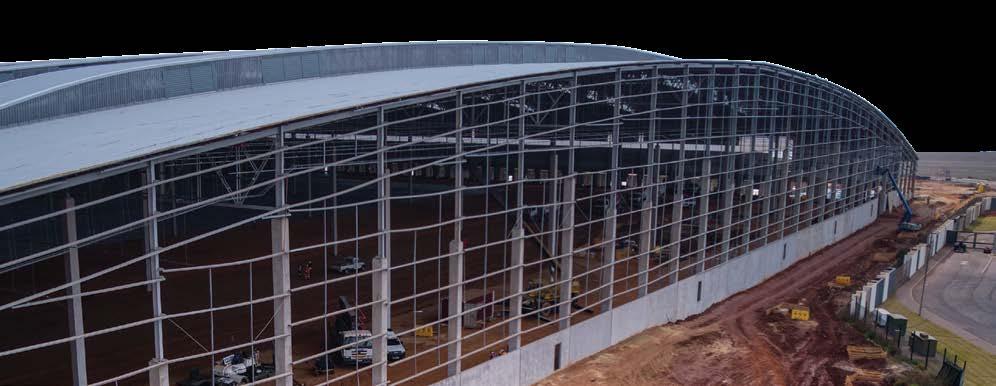
5 minute read
A roof to do South Africa proud
A roof to do
South Africa proud
Pick n Pay’s Eastport Distribution Centre (DC) is currently under construction at the Eastport Logistics Park, a Fortress REIT development, close to ORT International Airport in Gauteng.
Fortress REIT, Pick n Pay and Macsteel
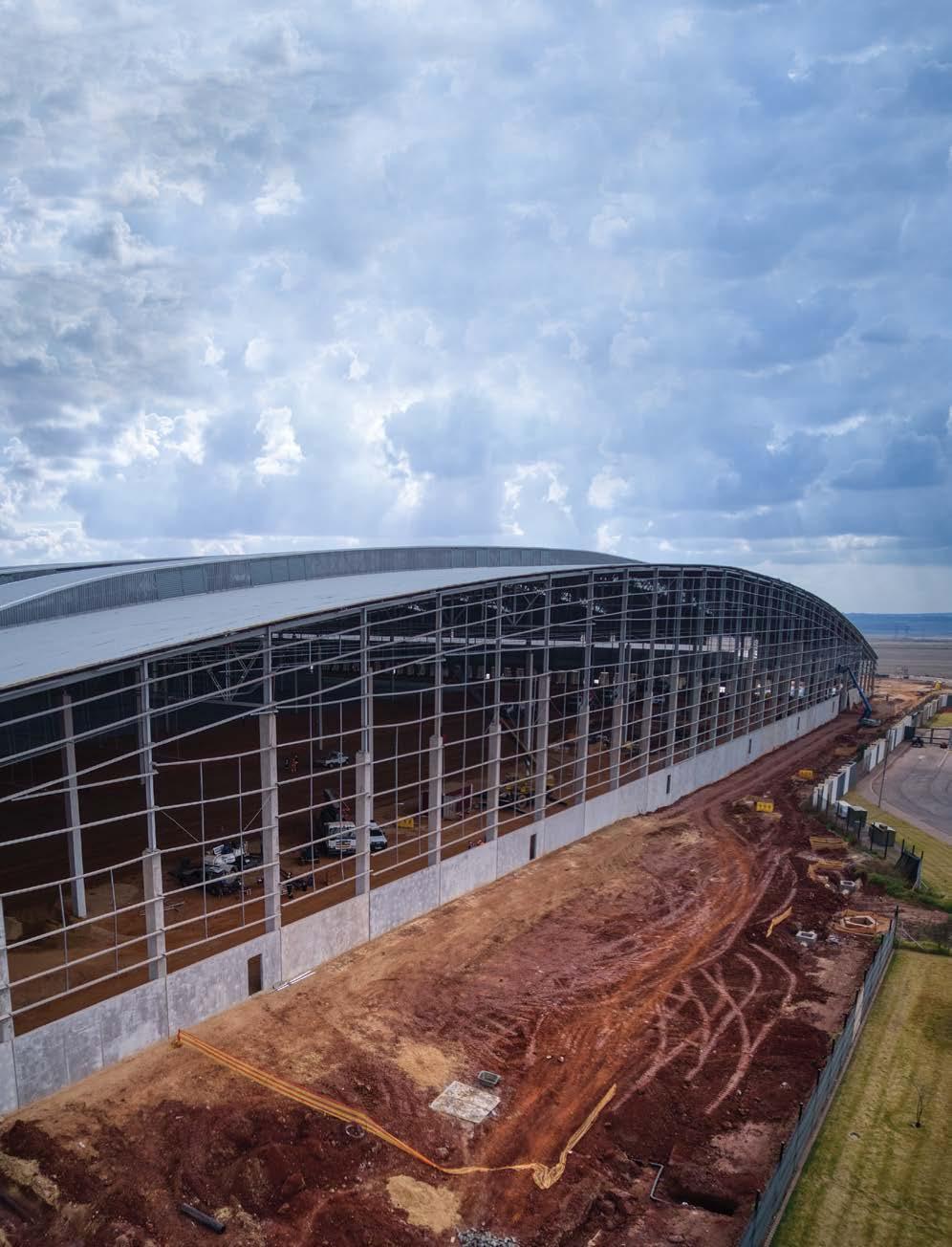
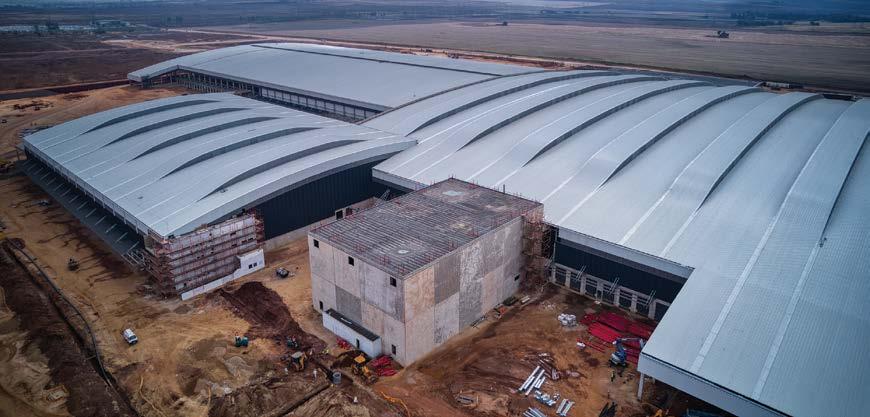
Developed in tandem with Fortress REIT, the leading supermarket chain confirmed the new development will cover 36 hectares of state-of-the art infrastructure and is valued at R2 billion - land and construction costs. When the development of the distribution centre is completed, Pick n Pay will purchase a 60% undivided share in the property for about R1.2 billion and will enter into a long-term lease for the 40% balance with Fortress REIT.
According to Marcel Basson, the Retail Executive at Pick n Pay: Supply Chain, “Our new DC is a consolidation of Longmeadow and three smaller distribution centres in Gauteng within the Pick n Pay network. The new Eastport DC will consolidate all dry goods, perishable and fresh products, as well as all general merchandise and imported goods into one location and under one roof. This will avoid duplication of supply chain and logistics capabilities, such as trucks and warehouse space, in multiple locations.
“We plan to occupy Eastport during 2023. This will be a phased approach, beginning with dry goods, followed by perishable groceries and finally general merchandise later in the year. It will serve a large store network across Gauteng, Mpumalanga, the Free State, North West and Limpopo provinces, including selected stores in the Northern Cape province.”
The Eastport distribution centre will also have capacity to support Pick n Pay’s store expansion plans and will cater for future customer demand in the coming years.
