems are failing because they were installed incorrectly in the first place.
“Generally mistakes relate to incorrectly undertaking the finer detail which can compromise the overall quality of these systems”, Brown says. His tips are as follows:
Poor waterproofing of outlets
Waterproofing of edges, such as parapets, are also frequently undertaken incorrectly. Internal and external angles are seldom rounded or filleted. Skilled and experienced contractors will always provide a 35mm radius at all internal angles.
The horizontal and vertical surfaces of various materials are subjected to different heat transference rates and, therefore, differential movement. The waterproofing membrane experiences unnecessary stresses and is very difficult to install if it is applied into or over a 90° angle. A competent contractor will avoid sharp edges by using a cove to reduce these stresses and ensure a neat finish. 45° fillets are also commonly used on internal corners to prevent cracking of the waterproofing material.
Correct fusion of torch-on waterproofing membranes
Experienced contractors will heat the lower face of the sheet until it softens and unroll the heated portion of the roll onto the primed substrate and then bear down on it. The membranes also have overlaps, with side laps typically 75mm and end laps 100mm in length. Overlaps are melted and pressed down simultaneously as they are unrolled.
Lap sealing is also complex and very rarely undertaken correctly. The upper layer is lifted about 70mm with a small trowel with a slightly rounded front point. Heat is then applied by torching in between the two layers to the full width of overlapping surfaces. The fusion of the interfaces of the overlaps is repeated along all the laps.
This is done while progressing at manageable distances of between 500mm and 700mm at a time. The flame is concentrated more on the adhesive surface of the upper layer. When melting starts, the membrane is pressed down onto the lower layer and ironed firmly in place with the heated trowel over the full width of the lap. This ensures adhesion of the entire lap.
As work progresses, the edges are reheated from the top and finished off with the same heated trowel to create a smooth seam. Notably, seasoned contractors will avoid excessively heating the membrane during application as this will damage the inner structure of the material. They will also ensure complete integrity of the lap welds. All side and end laps are laid out away from falls to avoid loading edges. If coves are not present, gusset pieces are applied to the outlets of internal floor and wall junctions. Where the membrane reaches the wall or parapet, it is turned up 100mm.
All membrane perimeters are also adequately counter flashed using the correct material. Two thin coats of reflective bituminous aluminium paint are then applied to the exposed torch-on membrane to increase the longevity of the waterproofing material and reduce internal building temperatures.
Property owner’s responsibility to ensure systems are adequately maintained by a reputable roofer Fidel Kampher, owner-operator Yolikamp Trading & Services, concurs with Brown, but adds that it is the responsibility of the property owner to ensure that these systems are also adequately maintained by a reputable roofer. This is considering that torch-on waterproofing membrane systems are also failing because they have not been adequately maintained or their upkeep undertaken by an inexperienced contractor.
“Even quality installations need to be maintained to avoid failure. While it is recommended that torch-on membrane waterproofing systems be maintained every three years, proactive property owners usually prefer that we do this for them every two to twoand-a-half years. In this way, they derive even more value from their investment,” Kampher says.
“Our industry day was yet another resounding success. Notably, it provided a perfect platform for some of the best roofers in the country to share their knowledge for the betterment of the industry. PRAWA looks forward to our next training day when we will again focus on various technical aspects of our trade,” Jeanine De Meyer, Chief Operations Officer of PRAWA, concludes.