Accordingly, for a giant warehousing project of this size, some rather extraordinary engineering feats have been undertaken. According to the retail giant, the Eastport DC will have a capacity of 150 000m2 . In addition, the new DC will be a green exemplar, confirms Basson.
“Solar panels covering a roof area of 6 400m2 will generate a significant proportion of the facility’s energy requirements, and ultimately save 2 320 tons of CO2 emissions every year”, he adds.
A roof to cover all
For a facility of this size, the eye is naturally drawn to the roof, which covers the facility in a sporty, curved design. The roof structure, which is of giant proportions, is the site where a recent world record was set.
The media were treated with images of what appears to be a suspended shipping container, dangling from a sky jacking boom lift.
Says Dave Reid, the National Product Specialist: Novotexi 440® at Macsteel, “This is a unique method to South Africa, used by Macsteel Novotexi 440 concealed fix roofing. The method is called Sky-Forming. This process of rollforming roof sheeting in long lengths is becoming the preferred method in constructing mega-warehousing.
“It dramatically improves the quality of the end product and has advantages on the critical path planning of the project as a whole in allowing following trades to simultaneously operate without blocking the ground space around the site.”
The roof is 160 000m2 and weighs around 860 tons.
Meanwhile, the base metal product used in this process, made by Safal Steel and called Colorplus® steel, is a coated steel sheet based on a patented zinc-aluminium alloy technology, which is coated onto steel substrate at the Safal Steel factory in KZN, as licenced by world licencing company, BIEC International Inc.
The coated sheet thus manufactured is then pre-painted with custom-designed coatings and available to clients in a range of colours. The coated steel substrate is rated 100AZ, meaning a specified coating width of the special aluminium-zinc (AZ) alloy coated on to a width of 27 microns.
“The roof sheets were sky-formed in 280m lengths using the Safal Steel 0.5mm G550 AZ100 Colorplus Sea Spray,” adds Reid.
Celebrating a world first
Macsteel was officially awarded the status of Guinness World Records™ title holder in June with an epic display of this special technology. In a nutshell, the company made South Africa proud when they broke a world record to become the new title holder for the longest roof span covered by a single metal corrugated sheet. The sheet spans 280 metres, across the widest part of the roof covering the new Pick n Pay flagship DC.
“We are thrilled to be officially recognised as a title holder. That said ‘Pursuing Reinvention’ is about more than setting a world record for us, it’s about taking our customers on the journey with us and finding innovative ways to grow our business while enabling our customers to keep their businesses thriving, especially in such a trying economic climate,” says Mike Benfield, Macsteel CEO.
The Eastport distribution centre will complete the Pick n Pay Group’s supply chain centralisation in the region and support the group’s growth ambitions for the next 15 years.
Project Team
Client: Pick n Pay Group Development manager: Fortress REIT Architect: ICM Architecture Project manager: Brown Barrow & Altini Quantity surveyor: Quanticost Structural & civil engineers: Sotiralis Consulting Engineers Main contractor: WBHO Structural steel erector: Cadcon Engineering Roofing contractor: Tate & Nicholson/Southey Holdings Roofing & cladding roll former: Macsteel Roofing & cladding material supplier: Safal Steel
Celebrating a world record on site - Macsteel.
Key facts
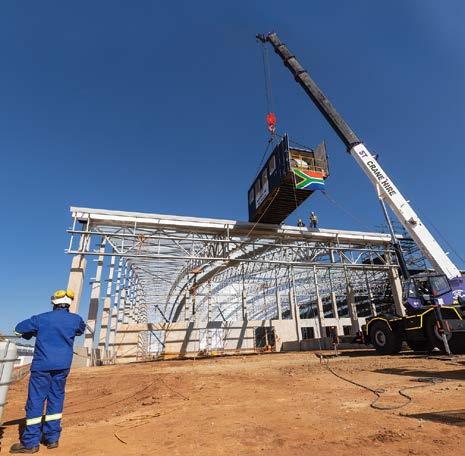
According to Fortress REIT, the new DC is the largest single-phase warehousing development in South Africa and it will be one of the largest distribution centres on the continent.
Some of the impressive stats for this development include: • The post-tension concrete floor will measure 146 886m2 once construction is complete. • The roof structure is considered to be the longest continuous roofing panel in the world; 165 716m2 of roof sheeting will be used to cover the dry goods, perishables, RRU and the main office. • 3 664 tons of structural steel will be used across the site. • The external concrete hardstands (light duty, heavy duty and ramps) will total 147 088m2 . • The dock pits will have 242 dock levellers across dry goods, perishables and recycling & reclamation units (RRU). • The dividing wall will use 800m3 of concrete and will measure 207.5m long and 26.5m high. • 4 700 light fittings will be installed across the site. • 203 000m of cables, trunking, data baskets and wiring will be used. • Tilt up panels/concrete walls will total 2 251m3 (for dry goods, RRU and perishables).
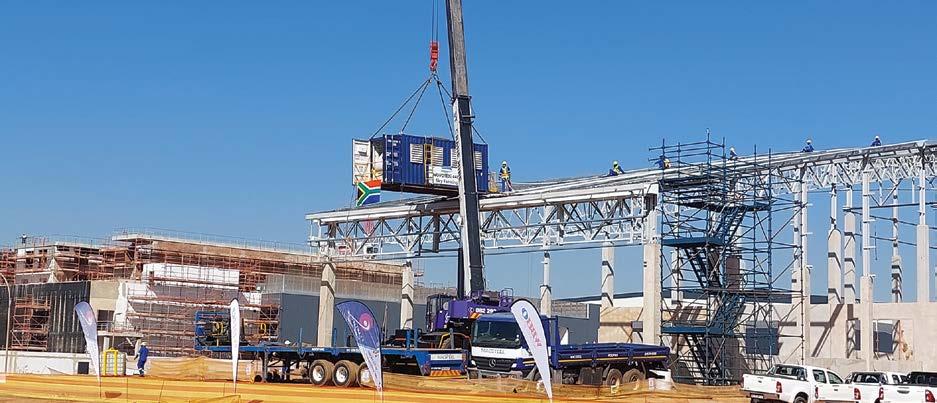
